The Importance of Instrument Calibration
The Importance of Instrument Calibration
Table of Contents
ToggleThe Importance of Instrument Calibration
Instrument calibration plays a vital role in asset management and plant maintenance. It ensures accurate and reliable measurement readings, compliance with regulatory and quality standards, and prevents errors and inaccuracies in data analysis. From enhancing product quality to supporting process optimization and efficiency, calibration is an essential aspect of maintaining a well-functioning industrial environment. In this article, we will explore the key reasons why instrument calibration is crucial in asset management and plant maintenance.
1. Ensures Accurate and Reliable Measurement Readings
Instrument calibration guarantees that measurement readings are accurate and reliable. By calibrating instruments, you establish a baseline reference point for their performance, enabling you to trust the data they provide. This accuracy is crucial in various industries, such as manufacturing, pharmaceuticals, and environmental monitoring, where precise measurements are essential for decision-making, compliance, and quality control.
2. Compliance with Regulatory and Quality Standards
Calibration is vital for complying with regulatory and quality standards. Many industries have specific requirements and regulations that demand accurate measurements and instrument calibration. Compliance ensures adherence to standards such as ISO 9001, ISO 17025, and other quality management systems, which are crucial for maintaining product quality, customer satisfaction, and legal compliance.
3. Prevention of Errors and Inaccuracies in Data Analysis
Calibration prevents errors and inaccuracies in data analysis. Instruments that are not calibrated may provide inaccurate measurements, leading to flawed data analysis and potentially incorrect decisions. Calibration ensures that the instruments are functioning within an acceptable range of accuracy, minimizing the risk of costly errors and enabling accurate data interpretation.
4. Enhancement of Product Quality and Consistency
Instrument calibration enhances product quality and consistency. By ensuring accurate measurements, calibrating instruments contributes to maintaining consistent product quality. In industries like food and beverage, pharmaceuticals, and automotive manufacturing, where precision and reliability are paramount, calibration helps deliver products that meet or exceed customer expectations.
5. Support for Process Optimization and Efficiency
Calibration supports process optimization and efficiency. Well-calibrated instruments provide reliable data that can be used to analyze and optimize processes. By identifying and rectifying deviations, calibration helps fine-tune processes, leading to increased efficiency, reduced waste, improved productivity, and overall cost savings.
6. Reduction of the Risk of Costly Production Failures
Instrument calibration reduces the risk of costly production failures. In industries such as oil and gas, chemical manufacturing, and power generation, where equipment failures can have severe consequences, calibration plays a crucial role in preventing unexpected breakdowns. By ensuring the accuracy and reliability of instruments, calibration minimizes the risk of production failures and associated financial losses.
7. Maintenance of Compliance with Industry-Specific Requirements
Calibration helps maintain compliance with industry-specific requirements. Different industries have their own standards and regulations, and calibration ensures that organizations meet those requirements. Whether it’s the aerospace, healthcare, or automotive industry, calibration is necessary to comply with industry-specific guidelines, maintain certifications, and ensure the safety and quality of products and services.
8. Extension of the Lifespan and Performance of Instruments
Regular calibration extends the lifespan and performance of instruments. Over time, instruments may drift from their initial calibration and provide inaccurate readings. By calibrating them at regular intervals, you can detect and correct any deviations, preserving the longevity of the instruments and maximizing their performance. This reduces the need for frequent repairs or replacements, saving both time and money.
9. Minimization of the Risk of Safety Hazards
Calibration minimizes the risk of safety hazards. In industries where safety is a critical concern, such as chemical processing, energy production, and healthcare, accurate measurements are vital for maintaining safe operating conditions. Calibration ensures that instruments used in safety systems, alarms, and monitoring equipment are functioning correctly, reducing the risk of accidents, injuries, and potential disasters.
10. Facilitation of Troubleshooting and Root Cause Analysis
Calibration facilitates troubleshooting and root cause analysis. When an instrument produces unexpected results or fails to perform as expected, calibration records can provide valuable insights into the underlying issues. By comparing the current performance to the calibrated baseline, maintenance professionals can identify the root causes of problems, streamline the troubleshooting process, and implement effective corrective actions.
11. Provision of Traceability and Accountability in Measurements
Instrument calibration provides traceability and accountability in measurements. Calibrated instruments are accompanied by calibration certificates that document the calibration process, standards used, and measurement uncertainties. These certificates establish traceability to recognized national or international measurement standards, ensuring the accuracy and reliability of the measurements. Additionally, calibration certificates provide accountability by identifying the responsible parties and their roles in the calibration process.
12. Support for Calibration Interval Management
Calibration interval management is crucial for efficient maintenance planning. By calibrating instruments regularly and tracking their performance over time, organizations can determine appropriate calibration intervals. Calibration interval management ensures that instruments are calibrated at the right frequency to maintain accuracy, optimize resources, and minimize downtime. It helps prevent unnecessary calibrations or prolonged periods without calibration, striking a balance between cost-effectiveness and measurement reliability.
13. Enablement of Compliance with Audit and Certification Requirements
Calibration enables compliance with audit and certification requirements. During audits or assessments, organizations are often required to provide evidence of calibration for their instruments. By having a robust calibration program in place and maintaining accurate calibration records, organizations can demonstrate their commitment to quality, compliance, and precision. Compliance with audit and certification requirements enhances the reputation and credibility of the organization.
14. Improvement of Customer Satisfaction and Trust
Calibration contributes to improved customer satisfaction and trust. Customers rely on accurate measurements and consistent product quality. By calibrating instruments, organizations ensure that their products meet the specified standards and customers’ expectations. Consistently delivering reliable and high-quality products builds trust, enhances customer satisfaction, and fosters long-term relationships, leading to increased customer loyalty and positive brand reputation.
15. Support for Effective Preventive Maintenance Programs
Calibration supports effective preventive maintenance programs. Preventive maintenance aims to detect and address issues before they result in failures or breakdowns. By including instrument calibration as part of the preventive maintenance program, organizations can proactively identify any deviations or abnormalities in instrument performance. This allows for timely adjustments or repairs, preventing potential equipment failures and costly downtime. Calibration acts as an integral component of preventive maintenance, ensuring that instruments remain in optimal condition and contributing to overall maintenance effectiveness.
16. Enhancement of Laboratory and Testing Accuracy
In laboratory and testing environments, calibration is crucial for ensuring accurate and reliable results. Precise measurements are essential in scientific research, quality control testing, and experiments. By calibrating instruments used in these settings, organizations can maintain the accuracy and consistency of their laboratory and testing processes. This leads to reliable data, valid research outcomes, and improved decision-making based on trustworthy results.
17. Ensurance of Compatibility and Consistency in Data Exchange
Data exchange between different instruments or systems requires compatibility and consistency. Calibration ensures that instruments used in data collection, analysis, and integration provide measurements that align with established standards. This compatibility and consistency in data exchange enable smooth collaboration, accurate data interpretation, and reliable decision-making across various departments, systems, or even organizations.
18. Enablement of Effective Instrument Comparison and Correlation
Instrument calibration enables effective instrument comparison and correlation. In situations where multiple instruments are used to measure the same parameter, calibration ensures that the readings are comparable and correlated. This allows for accurate data analysis, trend identification, and correlation studies. Calibration enables organizations to confidently integrate data from different instruments, facilitating comprehensive analysis and informed decision-making.
19. Facilitation of Data Integrity and Reliability in Research and Development
Research and development activities heavily rely on accurate and reliable data. Calibration plays a critical role in maintaining data integrity and reliability. Calibrated instruments provide precise measurements, reducing the potential for data errors or inconsistencies. This ensures that research outcomes and experimental results are trustworthy, enabling organizations to make informed decisions, develop innovative products, and advance scientific knowledge.
20. Minimization of Measurement Uncertainties and Variations
Calibration minimizes measurement uncertainties and variations. Instruments can be affected by various factors that introduce uncertainties or variations in measurements. By calibrating instruments regularly, organizations can identify and address these factors, reducing measurement uncertainties and variations. This leads to more precise and consistent measurements, improving the overall accuracy and reliability of data analysis and decision-making processes.
21. Support for Compliance with Good Laboratory Practices (GLP) and Good Manufacturing Practices (GMP)
Calibration supports compliance with Good Laboratory Practices (GLP) and Good Manufacturing Practices (GMP). These guidelines are essential in industries such as pharmaceuticals, biotechnology, and healthcare, where precision, accuracy, and quality are critical. By calibrating instruments according to GLP and GMP requirements, organizations demonstrate their commitment to maintaining high standards, ensuring product quality, and complying with regulatory expectations.
22. Enablement of Accurate Dosage and Formulation in Pharmaceuticals
Accurate dosage and formulation are crucial in the pharmaceutical industry. Improper calibration of instruments used in the production process can result in incorrect dosages or formulations, compromising the efficacy and safety of pharmaceutical products. Calibration ensures that instruments involved in dosage measurement, mixing, and formulation are precise and reliable, contributing to the production of high-quality medications with consistent therapeutic effects.
23. Enhancement of the Accuracy of Environmental Monitoring
Environmental monitoring calls for an exceptional level of precision, critical for correctly evaluating environmental conditions and potential impacts. This involves comprehensive procedures, including condition monitoring, which are integral to the calibration of instruments used in environmental monitoring. These instruments can range from air quality sensors and water quality analyzers to weather monitoring devices. The process of condition monitoring ensures the reliability and accuracy of data collection, which is indispensable for precise measurements.
24. Support for Calibration Traceability to National or International Standards
Calibration traceability is crucial for establishing the reliability and accuracy of measurements. Calibration processes should be traceable to recognized national or international measurement standards, such as those provided by national metrology institutes or accreditation bodies. By ensuring calibration traceability, organizations can have confidence in the accuracy of their measurements and demonstrate compliance with recognized standards, enhancing the credibility and reliability of their measurement results.
25. Enablement of Compliance with ISO 9001 and Other Quality Management Systems
ISO 9001 and other quality management systems require organizations to establish and maintain a calibration program. Compliance with these standards demonstrates a commitment to quality, customer satisfaction, and continuous improvement. Calibration plays a significant role in achieving compliance by ensuring accurate measurements, traceability, and adherence to documented procedures. Compliance with ISO 9001 and other quality management systems enhances the organization’s reputation, competitiveness, and ability to meet customer requirements.
26. Reduction of the Risk of Legal and Financial Liabilities
Failure to calibrate instruments can expose organizations to legal and financial liabilities. In industries where measurements impact safety, health, or regulatory compliance, inaccurate readings due to lack of calibration can result in legal penalties, litigation, or financial losses. By implementing a robust calibration program, organizations mitigate the risk of such liabilities, ensuring that measurements meet the necessary standards, regulations, and contractual obligations.
27. Facilitation of Effective Decision-Making Based on Accurate Measurements
Accurate measurements are essential for effective decision-making. In industries such as manufacturing, energy, and healthcare, decisions related to process adjustments, equipment maintenance, or product quality depend on reliable data. Calibration provides the assurance that the measurements used in decision-making are accurate and trustworthy. This enables organizations to make informed choices, optimize operations, and achieve their desired outcomes.
28. Ensures Proper Functioning of Safety Systems and Alarms
Proper calibration of instruments involved in safety systems and alarms is critical for the protection of personnel, assets, and the environment. Safety systems rely on accurate measurements to detect deviations, trigger alarms, and initiate safety protocols. By calibrating safety instruments regularly, organizations ensure that these systems function as intended, providing timely and accurate warnings in the event of any abnormality or hazard.
29. Optimization of Resource Allocation and Inventory Management
Calibration optimization improves resource allocation and inventory management. By calibrating instruments at appropriate intervals, organizations can allocate resources efficiently, avoiding unnecessary calibrations or excessive downtime. Accurate calibration records also help in managing inventory by ensuring that the necessary calibration components, standards, and tools are available when needed, reducing delays and improving overall operational efficiency.
30. Enhancement of the Overall Reliability and Credibility of Measurement Results
Instrument calibration enhances the overall reliability and credibility of measurement results. Whether it’s in research, manufacturing, or any other industry, accurate and traceable measurements are crucial for building trust in the data and results generated. Calibration ensures that the instruments
used to generate the measurements are accurate, reliable, and consistent. This, in turn, enhances the credibility of the measurement results, instills confidence in stakeholders, and strengthens the organization’s reputation for delivering quality and trustworthy outcomes.
Conclusion
Instrument calibration is of paramount importance in asset management and plant maintenance. It ensures accurate and reliable measurement readings, compliance with regulatory and quality standards, and prevents errors and inaccuracies in data analysis. By enhancing product quality, supporting process optimization, and minimizing safety hazards, calibration plays a crucial role in maximizing operational efficiency and reducing costly production failures. It facilitates troubleshooting, enables compliance with audit requirements, and improves customer satisfaction and trust. Moreover, calibration supports effective preventive maintenance programs, enhances laboratory accuracy, and ensures compatibility and consistency in data exchange. By optimizing resource allocation, minimizing measurement uncertainties, and enabling accurate decision-making, calibration contributes to the overall reliability and credibility of measurement results. Organizations that prioritize instrument calibration reap the benefits of improved efficiency, regulatory compliance, and enhanced stakeholder confidence.
Request a one-one demo with our solution engineering team.
Request a one-one demo with our solution engineering team.
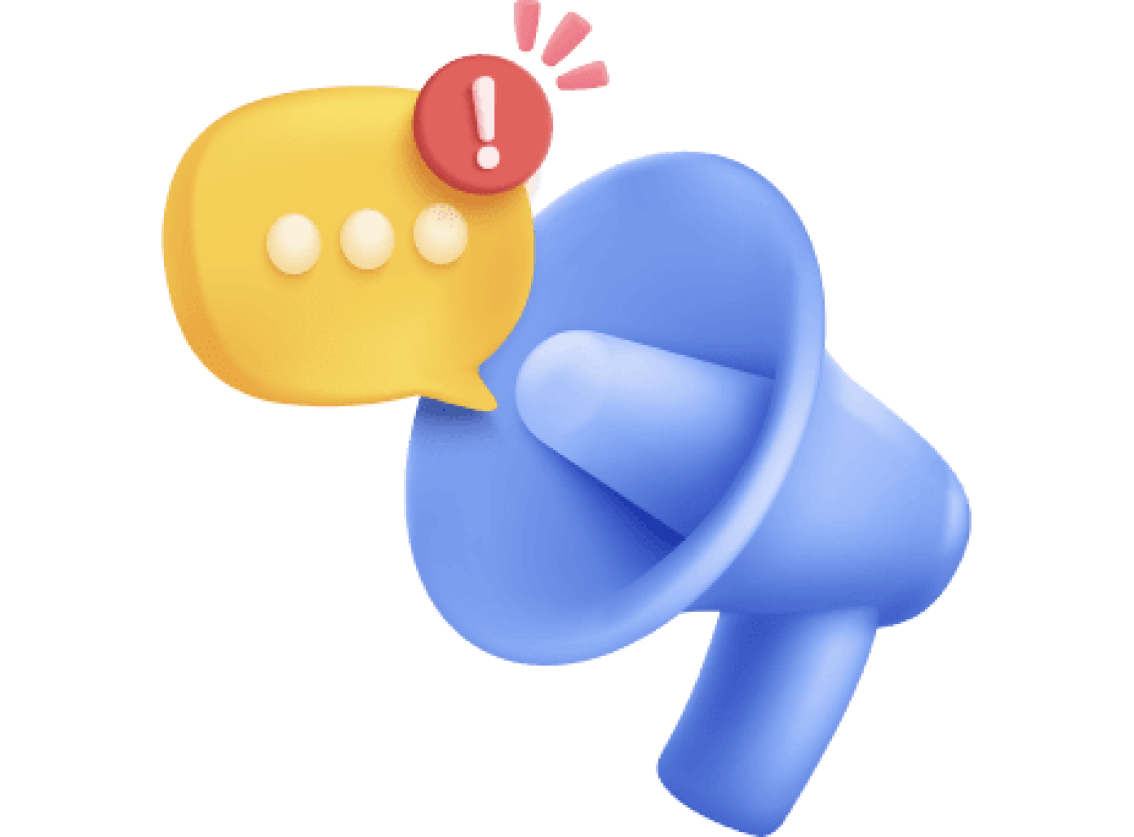