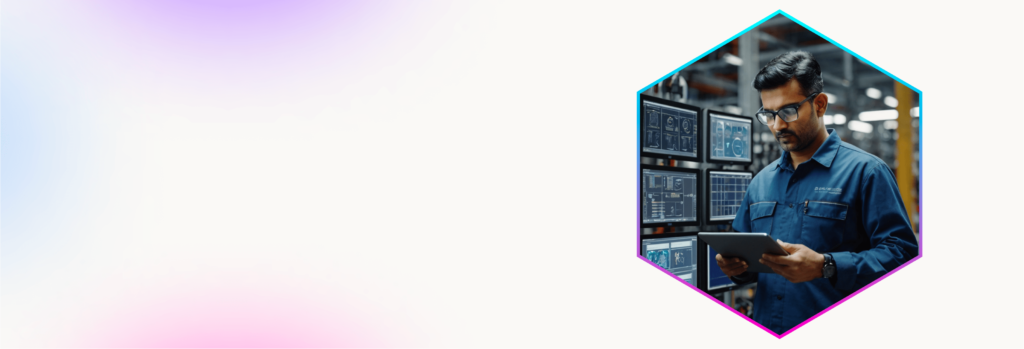
Solve Problems With
Why-Why Analysis
Table of Contents
ToggleWhat is Why Why Analysis?
Why-Why Analysis helps maintenance teams to ascertain the root causes of breakdowns and prevent a recurrence. It is an iterative, interrogative technique to discover and analyze the breakdown and investigate the details. This technique was popularized in the industry first by the Toyota Production System followers and subsequently by the Japanese Institute of Plant Management (JIPM) for Total Productive Maintenance (TPM) practitioners. This methodology is also known as 5Y analysis, Root Cause Analysis (RCA) and Cause and Effect Analysis.
Several alternative problem-solving techniques exist for root cause determination like Pareto Analysis, Fishbone (Ishikawa) Diagram, Failure Modes and Effects Analysis (FMEA), Gemba walks, etc. Why-Why Analysis scores over these alternative techniques due to its simplicity, easy adaptability by floor personnel and the ease with which the users can train.
Why Why Analysis Procedure
Why why analysis is used across industries like manufacturing, process, energy, utilities, etc. to investigate failures and identify root causes. Upon root cause identification, a countermeasure is taken to correct or prevent the issue from recurring.
The following illustrations explain the why-why the analysis was performed under different contexts.
Illustration 1: Frequent Belt Snaps impacting Surface Grinding machine operation in a Manufacturing Industry
The belt in the surface grinding machine gets frequently snapped during runtime, affecting the production and line output. Maintenance technicians replace the belt every time to resume operations, but a permanent fix can avoid costly outages. 5 why analysis is performed to determine the root cause.
Problem Statement: Frequent belt snaps in the primary transmission drive in the grinding machine
A series of repetitive Why’s are asked to identify the underlying root cause of the failure.
Why 1: Why did the belt snap? There were heavy wear and tear, despite a period of low usage.
Why 2: Why was there heavy wear and tear? Coolant carrying grinding muck drips on the belt. Accumulated muck damages the belt while running.
Why 3: Why does the coolant drip on the belt? The coolant chute leading from the grinding table to the sump is not big enough, and hence the coolant overflows.
Why 4: Why does the chute overflow? Coolant pump capacity was increased to accommodate higher feed of jobs, but the coolant chute was not modified.
Why 5: Why wasn’t the chute modified to accommodate higher flow? Design Flaw
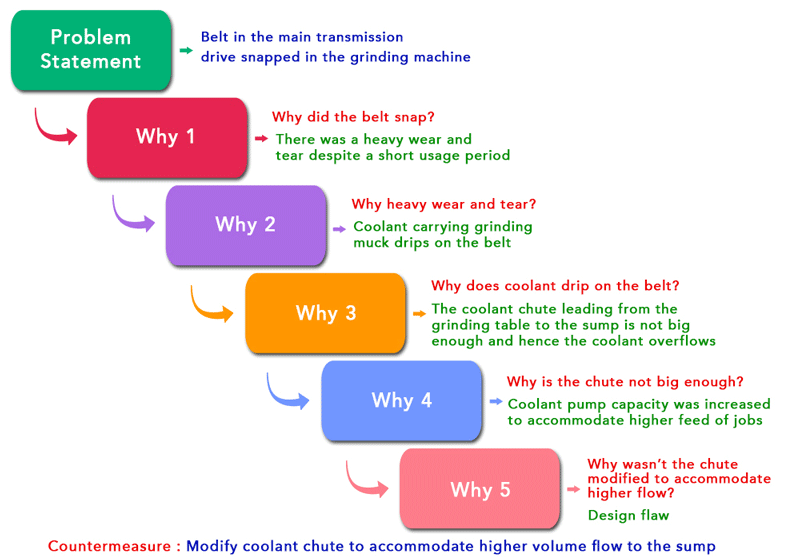
Root cause pertaining to the belt snap is the design oversight to increase chute size to accommodate higher coolant flow.
Countermeasure: Modify coolant chute to accommodate higher volume flow to the sump.
Corrective Action: Coolant chute to be modified to provide higher volume coolant flow.
Horizontal Deployment: Coolant chute to be modified in all surface grinding machines where the pump capacity has been increased.
Illustration 2: Performance Deterioration of a Lubricant Pump in a Process Industry
A lubricant pump runs don’t develop adequate head while pumping out the fluid. Maintenance team sees that an impeller is damaged and have replaced the impeller. Since the damaged impeller was replaced recently, a why-why analysis is performed to ascertain the root cause.
Problem Statement: Lubricant pump doesn’t develop adequate head
A series of repetitive Why’s are asked to identify the underlying root cause of the failure.
Why 1: Why doesn’t the pump develop adequate head? The pump runs with a heavy noise
Why 2: Why does the pump run with a heavy noise? Heavy vibration at the flange end of the pump
Why 3: Why heavy vibration at the flange end of the pump? Shaft misalignment and key damage
Why 4: Why shaft misalignment and key damage? One of the impellers is damaged
Why 5: Why is the impeller damaged? Abnormal levels of suspended impurities in the lubricant
Why 6: Why abnormal levels of suspended impurities? Lubricant sump is unclean
Root cause pertaining to the lubricant pump not developing adequate head is the poor operating quality, wherein debris and impurities have been allowed to accumulate in lubricant sump.
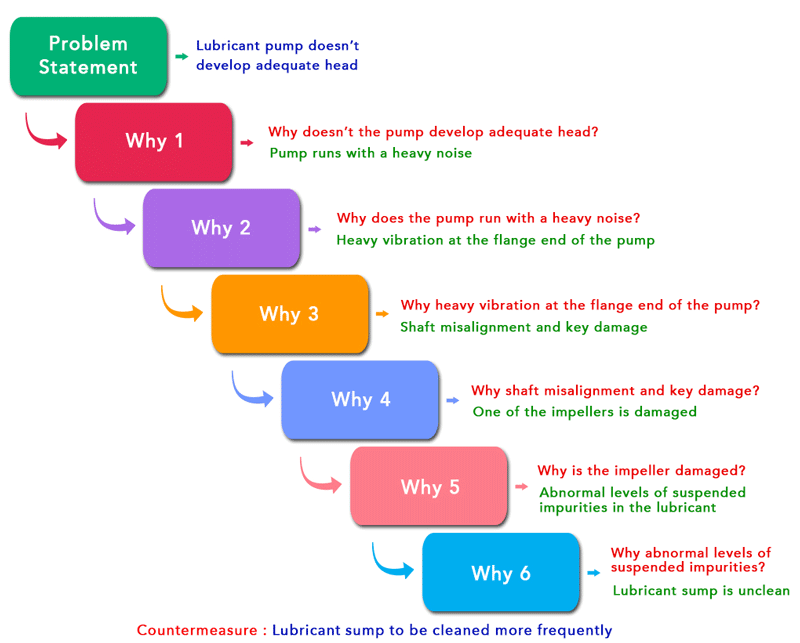
Countermeasure: Lubricant sump to be cleaned more frequently.
Corrective Action: Impeller to be changed, coolant sump to be cleaned.
Preventive Action: The lubricant sump should be cleaned once a month (currently it is a bi-monthly task).
Horizontal Deployment: Apply the revised Preventive Maintenance schedule (monthly) to all Lubricant pumps.
Benefits of Why-Why Analysis:
• Eliminates downtime losses by avoiding future failures
• Improves equipment life by reducing common shortcomings
• Enhances productivity by saving maintenance time
• Helps improve equipment life across similar equipment through horizontal deployment
• Strengthens process governance and enhances institutionalization of knowledge
Why-Why Analysis – Follow-up Actions:
The countermeasure is the final action taken in response to the root cause determined through why-why analysis. Principal countermeasures include Corrective Action and Preventive Action (CAPA).
Corrective Actions: All actions that have to be implemented in the equipment as an immediate and one-time measure to resolve the underlying root cause are termed as Corrective Actions.
Preventive Actions: All actions that need to be done proactively to avert the recurrence of the breakdown are termed Preventive Actions. These may include increasing the frequency of preventive maintenance, updating the tasks carried out as part of preventive maintenance or changing the schedule or actions relating to cleaning, lubrication, inspection, tightening and alignment (CLITA) activities about that equipment.
Why why analysis and the resultant corrective actions and preventive actions (CAPA) are essential for pursuing Total Productive Maintenance (TPM). A well designed Computerized Maintenance Management System (CMMS) will provide you the ability to perform why-why analysis and implement both Corrective Actions and Preventive Actions, right from the breakdown work order.
One Point Lessons
Sometimes the preventive action may include specific tasks by the equipment operators to avert the recurrence. One Point Lesson (OPL) is used as a useful tool to educate the operators on the steps to be taken. One point lesson can be viewed as a simplified standard operating procedure (SOP). It will be precise and covers a single aspect in detail, with adequate supporting illustrations.
Horizontal Deployment
Horizontal Deployment (HD) is the process of creating an organization-wide deployment scheme across the same class of equipment, from the learnings arising out of a Why-Why analysis. It can also originate from other activities like Kobetsu Kaizen, engineering development studies, etc. Proactive horizontal deployment can mitigate potential risks of failure, thereby saving precious time, effort and money.
A well-implemented asset codification schema or an advanced CMMS implementation can help in quickly identifying all the assets that belong to the same equipment class, across the enterprise including those assets that are present at other sites.
Multidimensional Why-Why Analysis
Multidimensional analysis is the process of analyzing the failure holistically, from various dimensions, often beyond the equipment related causes. It can involve analyzing the man-machine interface, operating environment, operator awareness, process issues, etc. to determine the indirect and supporting factors that contributed to the failure or inhibited the earlier detection or prevention of the crash. Based on the analysis outcome, suitable countermeasures like changes in the operating environment, process improvements and training sessions to improve awareness are implemented.
Best Practices for doing Why-Why Analysis:
Training and Practice:
Why-Why analysis is a crucial activity after the equipment is restored to normalcy. It can be taught to all the key stakeholders in the process, including lean production and maintenance teams. It’s the straightforward concept, and people can start using it with minimal training. Practice is the key to achieve best results in the Why Why analysis process. Each person can arrive at a different root cause analysis based on his personal experience. Champions can mentor the users and enhance they’re to come to the proper object to arrive at the appropriate root cause analysis. Like any other process, training and regular practice are the key factors in the quick adoption by the floor personnel.
Culture and Management Support:
Though the why why analysis is a simpler technique and can be practised by anyone with little training, sustaining the why why analysis for continuous improvement needs an enabling organization culture and supporting management.
Timeliness:
Why Why Analysis for a mandated breakdown has to be completed within 24-48 hours of the breakdown closure. This is important because the incident memories fade away with time and capturing them on time improves the effectiveness.
Collaboration:
Effective why-why analysis requires all the key stakeholders to collaborate. The most knowledgeable person about the problem should lead the analysis effort. Facilitators, who are aware of the process, can act as catalysts to enable a meticulous analysis, and proper determination of root cause and countermeasures.
Support for Learning:
Suitable mentoring for each user on the production floor to help them understand the basics and absorb the nuances. Each shop floor user should have a Why Why mentor. In the initial days, the Why Why analysis has to be vetted by the champion to fine-tune the user skills
Gemba:
Gemba is a Japanese term meaning the real place. Gemba’s walk to the breakdown area can help understand the problem from a holistic perspective, including the operating environment and conditions.
Institutionalizing the learning:
Business benefits will accrue exponentially when collective learning is propagated to all stakeholders.
Enterprise Systems:
Availability of tools like CMMS can help in the systematic capture of Why Why analysis and tracking the proper implementation of countermeasures. CMMS can be very beneficial as a training asset, process tool and knowledge repository for organizations that are implementing Total Productive Maintenance (TPM).
Why is MaintWiz an ideal solution for you?
MaintWiz is a new age industry 4.0 CMMS software that helps you to digitize your maintenance operations and supports you with powerful tools to help why-why analysis and implement countermeasures.
- Simple yet Structured: MaintWiz simplifies the why-why analysis process for the user by providing all the relevant information like breakdown details, failure codes, history, etc., at a single point to enable useful analysis. Simultaneously the tool-ification of the process allows for maintaining the rigour of the structured approach to provide comprehensive business benefits.
- Comprehensive: MaintWiz supports the JIPM templates to complete the why-why analysis and implement countermeasures.
- CAPA: Ability to assign corrective action and preventive action (CAPA) to resources and track them to closure. Supports seamless incorporation of preventive maintenance method changes right from the breakdown order.
- One Point Lessons: MaintWiz helps in capturing and publishing one-point lessons to improve operator awareness.
- Multi-site Support & Horizontal Deployment: Enables horizontal deployment across the enterprise.
- Analytics: MaintWiz provides comprehensive analytics with interactive reports to understand, learn and propagate from the root cause analysis. Dashboards and scorecards can help track your adoption, organizational maturity, and institutionalization.
- TPM Excellence: Aids TPM practitioners to focusing on the appropriate pillar (Kobetsu Kaizen, Jishu Hozen, Education, and Training etc.) for implementation of the countermeasure
MaintWiz is a ready-to-use CMMS to support Why Why analysis and your pursuit of TPM Excellence. MaintWiz is offered as a Software-as-a-Service (SaaS) on a monthly subscription model, which means there are no entry or exit costs associated with MaintWiz rollout.
Request a one-one demo with our solution engineering team.
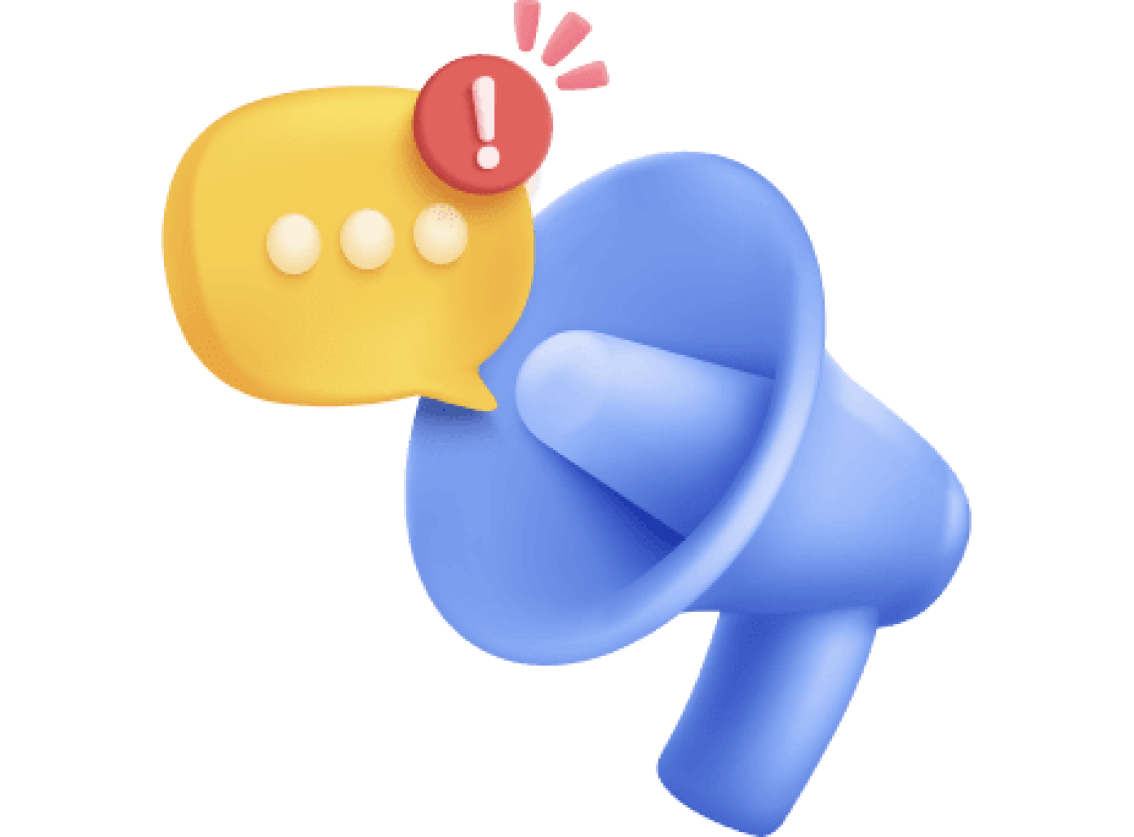
Request a one-one demo with our solution engineering team.