Preventive Maintenance Program for Filters
Preventive Maintenance Program for Filters
The Complete Guide to Defining Your Preventive Maintenance Program for Filters
Table of Contents
Toggle1. Introduction to Preventive Maintenance for Filters
Preventive maintenance for filters involves the regular inspection, cleaning, and replacement of filters in order to increase their performance, reliability, and uptime. This guide will provide an overview of preventive maintenance for filters, explain its importance, and describe the sub-assemblies and components of filters.
Overview of Preventive Maintenance for Filters
Preventive maintenance for filters is an essential part of plant maintenance and asset management. It involves a planned and proactive approach to filter maintenance, as opposed to a reactive approach that only addresses problems after they occur. By implementing a preventive maintenance program for filters, you can avoid unexpected downtime, reduce repair costs, and increase the lifespan of your equipment.
Importance of Preventive Maintenance for Filters
Preventive maintenance for filters is important for several reasons:
- Improved equipment performance
- Increased equipment reliability
- Reduced equipment downtime
- Lower maintenance costs
- Extended equipment lifespan
Sub-assemblies and Components of Filters
Filters are composed of various sub-assemblies and components, including:
- Filter media
- Filter housing
- Gaskets and seals
- Fasteners
- Mounting brackets
- Drain valves
- Pressure gauges
2. Components of a Preventive Maintenance Plan for Filters
A preventive maintenance plan for filters should include the following components:
Scheduled Inspections and Maintenance Tasks
Scheduled inspections and maintenance tasks are a crucial part of a preventive maintenance plan for filters. Regular inspections can help you identify potential problems before they lead to equipment failure, while maintenance tasks such as cleaning and lubrication can keep your filters running smoothly.
Recommended Frequency of Inspections and Maintenance Tasks
The frequency of inspections and maintenance tasks will depend on the type of filter, its operating conditions, and the manufacturer’s recommendations. Generally, filters should be inspected at least once a month and maintenance tasks such as cleaning and lubrication should be carried out on a regular basis.
Recording and Tracking Maintenance Activities
Recording and tracking maintenance activities is an important part of a preventive maintenance plan for filters. By keeping a record of all maintenance activities, you can track your progress and identify areas where improvements can be made. This information can also be used to plan future maintenance activities and schedule them at appropriate intervals.
Benefits of Preventive Maintenance for Filters
Preventive maintenance for filters offers several benefits, including:
Improved Equipment Performance
Regular maintenance can help ensure that filters are operating at peak performance, which can lead to improved equipment performance and efficiency.
Increased Equipment Reliability
Preventive maintenance can help reduce the risk of unexpected downtime due to equipment failure, which can increase equipment reliability and availability.
Reduced Equipment Downtime
By addressing potential problems before they lead to equipment failure, preventive maintenance can help reduce equipment downtime and associated repair costs.
Lower Maintenance Costs
Preventive maintenance can help identify potential problems early, before they lead to more serious and costly issues.
Extended Equipment Lifespan
Regular maintenance can help extend the lifespan of equipment by reducing the wear and tear caused by normal operation.
3. Tools and Techniques for Preventive Maintenance for Filters
There are several tools and techniques that can be used to implement a preventive maintenance program for filters:
Cleaning and Lubrication Methods
Regular cleaning and lubrication can help keep filters operating at peak performance. Some common cleaning and lubrication methods include:
- Chemical cleaning
- Mechanical cleaning
- Ultrasonic cleaning
- Dry cleaning
- Applying lubricants to moving parts
Inspection and Testing Procedures
Regular inspection and testing can help identify potential problems before they lead to equipment failure. Some common inspection and testing procedures include:
- Visual inspection
- Pressure drop measurement
- Filter efficiency testing
- Flow rate testing
- Particle size analysis
4. Repair and Replacement Guidelines
Repair and replacement guidelines should be established for each type of filter based on the manufacturer’s recommendations and industry best practices. Some common repair and replacement guidelines include:
- Replacing filters at recommended intervals
- Replacing damaged or worn components
- Repairing leaks and other damage
- Replacing filters that have reached the end of their useful life
Condition Monitoring Techniques
Condition monitoring techniques can help identify potential problems before they lead to equipment failure. Some common condition monitoring techniques include:
- Vibration analysis
- Oil analysis
- Thermography
- Acoustic emissions testing
- Ultrasound testing
5. Developing a Preventive Maintenance Program for Filters
To develop a preventive maintenance program for filters, follow these steps:
Identifying Critical Filters and Equipment
The first step in developing a preventive maintenance program for filters is to identify the critical filters and equipment that require regular maintenance.
Researching OEM Manuals and Recommendations
Research the original equipment manufacturer (OEM) manuals and recommendations for each type of filter to ensure that maintenance tasks are carried out according to their specifications.
Factoring Operational Conditions
Operational conditions such as the age of the equipment, operating conditions, and past failure history should be taken into account when developing a maintenance plan.
Establishing Maintenance Schedules and Tasks
Based on the information gathered, establish a maintenance schedule and list of tasks to be carried out for each type of filter.
Developing a System for Tracking and Recording Maintenance Activities
Develop a system for tracking and recording all maintenance activities, including the date of the activity, the person who carried out the activity, and any notes or comments regarding the activity.
6. Preventive Maintenance for Specific Filter Types
Each type of filter requires specific preventive maintenance activities. Here are some examples:
Air Filters
Air filters should be inspected and cleaned or replaced on a regular basis to prevent dirt and debris from clogging the filter and reducing airflow. In addition, the air filter housing should be inspected for leaks and damage, and the filter should be replaced if any issues are found.
Oil Filters
Oil filters should be replaced at regular intervals to prevent contamination of the oil system. In addition, the oil filter housing should be inspected for leaks and damage, and the filter should be replaced if any issues are found.
Hydraulic Filters
Hydraulic filters should be inspected and cleaned or replaced on a regular basis to prevent dirt and debris from clogging the filter and reducing hydraulic fluid flow. In addition, the hydraulic filter housing should be inspected for leaks and damage, and the filter should be replaced if any issues are found.
Fuel Filters
Fuel filters should be replaced at regular intervals to prevent contamination of the fuel system. In addition, the fuel filter housing should be inspected for leaks and damage, and the filter should be replaced if any issues are found.
7. Best Practices for Preventive Maintenance for Filters
Here are some best practices for preventive maintenance for filters:
Regular Inspections and Cleaning
Filters should be inspected and cleaned on a regular basis to prevent dirt and debris from clogging the filter and reducing airflow or fluid flow.
Proper Lubrication and Fluid Levels
Lubrication and fluid levels should be checked on a regular basis to ensure that filters are operating at peak performance.
Monitoring and Analyzing Filter Performance Data
Filter performance data should be monitored and analyzed on a regular basis to identify potential problems before they lead to equipment failure.
8. Measuring the Efficiency of Preventive Maintenance for Filters
Measuring the efficiency of a preventive maintenance program for filters can be done using key performance indicators (KPIs). Here are some examples:
Filter Performance
Filter performance can be measured by comparing the pressure drop across the filter before and after maintenance tasks are carried out.
Filter Uptime
Filter uptime can be measured by tracking the amount of time that filters are in operation without experiencing downtime due to equipment failure.
Filter Maintenance Costs
Filter maintenance costs can be measured by tracking the cost of labor, parts, and other expenses associated with maintenance tasks.
Filter Reliability
Filter reliability can be measured by tracking the number of maintenance tasks required and the frequency of equipment failure.
9. Role of CMMS
A computerized maintenance management system (CMMS) can be used to manage and track preventive maintenance activities for filters. Here are some ways that a CMMS can be used:
Master Data Management
A CMMS can be used to manage master data such as equipment and filter specifications, maintenance tasks, and maintenance schedules.
Equipment History
A CMMS can be used to track the maintenance history of each piece of equipment, including the date of the last maintenance task and any notes or comments regarding the task.
Preventive Maintenance Scheduling and Tracking
A CMMS can be used to schedule preventive maintenance tasks and track their completion.
Operational Technology Integration and Condition Based Maintenance
A CMMS can be integrated with other operational technology systems to provide real-time data and enable condition-based maintenance.
KPIs Monitoring
A CMMS can be used to monitor KPIs such as filter performance, filter uptime, and filter maintenance costs.
10. Conclusion
Preventive maintenance is essential for ensuring that filters are operating at peak performance and preventing equipment failure. By following best practices for preventive maintenance and using the tools and techniques outlined in this guide, you can develop a comprehensive preventive maintenance program for filters that will help improve equipment performance and reliability, reduce equipment downtime and maintenance costs, and extend equipment lifespan.
Request a one-one demo with our solution engineering team.
Request a one-one demo with our solution engineering team.
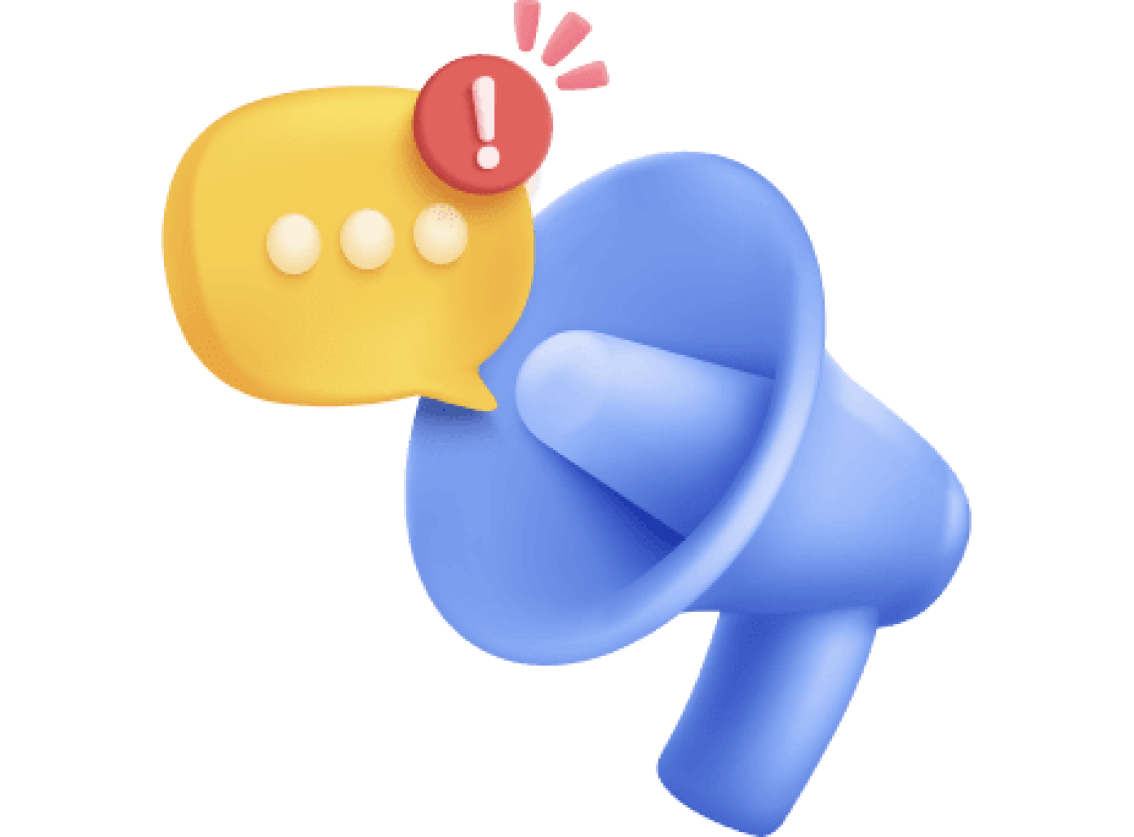