Troubleshooting Your Valves
Troubleshooting Your Valves
Table of Contents
ToggleA Step-by-Step Guide to Troubleshooting Your Valves: Maintenance and Repair Strategies
Valves are an essential part of many industrial processes. They are responsible for regulating the flow of fluids and gases in pipelines, and their proper functioning is crucial for the smooth operation of any manufacturing unit. In this guide, we will discuss the key aspects of valve maintenance and repair strategies, from valve inspection and troubleshooting to repairing techniques, testing and maintenance, and best practices. This guide is intended for Asset Managers, Maintenance Managers, Safety Officers, Manufacturing Professionals, Production in-charges, Supervisors, Consultants, and Experts who are responsible for the maintenance of valves in their organizations.
1. Introduction
Valve – definition, and uses in industry
A valve is a mechanical device that regulates the flow of fluids and gases in pipelines. It is used in a wide range of industrial processes, from oil and gas production to chemical manufacturing and water treatment. Valves can be manual or automated and come in various sizes, shapes, and materials, depending on the application.
The Importance of Valve Maintenance
Valve maintenance is essential to ensure the proper functioning and longevity of valves. Regular maintenance helps prevent valve failure, which can result in costly downtime, production losses, and safety hazards. A well-maintained valve can also improve the efficiency and performance of the overall system, reducing energy consumption and minimizing environmental impact.
Types of Valves
There are several types of valves, each with its unique features and applications. Here are some of the most common types of valves:
Gate valves
Gate valves are commonly used in applications that require full flow or no flow of liquids or gases. They are designed to open fully or close completely, with the gate moving up or down to allow or block the flow.
Globe valves
Globe valves are used in applications that require accurate flow control. They have a spherical body with a movable disk or plug that regulates the flow by moving up or down. They are commonly used in steam and water systems.
Ball valves
Ball valves are used in applications that require quick shutoff and precise control of flow. They have a spherical ball with a hole in the center that rotates to allow or block the flow. They are commonly used in chemical and petrochemical industries.
Butterfly valves
Butterfly valves are used in applications that require quick shutoff and low-pressure drop. They have a circular body with a disc that rotates to allow or block the flow. They are commonly used in HVAC systems and water treatment plants.
Check valves
Check valves are used in applications that require one-way flow control. They allow the fluid or gas to flow in only one direction, preventing backflow. They are commonly used in pipelines and pumping
stations.
The Benefits of Effective Troubleshooting
Effective troubleshooting can help identify and resolve valve problems before they escalate into costly and dangerous situations. Troubleshooting also helps improve the overall performance of the system, reducing energy consumption, and enhancing safety. Moreover, effective troubleshooting can extend the life of valves, reducing the need for frequent replacements and saving costs in the long run.
2. Key Sub-assemblies of Valves
Valves consist of several sub-assemblies, each of which plays a crucial role in the proper functioning of the valve. Understanding these sub-assemblies can help in troubleshooting and maintaining valves. Here are the key sub-assemblies of valves:
Body
The body of the valve is the outer casing that houses the internal components of the valve. It is typically made of metal or plastic and is designed to withstand high pressures and temperatures.
Trim
The trim of the valve includes all the internal components that come in contact with the fluid or gas being regulated by the valve. The trim may include the seat, disc, stem, and other parts that control the flow of fluid or gas through the valve.
Actuator
The actuator of the valve is responsible for opening and closing the valve. It may be manual, electric, or pneumatic, depending on the application.
Positioner
The positioner is an optional component that works with the actuator to control the valve’s opening and closing position. It ensures that the valve opens and closes precisely, improving the accuracy of flow control.
Bonnet
The bonnet of the valve is the top cover that connects the body to the actuator. It provides access to the internal components of the valve for maintenance and repair.
3. Top 10 Most Common Valve Problems
Valves are subject to wear and tear over time, and several problems can arise that affect their performance. Here are the top 10 most common valve problems:
Leakage – Leakage is one of the most common valve problems. It can occur due to wear and tear of the valve seat, stem, or packing. Leakage can result in reduced efficiency, increased energy consumption, and safety hazards.
Blockage – Blockage occurs when debris, dirt, or other foreign particles get stuck in the valve, preventing it from opening or closing properly. Blockage can lead to reduced flow rates, increased pressure drop, and valve failure.
Cavitation – Cavitation occurs when the pressure of the fluid or gas passing through the valve drops below the vapor pressure, causing bubbles to form and collapse. Cavitation can cause severe damage to the valve components, resulting in reduced efficiency and lifespan.
Erosion – Erosion occurs when the fluid or gas passing through the valve causes the valve components to wear out over time. Erosion can lead to reduced efficiency
, increased energy consumption, and safety hazards.
Corrosion – Corrosion occurs when the valve components come in contact with corrosive fluids or gases, resulting in rust, pitting, or other forms of degradation. Corrosion can weaken the valve components, leading to reduced efficiency, valve failure, and safety hazards.
Sticking – Sticking occurs when the valve components become jammed or stuck, preventing the valve from opening or closing properly. Sticking can result from the accumulation of dirt, debris, or corrosion on the valve components.
Fouling – Fouling occurs when the valve components become coated with a layer of material that reduces their efficiency. Fouling can result from the accumulation of dirt, debris, or corrosive materials on the valve components.
Noise – Noise can occur when the valve components vibrate or resonate, producing unwanted sounds. Noise can result from the valve components’ wear and tear or from the pressure of the fluid or gas passing through the valve.
Malfunctioning Actuator – A malfunctioning actuator can prevent the valve from opening or closing properly, leading to reduced efficiency and valve failure. A malfunctioning actuator can result from wiring issues, mechanical problems, or other factors.
Incorrect Valve Sizing – Incorrect valve sizing can result in reduced efficiency, increased energy consumption, and safety hazards. Improper sizing can lead to overloading of the valve components or insufficient flow rates.
4. Pre-Troubleshooting Steps
Before troubleshooting a valve, it is essential to conduct some initial assessments and gather information about the valve system. Here are some pre-troubleshooting steps to take:
Conducting an Initial Assessment
Before troubleshooting the valve, conduct an initial assessment of the system to determine the nature and extent of the problem. This assessment should include checking the pressure, temperature, and flow rates of the fluid or gas being regulated by the valve.
Gathering Information on the Valve System
Gather information on the valve system, including its age, make, and model, and any previous maintenance or repair work performed on it. This information can help in troubleshooting the valve and identifying any underlying issues.
Safety Precautions to Take
Before troubleshooting the valve, ensure that all safety precautions are in place. This includes wearing appropriate personal protective equipment (PPE), such as gloves, goggles, and earplugs, and following lockout/tagout procedures to prevent accidental release of energy.
5. Troubleshooting and Problem Identification
Troubleshooting and problem identification involve a systematic approach to identify and resolve valve problems. Here are the key steps involved:
Checking the Valve Position
Check the valve position to ensure that it is opening and closing properly. If the valve is not opening or closing fully, it could indicate a problem with the actuator or the valve assembly.
Inspecting the Valve Assembly
Inspect the valve assembly for any signs of wear
and tear, corrosion, or other damage. Check the valve components, such as the seat, disc, stem, and packing, for any signs of damage or deterioration. Replace any faulty components as necessary.
Troubleshooting the Valve Actuator
If the valve actuator is malfunctioning, troubleshoot the actuator to identify and resolve the problem. Check the wiring connections, the control circuit, and the power source to ensure that they are functioning correctly. If necessary, replace any faulty components.
Testing the Valve Control
Test the valve control to ensure that it is functioning correctly. This involves checking the pressure, temperature, and flow rates of the fluid or gas being regulated by the valve and comparing them to the desired levels. Adjust the control settings as necessary.
Inspecting the Valve Seals
Inspect the valve seals for any signs of wear and tear, corrosion, or other damage. Check the seals for any leaks or signs of wear that could affect the valve’s performance. Replace any faulty seals as necessary.
6. Repairing the Valve
Repairing a valve involves replacing faulty parts, repairing wiring issues, and cleaning and lubricating components. Here are the key steps involved:
Replacing Faulty Parts
Replace any faulty valve components, such as the seat, disc, stem, and packing, with new ones. Ensure that the replacement parts are compatible with the valve and meet the manufacturer’s specifications.
Repairing Wiring Issues
Repair any wiring issues that may be affecting the actuator’s performance. Check the wiring connections, the control circuit, and the power source to ensure that they are functioning correctly. Replace any faulty wiring as necessary.
Cleaning and Lubricating Components
Clean and lubricate the valve components, such as the stem and the bonnet, to ensure that they are functioning correctly. Use appropriate cleaning and lubrication products that are compatible with the valve materials.
7. Testing and Maintenance
After repairing the valve, it is essential to test it to ensure that it is functioning correctly. This involves running tests to check the valve’s performance and developing a maintenance plan to ensure that the valve continues to function correctly. Here are the key steps involved:
Running Tests to Ensure Proper Functionality
Run tests to check the valve’s performance, including leak testing, performance testing, and other tests as required. Compare the results to the desired levels and adjust the valve settings as necessary.
Developing a Maintenance Plan
Develop a maintenance plan for the valve system that includes regular inspections, cleaning, and lubrication of the valve components. The maintenance plan should also include scheduled replacement of any components that have a limited lifespan.
How CMMS Can Help
Computerized maintenance management systems (CMMS) can help automate the maintenance and repair of valve systems. CMMS can schedule maintenance tasks, track inventory, and generate reports on the valve system’s performance.
8. Best Practices
Here are some best practices for maintaining and troubleshooting valve systems:
Tips and Tricks
Use the following tips and tricks to maintain and troubleshoot valve systems:
Regular Maintenance
Perform regular maintenance on the valve system to prevent problems from arising
Use the Right Tools
Use the right tools for the job, such as wrenches, pliers, and multimeters, to ensure that the valve system is maintained and repaired correctly.
Follow Manufacturer’s Instructions
Follow the manufacturer’s instructions for maintenance and repair of the valve system. This ensures that the valve system is maintained and repaired correctly and helps prevent voiding the manufacturer’s warranty.
How to Prevent Most Common Problems
Use the following measures to prevent the most common valve problems:
Regular Maintenance
Perform regular maintenance on the valve system to prevent problems from arising. This includes inspecting the valve system, cleaning and lubricating components, and replacing any faulty parts.
Proper Installation
Ensure that the valve system is installed correctly and according to the manufacturer’s specifications. Improper installation can result in reduced efficiency, increased energy consumption, and safety hazards.
Use the Right Valve for the Job
Use the right valve for the job, taking into account factors such as pressure, temperature, and flow rates. Using the wrong valve can result in reduced efficiency, increased energy consumption, and safety hazards.
9. Conclusion
Troubleshooting and maintaining valve systems is essential for ensuring their optimal performance, reducing downtime, and preventing safety hazards. The key steps involved in troubleshooting a valve system include conducting an initial assessment, gathering information, troubleshooting and problem identification, and repairing the valve. By following best practices and using the right tools and techniques, you can prevent most valve problems and ensure that your valve system operates efficiently and reliably.
10. Key Takeaways
- Valve maintenance and troubleshooting are essential for ensuring optimal valve system performance and preventing safety hazards.
- The most common valve problems include leakage, corrosion, sticking, fouling, noise, malfunctioning actuators, and incorrect valve sizing.
- Before troubleshooting a valve, conduct an initial assessment, gather information, and take appropriate safety precautions.
- Troubleshooting and problem identification involve a systematic approach to identify and resolve valve problems.
- Repairing a valve involves replacing faulty parts, repairing wiring issues, and cleaning and lubricating components.
- After repairing the valve, it is essential to test it to ensure that it is functioning correctly and develop a maintenance plan to ensure its continued performance.
- Best practices for maintaining and troubleshooting valve systems include performing regular maintenance, using the right tools, and following the manufacturer’s instructions.
Request a one-one demo with our solution engineering team.
Request a one-one demo with our solution engineering team.
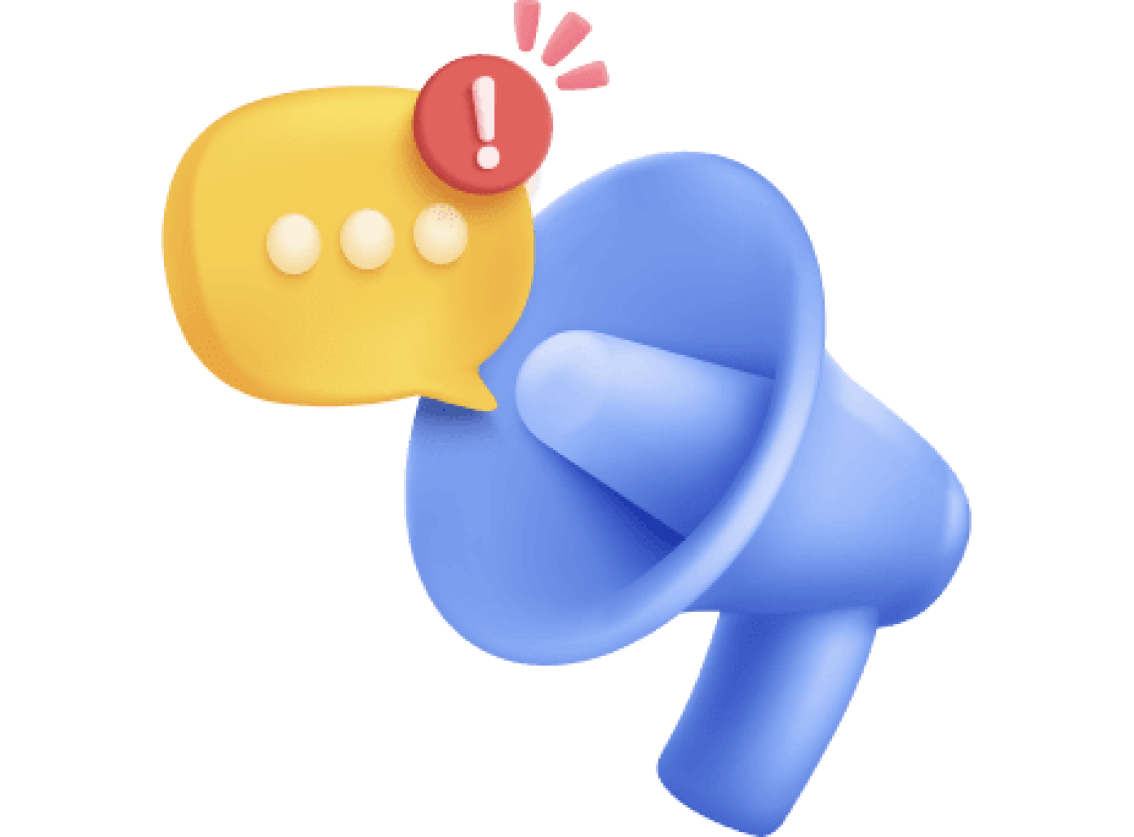