The Importance of Corrective Maintenance
The Importance of Corrective Maintenance
Table of Contents
ToggleThe Importance of Corrective Maintenance
Introduction:
Corrective maintenance is a crucial aspect of asset management and plant maintenance. It involves promptly addressing equipment failures and malfunctions to minimize production downtime, reduce costs, and ensure reliable equipment performance. By prioritizing urgent maintenance tasks and identifying underlying causes of failures, organizations can enhance operational efficiency, comply with safety standards, and optimize maintenance budgets. In this article, we will explore the key reasons why corrective maintenance is essential and its role in maintaining equipment reliability and overall business success.
1. Minimizing Production Downtime and Disruptions
Corrective maintenance allows for the swift resolution of equipment failures, minimizing production downtime and disruptions. By addressing issues promptly, organizations can avoid prolonged downtime that can result in lost productivity, missed deadlines, and dissatisfied customers.
2. Reducing the Risk of Equipment Damage and Further Complications
When equipment malfunctions are left unattended, they can lead to additional damage and complications. Corrective maintenance helps mitigate these risks by addressing problems at an early stage. Timely repairs prevent small issues from escalating into major failures that could cause extensive damage and require more costly repairs or replacements.
3. Preventing Potential Safety Hazards
Malfunctioning equipment can pose significant safety hazards in the workplace. Corrective maintenance plays a vital role in identifying and rectifying these hazards promptly. By ensuring the safe functioning of equipment, organizations protect their employees and maintain a secure working environment.
4. Ensuring Efficient and Reliable Equipment Performance
Corrective maintenance is essential for maintaining efficient and reliable equipment performance. By addressing failures promptly, organizations can prevent equipment from operating below optimal levels, ensuring smooth operations and preventing productivity bottlenecks.
5. Extending the Lifespan of Equipment
Promptly addressing equipment issues through corrective maintenance helps extend the lifespan of assets. By fixing problems before they worsen, organizations can avoid premature equipment failure, reduce the frequency of replacements, and optimize their long-term investments.
6. Saving Costs by Preventing Escalation
Corrective maintenance is a cost-effective strategy as it allows organizations to fix problems before they escalate. By addressing issues early on, organizations can avoid costly repairs, replacements, and production losses that would arise from prolonged equipment downtime.
7. Improving Overall Operational Efficiency
Effective corrective maintenance contributes to overall operational efficiency. By minimizing downtime, organizations can enhance productivity and meet production targets. It allows maintenance teams to focus their efforts on critical repairs, ensuring resources are allocated effectively.
8. Targeted Repairs and Replacements
Corrective maintenance enables organizations to prioritize repairs and replacements based on urgency and impact. By analyzing failure data, organizations can identify critical assets that require immediate attention, ensuring resources are allocated where they are most needed.
9. Identifying Underlying Causes of Equipment Failures
Corrective maintenance helps in identifying the underlying causes of equipment failures. By analyzing failure data, organizations can gain insights into recurring issues, take preventive actions, and improve maintenance practices to reduce the frequency of
failures. This proactive approach helps in addressing root causes and implementing effective solutions, resulting in improved equipment reliability.
10. Prioritizing Urgent Maintenance Tasks
Corrective maintenance allows organizations to prioritize urgent maintenance tasks. By promptly addressing critical failures, organizations can prevent further damage and disruptions. This ensures that resources and efforts are focused on the most pressing issues, reducing the impact on operations and minimizing downtime.
11. Compliance with Regulatory Requirements and Safety Standards
Corrective maintenance plays a vital role in ensuring compliance with regulatory requirements and safety standards. By promptly addressing equipment failures, organizations demonstrate their commitment to maintaining a safe working environment and adhere to industry regulations. This helps in avoiding penalties, legal issues, and reputational damage.
12. Maintaining Product and Service Quality
Equipment failures can have a direct impact on product and service quality. Corrective maintenance helps in maintaining consistent quality standards by promptly addressing equipment malfunctions. This ensures that products and services meet customer expectations, enhancing customer satisfaction and preserving the reputation of the organization.
13. Minimizing Unexpected Breakdowns and Associated Costs
Unplanned equipment breakdowns can result in unexpected costs and disruptions. Corrective maintenance helps in minimizing these breakdowns by addressing issues as soon as they arise. By proactively maintaining equipment, organizations can reduce the risk of sudden failures, avoid costly emergency repairs, and maintain smooth operations.
14. Identifying Trends and Patterns in Equipment Failures
Corrective maintenance assists in identifying trends and patterns in equipment failures. By analyzing failure data, organizations can detect recurring issues or common failure modes. This information can be used to identify systemic problems, develop preventive maintenance strategies, and improve equipment reliability.
15. Analysis of Failure Data for Improved Maintenance Practices
Corrective maintenance provides valuable data on equipment failures that can be analyzed to improve maintenance practices. By examining failure patterns, organizations can identify areas for improvement, such as enhancing training programs, adjusting maintenance schedules, or implementing equipment upgrades. This data-driven approach helps optimize maintenance activities and increase equipment availability.
16. Optimizing Spare Parts Inventory Management
Effective corrective maintenance enables organizations to optimize spare parts inventory management. By analyzing failure data and understanding the frequency of component failures, organizations can maintain an appropriate inventory of spare parts. This prevents unnecessary stockpiling of parts, reduces costs, and ensures timely availability when needed.
17. Insights into Equipment Performance and Reliability
Corrective maintenance provides valuable insights into equipment performance and reliability. By implementing condition monitoring and recording failure data, organizations can track the performance of assets, identify equipment that requires attention, and make data-driven decisions regarding repairs, replacements, or upgrades. This proactive approach, rooted in diligent condition monitoring, helps in maintaining high equipment reliability.
18. Troubleshooting and Diagnostics
Corrective maintenance facilitates troubleshooting and diagnostics. When equipment fails, maintenance teams can quickly diagnose the problem, identify the root cause, and implement appropriate solutions. This reduces the time required for repairs, minimizes production downtime, and improves overall operational efficiency.
19. Timely Resolution of Equipment Issues
Corrective maintenance ensures the timely resolution of equipment issues. By promptly addressing failures, organizations can avoid production delays and maintain a smooth workflow. This helps in meeting customer demands, fulfilling orders on time, and sustaining customer satisfaction.
20. Maintaining Customer Satisfaction
Corrective maintenance plays a critical role in maintaining customer satisfaction.
By minimizing equipment failures and addressing issues promptly, organizations can deliver products and services without disruptions. This enhances customer satisfaction by ensuring reliable and timely deliveries, reducing the risk of delays or quality issues that could negatively impact customer relationships.
21. Minimizing the Risk of Collateral Damage
Equipment failures can sometimes lead to collateral damage to other equipment or processes. Corrective maintenance helps in minimizing this risk by addressing failures promptly. By preventing further damage or disruptions, organizations can avoid additional costs, maintain operational continuity, and protect their assets.
22. Identifying Opportunities for Equipment Upgrades or Replacements
Corrective maintenance provides valuable insights into the performance and condition of equipment. By analyzing failure data and identifying recurring issues, organizations can recognize opportunities for equipment upgrades or replacements. This proactive approach ensures that organizations stay up to date with technology advancements, improving operational efficiency and competitiveness.
23. Equipment Maintenance Based on Usage Patterns
Corrective maintenance enables organizations to tailor their maintenance efforts based on equipment usage patterns. By analyzing failure data and understanding the frequency and intensity of equipment usage, organizations can optimize maintenance schedules, allocate resources efficiently, and reduce unnecessary maintenance activities.
24. Effective Resource Allocation
Corrective maintenance allows organizations to allocate their resources effectively. By prioritizing maintenance tasks based on urgency and impact, organizations can optimize the allocation of manpower, time, and budget. This ensures that resources are utilized where they are most needed, enhancing operational efficiency and cost-effectiveness.
25. Identifying and Rectifying Hidden or Intermittent Equipment Faults
Corrective maintenance helps in identifying and rectifying hidden or intermittent equipment faults. These faults may not be immediately apparent but can cause intermittent failures or affect equipment performance over time. By conducting thorough inspections and analyzing failure data, organizations can uncover these hidden faults and address them before they lead to significant disruptions.
26. Maintaining a Safe Working Environment
Corrective maintenance contributes to maintaining a safe working environment. By promptly addressing equipment failures and potential safety hazards, organizations ensure the well-being of their employees. This fosters a culture of safety, boosts employee morale, and reduces the risk of accidents or injuries.
27. Support for Proactive Maintenance Strategies
Corrective maintenance plays a vital role in supporting proactive maintenance strategies. By addressing failures promptly, organizations can prevent small issues from evolving into larger problems. This reduces the need for reactive maintenance and allows organizations to focus on preventive maintenance activities, ultimately improving equipment reliability and reducing maintenance costs.
28. Optimization of Maintenance Budget Allocation
Corrective maintenance helps in optimizing the allocation of maintenance budgets. By promptly addressing equipment failures, organizations can avoid costly emergency repairs or replacements. This enables them to allocate their budget more efficiently, focusing on preventive maintenance measures that prolong equipment lifespan and minimize unplanned expenses.
29. Continuous Improvement through Failure Data Analysis
Corrective maintenance provides valuable data through failure analysis. By analyzing failure data, organizations can identify trends, patterns, and common issues. This information can be used to drive continuous improvement initiatives, refine maintenance strategies, and enhance overall equipment reliability and performance.
30. Conclusion – Ensuring Efficient and Reliable Operations
Corrective maintenance is a crucial aspect of asset management and plant maintenance. By promptly addressing equipment failures, organizations can minimize production downtime, reduce costs, ensure reliable operations, and maintain high-quality products and services. The proactive nature of corrective maintenance allows organizations to identify underlying causes
of failures, prioritize urgent tasks, and optimize resource allocation. Furthermore, corrective maintenance helps organizations comply with safety standards, improve operational efficiency, and make informed decisions regarding equipment upgrades or replacements. By analyzing failure data and implementing continuous improvement practices, organizations can enhance equipment reliability, extend asset lifespan, and achieve long-term business success.
To learn more about the importance of corrective maintenance and its impact on asset management and plant maintenance, visit MaintWiz at www.maintwiz.com/corrective-maintenance.
Remember, proactive and timely corrective maintenance is key to minimizing disruptions, optimizing resources, and ensuring the smooth functioning of equipment. Incorporating effective maintenance strategies into your business operations will not only improve equipment reliability but also contribute to overall operational efficiency and customer satisfaction.
Take action today and prioritize corrective maintenance to maximize the potential of your assets, reduce costs, and enhance your organization’s competitiveness in the market.
Request a one-one demo with our solution engineering team.
Request a one-one demo with our solution engineering team.
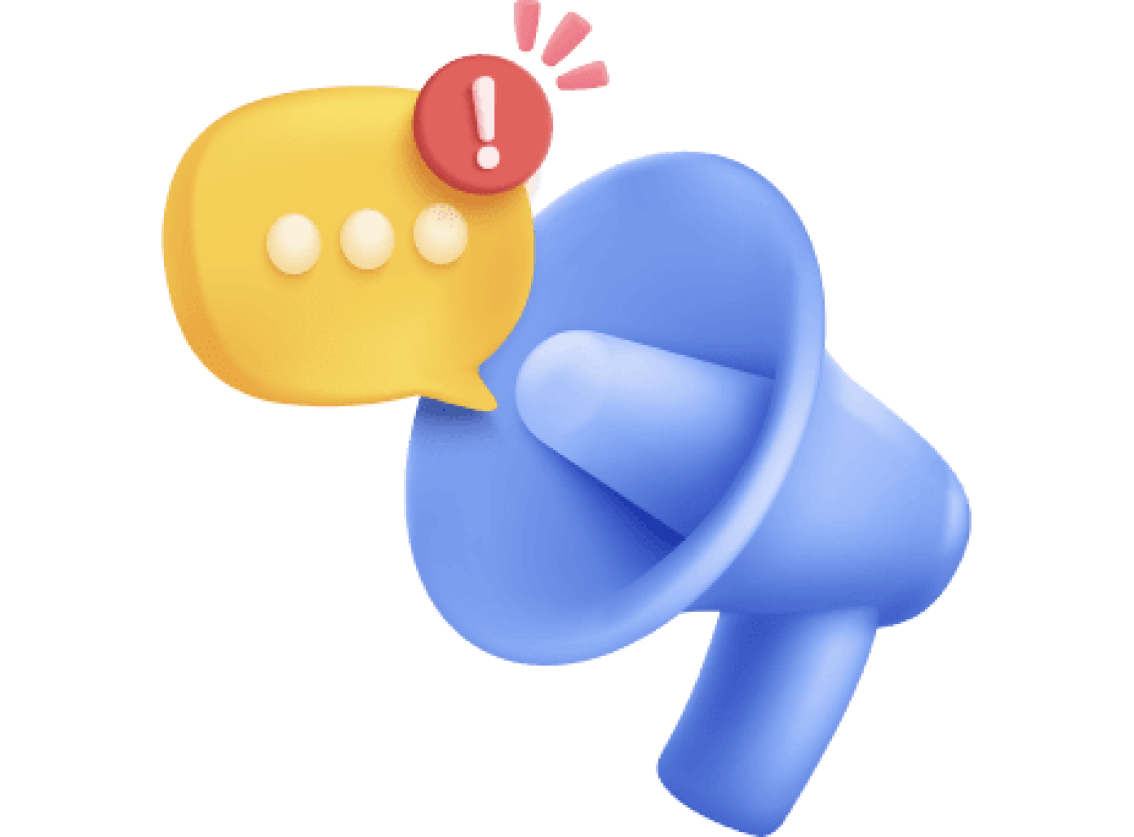