Unleash the Power of Industry 4.0
Unleash the Power of Industry 4.0
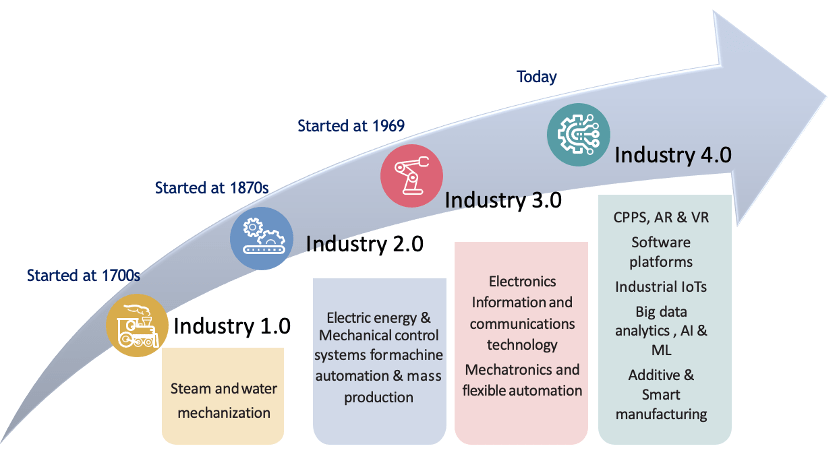
The big shift has happened because of connected assets and intelligent systems that combine real time information to provide insights at multiple levels to smarten the full value chain. When a billion people joined the Internet, it redefined how people communicate, interact and transact, thereby reimagining every possible industry. Even physical goods and services based industries like ecommerce and transportation have been upended very rapidly. Industry 4.0 brings in a trillion connected assets and its impact will be far reaching.
Table of Contents
ToggleIndustry 4.0 – The Convergence of Transformative Technologies
Internet has removed the distance barrier. Smartphones have broken the time barrier. Internet of things has enabled data capture at an elemental level. Connectivity has ensured that real time data can be monitored. Integration services built in has bridged the Operational Technologies (PLC, DCS, SCADA) with other enterprise technologies. Rule based systems and algorithms can enable process automations. Augmented reality can add experience that traverse between the real and virtual worlds. Big data provides enormous insights. Each of these technologies are high impact and a force of change. And Industry 4.0 brings in their convergence, wherein one or more independent technologies interoperate efficiently and integrate to define new outcomes that reshapes the process, business models and the basic constructs of the industry.
Application Areas
Industry 4.0 touches business, operations, people and information and recasts their interactions in myriad new ways to deliver innovation and efficiency, at scale to transform the whole value chain. Principal applications in the manufacturing domain include the following six areas.
1. Supply Chain Management: Supply chain consists of diverse components, sourced from multiple tiers of suppliers with many intermediary steps including transportation, storage, customs clearance etc. Information exchange, automation and intelligence can make the supply chain and associated processes more efficient. Driverless in-plant vehicles, intelligent containers and storage units, smart warehouses, sensor controlled cold chains, blockchain led distributed ledgers, process digitalization at ports and borders are few examples. Industry 4.0 technologies have integrated the enterprise with its long tail of supply value chain and has enabled real time information exchange of inventory, seamless communication of sales and operating plants, traceability of supplier components at a granular level, flexible ecosystem with better demand planning, reduction of inefficiencies and quick time to market.
2. Customer Relationship Management: Customer demands are changing rapidly and are expecting instantaneous gratification. Product life cycles are getting shorter. Beyond goods and services, experience has become pivotal. Customer feedback, positive or negative is getting amplified via social media. Industry 4.0 provides multitude of ways to segment, target, position, promote, influence, sell, process payments, deliver, manage and respond to customer demands at granular level and at scale simultaneously.
3. Business Models: Uberization has driven newer models around orchestration of experience led customer ownership. Electric vehicles and cheaper renewable energy is overturning the oil led economics.Self driving cars are information led and changing the fundamental design tenets. Span of customer interactions are becoming deeper and for selective vendors. Business processes and even established business models are getting commoditized and organizations are constantly innovating to gain newer capabilities and competencies.
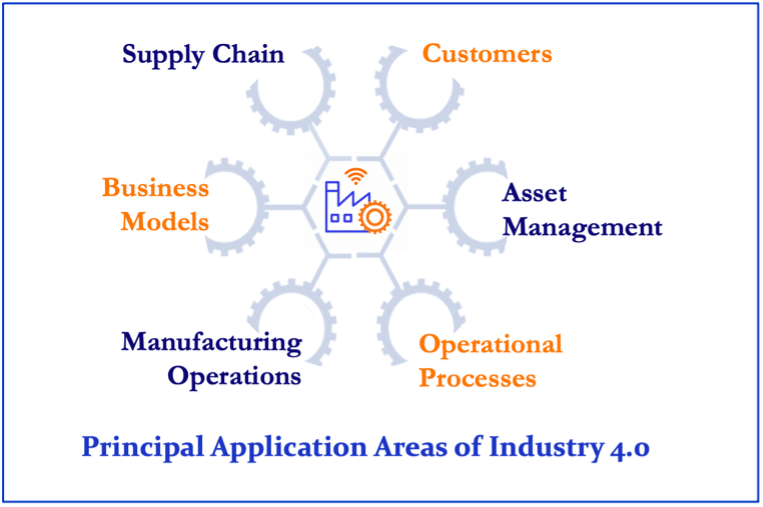
4. Manufacturing Operations: In response to high velocity external changes, technology has driven rapid changes in production systems to deliver newer and innovative products, that are better functionally and technically, greener and eco-friendly, in a faster and more efficient process, in safe and secure environment while being cheaper and cost effective. Autonomous robots are engaged for hazardous operations. 3D or additive manufacturing is employed for unique and custom manufacturing. Dynamic production planning and rapid change in product mix are becoming the norms. Production lines are getting automated and even remotely controlled. Non-intrusive testing and inspections discover defects at first mile of production. Traceability at component level enabled tracking and quick resolution.
5. Operational Process Efficiency: Industry 4.0 creates many technology led opportunities to identify and eliminate inefficiencies and bottlenecks and drive process optimization and operational excellence. Covid-19 accelerated a lot of digitalization in a very short span of time. Cloud based systems, remote monitoring tools, automated alerts and notifications on first symptoms have all become the essential support structure in the new normal of remote working. Digital era has led to information explosion and the agility required by market enabled decentralization of data for quick decision making and where possible automation of decision support. Stringent regulations and compliance led to robotics and computer vision based tools deployment. Industry 4.0 has led to higher asset utilization, operational efficiency enhanced people productivity and empowerment.
6. Asset Management & Plant Maintenance: Poor plant maintenance strategies can substantially reduce manufacturing efficiency. Traditionally plant maintenance has been heuristics based, driven by paper based processes, non-standard and fragmented. Digital era led to intelligent machines coupled with CMMS Software and technology integrations has led to efficient information capture at elementary level. Process standardization, risk based inspections and condition based interventions have led to preventive maintenance effectiveness. Simplification of technology has led to wider user adoption and higher engagement. Smart analytics implementation has led to predictive insights, metrics based management, goal based maintenance and better shop floor to top floor analytics. Smart Maintenance strategy has led to better plant maintenance, thereby improving asset uptime, utilisation and efficiency.
Maintenance 4.0 for Smart Plant Maintenance
Maintenance 4.0 is the application of the Industry 4.0 to improve Capital Assets Management and Plant Maintenance. Maintenance 4.0, using the digital technologies, provide a lot of information about the assets under management, including their performance and failure history and helps in improving the availability and reliability.MaintWiz provides a smart digital infrastructure leveraging the Industry 4.0 technologies to provide comprehensive Asset Care Solutions. MaintWiz Solution consists of
Building the Digital Foundation: Asset hierarchy (Plants / Projects, Equipment, Instruments, Utilities, Fleet), Process Assets (PM Schedules and Checksheets, Daily Patrolling tasks, Breakdown maintenance including Root Cause Analysis and CAPA activities, Inspection and Audit Schedules, Planning Tools, Horizontal Deployment etc.
Connecting the Systems: Connecting the Operational Technology (PLC / SCADA / DCS / MES) stack to the Enterprise Technology (SAP / Other ERP, Data warehouse, Homegrown applications). A Single Unified interface to all Asset related information and tools for Condition Monitoring.
Providing Outcome Oriented Analytics: Wide variety of analytics (EQP, Peer class comparison, financial, maintenance metrics etc.)
Enabling Smart Workforce: Simplifying technology to enable quick learning and adoption. Access to all critical information via Mobile for the front end team. Providing contextual information to improve decision making and productivity. Enabling complete transaction entry at point of work with One Click maintenance.
Request a one-one demo with our solution engineering team.
Request a one-one demo with our solution engineering team.
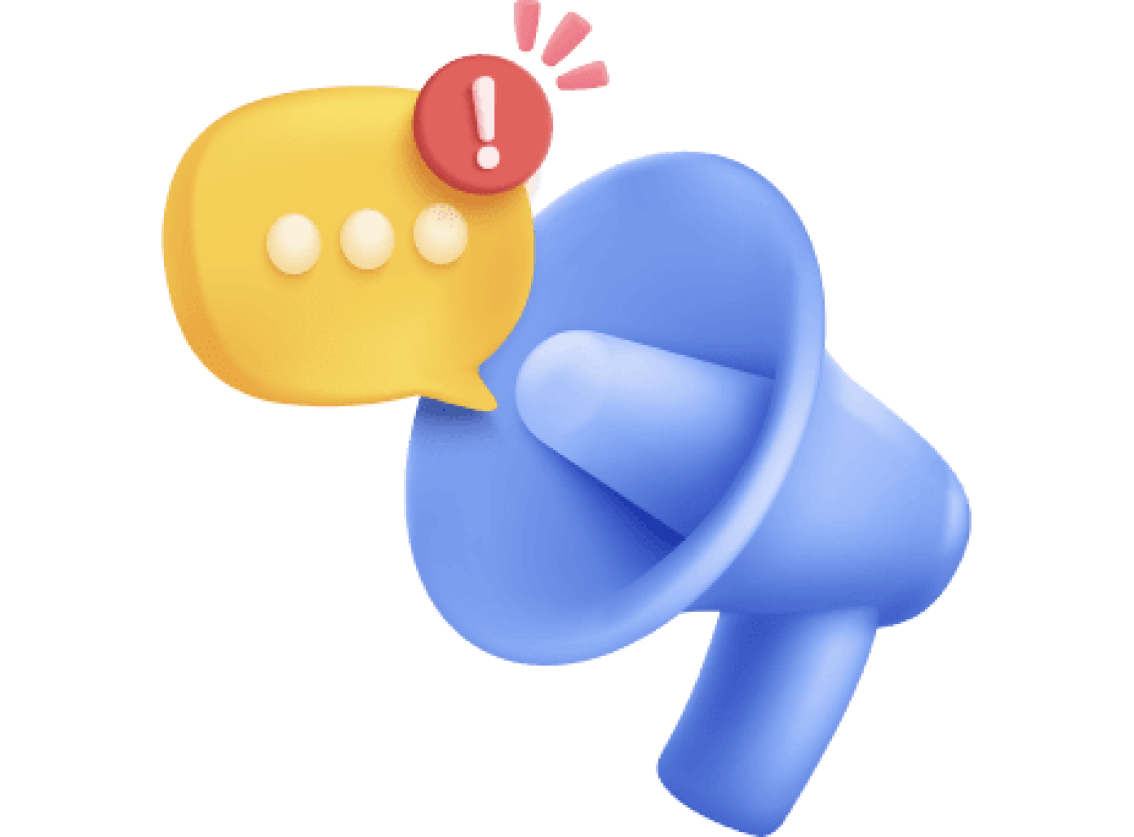