Preventive Maintenance Program for Compressors
Preventive Maintenance Program for Compressors
The Complete Guide to Defining Your Preventive Maintenance Program for Compressors
Table of Contents
Toggle1. Introduction to Preventive Maintenance for Compressors
Preventive maintenance is a crucial aspect of ensuring the reliability, safety, and efficiency of compressors. In this section, we will provide an overview of preventive maintenance for compressors, highlight its importance, and introduce the sub-assemblies and components of compressors that require maintenance.
Overview of Preventive Maintenance for Compressors
Preventive maintenance is a proactive approach to compressor maintenance that involves regularly scheduled inspections, cleaning, lubrication, testing, and repair to prevent unplanned downtime, reduce repair costs, and extend the compressor’s lifespan. A well-designed preventive maintenance program takes into account the operational conditions of the compressor, its age, and past failure history, and follows OEM manuals and recommendations.
Importance of Preventive Maintenance for Compressors
Preventive maintenance is critical for compressors for several reasons:
- Improves safety: Preventive maintenance ensures that compressors are operating safely and that safety devices and systems are functioning correctly.
- Maximizes uptime: Regular maintenance prevents unplanned downtime and ensures that compressors are available when needed.
- Reduces repair costs: Regular maintenance prevents major breakdowns, reduces repair costs, and extends the compressor’s lifespan.
- Improves efficiency: Preventive maintenance ensures that compressors are operating at peak efficiency, reducing energy consumption and costs.
- Enhances reliability: Regular maintenance improves the reliability of compressors, reducing the risk of breakdowns and failures.
Sub-assemblies and Components of Compressors
To develop an effective preventive maintenance plan for compressors, it is essential to understand the sub-assemblies and components that require maintenance. These may include:
- Air filters
- Oil filters
- Bearings
- Pistons
- Valves
- Cylinders
- Coolers
- Belts and pulleys
- Electrical systems
- Control systems
2. Components of a Preventive Maintenance Plan for Compressors
A well-designed preventive maintenance plan for compressors should include scheduled inspections and maintenance tasks, recommended frequency of inspections and maintenance tasks, and recording and tracking maintenance activities.
Scheduled Inspections and Maintenance Tasks
Scheduled inspections and maintenance tasks should be based on OEM manuals and recommendations, the compressor’s age and past failure history, and operational conditions. These may include:
- Checking air and oil filters
- Replacing air and oil filters
- Checking and adjusting belts and pulleys
- Checking and replacing worn or damaged components
- Lubrication
- Cleaning
- Testing
- Repairing or replacing components as needed
Recommended Frequency of Inspections and Maintenance Tasks
The frequency of inspections and maintenance tasks should be determined based on the compressor’s age and past failure history, operational conditions, and OEM manuals and recommendations. Typically, maintenance tasks should be performed monthly, quarterly, bi-annually, or annually, depending on the type and criticality of the compressor.
Recording and Tracking Maintenance Activities
Recording and tracking maintenance activities is essential to ensure that maintenance tasks are performed on schedule, to identify trends and issues, and to make informed decisions about repairs and replacements. This can be done using a computerized maintenance management system (CMMS) or a manual system that includes maintenance logs, work orders, and maintenance schedules.
Benefits of Preventive Maintenance for Compressors
Preventive maintenance offers several benefits for compressors. Here are the top five benefits:
Improved Safety
Preventive maintenance ensures that compressors are operating safely and that safety devices and systems are functioning correctly. This reduces the risk of accidents, injuries, and property damage.
Reduced Downtime and Repair Costs
Preventive maintenance prevents unplanned downtime and reduces the need for major repairs, reducing repair costs and downtime.
Extended Lifespan of Compressors
Regular maintenance extends the lifespan of compressors by reducing wear and tear, preventing corrosion, and ensuring that components are operating within their design limits.
Increased Efficiency
Preventive maintenance ensures that compressors are operating at peak efficiency, reducing energy consumption and costs.
Enhanced Reliability
Regular maintenance improves the reliability of compressors, reducing the risk of breakdowns and failures.
3. Tools and Techniques for Preventive Maintenance for Compressors
Effective preventive maintenance for compressors requires the use of specialized tools and techniques. In this section, we will explore some of the most common tools and techniques used in preventive maintenance for compressors.
Cleaning and Lubrication Methods
Cleaning and lubrication are essential components of preventive maintenance for compressors. Some common cleaning and lubrication methods include:
- Chemical cleaning
- Steam cleaning
- Ultrasonic cleaning
- Greasing
- Oil changes
- Oil analysis
Inspection and Testing Procedures
Inspection and testing procedures are used to identify issues and potential problems before they result in equipment failure. Some common inspection and testing procedures include:
- Vibration analysis
- Ultrasonic testing
- Thermography
- Acoustic emissions testing
- Visual inspections
- Functional testing
- Load testing
4. Repair and Replacement Guidelines
Repair and replacement guidelines help determine when components should be repaired or replaced. Some common repair and replacement guidelines include:
- Minimum thickness requirements
- Maximum wear limits
- Component life expectancy
- Manufacturer’s recommendations
Condition Monitoring Techniques
Condition monitoring techniques are used to assess the health of compressors and predict potential issues before they result in equipment failure. Some common condition monitoring techniques include:
- Vibration analysis
- Oil analysis
- Thermography
- Acoustic emissions testing
- Ultrasonic testing
- Real-time monitoring
5. Developing a Preventive Maintenance Program for Compressors
To develop an effective preventive maintenance program for compressors, it is essential to identify critical compressors and equipment, research OEM manuals and recommendations, factor in operational conditions, establish maintenance schedules and tasks, and develop a system for tracking and recording maintenance activities.
Identifying Critical Compressors and Equipment
Identifying critical compressors and equipment is essential to prioritize maintenance efforts and allocate resources effectively. Critical compressors may include those that are essential to the production process, those that are expensive to repair or replace, and those that pose safety risks if they fail.
Researching OEM Manuals and Recommendations
Researching OEM manuals and recommendations is essential to ensure that maintenance tasks are performed according to manufacturer specifications and guidelines. This may include reviewing maintenance schedules, recommended maintenance tasks, and parts lists.
Factoring Operational Conditions
Factoring operational conditions, such as the age of the equipment, operating conditions, and past failure history, is essential to determine the frequency of maintenance tasks and prioritize maintenance efforts.
Establishing Maintenance Schedules and Tasks
Establishing maintenance schedules and tasks involves determining the frequency of maintenance tasks and the specific tasks that need to be performed. This may include developing a maintenance checklist or work order that includes tasks such as cleaning, lubrication, inspection, testing, and repair.
Developing a System for Tracking and Recording Maintenance Activities
Developing a system for tracking and recording maintenance activities is essential to ensure that maintenance tasks are performed on schedule and to make informed decisions about repairs and replacements. This may include using a computerized maintenance management system (CMMS) or a manual system that includes maintenance logs, work orders, and maintenance schedules.
6. Preventive Maintenance for Specific Compressor Types
Different types of compressors require different maintenance procedures and techniques. In this section, we will explore preventive maintenance for some of the most common compressor types.
Types of Compressors
- Air compressors
- Oil-free compressors
- Oil-injected compressors
- Reciprocating compressors
- Rotary screw compressors
- Centrifugal compressors
- Portable compressors
- Stationary compressors
Preventive Maintenance for Each Type of Compressor
Air Compressors
- Clean or replace air filters
- Check and adjust belts and pulleys
- Check and replace worn or damaged components
- Lubricate components
- Clean compressor housing and cooling fins
Oil-Free Compressors
- Clean or replace air filters
- Check and adjust belts and pulleys
- Check and replace worn or damaged components
- Check and replace oil filters
- Clean compressor housing and cooling fins
Oil-Injected Compressors
- Check oil level and quality
- Change oil and filters
- Check and replace worn or damaged components
- Check and adjust belts and pulleys
- Clean compressor housing and cooling fins
Reciprocating Compressors
- Clean or replace air filters
- Check and adjust belts and pulleys
- Check and replace worn or damaged components
- Change oil and filters
- Clean compressor housing and cooling fins
Rotary Screw Compressors
- Change oil and filters
- Check and adjust belts and pulleys
- Check and replace worn or damaged components
- Clean compressor housing and cooling fins
- Inspect and clean air and oil coolers
Centrifugal Compressors
- Change oil and filters
- Inspect and clean air and oil coolers
- Check and adjust belts and pulleys
- Check and replace worn or damaged components
- Clean compressor housing and cooling fins
Portable Compressors
- Clean or replace air filters
- Check and adjust belts and pulleys
- Check and replace worn or damaged components
- Lubricate components
- Clean compressor housing and cooling fins
Stationary Compressors
- Clean or replace air filters
- Check and adjust belts and pulleys
- Check and replace worn or damaged components
- Lubricate components
- Clean compressor housing and cooling fins
7. Best Practices for Preventive Maintenance for Compressors
Adopting best practices for preventive maintenance can help improve the effectiveness and efficiency of maintenance efforts. Here are some best practices for preventive maintenance for compressors:
Regular Inspections and Cleaning
Regular inspections and cleaning are essential to ensure that compressors are operating safely and efficiently. Inspections should be conducted at least once a month, and cleaning should be performed as needed.
Proper Lubrication and Fluid Levels
Proper lubrication and fluid levels are essential to reduce wear and tear and ensure that compressors are operating efficiently. Lubrication should be performed according to manufacturer recommendations, and fluid levels should be checked regularly.
Monitoring and Analyzing Compressor Performance Data
Monitoring and analyzing compressor performance data can help identify trends and potential issues before they result in equipment failure. This can be done using a computerized maintenance management system (CMMS) or manual tracking system.
8. Measuring the Efficiency of Preventive Maintenance for Compressors
Measuring the efficiency of preventive maintenance efforts is essential to ensure that maintenance tasks are performed on schedule and to identify areas for improvement. Here are some key performance indicators (KPIs) that can be used to measure the efficiency of preventive maintenance for compressors:
Compressor Reliability
Compressor reliability is a critical KPI that measures the percentage of time that a compressor operates without failure. A high level of compressor reliability indicates that preventive maintenance efforts are effective.
Compressor Lifespan
Compressor lifespan is a KPI that measures the average lifespan of compressors in an organization. A longer compressor lifespan indicates that preventive maintenance efforts are effective and that equipment is being maintained properly.
Compressor Safety
Compressor safety is a KPI that measures the number of safety incidents related to compressors. A low number of safety incidents indicates that preventive maintenance efforts are effective in preventing equipment failures that could result in safety incidents.
Compressor Efficiency
Compressor efficiency is a KPI that measures the energy efficiency of compressors. A high level of compressor efficiency indicates that preventive maintenance efforts are effective in keeping equipment operating at peak performance.
Compressor Downtime
Compressor downtime is a KPI that measures the amount of time that compressors are offline due to maintenance or repair. A low level of compressor downtime indicates that preventive maintenance efforts are effective in reducing equipment failures and minimizing downtime.
9. Role of CMMS
A computerized maintenance management system (CMMS) is a software tool that can be used to manage preventive maintenance programs for compressors. Here are some key functions of a CMMS:
Master Data Management
A CMMS can be used to manage master data such as equipment records, parts lists, and maintenance schedules.
Equipment History
A CMMS can be used to track the maintenance history of compressors, including maintenance tasks performed, parts replaced, and downtime.
Preventive Maintenance Scheduling and Tracking
A CMMS can be used to schedule and track preventive maintenance tasks, ensuring that they are performed on schedule.
Operational Technology Integration and Condition Based Maintenance
A CMMS can be integrated with operational technology such as sensors and other monitoring equipment to enable condition-based maintenance.
KPIs Monitoring
A CMMS can be used to monitor KPIs such as compressor reliability, lifespan, safety, efficiency, and downtime, providing valuable insights into the effectiveness of preventive maintenance efforts.
10. Conclusion
Preventive maintenance is essential for compressors to operate safely and efficiently, and to minimize downtime and repair costs. A well-designed preventive maintenance program should include regular inspections and cleaning, proper lubrication and fluid levels, and monitoring of compressor performance data. By following best practices for preventive maintenance and using a CMMS to manage maintenance efforts, organizations can improve the reliability, lifespan, safety, efficiency, and cost-effectiveness of their compressors.
Request a one-one demo with our solution engineering team.
Request a one-one demo with our solution engineering team.
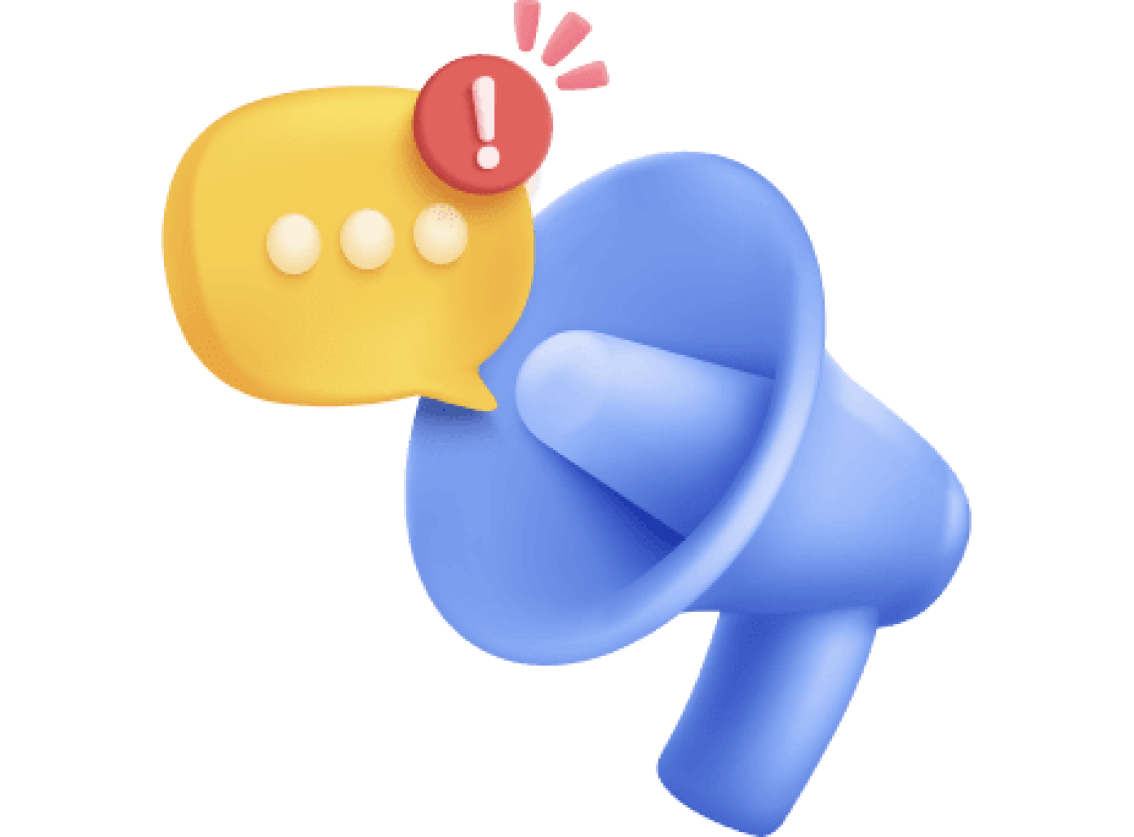