Preventive Maintenance Program for Generators
Preventive Maintenance Program for Generators
The Complete Guide to Defining Your Preventive Maintenance Program for Generators
Table of Contents
Toggle1. Introduction to Preventive Maintenance for Generators
Preventive maintenance for generators is an essential aspect of asset management and plant maintenance. In this comprehensive guide, we will cover everything you need to know about creating an effective preventive maintenance program for generators.
Overview of Preventive Maintenance for Generators
Preventive maintenance is a proactive approach to maintaining equipment to prevent unexpected failures and minimize downtime. For generators, preventive maintenance involves regularly scheduled inspections, maintenance tasks, and repair/replacement activities to ensure that the generator operates at peak performance levels.
Importance of Preventive Maintenance for Generators
Preventive maintenance is critical for generators for several reasons:
- Maximizes the lifespan of the generator
- Reduces the risk of unexpected failures
- Improves the reliability and performance of the generator
- Minimizes repair costs
- Ensures compliance with regulations and safety standards
Sub-assemblies and Components of Generators
Generators are complex machines that are made up of several sub-assemblies and components. The key sub-assemblies and components of generators include:
- Engine
- Alternator
- Control System
- Fuel System
- Cooling System
- Exhaust System
2. Components of a Preventive Maintenance Plan for Generators
A preventive maintenance plan for generators should include the following components:
Scheduled inspections and maintenance tasks
Regular inspections and maintenance tasks should be scheduled to ensure that the generator is in good working order. These tasks should include:
- Checking fluid levels
- Inspecting belts and hoses
- Inspecting and cleaning air filters
- Checking battery terminals and connections
- Checking fuel levels and filters
Recommended frequency of inspections and maintenance tasks
The frequency of inspections and maintenance tasks will depend on the specific generator and its operating conditions. However, a general rule of thumb is that preventive maintenance tasks should be performed every 200 to 300 hours of operation.
Recording and tracking maintenance activities
All maintenance activities should be recorded and tracked to ensure that the generator is being properly maintained. This information can be used to identify trends and patterns in generator performance and to plan for future maintenance activities.
3. Benefits of Preventive Maintenance for Generators
Here are the top five benefits of preventive maintenance for generators:
Maximizes Generator Lifespan
Preventive maintenance helps to extend the lifespan of a generator by identifying and correcting issues before they become major problems.
Reduces Unexpected Failures
Regular maintenance helps to reduce the risk of unexpected failures, which can be costly and time-consuming to repair.
Improves Reliability and Performance
Preventive maintenance helps to ensure that the generator operates at peak performance levels, which improves its reliability and performance.
Minimizes Repair Costs
Preventive maintenance can help to identify and correct issues before they become major problems, which can save on repair costs in the long run.
Ensures Compliance with Regulations and Safety Standards
Preventive maintenance helps to ensure that the generator is in compliance with regulations and safety standards, which is important for maintaining a safe work environment.
4. Tools and Techniques for Preventive Maintenance for Generators
Here are some of the tools and techniques that are used for preventive maintenance for generators:
Cleaning and Lubrication Methods
Generators should be regularly cleaned and lubricated to ensure that they operate at peak performance levels. The specific cleaning and lubrication methods will depend on the type of generator and its operating conditions.
Inspection and Testing Procedures
Regular inspections and testing procedures should be performed to ensure that the generator is in good working order. These procedures may include visual inspections, electrical testing, and vibration analysis.
Repair and Replacement Guidelines
Guidelines should be established for repairing or replacing components of the generator when necessary. These guidelines may include specific repair procedures, replacement schedules, and criteria for replacement.
Condition Monitoring Techniques
Condition monitoring techniques can be used to identify potential issues with the generator before they become major problems. Some of these techniques include oil analysis, thermography, and ultrasonic testing.
5. Developing a Preventive Maintenance Program for Generators
Here are the steps involved in developing a preventive maintenance program for generators:
Identifying Critical Generators and Equipment
The first step in developing a preventive maintenance program is to identify the critical generators and equipment that require maintenance. This may involve prioritizing equipment based on its importance to the business, its age, or its operating conditions.
Researching OEM Manuals and Recommendations
OEM manuals and recommendations should be consulted to determine the specific maintenance requirements for each generator and piece of equipment. These manuals will provide information on recommended maintenance schedules, maintenance tasks, and other important information.
Factoring Operational Conditions
The operational conditions of the generator should be factored in when developing a preventive maintenance program. This may include the age of the equipment, the operating environment, and the history of past failures.
Establishing Maintenance Schedules and Tasks
Maintenance schedules and tasks should be established based on the specific requirements of each generator and piece of equipment. This may involve creating a maintenance calendar that includes regular inspections and maintenance tasks.
Developing a System for Tracking and Recording Maintenance Activities
All maintenance activities should be recorded and tracked to ensure that the generator is being properly maintained. This information can be used to identify trends and patterns in generator performance and to plan for future maintenance activities.
6. Preventive Maintenance for Specific Generator Types
Here are some of the specific preventive maintenance activities that are recommended for different types of generators:
Diesel Generators
- Regular oil changes and filter replacements
- Regular fuel filter replacements
- Inspection of the fuel system for leaks or damage
- Inspection of the air intake system for damage or blockages
Standby Generators
- Regular testing of the automatic transfer switch
- Inspection of the battery and battery charger
- Inspection of the control panel for damage or wear
- Regular load testing
Emergency Generators
- Regular inspection and testing of the fuel system
- Regular inspection and testing of the cooling system
- Regular inspection and testing of the electrical system
- Inspection of the battery and battery charger
Commercial Generators
- Regular oil changes and filter replacements
- Regular fuel filter replacements
- Inspection of the fuel system for leaks or damage
- Inspection of the air intake system for damage or blockages
Industrial Generators
- Regular inspection and testing of the fuel system
- Regular inspection and testing of the cooling system
- Regular inspection and testing of the electrical system
- Inspection of the battery and battery charger
Home Generators
- Regular oil changes and filter replacements
- Regular fuel filter replacements
- Inspection of the fuel system for leaks or damage
- Inspection of the air intake system for damage or blockages
7. Best Practices for Preventive Maintenance for Generators
Here are some best practices for preventive maintenance for generators:
Regular Inspections and Cleaning
Regular inspections and cleaning should be performed to ensure that the generator is in good working order. This includes checking fluid levels, inspecting belts and hoses, and cleaning air filters.
Proper Lubrication and Fluid Levels
The generator should be properly lubricated and fluid levels should be checked regularly to ensure that it operates at peak performance levels.
Monitoring and Analyzing Generator Performance Data
Generator performance data should be monitored and analyzed to identify potential issues before they become major problems. This includes tracking fuel consumption, oil consumption, and other key performance indicators.
8. Measuring the Efficiency of Preventive Maintenance for Generators
Here are some key performance indicators that can be used to measure the efficiency of preventive maintenance for generators:
Availability
The availability of the generator measures the percentage of time that the generator is available for use. This is an important indicator of the effectiveness of preventive maintenance.
Reliability
The reliability of the generator measures the percentage of time that the generator operates without failure. This is an important indicator of the effectiveness of preventive maintenance.
Maintenance Cost
The maintenance cost of the generator measures the total cost of maintaining the generator over a specific period of time. This is an important indicator of the cost-effectiveness of preventive maintenance.
Mean Time Between Failures
The mean time between failures measures the average time between failures of the generator. This is an important indicator of the effectiveness of preventive maintenance.
Mean Time to Repair
The mean time to repair measures the average time it takes to repair the generator after a failure. This is an important indicator of the efficiency of maintenance activities.
9. Role of CMMS
Computerized maintenance management systems (CMMS) can be used to streamline and improve the effectiveness of preventive maintenance for generators. Here are some of the ways that CMMS can be used:
Master Data Management
CMMS can be used to manage master data for generators and equipment, including specifications, maintenance schedules, and repair histories.
Equipment History
CMMS can be used to track the maintenance history of generators and equipment, including maintenance activities, repairs, and inspections.
Preventive Maintenance Scheduling and Tracking
CMMS can be used to schedule and track preventive maintenance activities, including inspections, lubrication, and cleaning.
Operational Technology Integration and Condition-Based Maintenance
CMMS can be integrated with operational technology to enable condition-based maintenance. This involves using sensors and other devices to monitor the performance of the generator and trigger maintenance activities when necessary.
KPI Monitoring
CMMS can be used to monitor key performance indicators, including availability, reliability, maintenance cost, mean time between failures, and mean time to repair.
10. Conclusion
Preventive maintenance is an important aspect of asset management and plant maintenance, especially when it comes to generators. By developing a comprehensive preventive maintenance program, using the right tools and techniques, and measuring key performance indicators, businesses can ensure that their generators operate at peak performance levels and avoid costly downtime due to unexpected failures.
Request a one-one demo with our solution engineering team.
Request a one-one demo with our solution engineering team.
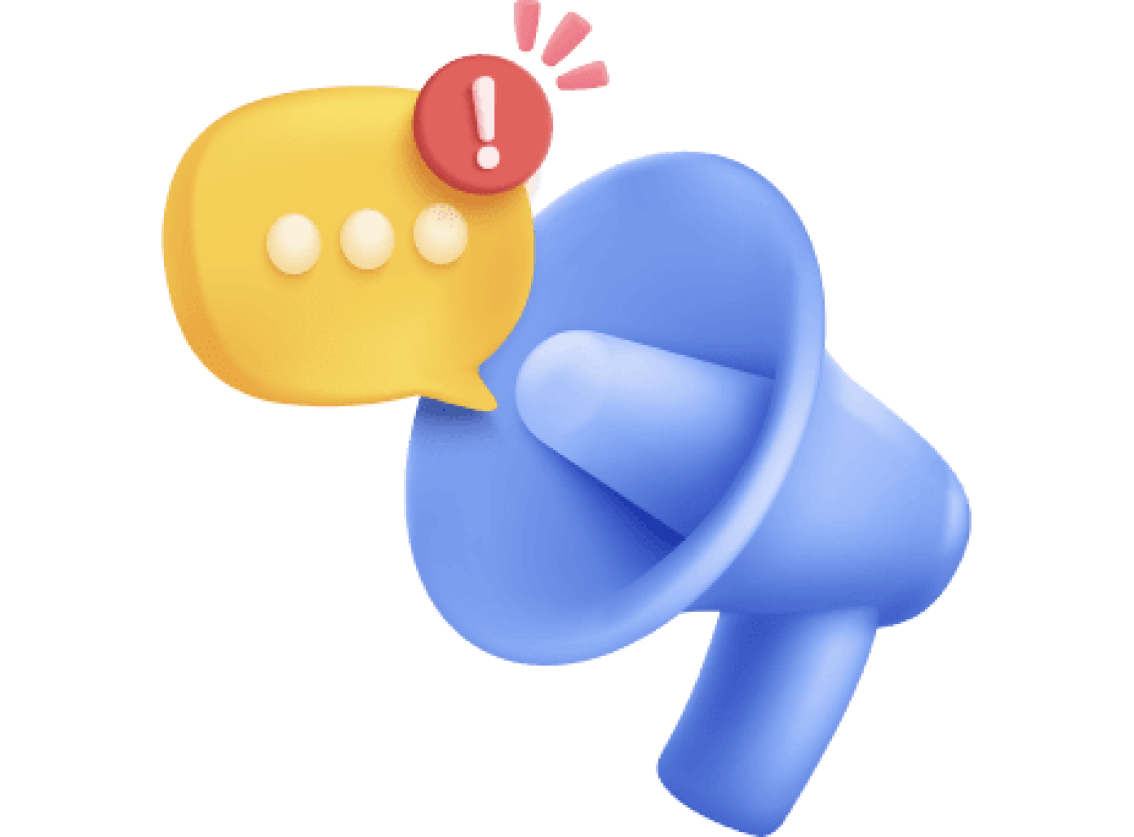