How to Use Data Analytics to Improve Your
Maintenance Operations
Data Analytics To Improve Maintenance Operations
Table of Contents
ToggleHow to Use Data Analytics to Improve Your Maintenance Operations
Welcome to MaintWiz CMMS, where we empower your maintenance operations with the transformative power of data analytics. In today’s digital age, leveraging data-driven insights is crucial for optimizing maintenance schedules, predicting failures, and enhancing asset reliability. Let’s explore how our cutting-edge CMMS solution can help you unlock the full potential of data analytics in maintenance.
1. Introduction to Data Analytics in Maintenance Operations
Modern maintenance operations rely on data analytics to gain valuable insights into equipment performance, optimize maintenance strategies, and reduce downtime. By harnessing the power of data, you can make informed decisions that drive operational efficiency and cost savings.
2. Collecting and Preparing Data for Analysis
To utilize data analytics effectively, it’s crucial to identify and gather relevant data from various sources such as sensors, equipment logs, and maintenance records. Our CMMS streamlines the data collection process and provides tools for data cleaning and preprocessing, ensuring data accuracy and consistency.
3. Key Performance Indicators (KPIs) for Maintenance
Defining meaningful KPIs is essential for measuring maintenance performance and aligning it with your business goals. Our CMMS enables you to track and analyze essential KPIs such as equipment downtime, mean time between failures, and overall equipment effectiveness, empowering you to make data-driven decisions to improve maintenance efficiency.
4. Implementing Data Analytics Tools and Technologies
Our CMMS integrates advanced data analytics tools such as predictive analytics and machine learning algorithms to uncover patterns, predict failures, and optimize maintenance schedules. With a user-friendly interface, you can seamlessly implement these tools into your existing maintenance management systems.
5. Analyzing Maintenance Data for Insights
Our CMMS offers powerful data analysis capabilities, including exploratory data analysis techniques and statistical analysis methods. By visualizing data and identifying patterns, trends, and anomalies, you gain valuable insights that drive proactive maintenance decision-making and improve overall equipment performance.
6. Predictive Maintenance and Failure Analysis
Utilizing data analytics, our CMMS empowers you to predict equipment failures before they occur. By identifying failure patterns and performing root cause analysis, you can implement preventive maintenance strategies to eliminate costly unplanned downtime and extend asset lifespan.
7. Optimization and Continuous Improvement
With data analytics, you can optimize maintenance schedules, ensuring maintenance activities are performed at the right time, reducing unnecessary maintenance and associated costs. Our CMMS also facilitates continuous improvement through feedback loops, enabling you to learn from data-driven insights and enhance maintenance processes.
8. Data Security and Privacy Considerations
We understand the importance of data security and privacy in maintenance analytics. MaintWiz CMMS follows best practices for data storage, access control, and encryption to safeguard your valuable maintenance data. Our system also ensures compliance with data protection regulations such as GDPR and CCPA.
9. Case Studies and Success Stories
Explore real-world case studies and success stories of organizations that have leveraged data analytics to improve maintenance operations. These are sourced from publicly available material. Discover how world over leading businesses have achieved significant cost savings, operational efficiency, and enhanced equipment reliability.
Leading Automotive Manufacturer
Challenges: High equipment downtime, reactive maintenance practices
Solution: Implemented a data analytics solution to monitor equipment health in real-time
How Condition Monitoring Helped: Predictive analytics identified early signs of equipment failure, allowing proactive maintenance and reducing unplanned downtime. The system provided insights into optimal maintenance schedules based on asset condition, leading to improved operational efficiency.
Acme Chemicals – Chemical Manufacturing
Challenges: Costly breakdowns, inefficient maintenance strategies
Solution: Leveraged data analytics to analyze historical maintenance data and identify failure patterns
How Condition Monitoring Helped: Through predictive maintenance, the company could detect abnormalities in critical equipment, preventing breakdowns and enabling planned maintenance. The data-driven approach optimized maintenance schedules, reducing overall maintenance costs.
Global Energy Solutions – Oil and Gas
Challenges: Unplanned shutdowns, high maintenance costs
Solution: Implemented an IoT-enabled system to collect real-time sensor data from equipment
How Condition Monitoring Helped: The system utilized data analytics algorithms to analyze equipment performance trends, detecting anomalies and predicting potential failures. By implementing predictive maintenance strategies, the company minimized unplanned shutdowns, improved safety, and reduced maintenance costs.
Precision Manufacturing Company – Aerospace
Challenges: Inefficient spare parts management, high inventory costs
Solution: Utilized data analytics to optimize spare parts inventory and procurement
How Condition Monitoring Helped: By analyzing equipment performance and failure patterns, the company identified critical spare parts and optimized inventory levels. Predictive analytics helped schedule maintenance activities to align with spare parts availability, reducing downtime and saving costs.
Mega Steel Mills – Steel Manufacturing
Challenges: Inaccurate maintenance forecasting, excessive maintenance activities
Solution: Deployed a data analytics platform to analyze historical and real-time maintenance data
How Condition Monitoring Helped: The system leveraged condition monitoring sensors to collect equipment data, enabling predictive maintenance. By analyzing equipment health and performance trends, the company achieved accurate maintenance forecasting, reducing unnecessary maintenance activities and improving overall equipment effectiveness.
PowerGen Utilities – Power Generation
Challenges: High maintenance costs, equipment failures
Solution: Integrated data analytics with existing maintenance management systems
How Condition Monitoring Helped: By combining data from multiple sources, including maintenance records, sensor data, and environmental factors, the company implemented predictive maintenance models. This enabled early detection of potential failures, reduced maintenance costs, and increased equipment reliability.
PharmaLife – Pharmaceutical Manufacturing
Challenges: Compliance with regulatory requirements, quality control issues
Solution: Utilized data analytics to monitor critical process parameters and equipment performance
How Condition Monitoring Helped: By analyzing real-time sensor data and historical quality data, the company implemented predictive analytics models to identify potential quality issues in the production process. This enabled proactive maintenance, ensuring compliance, and improving product quality.
FoodPro Inc. – Food and Beverage
Challenges: Unplanned downtime, ineffective maintenance scheduling
Solution: Implemented a data analytics solution to monitor equipment performance
How Condition Monitoring Helped: Real-time condition monitoring sensors were used to collect equipment data. The analytics platform provided insights into equipment health, enabling predictive maintenance scheduling. This reduced unplanned downtime, optimized maintenance efforts, and improved overall operational efficiency.
AutoParts Manufacturing – Automotive Components
Challenges: Equipment reliability issues, high maintenance costs
Solution: Adopted data analytics to monitor and analyze equipment performance
How Condition Monitoring Helped: The company utilized data analytics to monitor asset performance in real-time, enabling early detection of anomalies and potential failures. By implementing predictive maintenance, the company reduced breakdowns, improved asset utilization, and increased productivity.
TechFab Electronics – Electronics Manufacturing
Challenges: Inefficient asset utilization, frequent breakdowns
Solution: Implemented an integrated data analytics and machine learning system
How Condition Monitoring Helped: The system collected equipment sensor data and analyzed it using machine learning algorithms. This enabled the company to identify failure patterns, predict maintenance needs, and optimize maintenance schedules. By proactively addressing equipment reliability issues, the company reduced maintenance costs and improved overall equipment effectiveness.
10. Future Trends in Maintenance Data Analytics
As technology continues to advance, the future of maintenance analytics looks promising. With emerging technologies like IoT and AI, our CMMS is continuously evolving to stay at the forefront of predictive maintenance advancements. We aim to help you navigate the challenges and embrace the opportunities that big data presents for maintenance optimization.
Conclusion
At MaintWiz CMMS, we believe that data analytics is the key to unlocking the full potential of your maintenance operations. By harnessing the power of data-driven insights, you can optimize maintenance schedules, predict failures, and improve asset reliability. Take the first step towards transforming your maintenance operations by leveraging the advanced features and benefits offered by our CMMS.
Key Takeaways:
- Data analytics enhances maintenance decision-making and operational efficiency.
- Effective data collection and preparation are essential for accurate analysis.
- Meaningful KPIs help measure maintenance performance and drive improvements.
- Implementing data analytics tools empowers proactive maintenance strategies.
- Analyzing maintenance data reveals valuable insights for optimization.
- Predictive maintenance prevents failures and extends equipment lifespan.
- Data-driven optimization and continuous improvement enhance reliability.
- Data security and privacy are prioritized in MaintWiz CMMS.
- Real-world case studies highlight the impact of data analytics.
- Future trends involve emerging technologies and big data challenges.
Request a one-one demo with our solution engineering team.
Request a one-one demo with our solution engineering team.
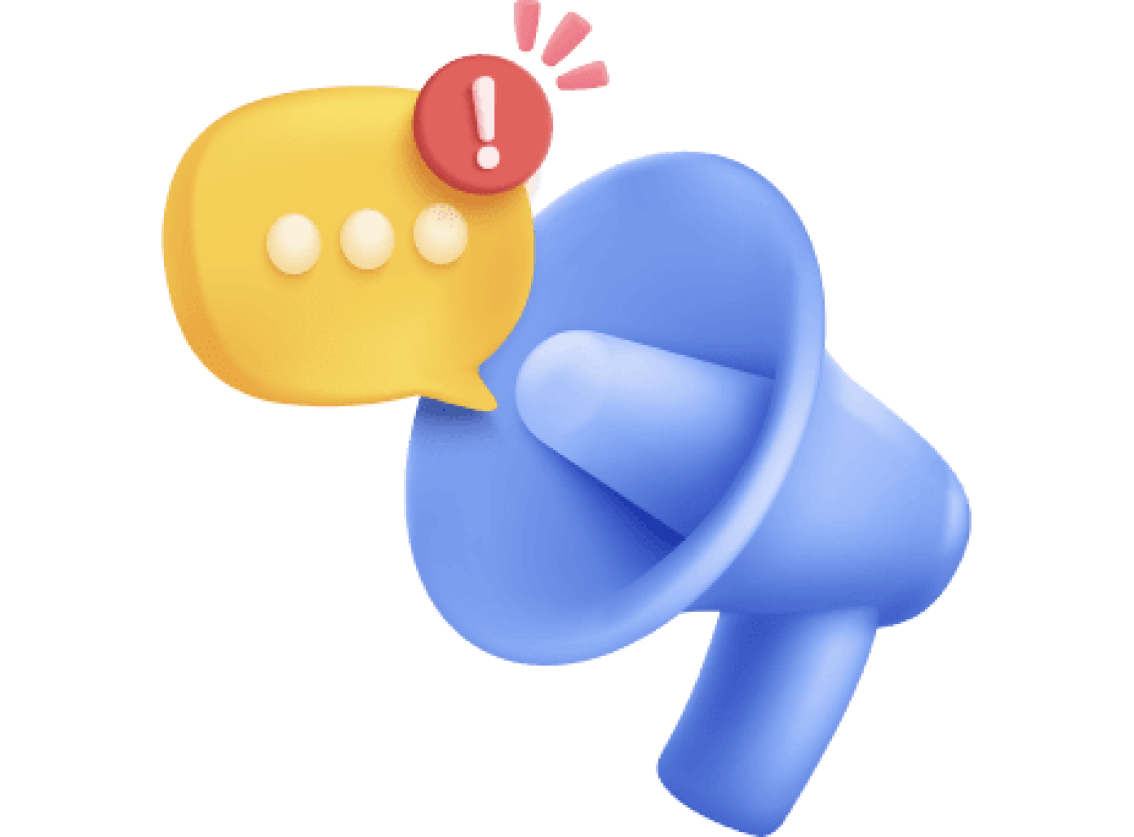