Troubleshooting Your Presses
Troubleshooting Your Presses
Table of Contents
ToggleA Step-by-Step Guide to Troubleshooting Your Presses: Maintenance and Repair Strategies
As an Asset or Plant Manager, it’s crucial to ensure that your presses are well-maintained and operating efficiently to optimize productivity and reduce downtime. Troubleshooting press issues can be a daunting task, but with the right strategies and knowledge, you can identify and fix common problems with ease.
1. Introduction
Press Definition and Uses in Industry
A press is a machine tool that is used to shape and form materials through compression. Presses are commonly used in the manufacturing industry for a variety of applications, including metal stamping, forging, and forming. They are also used in the plastics, rubber, and wood industries.
The Importance of Press Maintenance
Press maintenance is crucial to ensure safe and efficient operation. Neglecting press maintenance can result in breakdowns, downtime, and increased costs. Regular maintenance can help prevent issues and ensure that your presses are operating at optimal performance.
Types of Presses
There are several types of presses commonly used in industry, including mechanical, hydraulic, pneumatic, electrical, and power presses. Each type has its own unique features and operating characteristics.
The Benefits of Effective Troubleshooting
Effective troubleshooting can help identify and fix issues before they lead to more significant problems. This can help reduce downtime, increase productivity, and save on repair costs in the long run.
2. Key Sub-Assemblies of Presses
Mechanical Presses
Mechanical presses use a flywheel and a clutch to generate and transfer energy to the die. They are known for their high accuracy and repeatability, making them ideal for high-precision applications. Common issues with mechanical presses include misalignment, vibration, and noise.
Hydraulic Presses
Hydraulic presses use fluid pressure to generate and transfer energy to the die. They are known for their high force and versatility, making them ideal for a wide range of applications. Common issues with hydraulic presses include valve and cylinder problems, as well as issues with the clutch and brake systems.
Pneumatic Presses
Pneumatic presses use compressed air to generate and transfer energy to the die. They are known for their low cost and fast cycle times, making them ideal for high-speed applications. Common issues with pneumatic presses include leaks and problems with the air supply system.
Electrical Presses
Electrical presses use electric motors to generate and transfer energy to the die. They are known for their high precision and energy efficiency, making them ideal for high-precision and high-volume applications. Common issues with electrical presses include problems with the motor and speed control systems.
Power Presses
Power presses use a combination of mechanical, hydraulic, and electrical systems to generate and transfer energy to the die. They are known for their high force and versatility, making them ideal for a wide range of applications. Common issues with power presses include problems with the clutch and brake systems, as well as issues with the motor and speed control systems.
Free Daily, Weekly, Monthly, Quarterly and Annual Preventive Maintenance Checklists for different Equipment Categories.
3. Top 12 Most Common Press Problems
a. Mechanical Issues
Misalignment
Misalignment is a common issue with mechanical presses that can lead to increased wear and tear on the machine and decreased accuracy. Causes of misalignment include worn bearings, loose bolts, and improper installation.
Vibration
Vibration is another common issue with mechanical presses that can lead to increased wear and tear and decreased accuracy. Causes of vibration include unbalanced or worn components, loose bolts, and improper installation.
Noise
Noise is a common issue with mechanical presses that can be caused by worn or loose components, improperly lubricated parts, or improper installation. Excessive noise can lead to operator discomfort and decreased productivity.
b. Electrical Issues
Motor Problems
Motor problems can be caused by a variety of issues, including worn or faulty bearings, improper lubrication, and electrical issues. Symptoms of motor problems include decreased performance, increased noise, and overheating.
Speed Control Problems
Speed control problems can be caused by issues with the control circuit, the motor, or the speed sensor. Symptoms of speed control problems include decreased performance, inaccurate speed control, and erratic operation.
Sensor Problems
Sensor problems can be caused by a variety of issues, including faulty sensors, loose connections, and wiring issues. Symptoms of sensor problems include inaccurate readings, erratic operation, and decreased performance.
c. Hydraulic Issues
Valve and Cylinder Problems
Valve and cylinder problems can be caused by worn or damaged seals, improperly adjusted valves, or damaged cylinders. Symptoms of valve and cylinder problems include leaks, decreased performance, and erratic operation.
Clutch and Brake Problems
Clutch and brake problems can be caused by worn or damaged components, improper adjustment, or hydraulic system issues. Symptoms of clutch and brake problems include decreased performance, erratic operation, and excessive wear on the clutch and brake components.
d. Pneumatic Issues
Leakage
Leakage is a common issue with pneumatic presses that can lead to decreased performance and increased operating costs. Causes of leakage include worn or damaged seals, loose connections, and improper installation.
Air Supply Problems
Air supply problems can be caused by issues with the compressor, the air supply system, or the air treatment system. Symptoms of air supply problems include decreased performance, erratic operation, and increased operating costs.
e. Safety Issues
Hazardous Operations
Hazardous operations can be caused by improper training, improper use of personal protective equipment, or improper installation or maintenance of the press. Symptoms of hazardous operations include operator injury, damage to equipment or materials, and
violations of safety regulations.
Regulatory Compliance
Regulatory compliance is crucial to ensure safe and efficient operation of presses. Compliance with regulations, codes, and standards can help prevent accidents, reduce liability, and ensure customer satisfaction. Failure to comply with regulations can result in fines, legal action, and damage to the company’s reputation.
4. Pre-Troubleshooting Steps
Conducting an Initial Assessment
Before troubleshooting press issues, it’s important to conduct an initial assessment to gather information about the problem. This can include observing the press in operation, interviewing operators or maintenance personnel, and reviewing maintenance logs or repair records.
Gathering Information on the Press System
Gathering information on the press system can help identify potential issues and ensure that the correct troubleshooting steps are taken. This can include reviewing equipment specifications and manuals, checking for updates or recalls, and consulting with manufacturers or experts.
Safety Precautions to Take
Taking safety precautions is crucial to ensure that troubleshooting is conducted safely and effectively. This can include wearing appropriate personal protective equipment, following lockout/tagout procedures, and ensuring that all personnel are properly trained and informed of safety hazards and procedures.
5. Troubleshooting and Problem Identification
Checking the Power Supply
Checking the power supply is the first step in troubleshooting press issues. This can include checking for proper voltage and current, ensuring that the electrical connections are secure, and checking for proper grounding.
Inspecting the Press Assembly
Inspecting the press assembly can help identify issues with mechanical, hydraulic, or pneumatic systems. This can include checking for worn or damaged components, leaks, and alignment issues.
Troubleshooting the Motor
Troubleshooting the motor can help identify issues with electrical or power systems. This can include checking for proper voltage and current, testing the motor for proper operation, and checking for worn or damaged components.
Testing the Speed Control
Testing the speed control can help identify issues with electrical or power systems. This can include checking for proper voltage and current, testing the speed sensor and control circuit, and checking for worn or damaged components.
Inspecting the Clutch and Brake Systems
Inspecting the clutch and brake systems can help identify issues with hydraulic or pneumatic systems. This can include checking for proper adjustment and operation, inspecting for worn or damaged components, and checking for leaks.
6. Repairing the Press
Replacing Faulty Parts
Replacing faulty parts can help resolve press issues and ensure safe and efficient operation. This can include ordering and installing replacement parts, following manufacturer’s instructions, and ensuring that proper safety precautions are taken.
Repairing Wiring Issues
Repairing wiring issues can help resolve electrical or power system issues. This can include identifying and repairing damaged or worn wiring, ensuring that all connections are secure, and following manufacturer’s instructions.
Cleaning and Lubricating Components
Cleaning and lubricating components can help prevent future issues and ensure that the press operates smoothly and efficiently. This can include cleaning and lubricating bearings, gears, and other moving parts, following manufacturer’s instructions and using appropriate cleaning and lubrication products.
7. Testing and Maintenance
Running Tests to Ensure Proper Functionality
Running tests to ensure proper functionality can help verify that press issues have been resolved and that the press is operating safely and efficiently. This can include conducting performance tests, verifying speed control and accuracy, and ensuring that all safety features are functioning properly.
Developing a Maintenance Plan
Developing a maintenance plan can help prevent future issues and ensure that the press operates safely and efficiently. This can include scheduling regular maintenance tasks, conducting periodic inspections, and following manufacturer’s recommendations for maintenance and service.
How CMMS can help
Computerized Maintenance Management Systems (CMMS) can help streamline maintenance processes, track equipment performance, and ensure compliance with regulatory requirements. CMMS software can help automate tasks such as scheduling and work order generation, and can provide real-time data on equipment performance and maintenance needs.
Best Practices
Tips and Tricks
Train Operators and Maintenance Personnel
Proper training of operators and maintenance personnel can help prevent issues and ensure that troubleshooting and repair tasks are conducted safely and effectively.
Follow Manufacturer’s Recommendations
Following manufacturer’s recommendations for maintenance and service can help prevent issues and ensure that the press operates safely and efficiently.
Regularly Inspect and Maintain Equipment
Regular inspections and maintenance can help prevent issues and ensure that the press operates safely and efficiently.
8. How to Prevent Most Common Problems
Follow Proper Lubrication Procedures
Proper lubrication can help prevent issues such as vibration and wear on components.
Ensure Proper Alignment
Proper alignment can help prevent issues such as misalignment and decreased accuracy.
Regularly Check for Leaks and Loose Connections
Regular checks for leaks and loose connections can help prevent issues such as decreased performance and increased operating costs.
9. Conclusion
Recap of Troubleshooting Steps
Troubleshooting press issues requires a systematic approach that involves identifying the problem, gathering information, and testing and repairing components as needed. Safety precautions must be taken throughout the process to ensure safe and effective troubleshooting and repair.
The Importance of Regular Maintenance
Regular maintenance is crucial to prevent issues and ensure that the press operates safely and efficiently. Following best practices and manufacturer’s recommendations can help prevent most common issues and ensure customer satisfaction and optimal performance.
10. Key Takeaways
- Presses are widely used in industry and require regular maintenance and troubleshooting to ensure safe and efficient operation.
- Common issues with presses include mechanical, electrical, hydraulic, pneumatic, and safety issues.
- Troubleshooting requires a systematic approach that involves identifying the problem, gathering information, and testing and repairing components as needed.
- Regular maintenance is crucial to prevent issues and ensure safe and efficient operation.
Request a one-one demo with our solution engineering team.
Request a one-one demo with our solution engineering team.
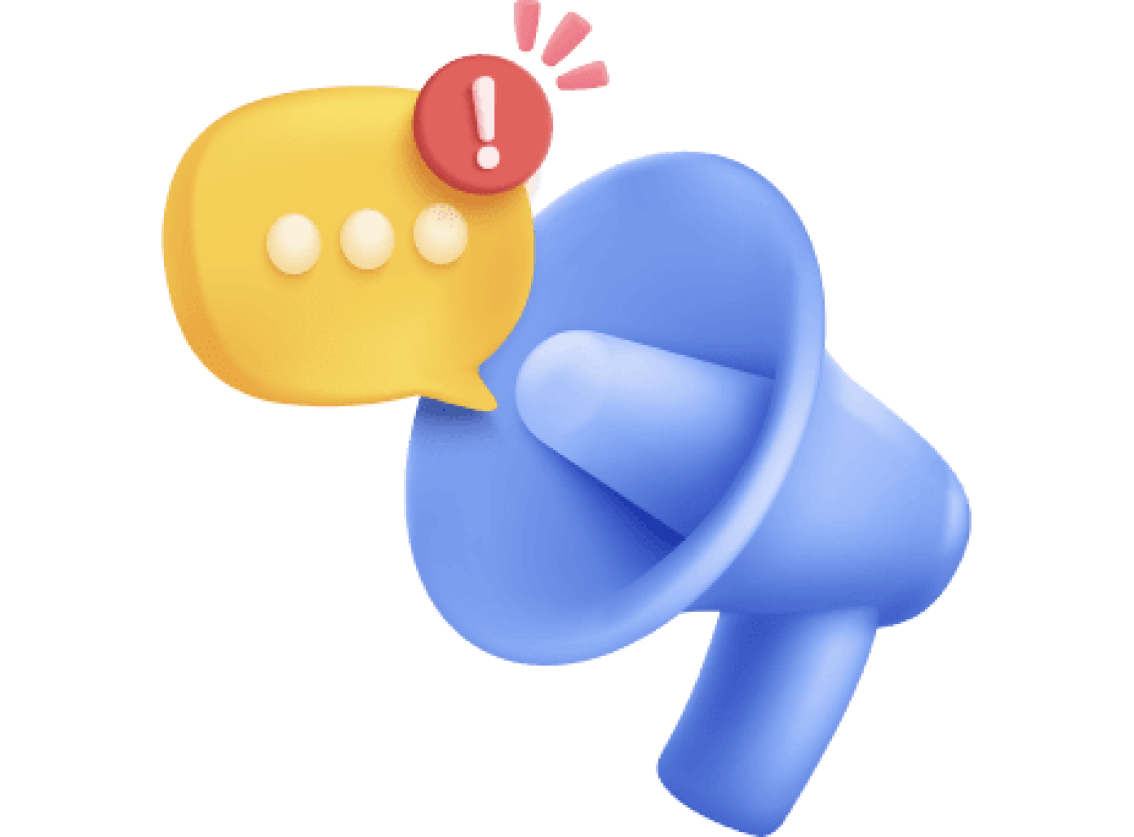