Troubleshooting Your Heat Exchangers
Troubleshooting Your Heat Exchangers
Table of Contents
ToggleA Step-by-Step Guide to Troubleshooting Your Heat Exchangers: Maintenance and Repair Strategies
Heat exchangers play a vital role in various industries, such as power generation, oil and gas, chemical processing, and HVAC systems. They are used to transfer heat from one fluid to another fluid without mixing them. Heat exchangers are designed to operate efficiently for an extended period, but like any other equipment, they require maintenance and repairs to ensure optimal performance. In this article, we will provide a comprehensive guide on troubleshooting your heat exchangers from a plant maintenance and asset management perspective.
1. Introduction
Heat Exchanger – definition, and uses in industry
A heat exchanger is a device that transfers heat between two or more fluids that are at different temperatures. The fluids can be liquids, gases, or a combination of both. Heat exchangers are used in various industries, including chemical processing, petroleum refining, power generation, and HVAC systems. They are designed to improve energy efficiency, reduce operating costs, and maintain a safe operating environment.
Importance of heat exchanger maintenance
Heat exchanger maintenance is crucial to ensure that the equipment operates efficiently and safely. Proper maintenance can prevent issues such as fouling, scaling, corrosion, and cracking, which can lead to reduced heat transfer efficiency, higher energy consumption, and equipment failure. Regular maintenance can also extend the life of the equipment, reduce downtime, and improve overall productivity.
Types of heat exchangers
There are several types of heat exchangers, including shell and tube, plate and frame, spiral, and air-cooled heat exchangers. Each type has its advantages and disadvantages, and the choice of heat exchanger depends on the specific application, operating conditions, and fluid properties.
2. Key Sub-assemblies of Heat Exchangers
Heat exchangers consist of several sub-assemblies that work together to transfer heat from one fluid to another. Understanding these sub-assemblies is crucial to identify and troubleshoot heat exchanger problems.
Tubes and tube sheets
Tubes and tube sheets are the primary components of shell and tube heat exchangers. The tubes carry the fluid that needs to be cooled or heated, while the tube sheets hold the tubes in place and provide a seal between the two fluids.
Shell
The shell is the outermost component of the shell and tube heat exchanger. It contains the tubes and provides a barrier between the two fluids.
Baffles
Baffles are installed inside the shell of the shell and tube heat exchanger. They direct the flow of the fluid and improve the heat transfer efficiency.
Gaskets
Gaskets are used to provide a seal between the tube sheets and the shell in shell and tube heat exchangers. They prevent fluid from leaking between the two fluids.
Plates
Plates are used in plate and frame heat exchangers. They are arranged in a stack and held together by a frame. The plates create channels for the fluids to flow through and transfer heat between them.
Fans
Fans are used in air-cooled heat exchangers to remove heat from the fluid. They blow air over the heat exchanger fins, which removes heat from the fluid and dissipates it into the atmosphere.
Fins
Fins are used in air-cooled heat exchangers to increase the surface area and improve the heat transfer efficiency. The fins increase the contact area between the fluid and the air, which improves the heat transfer rate.
Free Daily, Weekly, Monthly, Quarterly and Annual Preventive Maintenance Checklists for different Equipment Categories.
3. Top 10 Most Common Heat Exchanger Problems
Heat exchangers can experience various issues that can affect their performance and efficiency. Here are the top ten most common heat exchanger problems:
Fouling
Fouling occurs when deposits build up on the surface of the heat exchanger, reducing the heat transfer efficiency. Fouling can be caused by sediment, biological growth, or chemical reactions.
Corrosion
Corrosion occurs when the metal surfaces of the heat exchanger react with the fluid, causing degradation and damage. Corrosion can be caused by the fluid’s pH level, temperature, and chemical composition.
Scaling
Scaling occurs when mineral deposits build upon the heat exchanger surface, reducing the heat transfer efficiency. Scaling can be caused by hard water or high mineral content in the fluid.
Cracking
Cracking occurs when the heat exchanger experiences excessive pressure or temperature, causing structural damage. Cracking can lead to leaks and equipment failure.
Leaks
Leaks can occur when the heat exchanger tubes or seals become damaged, causing fluid to escape. Leaks can lead to reduced performance, environmental contamination, and safety hazards.
Fluid Contamination
Fluid contamination occurs when the heat exchanger fluid becomes contaminated with foreign substances, such as dirt, oil, or chemicals. Contaminated fluid can reduce the heat transfer efficiency and damage the equipment.
Blockages
Blockages occur when debris or sediment accumulates in the heat exchanger, reducing the fluid flow and heat transfer efficiency. Blockages can lead to increased energy consumption and equipment failure.
Mechanical Damage
Mechanical damage occurs when the heat exchanger experiences physical damage, such as dents, scratches, or bent tubes. Mechanical damage can reduce the heat transfer efficiency and lead to leaks.
Temperature Variations
Temperature variations can occur when the heat exchanger experiences temperature fluctuations, causing stress on the equipment. Temperature variations can lead to equipment failure, leaks, and reduced performance.
Vibration
Vibration occurs when the heat exchanger experiences excessive vibrations, causing stress on the equipment. Vibration can lead to equipment failure, leaks, and reduced performance.
4. Pre-Troubleshooting Steps
Conducting an Initial Assessment
Before troubleshooting the heat exchanger, it’s essential to conduct an initial assessment to identify the potential causes of the problem. The assessment should include identifying the symptoms, such as reduced heat transfer efficiency, leaks, or unusual noises, and collecting information on the equipment’s operating conditions, such as fluid flow rates, temperature, and pressure.
Gathering Information on the Heat Exchanger System
Gathering information on the heat exchanger system is crucial to identify the root cause of the problem. The information should include the heat exchanger type, size, and specifications, the fluid properties, and the operating conditions. This information can help narrow down the potential causes and identify the appropriate troubleshooting steps.
Safety Precautions to Take
Heat exchangers can be dangerous to work on, especially if they contain hazardous fluids or operate at high temperatures and pressures. It’s essential to take proper safety precautions, such as wearing protective gear, following the lockout/tag-out procedures, and using appropriate tools and equipment.
5. Identifying the Problem
Checking for Leaks
Leaks are a common problem in heat exchangers, and they can be caused by damaged tubes, gaskets, or seals. Checking for leaks should be the first step in troubleshooting the heat exchanger. The best way to identify leaks is by conducting a visual inspection or using a leak detection tool.
Measuring Temperature and Pressure
Temperature and pressure measurements can provide valuable information on the heat exchanger’s operating conditions. Monitoring temperature and pressure can help identify potential problems, such as fouling, scaling, or blockages. It’s essential to measure the temperature and pressure at different points in the heat exchanger to identify any variations.
Inspecting the Heat Exchanger
A visual inspection of the heat exchanger can provide valuable information on the equipment’s condition. Inspecting the heat exchanger involves looking for signs of damage, such as cracks, dents, or corrosion. It’s essential to inspect all the sub-assemblies, including tubes, tube sheets, shell, baffles, and gaskets.
Testing the Fluids
Testing the fluids can help identify potential issues, such as fluid contamination or chemical reactions. Fluid testing involves analyzing the fluid properties, such as pH level, viscosity, and conductivity. It’s essential to test both the inlet and outlet fluids to identify any variations.
6. Repairing the Heat Exchanger
Cleaning and Descaling
Cleaning and descaling the heat exchanger can help remove fouling, scaling, and other deposits that reduce the heat transfer efficiency. Cleaning can be done using mechanical, chemical, or thermal methods, depending on the type and severity of the fouling. Descaling involves removing mineral deposits using chemical or mechanical methods.
Replacing Damaged Parts
Replacing damaged parts, such as tubes, tube sheets, or gaskets, can help restore the heat exchanger’s performance and efficiency. It’s essential to use appropriate replacement parts that meet the heat exchanger’s specifications and operating conditions.
Welding and Patching
Welding and patching can be used to repair cracks or leaks in the heat exchanger. Welding involves fusing the metal surfaces together using heat, while patching involves covering the damaged area with a patch or sealant. It’s essential to use appropriate welding and patching techniques that do not compromise the heat exchanger’s structural integrity.
7. Testing and Maintenance
Running Tests to Ensure Proper Functionality
After repairing the heat exchanger, it’s essential to run tests to ensure that it’s functioning correctly. Testing can include pressure testing, temperature testing, flow rate testing, and efficiency testing. Testing can help identify any residual problems and ensure that the heat exchanger is operating at its optimal performance.
Developing a Maintenance Plan
Developing a maintenance plan can help prevent future problems and extend the heat exchanger’s lifespan. The maintenance plan should include regular cleaning, inspection, and testing procedures, as well as appropriate repairs and replacements. The maintenance plan should be tailored to the heat exchanger’s specific operating conditions and fluid properties.
How CMMS Can Help
A Computerized Maintenance Management System (CMMS) can help automate and streamline the maintenance process, making it more efficient and effective. CMMS can help schedule maintenance tasks, track equipment performance, and generate reports on maintenance activities. CMMS can also help identify potential problems and recommend appropriate solutions.
8. Best Practices
Proper Installation and Positioning
Proper installation and positioning can help ensure that the heat exchanger is operating at its optimal performance. The heat exchanger should be installed according to the manufacturer’s specifications, and it should be positioned to facilitate proper fluid flow and heat transfer. Proper installation and positioning can also help prevent mechanical damage and leaks.
Regular Cleaning and Maintenance
Regular cleaning and maintenance can help prevent fouling, scaling, and other deposits that reduce the heat transfer efficiency. Regular cleaning and maintenance should be performed according to the heat exchanger’s specific operating conditions and fluid properties. It’s essential to use appropriate cleaning and maintenance procedures that do not damage the equipment.
Monitoring Fluid Flow Rates
Monitoring fluid flow rates can help identify potential problems, such as blockages or leaks. Fluid flow rates should be monitored regularly and adjusted as necessary to ensure proper flow and heat transfer. It’s essential to use appropriate monitoring equipment and techniques that do not compromise the heat exchanger’s structural integrity.
9. Conclusion
In conclusion, troubleshooting a heat exchanger requires a systematic and thorough approach that involves identifying the symptoms, gathering information, and identifying the root cause of the problem. Repairing the heat exchanger involves cleaning, descaling, replacing damaged parts, and welding or patching. Testing and maintenance involve running tests to ensure proper functionality and developing a maintenance plan. Best practices include proper installation and positioning, regular cleaning and maintenance, and monitoring fluid flow rates. By following these steps and best practices, you can maximize the heat exchanger’s performance and efficiency and prevent future problems.
10. Key Takeaways
- Heat exchangers are critical equipment used in various industries to transfer heat between fluids.
- Common heat exchanger problems include fouling, corrosion, scaling, cracking, leaks, and fluid contamination.
- Pre-troubleshooting steps include conducting an initial assessment, gathering information on the heat exchanger system, and taking safety precautions.
- Identifying the problem involves checking for leaks, measuring temperature and pressure, inspecting the heat exchanger, and testing the fluids.
- Repairing the heat exchanger involves cleaning, descaling, replacing damaged parts, and welding or patching.
- Testing and maintenance involve running tests to ensure proper functionality and developing a maintenance plan.
- Best practices include proper installation and positioning, regular cleaning and maintenance, and monitoring fluid flow rates.
Request a one-one demo with our solution engineering team.
Request a one-one demo with our solution engineering team.
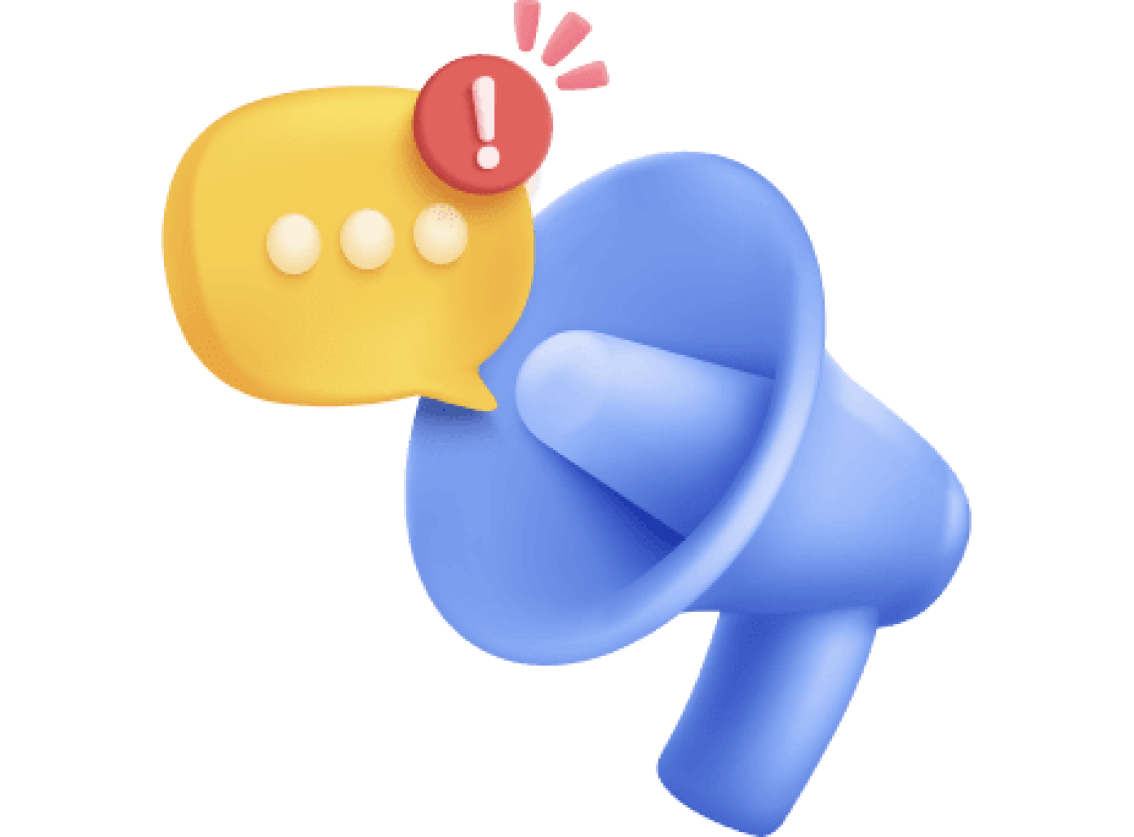