The Importance of Maintenance Checklists
The Importance of Maintenance Checklists
Table of Contents
ToggleThe Importance of Maintenance Checklists
Introduction
A well-structured and systematic maintenance process is vital for the smooth operation of any enterprise. Maintenance checklists play a crucial role in ensuring that all necessary tasks are performed consistently and efficiently. By providing a comprehensive list of tasks to be completed, checklists help reduce human error, enhance safety, and improve overall equipment reliability and performance. In this article, we will explore the key aspects of maintenance checklists from an asset management and plant maintenance perspective, highlighting their importance and benefits.
1. Systematic and Consistent Task Performance
Maintenance checklists ensure that all necessary tasks are performed systematically and consistently. By following a predefined checklist, technicians can ensure that no critical steps are missed during maintenance procedures. This standardized approach helps in maintaining the reliability and performance of equipment by eliminating guesswork and reducing the time required for troubleshooting.
2. Early Issue Identification and Prevention
One of the primary benefits of maintenance checklists is their ability to identify potential issues or malfunctions before they become major problems. By including thorough inspection points in the checklist, technicians can spot early warning signs of equipment failure or deterioration. This early identification enables proactive measures to be taken, such as timely repairs or component replacements, minimizing the risk of unplanned downtime and associated costs.
3. Accountability and Compliance
Maintenance checklists provide a clear record of completed maintenance tasks, ensuring accountability and compliance. With documented evidence of maintenance activities, organizations can demonstrate their adherence to regulatory requirements and industry standards. This record also proves valuable in audits and legal proceedings, safeguarding the enterprise against potential liabilities.
4. Reduced Human Error
Human error can have significant consequences in maintenance operations. Maintenance checklists help reduce human error by providing a comprehensive list of tasks to be completed. Technicians can refer to the checklist to ensure that each step is carried out accurately and no important tasks are overlooked. This systematic approach minimizes the likelihood of errors and enhances the overall quality and effectiveness of maintenance procedures.
5. Enhanced Safety and Compliance
Adhering to safety regulations is of utmost importance in plant maintenance. Maintenance checklists contribute to enhancing safety by ensuring that maintenance procedures are carried out correctly and in compliance with safety regulations. By incorporating safety guidelines and precautions in the checklist, organizations can minimize the risk of accidents, injuries, and equipment damage, creating a safer working environment for technicians and personnel.
6. Efficient Troubleshooting
When issues arise, efficient troubleshooting is crucial for minimizing equipment downtime. Maintenance checklists aid in troubleshooting by providing a structured approach to problem-solving. Technicians can refer to the checklist to identify potential causes and systematically eliminate them, narrowing down the root cause more effectively. This structured troubleshooting approach saves time and resources, enabling faster equipment restoration and reducing operational disruptions.
7. Extended Equipment Lifespan
Regular maintenance and timely repairs are essential for extending the lifespan of equipment and assets. Maintenance checklists ensure that scheduled maintenance tasks are not missed or delayed. By following the checklist
and performing routine inspections, technicians can identify any signs of wear and tear, damage, or potential issues. Timely repairs and maintenance interventions can prevent further deterioration and extend the lifespan of equipment. This proactive approach helps organizations maximize the value of their assets and avoid premature equipment replacements, saving costs in the long run.
8. Documented Maintenance History
Maintenance checklists provide a documented history of maintenance activities for each asset. By recording details such as dates, tasks performed, and any observations or findings, organizations can track trends and identify recurring issues. This historical data is valuable for analyzing the performance and reliability of equipment, identifying patterns of failures, and making data-driven decisions for improvement. It also facilitates audits, compliance assessments, and warranty claims.
9. Planning and Scheduling
Effective planning and scheduling of maintenance tasks are crucial for optimizing resources and minimizing downtime. Maintenance checklists assist in planning and scheduling by outlining the required tasks and their recommended intervals. By following the checklist, organizations can ensure that maintenance activities are performed at the appropriate times, considering factors such as usage patterns, equipment specifications, and manufacturer recommendations. This systematic approach helps in streamlining maintenance operations and minimizing disruptions to production or service delivery.
10. Communication and Collaboration
In larger enterprises, maintenance operations involve multiple teams and stakeholders. Maintenance checklists facilitate communication and collaboration among these teams by providing a standardized reference. With a checklist in place, everyone involved in the maintenance process can understand the tasks and expectations, ensuring clarity and alignment. It promotes effective coordination, reduces miscommunication, and fosters a collaborative environment where teams work together towards common maintenance goals.
11. Quality Control
Maintenance checklists support quality control by outlining specific criteria and standards to be met during inspections and maintenance tasks. These criteria may include performance parameters, regulatory compliance, cleanliness standards, or equipment specifications. By incorporating quality control elements in the checklist, organizations can ensure that maintenance activities meet the required standards. This helps in preventing product quality issues, service delivery problems, and customer dissatisfaction.
12. Inventory Management
Maintenance tasks often require spare parts, tools, or supplies. Maintenance checklists can assist in inventory management by identifying the specific spare parts and supplies needed for each task. By referencing the checklist, organizations can keep track of the inventory levels and plan for procurement or stock replenishment. This ensures that technicians have the necessary resources readily available, minimizing delays in maintenance activities and optimizing inventory costs.
13. Regulatory Compliance
Complying with regulatory requirements and industry standards is a critical aspect of maintenance operations, especially in regulated industries. Maintenance checklists help in ensuring compliance by including specific tasks, inspections, or documentation required to meet regulatory obligations. By following the checklist, organizations can demonstrate their commitment to compliance, avoid penalties or fines, and maintain a positive reputation in the industry.
14. Proactive Maintenance Approach
Maintenance checklists are integral tools that facilitate a proactive maintenance approach by emphasizing the importance of preventive maintenance. These lists incorporate tasks such as lubrication, calibration, or cleaning. By diligently following these steps, organizations can circumvent equipment failures, minimize breakdowns, and optimize overall performance. The emphasis on preventive maintenance reduces the reliance on reactive maintenance, where repairs are done only after a failure has occurred. Consequently, this proactive approach helps organizations achieve higher equipment reliability and availability, resulting in fewer disruptions and increased productivity.
15. Equipment Warranties
Many equipment manufacturers provide warranties that require regular maintenance as a condition. Maintenance checklists ensure that recommended maintenance tasks are performed as per the manufacturer’s guidelines. By following the checklist, organizations can safeguard their warranty claims and ensure that equipment
remains covered. This not only protects the organization’s investment but also gives them peace of mind knowing that the equipment is being properly maintained according to the manufacturer’s specifications.
16. Product Quality and Service Delivery
The quality of products or services delivered by an organization can be directly affected by the condition of the equipment used in their production or delivery. Maintenance checklists help in identifying and addressing issues that may impact product quality or service delivery. By including relevant inspections and maintenance tasks in the checklist, organizations can ensure that equipment is functioning optimally, minimizing the risk of defects, errors, or service disruptions. This contributes to overall customer satisfaction and helps maintain a positive brand image.
17. Evaluation and Improvement
Maintenance checklists provide a basis for evaluating the effectiveness of maintenance procedures and making improvements. By regularly reviewing completed checklists and analyzing the data, organizations can identify areas for improvement, such as recurring issues, inefficient processes, or gaps in training. This feedback loop enables continuous improvement in maintenance operations, resulting in increased efficiency, reduced costs, and enhanced equipment reliability.
18. Risk Mitigation
Unplanned equipment downtime can lead to significant financial losses, operational disruptions, and potential safety risks. Maintenance checklists help reduce the risk of unplanned downtime by catching issues early on. By including comprehensive inspections and tasks in the checklist, organizations can detect and address potential problems before they escalate into major failures. This proactive risk mitigation approach helps in maintaining uninterrupted operations, meeting production or service targets, and ensuring a safe working environment for employees.
19. Training and Knowledge Transfer
Maintenance checklists serve as valuable training tools, particularly for new technicians or employees joining the maintenance team. The checklist provides a step-by-step guide to performing maintenance tasks, ensuring that new technicians understand the required procedures and follow them accurately. It facilitates knowledge transfer and helps maintain consistency in maintenance practices across the organization. Additionally, the checklist can be used for training purposes, enabling technicians to enhance their skills and stay updated on best practices in maintenance.
20. Cost Control
Emergency repairs and expensive equipment replacements can significantly impact an organization’s budget. Maintenance checklists contribute to cost control by minimizing the need for such emergency measures. By ensuring regular maintenance and timely repairs through the checklist, organizations can prevent major failures or breakdowns that require costly interventions. This proactive approach helps in optimizing maintenance costs, extending equipment lifespan, and maximizing the return on investment.
21. Asset Management
Maintenance checklists support effective asset management by providing a comprehensive overview of maintenance activities for each asset. Organizations can track the maintenance history, costs, and performance of assets through the checklist. This information is valuable for decision-making regarding asset repair, replacement, or retirement. By understanding the maintenance requirements and patterns of each asset, organizations can develop data-driven asset management strategies, ensuring optimal utilization of resources and minimizing downtime risks.
Conclusion
Maintenance checklists are indispensable tools for efficient asset management and plant maintenance. They ensure systematic and consistent task performance, early issue identification, and accountability. By reducing human error, enhancing safety, and improving efficiency, checklists contribute to the overall reliability and performance of equipment. They provide a documented history of maintenance activities, aid in planning and scheduling, and facilitate communication and collaboration among maintenance teams. By emphasizing quality control, compliance, and a proactive approach, checklists help organizations achieve cost control, customer satisfaction, and effective asset management. Incorporating maintenance checklists in maintenance operations is a strategic investment that yields long-term benefits, ensuring optimized equipment performance and minimizing operational risks.
Request a one-one demo with our solution engineering team.
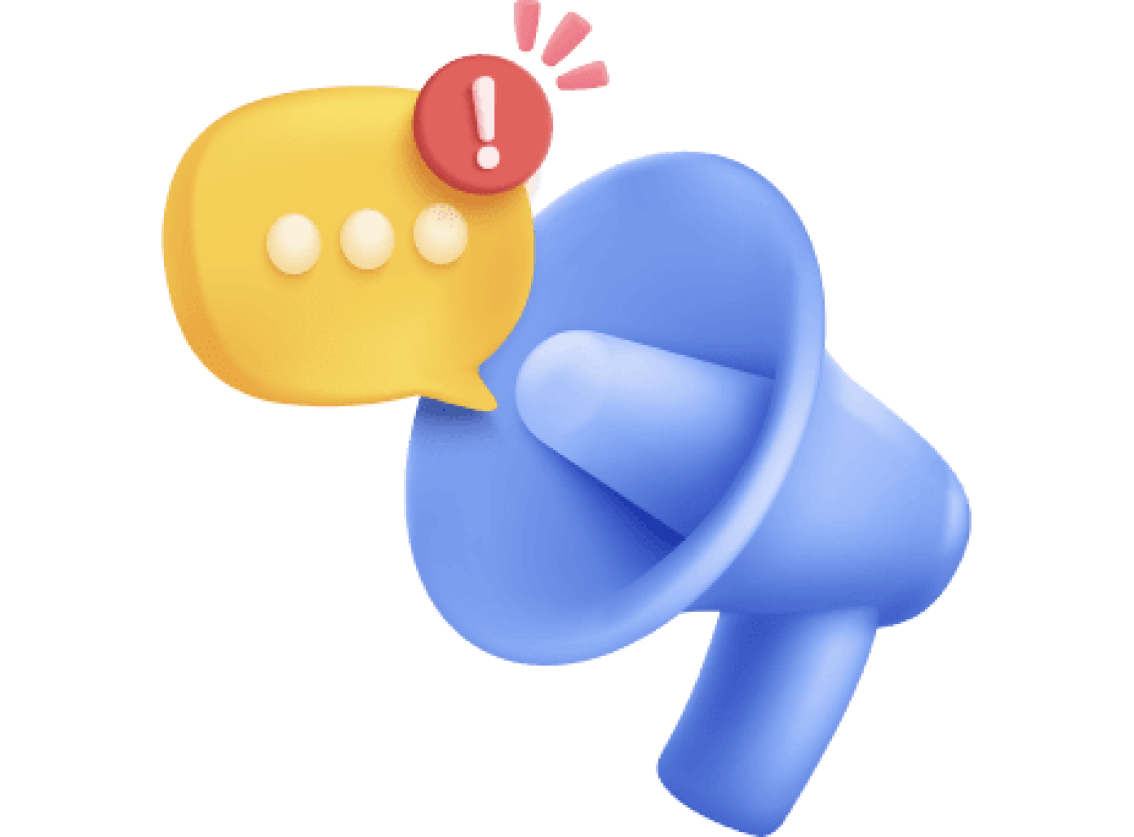
Request a one-one demo with our solution engineering team.
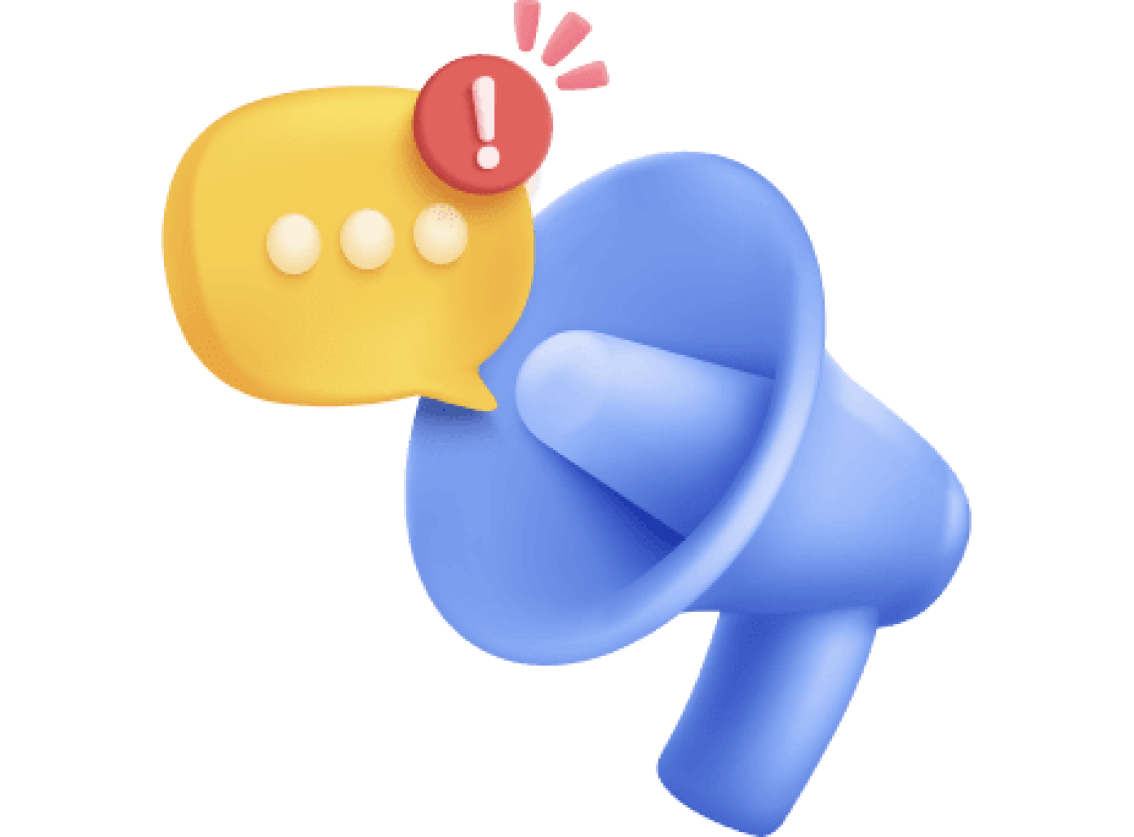