AI-Driven Predictive Maintenance: Revolutionizing Asset Management
Revolutionizing Asset Management
Table of Contents
ToggleAI-Driven Predictive Maintenance: Revolutionizing Asset Management
The Evolution of Industrial Maintenance: From Reactive to Predictive
In the fast-paced world of industrial operations, unplanned downtime is the nemesis of productivity. Traditional maintenance approaches are no longer sufficient to meet the demands of modern manufacturing and process industries. Enter AI-driven predictive maintenance – a game-changer in the realm of asset management and Total Productive Maintenance (TPM).
Gone are the days of reactive maintenance or even scheduled preventive maintenance. Today’s industry leaders are leveraging the power of artificial intelligence and machine learning to predict equipment failures before they occur, optimize maintenance schedules, and maximize Overall Equipment Effectiveness (OEE).
Understanding AI-Driven Predictive Maintenance
AI-driven predictive maintenance is not just a buzzword; it’s a revolutionary approach that combines advanced analytics, machine learning algorithms, and real-time data to forecast potential equipment failures and maintenance needs. This proactive strategy allows organizations to move beyond traditional maintenance models and embrace a more efficient, cost-effective approach to asset management.
Key Components of AI-Driven Predictive Maintenance
- Data Collection: Sensors and IoT devices gather real-time data on equipment performance, environmental conditions, and operational parameters.
- Data Analysis: Advanced analytics and machine learning algorithms process and analyze the collected data to identify patterns and anomalies.
- Predictive Modeling: AI models use historical and real-time data to predict potential failures and optimal maintenance windows.
- Decision Support: Insights and recommendations are provided to maintenance teams and decision-makers to guide maintenance actions.
The Impact of AI on Asset Management and TPM
Implementing AI-driven predictive maintenance can have a profound impact on your organization’s asset management strategy and Total Productive Maintenance initiatives. Here’s how:
Enhancing Reliability-Centered Maintenance (RCM)
AI takes Reliability-Centered Maintenance to the next level by providing more accurate and timely insights into equipment health. This allows maintenance teams to focus their efforts on the most critical assets and failure modes, improving overall reliability and reducing the risk of unexpected breakdowns.
Optimizing Maintenance Schedules
By analyzing historical data and predicting future maintenance needs, AI helps organizations move away from rigid, time-based maintenance schedules. This results in more efficient use of resources, reduced unnecessary maintenance, and minimized disruption to production schedules.
Maximizing Overall Equipment Effectiveness (OEE)
AI-driven predictive maintenance directly contributes to improved OEE by reducing unplanned downtime, optimizing equipment performance, and ensuring consistent product quality. This holistic approach to asset management leads to significant improvements in productivity and profitability.
Implementing AI-Driven Predictive Maintenance: A Strategic Approach
While the benefits of AI-driven predictive maintenance are clear, implementing such a system requires careful planning and execution. Here’s a strategic approach to get you started:
1. Assess Your Current Maintenance Strategy
Begin by evaluating your existing maintenance processes, identifying pain points, and determining areas where predictive maintenance could have the most significant impact.
2. Invest in Data Infrastructure
Ensure you have the necessary sensors, IoT devices, and data collection systems in place to gather high-quality, real-time data from your critical assets.
3. Choose the Right CMMS Solution
Select a Computerized Maintenance Management System (CMMS) that integrates AI and machine learning capabilities. This will serve as the backbone of your predictive maintenance program, providing a centralized platform for data analysis, work order management, and decision support.
4. Develop AI Models and Algorithms
Work with data scientists and maintenance experts to develop AI models tailored to your specific equipment and processes. These models should be capable of accurately predicting failures and recommending optimal maintenance actions.
5. Train Your Team
Invest in training programs to ensure your maintenance team understands the principles of AI-driven predictive maintenance and can effectively use the new tools and insights provided.
6. Start Small and Scale
Begin by implementing AI-driven predictive maintenance on a subset of critical assets. Use the lessons learned from this pilot phase to refine your approach before scaling to your entire operation.
The Future of AI in Industrial Maintenance
As AI and machine learning technologies continue to evolve, the future of industrial maintenance looks increasingly intelligent and autonomous. Some emerging trends to watch include:
Digital Twins for Advanced Simulation
Digital twin technology, combined with AI, will enable more accurate simulations of equipment performance under various conditions, further enhancing predictive capabilities.
Edge Computing for Real-Time Analysis
The rise of edge computing will allow for faster, more localized processing of maintenance data, enabling near-instantaneous decision-making and response to potential issues.
AI-Powered Autonomous Maintenance
As AI systems become more sophisticated, we may see the emergence of fully autonomous maintenance systems capable of diagnosing issues and initiating corrective actions without human intervention.
Conclusion: Embracing the AI Revolution in Asset Management
AI-driven predictive maintenance represents a paradigm shift in how organizations approach asset management and TPM. By harnessing the power of artificial intelligence and machine learning, companies can dramatically improve equipment reliability, reduce maintenance costs, and drive operational excellence.
As a CXO, the question is no longer whether to adopt AI-driven predictive maintenance, but how quickly you can implement this transformative technology to gain a competitive edge in your industry.
Ready to revolutionize your asset management strategy with AI-driven predictive maintenance? Contact us today to learn how our advanced CMMS solutions can help you unlock the full potential of your industrial assets and drive sustainable growth for your organization.
Request a one-one demo with our solution engineering team.
Request a one-one demo with our solution engineering team.
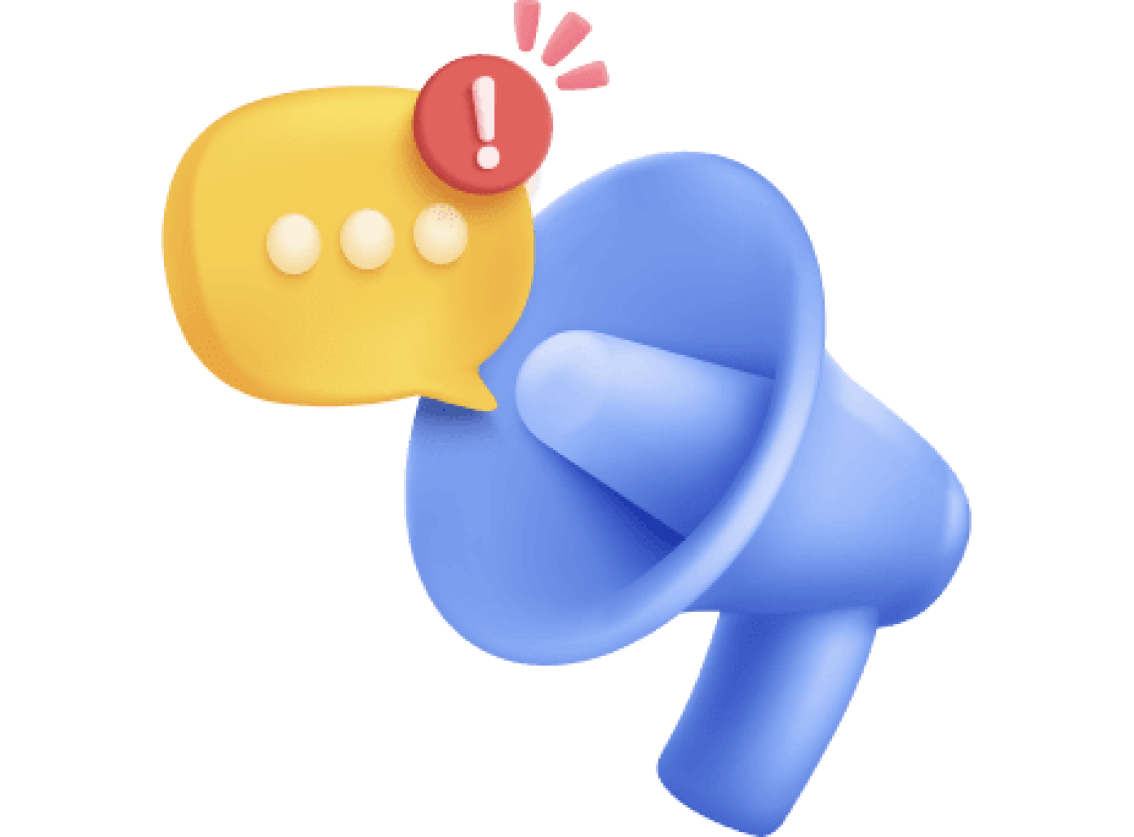