Troubleshooting Your Conveyors
Troubleshooting Your Conveyors
Table of Contents
ToggleA Step-by-Step Guide to Troubleshooting Your Conveyors: Maintenance and Repair Strategies
Introduction
Conveyors are an integral part of many industrial processes, used to transport materials from one point to another. From manufacturing to mining, conveyor systems are crucial for improving efficiency and reducing manual labor. However, like any machinery, conveyors can experience problems and breakdowns that can cause significant downtime and disrupt production. That’s why it’s essential to have a maintenance and troubleshooting plan in place to minimize these risks. In this article, we’ll discuss the key steps to troubleshooting your conveyors, from identifying problems to repairing and maintaining your system.
Types of Conveyors
1. Belt Conveyors
Belt conveyors use a belt to transport materials from one point to another. They are ideal for applications that require materials to be moved over long distances or up inclines. Belt conveyors are versatile and can handle a wide range of materials, from bulk materials to small parts.
2. Roller Conveyors
Roller conveyors use rollers to transport materials. They are ideal for applications that require materials to be moved quickly and efficiently. Roller conveyors are often used in warehouses and distribution centers.
3. Chain Conveyors
Chain conveyors use chains to transport materials. They are ideal for heavy-duty applications that require materials to be moved over long distances or in harsh environments. Chain conveyors are often used in the automotive and mining industries.
4. Screw Conveyors
Screw conveyors use a screw to transport materials. They are ideal for applications that require materials to be moved vertically or at an angle. Screw conveyors are often used in the food and chemical industries.
5. Air Conveyors
Air conveyors use air to transport materials. They are ideal for applications that require materials to be moved quickly and efficiently without contact. Air conveyors are often used in the electronics and pharmaceutical industries.
The Importance of Conveyor Maintenance
Maintaining your conveyor system is crucial for ensuring its longevity and preventing breakdowns. Regular maintenance can also help you identify potential problems before they become major issues that can cause significant downtime and disrupt production. Proper maintenance can also help you reduce costs associated with repairs and replacements, as well as improve the efficiency and performance of your conveyor system.
The Benefits of Effective Troubleshooting
Effective troubleshooting can help you identify the root cause of a problem and implement solutions to prevent it from happening again. Troubleshooting can also help you reduce downtime and minimize the impact of breakdowns on production. Proper troubleshooting can also help you improve the reliability and efficiency of your conveyor system, as well as reduce costs associated with repairs and replacements.
Key Sub-assemblies of Conveyors
1. Belt
The belt is the most critical component of a conveyor system. It is responsible for transporting materials from
one point to another. Proper maintenance and inspection of the belt is crucial for ensuring the efficiency and longevity of the conveyor system.
2. Rollers and Idlers
Rollers and idlers are responsible for supporting the weight of the conveyor belt and materials. They should be inspected regularly for wear and tear and replaced if necessary.
3. Bearings
Bearings are responsible for supporting the load of the conveyor system. They should be lubricated regularly to prevent wear and tear and ensure smooth operation of the system.
4. Gear Reducers
Gear reducers are responsible for reducing the speed of the conveyor motor and increasing torque. They should be inspected regularly for wear and tear and replaced if necessary.
5. Electrical Components
Electrical components, such as motors and sensors, are responsible for the operation of the conveyor system. They should be inspected regularly for proper functioning and replaced if necessary.
Top 10 Most Common Conveyor Problems
1. Belt Tracking Problems
Belt tracking problems occur when the conveyor belt starts to veer off-center, causing it to rub against other components and eventually wear down. This can be caused by a misaligned belt, incorrect tension, or worn components.
2. Belt Tension Issues
Belt tension issues can cause the belt to slip or loosen, which can result in reduced performance and increased wear and tear. This can be caused by incorrect belt tensioning or worn components.
3. Chain Wear
Chain wear occurs when the chains that drive the conveyor system become worn down, causing the system to lose efficiency and eventually fail. This can be caused by lack of lubrication, incorrect tension, or worn components.
4. Motor Overheating
Motor overheating can occur when the motor that drives the conveyor system becomes too hot, causing it to fail. This can be caused by overloading, lack of ventilation, or worn components.
5. Bearing Problems
Bearing problems occur when the bearings that support the conveyor system become worn down, causing the system to lose efficiency and eventually fail. This can be caused by lack of lubrication, incorrect tension, or worn components.
6. Gear Reducer Issues
Gear reducer issues can occur when the gear reducers that reduce the speed of the conveyor motor and increase torque become worn down, causing the system to lose efficiency and eventually fail. This can be caused by lack of lubrication, incorrect tension, or worn components.
7. Sensor Problems
Sensor problems occur when the sensors that control the operation of the conveyor system become faulty, causing the system to malfunction. This can be caused by wiring issues, incorrect calibration, or worn components.
8. Control System Issues
Control system issues can occur when the control system that manages the operation of the conveyor system becomes faulty, causing the system to malfunction. This can be caused by wiring issues, incorrect calibration, or worn components.
9. Material Handling Issues
Material handling issues occur when the materials being transported by the conveyor system become stuck, causing the system to lose efficiency and eventually fail.
This can be caused by incorrect loading, worn components, or inadequate lubrication.
10. Noise Problems
Noise problems occur when the conveyor system becomes excessively noisy, causing disruptions and discomfort for workers. This can be caused by worn components, inadequate lubrication, or incorrect tensioning.
Pre-Troubleshooting Steps
Before troubleshooting your conveyor system, there are several steps you can take to prepare and ensure your safety.
Conducting an Initial Assessment
Conducting an initial assessment can help you identify potential problems and hazards before starting troubleshooting. This includes inspecting the system for any visible signs of wear and tear, checking the tension of the belt or chain, and ensuring that all components are properly aligned and secured.
Gathering Information on the Conveyor System
Gathering information on the conveyor system can help you identify the type of system you are working with, as well as its specifications and maintenance history. This can include reviewing the OEM manual, equipment specifications, and any other publicly available maintenance-related literature.
Safety Precautions to Take
Taking safety precautions is crucial when troubleshooting a conveyor system. This includes wearing appropriate personal protective equipment (PPE), such as safety glasses and gloves, and ensuring that the system is properly shut down and locked out to prevent accidental start-up.
Troubleshooting and Problem Identification
Troubleshooting your conveyor system involves identifying the root cause of a problem and implementing solutions to prevent it from happening again. This can include checking the power supply, inspecting the conveyor assembly, troubleshooting the motor, testing the speed control, and inspecting the gearbox.
Checking the Power Supply
Checking the power supply is the first step in troubleshooting your conveyor system. This includes checking that the power source is connected and functioning properly, and that there are no loose or damaged connections.
Inspecting the Conveyor Assembly
Inspecting the conveyor assembly involves checking for any visible signs of wear and tear, such as cracks, breaks, or damage to components. This also includes checking that the belt or chain is properly tensioned and aligned, and that all components are securely fastened.
Troubleshooting the Motor
Troubleshooting the motor involves checking that it is receiving power and functioning properly. This can include checking that the motor is not overheating, that there are no loose or damaged connections, and that the motor is properly lubricated.
Testing the Speed Control
Testing the speed control involves checking that it is functioning properly and that the conveyor system is running at the correct speed. This can include adjusting the speed control settings and checking that the system is not overloaded.
Inspecting the Gearbox
Inspecting the gearbox involves checking that it is functioning properly and that all components are properly lubricated. This can include checking for any visible signs of wear and tear, such as cracks, breaks, or damage to components.
Repairing the Conveyor
Repairing your conveyor system involves replacing faulty parts, repairing belt alignment issues, and cleaning and lubricating components.
Replacing Faulty Parts
Replacing faulty parts involves identifying the specific components that are causing the problem and replacing them with new or refurbished parts. This can include replacing bearings, motors, sensors, or any other components that are worn
or damaged.
Repairing Belt Alignment Issues
Repairing belt alignment issues involves identifying the root cause of the misalignment and implementing solutions to prevent it from happening again. This can include adjusting the tension of the belt or chain, replacing worn components, or realigning the system.
Cleaning and Lubricating Components
Cleaning and lubricating components involves removing any debris or buildup on the system and applying lubricant to prevent wear and tear. This can include lubricating bearings, rollers, and idlers, as well as cleaning the belt or chain.
Testing and Maintenance
After repairing your conveyor system, it is important to run tests to ensure proper functionality and develop a maintenance plan to prevent future problems. This can include using CMMS (Computerized Maintenance Management System) software to schedule routine maintenance tasks and track maintenance history.
Running Tests to Ensure Proper Functionality
Running tests involves ensuring that the conveyor system is running smoothly and efficiently after repairs have been made. This can include checking that the system is properly aligned and tensioned, that there are no unusual noises or vibrations, and that all components are functioning properly.
Developing a Maintenance Plan
Developing a maintenance plan involves scheduling routine maintenance tasks, such as lubrication and inspection, to prevent future problems and ensure the longevity of the conveyor system. This can be done using CMMS software or by developing a manual maintenance schedule.
How CMMS can Help
CMMS (Computerized Maintenance Management System) software can help streamline the maintenance process by automating tasks such as scheduling, tracking maintenance history, and generating reports. This can help ensure that routine maintenance tasks are completed on time and that the conveyor system is operating at peak efficiency.
Best Practices
Implementing best practices can help prevent common conveyor problems and ensure the longevity of the system.
Tips and Tricks
Implementing tips and tricks such as using the correct lubricant, regularly inspecting the system, and properly aligning the belt or chain can help prevent common problems and ensure the efficiency of the system.
How to Prevent Most Common Problems
Preventing the most common problems, such as belt tracking issues, chain wear, and motor overheating, involves implementing regular maintenance tasks and identifying potential problems before they occur. This can include scheduling routine inspections, lubrication, and replacing worn components as needed.
Conclusion
Troubleshooting your conveyor system involves identifying potential problems and implementing solutions to prevent them from occurring. By conducting regular maintenance tasks and identifying potential problems early on, you can ensure the longevity and efficiency of your conveyor system.
Recap of Troubleshooting Steps
- Conduct an initial assessment
- Gather information on the conveyor system
- Take safety precautions
- Check the power supply
- Inspect the conveyor assembly
- Troubleshoot the motor
- Test the speed control
- Inspect the gearbox
- Replace faulty parts
- Repair belt alignment issues
- Clean and lubricate components
- Run tests to ensure proper functionality
- Develop a maintenance plan
The Importance of Regular Maintenance
Regular maintenance is crucial for preventing common conveyor problems and ensuring the efficiency and longevity of the system. By implementing routine maintenance
tasks and identifying potential problems early on, you can save time and money in the long run.
Key Takeaways
- Conveyor systems are used in a variety of industries to transport materials.
- Common conveyor problems include belt tracking issues, chain wear, motor overheating, and bearing problems.
- Before troubleshooting your conveyor system, take safety precautions and conduct an initial assessment.
- Troubleshooting your conveyor system involves identifying the root cause of a problem and implementing solutions to prevent it from happening again.
- Repairing your conveyor system involves replacing faulty parts, repairing belt alignment issues, and cleaning and lubricating components.
- Running tests after repairs have been made and developing a maintenance plan can help ensure proper functionality and prevent future problems.
- Implementing best practices, such as using the correct lubricant and regularly inspecting the system, can help prevent common conveyor problems.
- Regular maintenance is crucial for preventing common conveyor problems and ensuring the longevity and efficiency of the system.
Request a one-one demo with our solution engineering team.
Request a one-one demo with our solution engineering team.
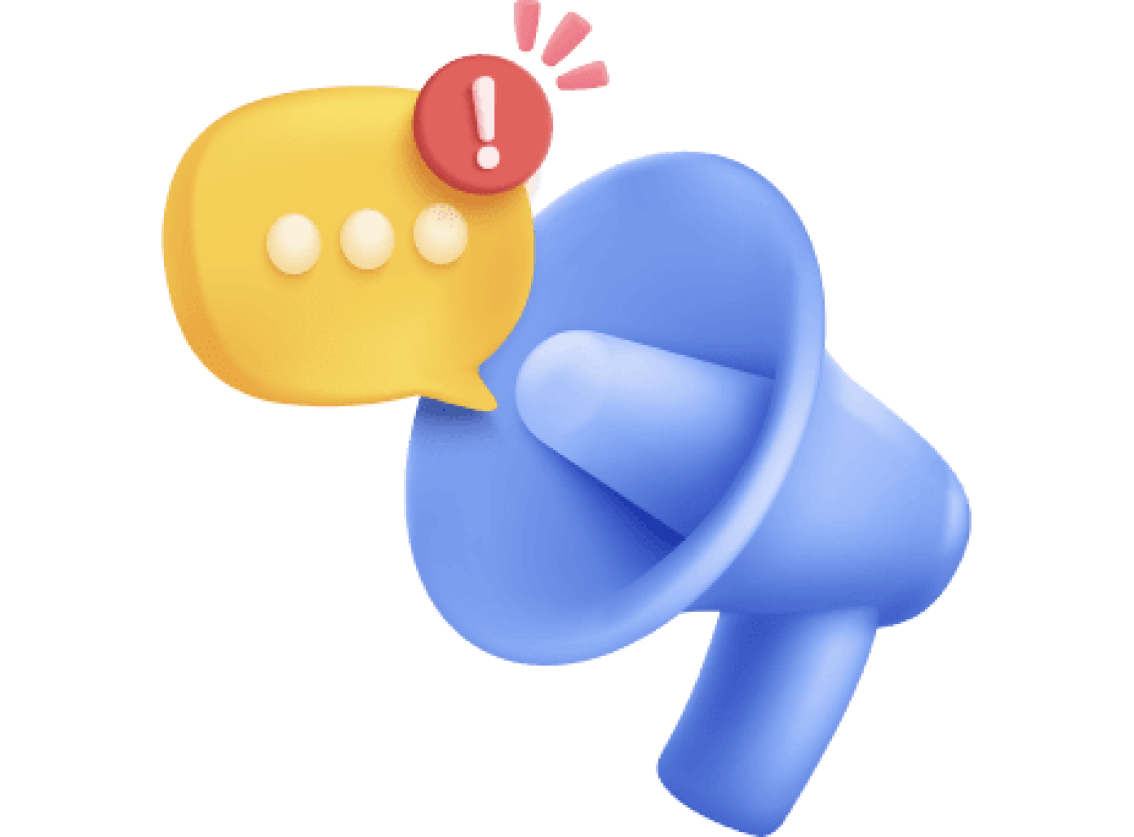