Preventive Maintenance Program for Material Handling Equipment
Preventive Maintenance Program for Material Handling Equipment
The Complete Guide to Defining Your Preventive Maintenance Program for Material Handling Equipment
Table of Contents
ToggleAs a plant maintenance expert, you know that maintaining your material handling equipment is critical to your plant’s success. One way to ensure that your equipment operates efficiently and safely is to implement a preventive maintenance program. In this guide, we’ll cover all the aspects of creating a preventive maintenance program for material handling equipment that will help you achieve optimal results.
1. Introduction to Preventive Maintenance for Material Handling Equipment
Overview Preventive Maintenance for Material
Handling Equipment
Preventive maintenance refers to the practice of regularly inspecting and maintaining equipment to prevent breakdowns, reduce downtime, and increase productivity. For material handling equipment, it involves performing routine inspections, cleaning, lubrication, and repairs to ensure optimal performance and extend the equipment’s service life.
Importance of Preventive Maintenance for Material Handling Equipment
Preventive maintenance is critical for material handling equipment because it helps to:
- Reduce downtime and repair costs
- Improve equipment reliability and safety
- Maximize equipment productivity and efficiency
- Ensure compliance with regulations and standards
- Extend equipment service life
Sub-assemblies and Components of Material Handling Equipment
Material handling equipment comprises various sub-assemblies and components that require regular maintenance. These include:
- Drive and power transmission systems
- Hydraulic systems
- Electrical systems
- Control systems
- Structural components
2. Components of a Preventive Maintenance Plan for Material Handling Equipment
Scheduled inspections and maintenance tasks
A preventive maintenance plan for material handling equipment should include scheduled inspections and maintenance tasks. These tasks should cover all the equipment’s sub-assemblies and components and should be performed at regular intervals.
Recommended frequency of inspections and maintenance tasks
The frequency of inspections and maintenance tasks should be based on the equipment’s service manual recommendations and operational conditions. For example, equipment operating under harsh conditions may require more frequent maintenance than equipment operating under normal conditions.
Recording and tracking maintenance activities
A preventive maintenance plan should also include a system for recording and tracking maintenance activities. This system should capture information about maintenance tasks performed, parts replaced, and any issues identified during inspections. This information can be used to optimize maintenance schedules, improve equipment reliability, and track maintenance costs.
Benefits of Preventive Maintenance for Material Handling Equipment
Implementing a preventive maintenance program for material handling equipment can bring numerous benefits to your plant. Some of these benefits include:
- Optimized equipment reliability: Preventive maintenance ensures that your equipment is operating efficiently, reducing the risk of unexpected downtime.
- Cost-effective maintenance: Preventive maintenance reduces the need for costly emergency repairs and
minimizes equipment downtime, leading to cost savings for your plant. - Compliance with regulations: A well-implemented preventive maintenance program can help your plant stay compliant with industry regulations and safety standards.
- Increased equipment service life: Regular maintenance can extend your equipment’s service life, allowing you to get the most out of your investment.
- Improved equipment productivity: Preventive maintenance helps to keep your equipment operating at peak performance, improving productivity and throughput.
3. Tools and Techniques for Preventive Maintenance for Material Handling Equipment
Overview of tools and techniques
Preventive maintenance for material handling equipment involves various tools and techniques, including:
- Cleaning and lubrication methods
- Inspection and testing procedures
- Repair and replacement guidelines
- Condition monitoring techniques
Cleaning and Lubrication Methods
Cleaning and lubrication are essential preventive maintenance tasks for material handling equipment. Proper cleaning and lubrication can prevent wear and tear on equipment components and reduce the risk of breakdowns. Some commonly used cleaning and lubrication methods include:
- Using the right cleaning agents and lubricants for each component
- Following recommended cleaning and lubrication schedules
- Performing visual inspections of components to detect signs of wear and damage
Inspection and Testing Procedures
Regular inspections and testing of material handling equipment can help detect issues early and prevent more significant problems from occurring. Some commonly used inspection and testing procedures include:
- Visual inspections of components and systems
- Non-destructive testing techniques such as ultrasonic, magnetic particle, and dye penetrant testing
- Vibration analysis
- Infrared thermography
4.Repair and Replacement Guidelines
When issues are detected during inspections, it is important to follow established repair and replacement guidelines. These guidelines should be based on the equipment manufacturer’s recommendations and should cover all components and sub-assemblies.
Condition Monitoring Techniques
Condition monitoring techniques can help detect potential issues before they cause equipment breakdowns. Some commonly used condition monitoring techniques include:
- Vibration analysis
- Infrared thermography
- Oil analysis
- Acoustic emission testing
- Ultrasonic testing
By implementing these tools and techniques, you can ensure that your preventive maintenance program is effective and comprehensive.
5. Developing a Preventive Maintenance Program for Material Handling Equipment
Identifying critical Material Handling Equipment and equipment
The first step in developing a preventive maintenance program for material handling equipment is to identify the critical equipment and components that require maintenance. This includes equipment that is essential to plant operations and those that are prone to breakdowns or failures.
Researching OEM Manuals and recommendations
Once you have identified the critical equipment, you should research the equipment manufacturer’s manuals and recommendations. These documents will provide guidance on recommended maintenance schedules, tasks, and procedures.
Factoring Operational Conditions
When developing a preventive maintenance program, it is essential to consider the operational conditions of the equipment. This includes factors such as the age of the equipment, operating conditions, and past failure history. By factoring in these operational conditions, you can develop a maintenance program that is tailored to your specific equipment and plant environment.
Establishing maintenance schedules and tasks
Based on your research and operational conditions, you should establish a maintenance schedule and tasks for each piece of critical equipment. This schedule should include regular inspections, cleaning, lubrication, and repairs as needed.
Developing a system for tracking and recording maintenance activities
Finally, you should develop a system for tracking and recording all maintenance activities. This system should capture information about maintenance tasks performed, parts replaced, and any issues identified during inspections. By tracking and recording this information, you can optimize your maintenance schedules, improve equipment reliability, and track maintenance costs.
6. Preventive Maintenance for Specific Material Handling Equipment Types
Material handling equipment comes in various types, and each type requires specific preventive maintenance activities. Here are some preventive maintenance activities that should be carried out for the following types of equipment:
Forklifts
Forklifts are a common type of material handling equipment used in many industries. Preventive maintenance activities for forklifts include:
- Checking fluid levels and topping off as needed
- Inspecting tires for wear and damage
- Cleaning and inspecting brakes
- Checking lift chains and forks for wear and damage
Conveyor Systems
Conveyor systems are another critical type of material handling equipment. Preventive maintenance activities for conveyor systems include:
- Inspecting and cleaning rollers and bearings
- Checking belt tension and alignment
- Inspecting and replacing worn or damaged belts
- Cleaning and lubricating motors and gearboxes
Cranes
Cranes are essential in many industries, and preventive maintenance is critical to their safe and efficient operation. Preventive maintenance activities for cranes include:
- Inspecting and lubricating hoist chains and wire ropes
- Checking fluid levels and topping off as needed
- Cleaning and inspecting brakes
- Inspecting and replacing worn or damaged cables and slings
Pallet Jacks
Pallet jacks are commonly used in warehouses and distribution centers to move heavy loads. Preventive maintenance activities for pallet jacks include:
- Checking fluid levels and topping off as needed
- Inspecting tires for wear and damage
- Cleaning and inspecting brakes
- Inspecting and lubricating forks and lift cylinders
7. Best Practices for Preventive Maintenance for Material Handling Equipment
Importance of best practices
Implementing best practices for preventive maintenance can help to optimize your equipment reliability, safety, and productivity. Here are some best practices to consider:
Regular inspections and cleaning
Regular inspections and cleaning
are critical to keeping your material handling equipment operating at peak performance. By identifying and addressing issues early, you can prevent more significant problems from occurring and minimize equipment downtime.
Proper lubrication and fluid levels
Proper lubrication and fluid levels are essential to the safe and efficient operation of material handling equipment. Ensure that you are using the right lubricants for each component and that fluid levels are checked and topped off regularly.
Monitoring and analyzing Material Handling Equipment performance data
Monitoring and analyzing equipment performance data can help you detect issues early and optimize your preventive maintenance program. By tracking metrics such as equipment runtime, vibration, and temperature, you can identify trends and patterns that may indicate impending issues.
8. Measuring the Efficiency of Preventive Maintenance for Material Handling Equipment
Importance of KPI
Key performance indicators (KPIs) are critical for measuring the efficiency and effectiveness of your preventive maintenance program. By tracking KPIs, you can identify areas for improvement and optimize your program over time.
Key Performance Indicators
Here are some essential KPIs to track for your preventive maintenance program:
- Downtime: Measure the total amount of equipment downtime and track the causes.
- Cost of maintenance: Track the total cost of maintenance activities, including labor, parts, and outside contractors.
- Equipment reliability: Measure the overall reliability of your equipment, including the mean time between failures (MTBF) and mean time to repair (MTTR).
- Maintenance compliance: Track compliance with maintenance schedules and tasks to ensure that all critical equipment is properly maintained.
- Maintenance backlog: Measure the number of maintenance tasks that are overdue or have not been completed.
- Safety incidents: Track the number and severity of safety incidents related to equipment failure or malfunction.
- Equipment utilization: Measure the utilization of your equipment to identify opportunities for optimization and improvement.
- Maintenance cost per unit: Track the cost of maintenance per unit of output to ensure that maintenance activities are cost-effective.
9. Role of CMMS
Master Data Management
A computerized maintenance management system (CMMS) can be an essential tool for implementing a comprehensive preventive maintenance program. A CMMS can help you manage master data such as equipment information, maintenance schedules, and task lists.
Equipment History
A CMMS can also help you track equipment history, including maintenance activities, repairs, and replacement of components. By tracking this information, you can identify trends and patterns and optimize your preventive maintenance program over time.
Preventive Maintenance Scheduling and Tracking
A CMMS can help you schedule and track preventive maintenance tasks, ensuring that critical equipment is properly maintained and reducing the risk of breakdowns and failures.
Operational Technology Integration and Condition Based Maintenance
A CMMS can integrate with operational technology such as sensors and data analytics tools to enable condition-based maintenance. By monitoring equipment performance data in real-time, a CMMS can trigger maintenance activities based on the actual condition of the equipment, rather than on a fixed schedule.
KPIs Monitoring
A CMMS can also help you monitor and track KPIs related to your preventive maintenance program, allowing you to identify areas for improvement and optimize your program over time.
10. Conclusion
Implementing a comprehensive preventive maintenance program for material handling equipment is critical to ensuring equipment reliability, safety, and productivity. By following the key components and best practices outlined in this guide, you can develop a program that is tailored to your specific equipment and plant environment. Remember to track and monitor KPIs related to your program to ensure that you are achieving the desired results and to optimize your program over time. A CMMS can be an essential tool for implementing a comprehensive preventive maintenance program, helping you manage equipment information, track maintenance history, schedule preventive maintenance tasks, and integrate with operational technology for condition-based maintenance.
Request a one-one demo with our solution engineering team.
Request a one-one demo with our solution engineering team.
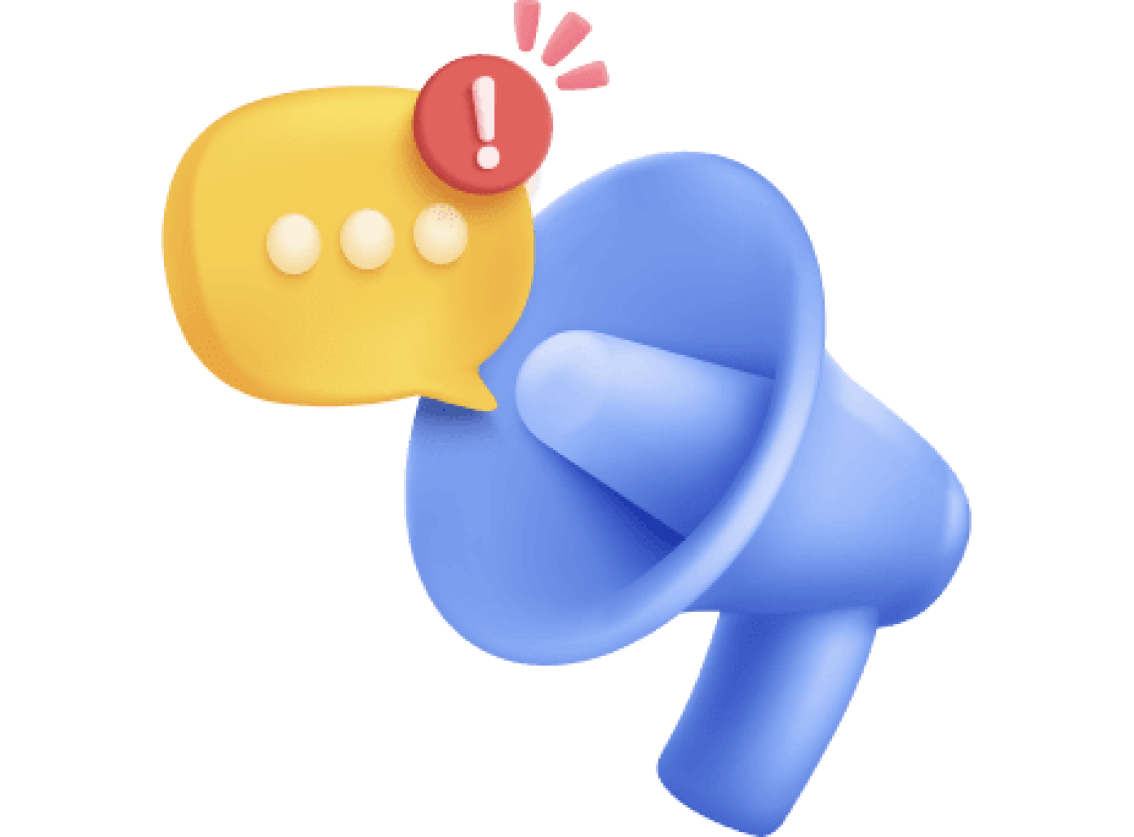