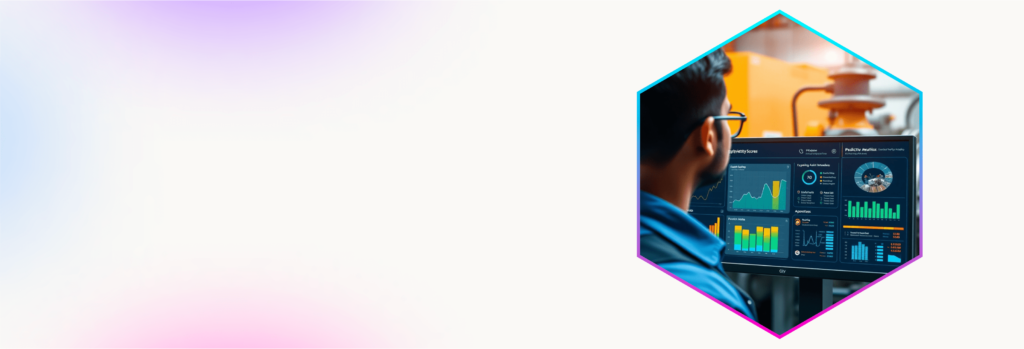
Everything on
OEE
Table of Contents
ToggleWhat is OEE?
Overall Equipment Effectiveness is a measure of the efficacy of the plant operations. OEE has been popularized by the Total Productive Maintenance (TPM) movement and is often considered the gold standard in measuring operational efficiency.
OEE helps in understanding the systemic deficiencies that prevent companies from reaching the maximum goal of 100% efficiency and provides insights into the causes and possible remediation. The simplicity in calculating the OEE metric and its universal applicability across industries has made OEE a best practice and industry favourite to measure operational effectiveness and identify opportunities for improvement.
How is OEE calculated?
OEE = Rate of Availability x Rate of Performance x Rate of Quality
OEE is calculated as a standard measurement that expresses the impact of equipment availability, performance, and the quality of output.
Availability is calculated as the ratio of total available production time to planned production time. Thus, it captures the loss in the productive time of operations due to unscheduled downtime. Any scheduled downtime to undertake preventive maintenance is adjusted and therefore does not impact the OEE calculation.
Performance is calculated as the ratio of total units produced to production capacity. Thus, it accounts for the factors that slow down the output, including slower rate and minor stoppages.
Quality is calculated as the ratio of good parts produced by the total number of products produced. Thus, it’s a measure of the defective parts provided, that do not comply with the established quality standards and require rework.
Each of the factors can theoretically attain a maximum of 100%, and thus OEE can have a maximum value of 100%. An Overall Equipment Effectiveness score of 100% means the plant operations work perfectly without any downtime, producing the product at the ideal capacity and there are no rejects in production output.
Alternately the shortfall of OEE from 100% gives an accurate measure of the different losses experienced in the plant operations that prevented the system from performing at its full potential. TPM classifies these losses occurring on the shop floor as 16 types of failures in Gemba (“the real place”). OEE’s beauty lies in its simplicity, and it captures the operational effectiveness over a period. Though in itself, it does not give insights into the principal causes, analysis of the losses that result in deficiencies in Availability, Performance, and Quality can provide the insights needed.
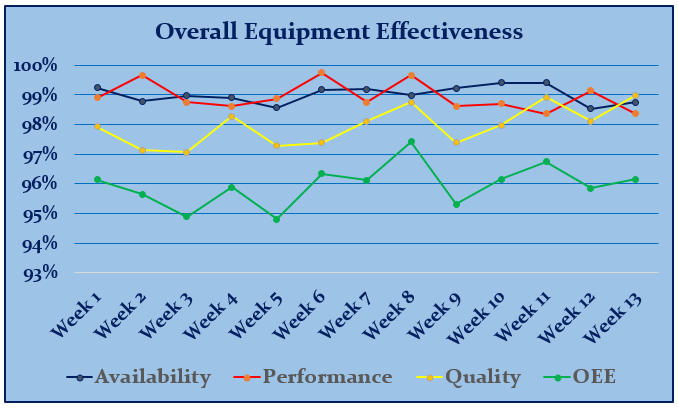
Advantages of OEE
- Most straightforward concept: OEE is very simple and easy to learn. Organizations can start measuring OEE with just pencil and paper. The ability to understand, collect data and compute values is effortless.
- Powerful application: OEE trend gives compelling insights into the effectiveness of operations and can lead to an identification of the underlying problems, often hitherto unknown.
- Extensible: OEE can be measured for a single piece of equipment or a production line or an entire plant. The concept is extensible across a group of assets. It’s independent of size and scale of operations, and thus can be rolled out for an organization of any size.
- Increased process quality: Defective products cause loss of revenue, reputation, and time and have costs associated with their recall and rework. Identification and avoidance of root cause analysis (Why why analysis) that impact quality can save precious time, effort and money.
- Bringing people together in plant operations: With OEE as the common goal, the different stakeholders in the plant operations (production, maintenance, cost accountants) can all be brought together with a single area of focus – continuous improvement.
- Reduce repair costs and downtime: Analysis of OEE leads to avoiding losses and the production team can embark on tasks that can increase equipment uptime and asset life.
How to Implement OEE?
- Define: Define the objectives and scope. Select the pilot equipment. Identify the points of measurement and assign ownership.
- Train: Build the team and train them on the goals, process, data collection, computation, analysis, and improvements.
- Organize: Organize the collection of data from the different sources in the set OEE tracking software frequency and enable proper record keeping.
- Compute: Compute Availability, Performance, Quality and Overall Equipment Effectiveness at the specified instances. Prepare the charts and graphs to show the overall trends.
- Analyse & Act: As a team, analyze the trends and identify the losses that inhibit the operations from achieving their full potential. Devise an action plan to tackle the opportunities for improvement.
- Institutionalize: Institutionalize the Overall Equipment Effectiveness culture across the larger organization. Enable interactions across teams for learning from each other.
- Improve: Rinse and Repeat the process for continuous improvement.
Kotetsu Kaizen pillar of TPM places a lot of emphasis on improving OEE and OEE is often used as a measure of the success of TPM implementation. Calculation of OEE, charting of trends and analysis were all manually done earlier and due to the intensive calculations, it was done post facto. With the proliferation of affordable software, computations are automated now, and OEE availability is in real-time. Computerized Maintenance Management Systems (CMMS) can capture the data directly from the equipment and other production planning systems and as well can take manual inputs to compute dynamically.
Why is MaintWiz ideal for you?
MaintWiz is a new age industry 4.0 CMMS platform that helps you to digitize your maintenance operations and assist you with powerful tools to compute Overall Equipment Effectiveness, visualize trends, analyze losses, action improvements and institutionalize process excellence.
MaintWiz is a Simple, Easy-to-use, Integrated, Cost effective and Scalable CMMS Software solution. It is the ideal solution for organizations that want to measure and improve Overall Equipment Effectiveness / pursue TPM Excellence, Business benefits include:
1. Simple to Use:
MaintWiz is easy to roll out, access and update. Provides intuitive screens that facilitate natural learning and increase user engagement.
2. Complex Calculations:
MaintWiz supports a flexible asset hierarchy to mimic your operational floor and can calculate OEE for not just the equipment, but can also for the production line and plant, often adjusting for various complexities involving standby machines and differential shifts.
3. Multi-Site Support:
MaintWiz is offered as a Software-as-a-Service solution and thus has been designed to support multiple sites. It enables OEE tracking and compares the OEE adoption and effectiveness across various locations.
4. Data Collection:
MaintWiz supports direct data capture from electronic data sources (sensors, SCADA or Enterprise Systems) or can allow direct data entry via excel uploads. MaintWiz Mobile app can swipe QR codes to enable direct data entry with minimal effort, right at the point of work.
5. Interactive Reports:
Presents interactive reports to zoom in for a specified time or clicks to drill down and analyze the underlying data. Supports dashboards and scorecards to show progress.
6. Supporting Tools:
It also provides supporting tools for analysis, inferences, learning and record keeping, thus enabling your continuous improvement journey.
7. TPM Certification:
MaintWiz presents robust features to support and achieve TPM Excellence.
With MaintWiz there are no entry or exit costs. It’s offered on a monthly subscription basis. Excel templates-based data upload enables you to start quickly on Day 1. Experience the complete power with Zero Capital Investments and Zero Implementation Time.
Request a one-one demo with our solution engineering team.
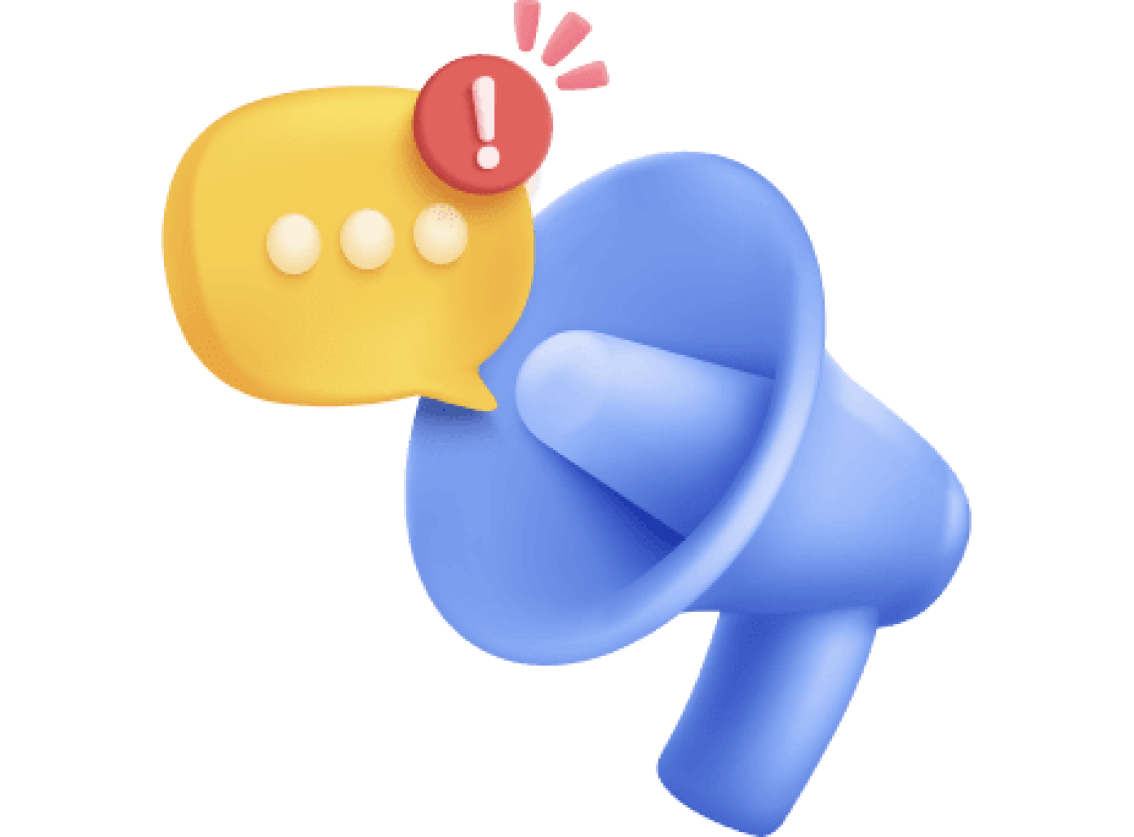
Request a one-one demo with our solution engineering team.