Preventive Maintenance Program
for Turbines
Preventive Maintenance Program for Turbines
The Complete Guide to Defining Your Preventive Maintenance Program for Turbines
Table of Contents
ToggleIf you’re involved in plant maintenance or asset management, you know how important it is to have an effective preventive maintenance program in place for your turbines. Preventive maintenance helps to minimize breakdowns, increase safety, reduce downtime, and optimize efficiency. But how do you develop a comprehensive preventive maintenance plan for turbines? In this guide, we’ll cover the key components of a preventive maintenance plan, the benefits of preventive maintenance, tools and techniques for maintenance, best practices, and more.
1. Introduction to Preventive Maintenance for Turbines
Overview of Preventive Maintenance for Turbines
Preventive maintenance is a proactive approach to maintenance that involves regular inspections, cleaning, lubrication, testing, repair, and replacement of components to prevent breakdowns and extend the life of the equipment. Preventive maintenance programs are designed to identify potential problems before they become major issues, reducing downtime and maintenance costs.
Importance of Preventive Maintenance for Turbines
Turbines are critical components of many industrial processes, and downtime can be costly. Preventive maintenance helps to ensure that turbines operate safely and efficiently, reducing the risk of breakdowns and costly repairs. A well-designed preventive maintenance program can also help to extend the lifespan of turbines, maximizing your return on investment.
Sub-assemblies and Components of Turbines
A typical turbine consists of several sub-assemblies and components, including the rotor, stator, bearings, shaft, and cooling system. Each of these components requires regular inspection, cleaning, and maintenance to ensure optimal performance and prevent breakdowns.
2. Components of a Preventive Maintenance Plan for Turbines
Scheduled Inspections and Maintenance Tasks
A preventive maintenance plan should include scheduled inspections and maintenance tasks for all critical components of the turbines. Inspections should be conducted on a regular basis, with maintenance tasks performed as needed. Regular inspections help to identify potential problems before they become major issues, reducing downtime and maintenance costs.
Recommended Frequency of Inspections and Maintenance Tasks
The frequency of inspections and maintenance tasks will depend on several factors, including the age of the equipment, operating conditions, and past failure history. In general, critical components should be inspected at least once per year, with more frequent inspections for components that are subject to high wear and tear.
Recording and Tracking Maintenance Activities
Recording and tracking maintenance activities is an essential component of a preventive maintenance program. A maintenance log should be kept for each turbine, with details of all inspections, maintenance tasks, and repairs performed. This information can be used to identify trends and patterns in maintenance issues, enabling you to optimize your maintenance program over time.
3. Benefits of Preventive Maintenance for Turbines
Improved Safety
Preventive maintenance helps to identify potential safety hazards before they become major issues. By keeping your turbines in good condition, you can reduce the risk of accidents and injuries in the workplace.
Increased Efficiency
By regularly inspecting and maintaining critical components of your turbines, you can ensure that they are operating at peak efficiency. This can help to reduce energy consumption and minimize operational costs.
Reduced Downtime
Preventive maintenance can help to minimize unexpected breakdowns and repairs, reducing downtime and lost productivity. By identifying potential issues before they become major problems, you can schedule maintenance and repairs at a time that is convenient for your operations.
Cost Reduction
Preventive maintenance can help to reduce maintenance costs over time by identifying potential issues before they become major problems. By regularly maintaining your turbines, you can also extend their lifespan, reducing the need for costly replacements.
Asset Management
A well-designed preventive maintenance program can help to extend the lifespan of your turbines, maximizing your return on investment. By regularly inspecting and maintaining critical components, you can also identify potential issues that may require replacement or upgrade in the future.
4. Tools and Techniques for Preventive Maintenance for Turbines
Cleaning and Lubrication Methods
Cleaning and lubrication are essential components of preventive maintenance for turbines. Regular cleaning helps to remove dirt and debris that can damage critical components, while lubrication helps to reduce friction and wear. Specific cleaning and lubrication methods will depend on the type of turbine and its components.
Inspection and Testing Procedures
Regular inspections and testing are critical components of preventive maintenance for turbines. Inspections should be conducted on a regular basis to identify potential issues, while testing can help to ensure that critical components are operating as intended. Specific inspection and testing procedures will depend on the type of turbine and its components.
Repair and Replacement Guidelines
If issues are identified during inspections and testing, repair and replacement guidelines should be established. These guidelines should specify the conditions under which repairs or replacements should be performed, as well as the specific procedures and components that should be used.
Condition Monitoring Techniques
Condition monitoring techniques can help to identify potential issues before they become major problems. Specific techniques will depend on the type of turbine and its components, but may include vibration analysis, thermography, and ultrasonic testing.
5. Developing a Preventive Maintenance Program for Turbines
Identifying Critical Turbines and Equipment
The first step in developing a preventive maintenance program for turbines is to identify critical turbines and equipment. These may include turbines that are critical to your operations or turbines that are subject to high wear and tear.
Researching OEM Manuals and Recommendations
Once critical turbines and equipment have been identified, OEM manuals and recommendations should be researched to identify specific maintenance requirements and procedures. These manuals will provide detailed information on recommended maintenance tasks, inspection frequencies, and repair procedures.
Factoring Operational Conditions
The age of the equipment, operating conditions, and past failure history should be factored in when developing a preventive maintenance program. Components that are subject to high wear and tear or that have a history of failures should be inspected and maintained more frequently than other components.
Establishing Maintenance Schedules and Tasks
Maintenance schedules and tasks should be established for all critical turbines and equipment. These schedules should specify the frequency of inspections and maintenance tasks, as well as the specific procedures and components that should be used.
Developing a System for Tracking and Recording Maintenance Activities
Finally, a system for tracking and recording maintenance activities should be developed. This system should include a maintenance log for each turbine, with details of all inspections, maintenance tasks, and repairs performed. This information can be used to identify trends and patterns in maintenance issues, enabling you to optimize your maintenance program over time.
6. Preventive Maintenance for Specific Turbine Types
Types of Turbines
- Gas Turbines
- Steam Turbines
- Hydro Turbines
- Wind Turbines
- Combustion Turbines
Preventive Maintenance Activities for Each Type of Turbine
Gas Turbines
- Cleaning and inspection of air filters
- Inspection and testing of combustion components
- Lubrication of bearings and other moving parts
- Inspection and testing of electrical components
- Testing of control systems
Steam Turbines
- Cleaning and inspection of steam nozzles and blades
- Inspection and testing of bearings
- Lubrication of bearings and other moving parts
- Inspection and testing of electrical components
- Testing of control systems
Hydro Turbines
- Cleaning and inspection of intake screens
- Inspection and testing of bearings
- Lubrication of bearings and other moving parts
- Inspection and testing of electrical components
- Testing of control systems
Wind Turbines
- Cleaning and inspection of blades
- Inspection and testing of bearings and gearboxes
- Lubrication of bearings and other moving parts
- Inspection and testing of electrical components
- Testing of control systems
Combustion Turbines
- Cleaning and inspection of air filters
- Inspection and testing of combustion components
- Lubrication of bearings and other moving parts
- Inspection and testing of electrical components
- Testing of control systems
7. Best Practices for Preventive Maintenance for Turbines
Regular Inspections and Cleaning
Regular inspections and cleaning should be performed to identify potential issues and remove dirt and debris that can damage critical components.
Proper Lubrication and Fluid Levels
Proper lubrication and fluid levels should be maintained to reduce friction and wear and prevent overheating and other issues.
Monitoring and Analyzing Turbine Performance Data
Performance data should be monitored and analyzed on a regular basis to identify potential issues and optimize performance. This data can also be used to establish baseline performance metrics and identify areas for improvement.
8. Measuring the Efficiency of Preventive Maintenance for Turbines
Key Performance Indicators (KPIs)
- Equipment Availability
- Mean Time Between Failures (MTBF)
- Mean Time to Repair (MTTR)
- Overall Equipment Effectiveness (OEE)
- Maintenance Cost as a Percentage of Asset Value
9. Role of Computerized Maintenance Management System (CMMS)
Master Data Management
CMMS systems can be used to manage master data for turbines, including equipment specifications, maintenance requirements, and performance data. This information can be used to optimize maintenance programs and improve turbine performance.
Equipment History
CMMS systems can be used to track equipment history, including maintenance activities, repairs, and replacements. This information can be used to identify trends and patterns in maintenance issues, enabling you to optimize your maintenance program over time.
Preventive Maintenance Scheduling and Tracking
CMMS systems can be used to schedule and track preventive maintenance activities, ensuring that all critical components are inspected and maintained on a regular basis. This can help to reduce unexpected breakdowns and repairs, minimizing downtime and lost productivity.
Operational Technology Integration and Condition Based Maintenance
CMMS systems can be integrated with operational technology (OT) systems, enabling condition-based maintenance. By monitoring real-time performance data, you can identify potential issues before they become major problems, enabling you to schedule maintenance and repairs at a time that is convenient for your operations.
KPIs Monitoring
CMMS systems can be used to monitor key performance indicators (KPIs), enabling you to identify trends and patterns in maintenance issues, optimize your maintenance program over time, and improve turbine performance.
10. Conclusion
Preventive maintenance is essential for ensuring that turbines are operating at peak efficiency and minimizing downtime and maintenance costs. By developing a well-designed preventive maintenance program, using appropriate tools and techniques, and integrating a CMMS system, you can optimize your maintenance program over time and maximize your return on investment.
Remember to regularly inspect and clean your turbines, maintain proper lubrication and fluid levels, and monitor performance data to identify potential issues and optimize performance. By following these best practices and measuring KPIs, you can continuously improve your maintenance program and ensure that your turbines are operating at peak efficiency.
Request a one-one demo with our solution engineering team.
Request a one-one demo with our solution engineering team.
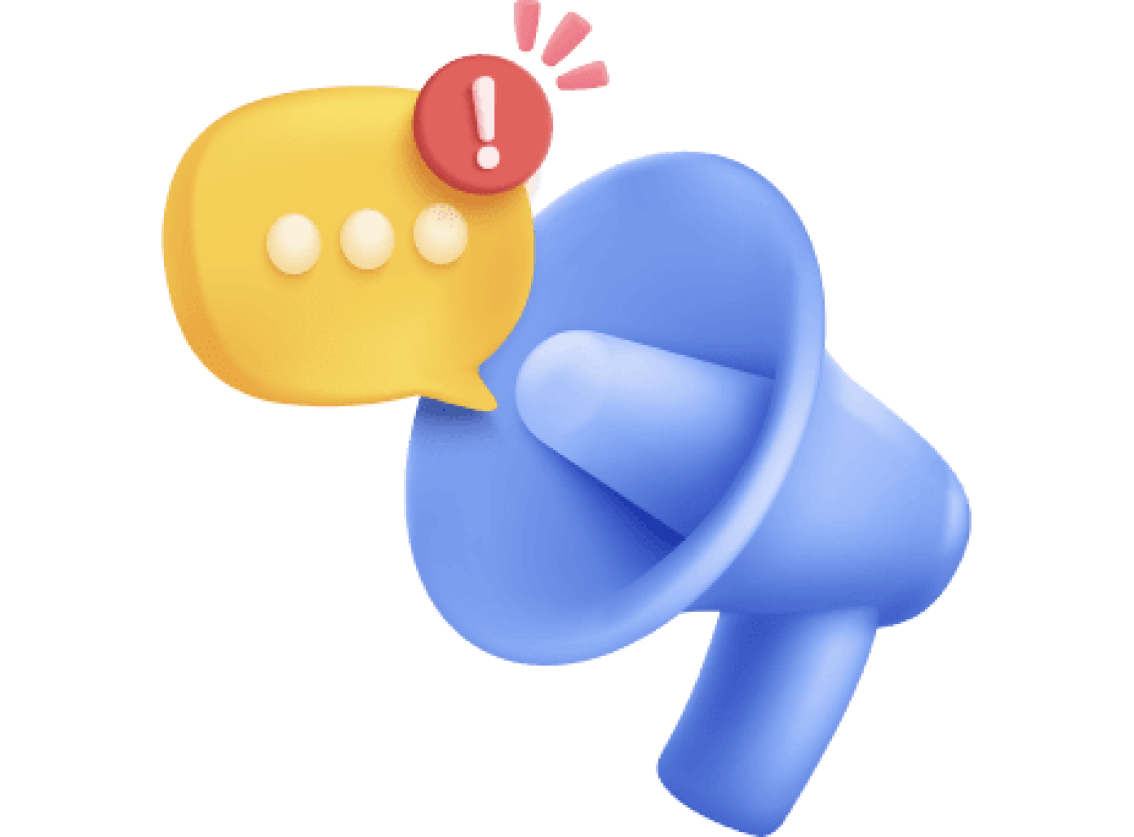