Predictive Maintenance: Future of Asset Care
Predictive Maintenance: Future of Asset Care
Table of Contents
ToggleWhat is Predictive Maintenance?
Predictive Maintenance (PdM) is a technique used to determine the potential failure of a system or component in equipment, using specific critical parameters or equipment condition. Predictive maintenance issues warnings on the occurrence of first symptoms. Thus it not only prevents catastrophic failure and consequent downtime, But it also gives enough notice for the maintenance team to schedule the fix and mobilize spares and technicians, if any, that are needed. Predictive Maintenance relies on Condition Monitoring to detect early signs of equipment failure, allowing for timely interventions.
Reliability-centered maintenance (RCM) emphasizes the use of predictive maintenance techniques to determine the risk of failures and thus no minimum safe maintenance. While Preventive Maintenance follows a scheduled approach, combining it with Predictive Maintenance optimizes asset reliability.
Difference between Preventive Maintenance and Predictive Maintenance
While the result of both preventive maintenance and predictive maintenance are same, in terms of regarding a spare part or component before it fails, their approach to determining the element that needs to be replaced differs widely.
- Preventive maintenance is often time-based and done on a periodic basis and thus uses elapsed time as an indicator for replacement. Predictive maintenance is risk-based approach and uses the probability of failure as the basis for alternative and uses equipment performance or condition as a factor in determining the risk of failure.
- Preventive maintenance is a heuristic based approach based on past equipment history and manufacturer’s specifications. Predictive maintenance is a statistical approach to predict outcomes.
- Preventive maintenance is triggered at pre-set time intervals whereas predictive maintenance is triggered when equipment condition warrants replacement.
- Mathematically preventive maintenance follows a linear model to predict failure whereas predictive maintenance follows an exponential or other statistical distribution to determine the probability of failure.
Preventive Maintenance follows a simple and easy to use approach. Predictive Maintenance is an involved process requiring supporting tools to capture and process the data to compute the risk of failure. In practice, predictive maintenance is used for critical and expensive components or systems. Applying materiality principle, lesser costly parts are replaced with a preventive maintenance approach and along with predictive maintenance of a vital system.
Benefits of Predictive Maintenance:
- Operational continuity: Reduction in both planned and unplanned downtime.
- Avoids failures: By monitoring critical parameters, predictive maintenance gives a more accurate warning of imminent collapse. Corrective action can be taken at the opportune time and, thus a costly failure and associated downtime can be avoided.
- Prevents unnecessary replacements: With the right information at the right time, predictive maintenance avoids the need to shut down the equipment regularly on an elapsed time basis. Thus it avoids unnecessary replacements, person-hours, and associated planned downtime.
- Increases Safety of Operations: Predictive Maintenance factors in multiple variables and thus can predict the failures and consequences much better. Alerts and notifications severe implications to assets, people, and environment.
- Lifetime: Predictive Maintenance can forecast the lifetime of the equipment better and thus help in identifying the ideal time for retiring the equipment. Alternative techniques aren’t as useful in determining the optimal production deployment.
Predictive Maintenance Use Cases:
The power of Predictive Maintenance can be leveraged in a wide variety of ways to support the business outcome. The following illustration predictive maintenance under different contexts
Illustration 1: Residual life calculation of critical component: Hoist ropes support the baggage in bulk cargo handling cranes. Breakage during operations can cause damage to cargo, loss of productivity and safety issues. Predictive maintenance can give alerts on first symptoms.
Illustration 2: Environmental and People Safety, Breakage of pipelines transporting hazardous material can cause massive damage to environment and people in the vicinity. Predictive maintenance can give warnings while the leakages are minor, thereby avoiding near accidents.
Illustration 3: Passenger Safety & Operational efficiency Rolling stock of railway carriages are subject to a variety of conditions. Failure can be catastrophic causing damage to passengers and goods and impacting movement of other transports. Predictive maintenance can identify failures before they occur.
Illustration 4: Fuel conservation for operational efficiency Predictive analytics can determine the efficient workloads and optimum speeds under different environmental conditions to conserve fuel for an inland vessel.
Illustration 5: Multi-factor analysis to identify operational efficiency and predict failures Critical parameters analysis to determine causes for loss of operational efficiency. Comparison of the similar class of equipment (e.g., Twin engines of a ship) under same operating conditions to evaluate performance and resolve deficiencies.
Illustration 6: Spare Parts selection Comparison of 2 spare parts with identical specifications from different vendors on the variety of critical parameters to determine suitability for essential equipment.
Illustration 7: Tool bit breakage Monitoring of multiple environmental factors and operational parameters while drilling in Oil & Gas industry to warn hard surface, thereby protecting tool bit from breakage.
Role of CMMS in Predictive Maintenance
Equipment conditional parameters can be monitored (condition monitoring) through many systems viz. Monitoring mechanisms built by the manufacturer, distributed control system, SCADA, Sensors or via the Internet of Things. Often a combination of these systems can also be used to monitor the critical parameters of different equipment or systems. Integration of the various methods requires a common platform to capture, aggregate, analyze and predict outcomes and notify downstream actions. Computerized Maintenance Management Systems (CMMS) generally play the role of such common platform. CMMS have built-in interfaces to deal with the different protocols and devices. They can be configured to handle the volume, variety, and velocity of information coming from such automated sources. Intelligence built in the CMMS can correlate the different parameters, apply statistical and other techniques to determine the risk of failures. Based on the equipment, nature of the issue, probability, and impact, proper downstream actions such as notifications, warnings or red alerts can be configured. The utility of Predictive maintenance is in triggering the right maintenance plan and to meet this objective predictive maintenance system needs to be integrated with CMMS. Modern CMMS have predictive maintenance modules that can capture and analyze the condition monitoring data and initiate downstream actions.
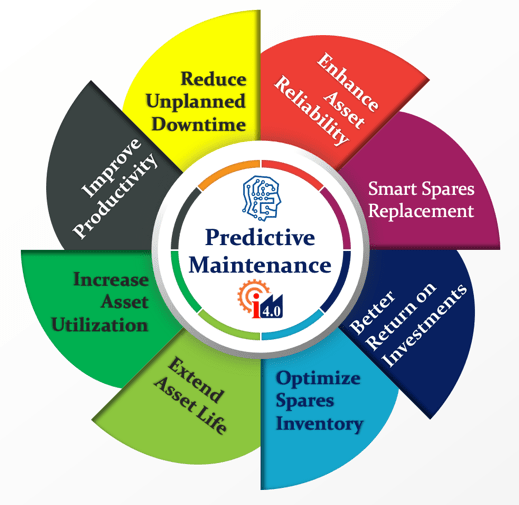
Future of Predictive Maintenance:
Multiple variables that influence the equipment condition can be enlisted and, their combined behavior can be used to model the system behavior. Iterative models can be constructed to simulate interrelated system behavior and perform sensitivity analysis on how a change in a particular parameter can impact the parent system or collective system.
Operational and performance data collected over time for particular equipment can use for modeling a digital twin of the tangible asset. Such digital twin can provide valuable insights on the mechanics and metrics of the physical asset under extreme testing conditions and help determine equipment resilience and risk. Digital twins can help immensely in workload optimization under harsh operating conditions or corollary in a determination of design capacity to take on the load efficiently. Digital twins have applications in capacity determination, performance optimization, efficient utilization, asset life calculation, risk modeling and safety testing. Utilize MaintWiz’s Asset Management system alongside Predictive Maintenance to gain complete control over asset health and performance.
Why is MaintWiz ideal solution for your Predictive Maintenance program?
MaintWiz is a Simple, Easy to use, Integrated, Scalable, and cost-effective industry 4.0 CMMS platform. It provides readymade features to support predictive maintenance.
Improve your Overall Equipment Effectiveness (OEE) by applying Predictive Maintenance to reduce downtime and maximize output.
Interfaces: MaintWiz supports a wide variety of protocols and interfaces to enable data capture from a variety of sources. Captured data can be stored and analyzed to give insights on performance and life.
Integration: It can integrate with different devices, sensors, Internet of Things, SCADA, DCS and other automated means of data capture.
Condition monitoring: It supports condition monitoring of critical parameters. Data ingested is validated against set business rules and, downstream actions can initiate on a breach.
Asset Intelligence: MaintWiz allows comparison of parameters against industry standards and benchmarks, comparison of equipment against itself over time (trend analysis) and comparison of critical parameters across same class of equipment.
Modeling: MaintWiz provides powerful tools for modeling and analytics to determine system behavior and variance. Analytics offer action-oriented insights to support business outcomes.
Horizontal Comparison & Deployment: MaintWiz supports comparison of the same class of equipment under different parameters to determine performance degradation and identify failure symptoms. It also supports propagation of corrective and preventive actions across similar class of equipment.
MaintWiz can help you build a reliable maintenance system. Experience the power of MaintWiz Today.
MaintWiz’s Actionable Analytics provides deep insights that complement Predictive Maintenance, enabling data-driven maintenance decisions.
See how Predictive Maintenance can revolutionize your maintenance strategy.
Request a demo to explore the possibilities with MaintWiz.
Request a one-one demo with our solution engineering team.
Request a one-one demo with our solution engineering team.
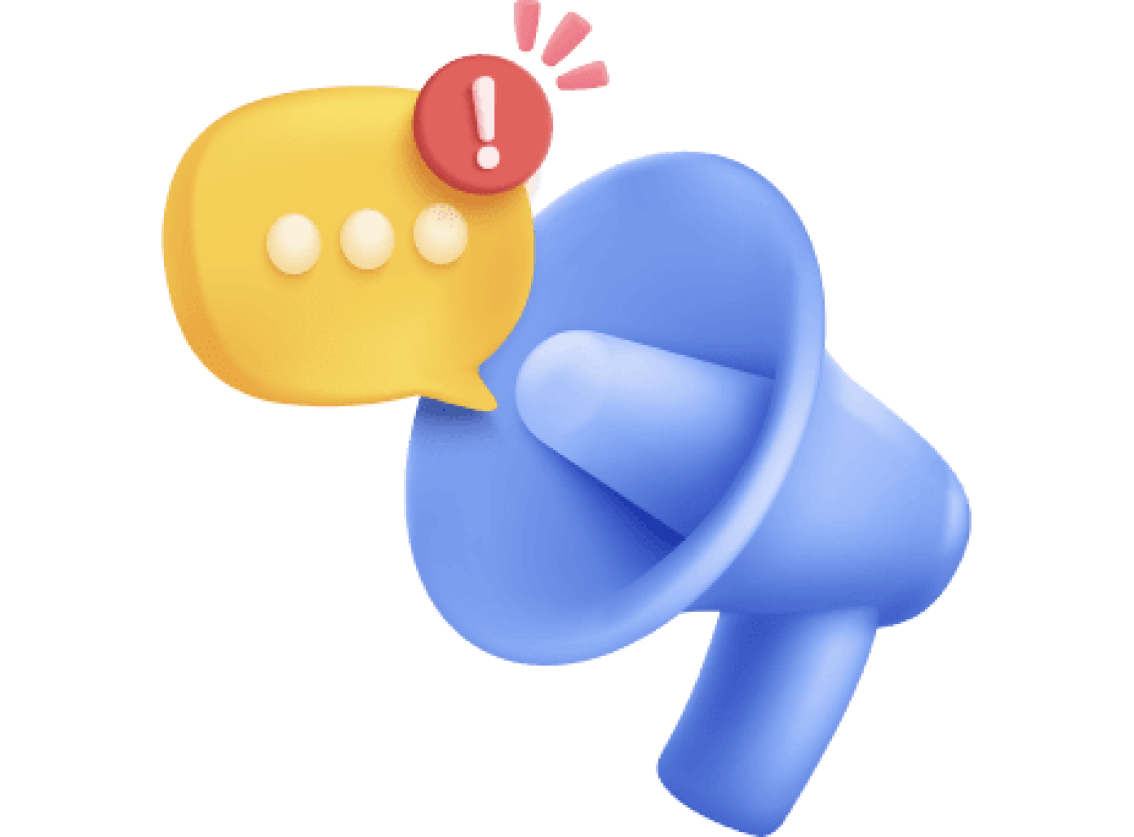