Preventive Maintenance Program
for Separators
Preventive Maintenance Program for Separators
The Complete Guide to Defining Your Preventive Maintenance Program for Separators
Table of Contents
Toggle1. Introduction to Preventive Maintenance for Separators
Preventive maintenance is a proactive approach to maintenance that involves regularly inspecting, cleaning, lubricating, repairing, and replacing components of equipment to prevent breakdowns and prolong the life of the equipment. In this section, we will provide an overview of preventive maintenance for separators, discuss the importance of preventive maintenance, and examine the sub-assemblies and components of separators.
Overview Preventive Maintenance for Separators
Separators are used in a variety of industrial applications to separate liquid and solid particles from a mixture. They are critical components of many processes and their failure can lead to significant downtime and production losses. Preventive maintenance for separators involves regularly inspecting and servicing the components of the separator to prevent failures and extend its life.
Importance of Preventive Maintenance for Separators
Preventive maintenance is important for separators for several reasons:
- Minimizes downtime and production losses
- Improves equipment reliability and productivity
- Reduces maintenance costs by identifying and addressing issues early
- Increases safety by ensuring that equipment is functioning properly
- Extends the life of the equipment
Sub-assemblies and Components of Separators
A separator is comprised of several sub-assemblies and components that must be inspected and serviced regularly to ensure its proper functioning. These components include:
- Separator motor
- Separator drive
- Separator filter
- Separator system
- Separator vibration and noise
- Separator power consumption
- Separator airflow and capacity
- Separator wear parts
- Separator heating and cooling
- Separator controls
- Separator bearings and seals
- Separator heating elements, igniter, pilot light, thermostat, timer, and sensors
2. Components of a Preventive Maintenance Plan for Separators
A preventive maintenance plan for separators should include scheduled inspections and maintenance tasks, recommended frequency of inspections and maintenance tasks, and a system for recording and tracking maintenance activities.
Scheduled inspections and maintenance tasks
The preventive maintenance plan should include a schedule of inspections and maintenance tasks for each component of the separator. These tasks should be performed at regular intervals and should be based on the manufacturer’s recommendations, the age of the equipment, and the operating conditions. Some of the tasks that should be included in the plan are:
- Inspections of the separator motor, drive, filter, system, vibration, and noise
- Cleaning of the separator and its components
- Lubrication of bearings, seals, and other moving parts
- Repair and replacement of worn or damaged parts
- Calibration and testing of controls and sensors
Recommended frequency of inspections and maintenance tasks
The frequency of inspections and maintenance tasks should be determined based on the manufacturer’s recommendations, the age of the equipment, and the operating conditions. In general, more frequent inspections and maintenance tasks are required for older equipment and equipment that operates in harsh conditions. The frequency of maintenance tasks should be documented in the preventive maintenance plan.
Recording and tracking maintenance activities
It is important to record and track all maintenance activities performed on the separator. This information can be used to identify trends and potential issues, track maintenance costs, and provide documentation for regulatory compliance. A maintenance log or software program should be used to document all maintenance activities and record any issues that are identified during inspections.
3. Benefits of Preventive Maintenance for Separators
Preventive maintenance offers several benefits for separators:
- Improved reliability and productivity
- Reduced maintenance costs
- Extended equipment life
- Improved safety and compliance with regulations
- Reduced downtime and production losses
4. Tools and Techniques for Preventive Maintenance for Separators
Several tools and techniques are available for preventive maintenance for separators. These include cleaning and lubrication methods, inspection and testing procedures, repair and replacement guidelines, and condition monitoring techniques.
Overview of tools and techniques
Tools and techniques that are commonly used for preventive maintenance for separators include:
- Cleaning brushes, solvents, and degreasers
- Lubrication equipment, such as grease guns and oilers
- Inspection equipment, such as borescopes and vibration analyzers
- Testing equipment, such as pressure gauges and thermometers
- Condition monitoring equipment, such as sensors and data loggers
Cleaning and Lubrication Methods
Proper cleaning and lubrication are essential for maintaining the performance and longevity of the separator. Cleaning should be performed regularly to remove dirt, dust, and other contaminants from the separator and its components. Lubrication should be performed according to the manufacturer’s recommendations using the appropriate lubricant.
Inspection and Testing Procedures
Regular inspections and testing are necessary to identify potential issues with the separator before they become major problems. Some common inspection and testing procedures include:
- Visual inspections of the separator and its components
- Vibration analysis to detect issues with bearings and other rotating components
- Pressure testing to detect leaks and other issues with the separator
- Thermal imaging to detect issues with overheating components
Repair and Replacement Guidelines
If issues are identified during inspections or testing, it is important to repair or replace the affected components as soon as possible to prevent further damage to the separator. Guidelines for repair and replacement should be established based on the manufacturer’s recommendations and the severity of the issue. In some cases, it may be more cost-effective to replace the entire separator rather than attempting to repair it.
Condition Monitoring Techniques
Condition monitoring techniques are used to assess the condition of the separator and its components in real-time. Some common condition monitoring techniques include:
Vibration analysis to detect issues with bearings and other rotating components
- Identify abnormal vibration levels
- Detect bearing wear and misalignment
- Diagnose issues with the separator motor and drive
- Prevent catastrophic failure
Oil analysis to detect issues with the lubrication system
- Identify contaminants in the oil
- Detect wear particles from the separator components
- Determine the oil’s viscosity and acidity
- Prevent lubrication-related failures
Thermography to detect issues with the separator’s electrical components
- Identify overheating components
- Detect issues with electrical connections and insulation
- Prevent electrical-related failures
Ultrasound to detect issues with the separator’s compressed air system
- Identify leaks in the compressed air system
- Detect issues with the compressor and other components
- Prevent compressed air-related failures
Infrared thermography to detect issues with the separator’s insulation and heating elements
- Identify overheating components
- Detect issues with insulation and heating elements
- Prevent insulation and heating-related failures
5. Developing a Preventive Maintenance Program for Separators
Developing a comprehensive preventive maintenance program for separators involves several steps, including identifying critical separators and equipment, researching OEM manuals and recommendations, factoring operational conditions, establishing maintenance schedules and tasks, and developing a system for tracking and recording maintenance activities.
Identifying critical Separators and equipment
The first step in developing a preventive maintenance program for separators is to identify the critical separators and equipment that are essential to the production process. These may include separators that are used in high-throughput operations or that are difficult or expensive to replace.
Researching OEM Manuals and recommendations
The manufacturer’s recommendations for maintenance should be used as a starting point for developing a preventive maintenance plan. OEM manuals and recommendations can provide valuable information on the components and subsystems of the separator, the recommended maintenance intervals, and the required maintenance tasks.
Factoring Operational Conditions
The preventive maintenance plan should take into account the operational conditions of the separator, including the age of the equipment, the operating conditions, and the past failure history. Older equipment or equipment that operates in harsh conditions may require more frequent maintenance.
Establishing maintenance schedules and tasks
The preventive maintenance plan should include a schedule of inspections and maintenance tasks for each separator and component. The frequency of inspections and maintenance tasks should be based on the manufacturer’s recommendations, the age of the equipment, and the operating conditions. The plan should also include a list of maintenance tasks for each inspection, including cleaning, lubrication, inspection, and testing procedures.
Developing a system for tracking and recording maintenance activities
A system should be developed to track and record all maintenance activities performed on the separator. This system should include a maintenance log or software program to document all maintenance activities and record any issues that are identified during inspections. The system should also include a method for tracking maintenance costs and identifying trends and potential issues.
6. Preventive Maintenance for Specific Separator Types
Preventive maintenance for specific separator types may vary depending on the design and components of the separator. Some common separator types and their associated maintenance requirements are:
Centrifugal Separators
- Regular inspection of the separator bowl and its components
- Cleaning and lubrication of the bowl bearings and seals
- Inspection and replacement of the bowl gaskets and o-rings
- Testing of the separator’s vibration levels
Magnetic Separators
- Regular inspection of the magnet and its components
- Cleaning and lubrication of the magnet bearings and seals
- Inspection and replacement of the magnet gaskets and o-rings
- Testing of the separator’s magnetic field strength
Gas Separators
- Regular inspection of the separator housing and its components
- Cleaning and lubrication of the separator valves and regulators
- Inspection and replacement of the separator filters and membranes
- Testing of the separator’s pressure and flow rates
Electric Separators
- Regular inspection of the separator motor and its components
- Cleaning and lubrication of the motor bearings and seals
- Inspection and replacement of the motor brushes and commutator
- Testing of the separator’s electrical components, including the wiring and controls
Conveyor Separators
- Regular inspection of the conveyor belt and its components
- Cleaning and lubrication of the conveyor bearings and rollers
- Inspection and replacement of the conveyor belts and chains
- Testing of the separator’s alignment and tensioning
7. Best Practices for Preventive Maintenance for Separators
Following best practices for preventive maintenance for separators can help to ensure maximum reliability and performance. Some key best practices include:
- Regular inspections and cleaning
- Proper lubrication and fluid levels
- Monitoring and analyzing Separator performance data
8. Measuring the Efficiency of Preventive Maintenance for Separators
Key performance indicators (KPIs) should be used to measure the efficiency of preventive maintenance for separators. Some common KPIs include:
- Downtime reduction
- Reliability improvement
- Productivity improvement
- Efficiency improvement
- Cost savings
- Reduction in emergency repairs
- Improvement in safety
- Optimization of maintenance schedules
9. Role of CMMS
Computerized maintenance management systems (CMMS) can be used to manage the preventive maintenance program for separators. A CMMS can help to automate the preventive maintenance process, including master data management, equipment history, preventive maintenance scheduling and tracking, operational technology integration, and KPIs monitoring.
- Master Data Management
- Equipment History
- Preventive Maintenance Scheduling and Tracking
- Operational Technology Integration and Condition Based Maintenance
- KPIs Monitoring
10. Conclusion
Defining a preventive maintenance program for separators is an essential part of plant maintenance and asset management. A comprehensive preventive maintenance program can help to improve the reliability, performance, and safety of separators, reduce downtime, and lower maintenance costs. By following the best practices for preventive maintenance and using condition monitoring techniques and CMMS, plant maintenance and asset management professionals can ensure that separators operate at peak efficiency and provide maximum value to the organization.
Request a one-one demo with our solution engineering team.
Request a one-one demo with our solution engineering team.
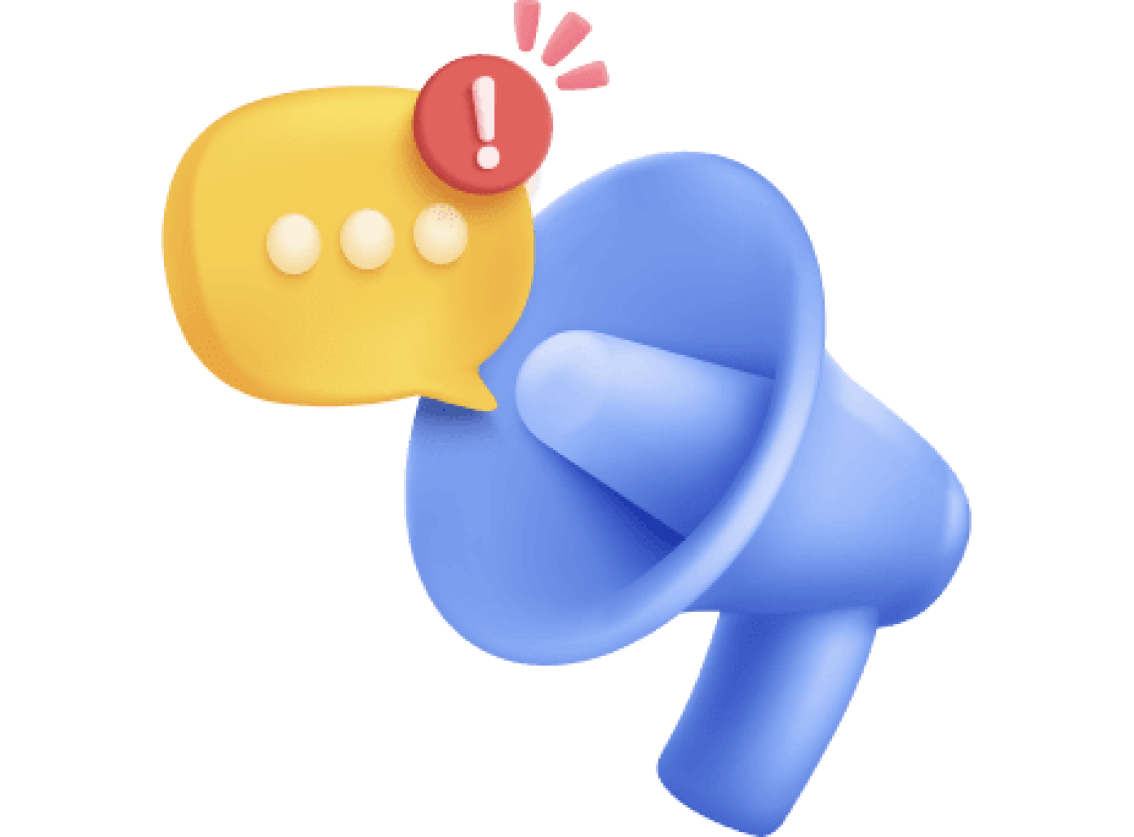