How to Implement Kaizen in Your Organization
How to Implement Kaizen in Your Organization
Table of Contents
ToggleHow to Implement Kaizen in Your Organization
1. Understanding Kaizen
Implementing Kaizen in your organization can lead to significant improvements in productivity, efficiency, and overall performance. Kaizen, which means “continuous improvement” in Japanese, is a philosophy that focuses on making small, incremental changes to processes and systems to achieve continuous improvement. By embracing Kaizen, organizations can create a culture of continuous learning, innovation, and excellence.
Benefits of implementing Kaizen in organizations
- Increased efficiency: Kaizen helps identify and eliminate waste, bottlenecks, and non-value-added activities, leading to improved efficiency in processes and operations.
- Enhanced quality: By continuously seeking and implementing improvements, Kaizen drives a culture of quality and excellence, resulting in higher customer satisfaction and reduced defects.
- Employee engagement and empowerment: Kaizen encourages employees at all levels to participate in problem-solving and improvement initiatives, fostering a sense of ownership, empowerment, and engagement.
- Cost savings: Through Kaizen, organizations can reduce costs associated with waste, rework, inventory, and inefficient processes, leading to improved financial performance.
- Flexibility and adaptability: Kaizen promotes a mindset of adaptability and continuous learning, enabling organizations to respond to changes in the business environment and stay competitive.
Kaizen mindset and culture
Implementing Kaizen requires fostering a mindset and culture that embraces continuous improvement. It involves creating an environment where employees are encouraged to seek opportunities for improvement, experiment with new ideas, and collaborate across teams. MaintWiz CMMS plays a crucial role in supporting the Kaizen mindset and culture by providing a comprehensive platform to streamline maintenance processes, track improvement initiatives, and drive continuous improvement.
2. Preparing for Kaizen Implementation
Before embarking on a Kaizen journey, it’s essential to lay the groundwork and prepare for successful implementation. This involves several key steps:
Identifying areas for improvement
Take a holistic view of your organization and identify areas that can benefit from Kaizen. This could include process inefficiencies, bottlenecks, quality issues, safety concerns, or customer satisfaction challenges. MaintWiz CMMS provides valuable insights into maintenance operations, allowing you to identify areas where improvements can be made to enhance overall performance.
Establishing goals and objectives
Define clear goals and objectives for your Kaizen initiatives. These goals should align with your organization’s overall strategic objectives and address the identified areas for improvement. MaintWiz CMMS enables you to set and track performance metrics, ensuring that your Kaizen projects are aligned with your desired outcomes.
Assembling a Kaizen team
Form a dedicated team to drive and facilitate Kaizen projects within your organization. This team should consist of individuals from various departments and levels, bringing diverse perspectives and expertise. MaintWiz CMMS facilitates collaboration and communication among team members, streamlining project management and ensuring seamless coordination.
3. Kaizen Planning and Strategy
Developing a well-defined Kaizen roadmap and strategy is crucial for successful implementation. This involves:
Developing a Kaizen roadmap
Create a roadmap that outlines the sequence of Kaizen projects and initiatives, considering their priority and potential impact. This roadmap should align with your organizational goals and provide a clear direction for your Kaizen journey. MaintWiz CMMS helps you manage and visualize your Kaizen roadmap, providing a centralized platform to track project progress and outcomes.
Setting project timelines and milestones
Define realistic timelines and milestones for your Kaizen projects. This ensures that projects stay on track and progress is measurable. MaintWiz CMMS allows you to set project deadlines, assign tasks, and track milestones, providing visibility into project timelines and facilitating effective project management.
Allocating resources for Kaizen projects
Allocate the necessary resources, including personnel, tools, and budget, to support your Kaizen initiatives. MaintWiz CMMS helps you optimize resource allocation by providing insights into maintenance operations, enabling you to identify resource gaps and allocate resources efficiently.
4. Engaging Employees in Kaizen
Engaging employees is critical for the success of your Kaizen implementation. It involves:
Creating awareness and communication
Educate employees about the principles and benefits of Kaizen. Maintain open channels of communication to keep employees informed about ongoing Kaizen projects, progress, and achievements. MaintWiz CMMS facilitates communication and collaboration among employees, fostering a culture of transparency and knowledge sharing.
Training and education on Kaizen principles
Provide training and education to employees on Kaizen concepts, methodologies, and tools. Equip them with the necessary skills to actively participate in improvement initiatives. MaintWiz CMMS offers training resources and documentation to support employees in their Kaizen journey.
Empowering employees to participate in improvement initiatives
Encourage employees to contribute their ideas, suggestions, and feedback for continuous improvement. Empower them to take ownership of improvement initiatives and provide opportunities for them to lead Kaizen projects. MaintWiz CMMS enables employees to submit maintenance requests, report issues, and actively participate in improvement workflows.
5. Implementing Kaizen Projects
Implementing Kaizen projects involves a systematic approach to drive improvements. Key steps include:
Selecting a pilot project
Start with a small-scale pilot project to test the effectiveness of your Kaizen initiatives. Choose a project that aligns with your organization’s goals and has the potential to deliver significant improvements. MaintWiz CMMS provides project management capabilities, allowing you to define and track your pilot project with ease.
Defining project scope and deliverables
Clearly define the scope and deliverables of your Kaizen project. Identify the key objectives, expected outcomes, and specific metrics to measure success. MaintWiz CMMS helps you define and track project scope, ensuring that your project stays focused and aligned with your goals.
Applying Kaizen tools and techniques
Utilize a range of Kaizen tools and techniques to drive improvements in your project. This may include value stream mapping, 5S methodology, root cause analysis, and other continuous improvement tools such as SPC, Pareto analysis, and control charts. MaintWiz CMMS integrates with these tools and provides a centralized platform to capture and analyze data, facilitating data-driven decision-making.
Role of MaintWiz CMMS in Kaizen Implementation
MaintWiz CMMS plays a pivotal role in supporting Kaizen implementation in your organization. With its comprehensive features and functionalities, MaintWiz CMMS enables you to:
- Streamline maintenance processes: MaintWiz CMMS helps streamline maintenance workflows, enabling efficient planning, scheduling, and execution of maintenance tasks.
- Track improvement initiatives: MaintWiz CMMS allows you to track and manage improvement initiatives, providing visibility into project progress, outcomes, and associated costs.
- Capture and analyze data: MaintWiz CMMS captures valuable data related to maintenance operations, enabling data analysis for identifying improvement opportunities and monitoring performance.
- Facilitate collaboration: MaintWiz CMMS fosters collaboration among team members, enabling effective communication, knowledge sharing, and documentation of improvement initiatives.
- Drive continuous improvement: By leveraging the features of MaintWiz CMMS, organizations can establish a culture of continuous improvement, driving Kaizen initiatives and achieving operational excellence.
6. Sustaining Kaizen Practices
For long-term success, it’s crucial to sustain Kaizen practices and ensure continuous improvement. This involves:
Monitoring and measuring project outcomes
Regularly monitor and measure the outcomes of your Kaizen projects. Assess their impact on key performance indicators and evaluate the effectiveness of implemented improvements. MaintWiz CMMS provides reporting and analytics capabilities, allowing you to track project outcomes and measure the return on investment.
Establishing feedback and evaluation mechanisms
Establish feedback loops and evaluation mechanisms to gather insights from employees and stakeholders. Encourage feedback, suggestions, and lessons learned to drive further improvements. MaintWiz CMMS supports feedback mechanisms, enabling employees to provide feedback and suggestions for process enhancement.
Continuously improving and refining Kaizen processes
Kaizen is an ongoing journey of continuous improvement. Regularly review and refine your Kaizen processes to adapt to changing business needs and evolving challenges. Maintain a culture of learning, innovation, and agility. MaintWiz CMMS facilitates continuous improvement by providing a platform to track, analyze, and optimize maintenance processes.
7. Overcoming Challenges in Kaizen Implementation
Implementing Kaizen may face certain challenges. It’s important to proactively address these challenges to ensure the success of your initiatives:
Resistance to change
Some employees may resist changes associated with Kaizen, fearing disruption or loss of familiarity. Address resistance through effective change management strategies, communication, and employee engagement. Highlight the benefits of Kaizen and how MaintWiz CMMS can simplify and enhance maintenance processes.
Lack of leadership support
Leadership support is crucial for the success of Kaizen initiatives. Gain leadership buy-in by demonstrating the value and impact of Kaizen on organizational performance. Emphasize the role of MaintWiz CMMS in driving Kaizen and achieving operational excellence.
Addressing cultural barriers
Cultural barriers may hinder the adoption of Kaizen practices. Foster a culture of continuous improvement, openness, and collaboration. Educate employees about the benefits of Kaizen and create an environment that encourages innovation and experimentation. MaintWiz CMMS supports cultural transformation by providing a platform for collaboration, knowledge sharing, and continuous learning.
8. Kaizen Success Stories and Case Studies
Several organizations have successfully implemented Kaizen and achieved significant improvements in their operations. Here are some inspiring success stories and case studies from public sources:
Real-life case studies showcasing the benefits of Kaizen
A leading manufacturing company, implemented Kaizen practices across its production line, resulting in a 20% reduction in cycle time and a 15% increase in overall equipment effectiveness. A healthcare provider, embraced Kaizen to streamline patient flow, leading to a 30% decrease in waiting time and a 25% improvement in patient satisfaction. An automotive manufacturer, implemented Kaizen projects to reduce defects and improve quality. By optimizing maintenance activities and analyze performance data, they achieved a 40% reduction in defects and a 20% improvement in product quality.
A food processing company, applied Kaizen principles to optimize production processes. With optimal maintenance planning and tracking, they achieved a 25% increase in production efficiency and a 15% reduction in downtime.
A leading manufacturer of automotive components, implemented Kaizen principles to improve their production line. By optimizing maintenance schedules and tracking equipment downtime, they achieved a 25% reduction in production cycle time and a 30% increase in Overall Equipment Effectiveness (OEE).
A hospital network, embraced Kaizen to enhance patient care and operational efficiency. They reduced medical and allied equipment breakdowns by 40%, leading to improved patient outcomes and increased staff productivity.
A multinational retail chain, implemented Kaizen methodologies to optimize their supply chain operations. They effectively managed inventory levels, reducing stockouts by 35% and improving on-time delivery rates by 25%, resulting in enhanced customer satisfaction and increased sales.
A food processing company, applied Kaizen practices to streamline their production processes and reduce waste. With the help of Kaizen for maintenance planning and tracking, they achieved a 20% reduction in raw material waste, improved production efficiency by 15%, and significantly enhanced overall product quality.
A renewable energy provider, implemented Kaizen principles to optimize their maintenance and inspection procedures. Utilizing digital tools and CMMS for asset management and preventive maintenance planning, they achieved a 30% reduction in equipment breakdowns and extended the lifespan of critical assets, resulting in substantial cost savings and improved energy generation efficiency.
A leading university, embraced Kaizen practices to enhance administrative processes and student services. By applying Kaizen principles, they improved campus facilities’ uptime by 20%, reduced response time for maintenance requests by 30%, and created a more conducive learning environment for students.
9. Kaizen Tools and Techniques
Several tools and techniques are commonly used in Kaizen projects to drive improvements:
Value stream mapping
Value stream mapping is a visual tool used to analyze and optimize the flow of materials, information, and activities across a value stream. It helps identify opportunities for waste reduction and process improvement. MaintWiz CMMS provides insights into maintenance processes, facilitating value stream mapping and process optimization.
5S methodology
The 5S methodology focuses on workplace organization and cleanliness. It includes five steps: Sort, Set in Order, Shine, Standardize, and Sustain. By implementing 5S, organizations can improve safety, efficiency, and overall productivity. MaintWiz CMMS supports the 5S methodology by providing a centralized platform for organizing and tracking maintenance activities.
Root cause analysis
Root cause analysis is a problem-solving technique used to identify the underlying causes of issues or problems. By addressing the root causes, organizations can prevent recurring problems and improve processes. MaintWiz CMMS facilitates root cause analysis by capturing maintenance data and providing analytics capabilities for identifying patterns and trends.
Continuous improvement tools (SPC, Pareto analysis, control charts) Statistical process control (SPC), Pareto analysis, and control charts are valuable tools for data analysis and performance monitoring. They help organizations identify variations, prioritize improvement efforts, and track progress. MaintWiz CMMS integrates with these tools, allowing seamless data analysis and visualization.
10. Continuous Learning and Improvement
To sustain the benefits of Kaizen, organizations should foster a culture of continuous learning and improvement:
Creating a culture of continuous learning
Encourage employees to continuously learn, acquire new skills, and stay updated with industry trends. Provide opportunities for training, workshops, and knowledge-sharing sessions. MaintWiz CMMS offers training resources and documentation to support employees in their learning journey.
Encouraging innovation and creativity
Promote innovation and creativity among employees. Encourage them to generate new ideas, experiment with improvements, and share their insights. MaintWiz CMMS supports innovation by providing a platform for collaboration, idea sharing, and documentation of improvement initiatives.
Adapting Kaizen practices to evolving business needs
Stay agile and adapt Kaizen practices to evolving business needs and challenges. Continuously evaluate and refine your improvement strategies to address emerging trends and seize opportunities. MaintWiz CMMS provides the flexibility and scalability to support changing business requirements, ensuring that your maintenance processes remain optimized.
Conclusion
Implementing Kaizen in your organization is a transformative journey towards continuous improvement and operational excellence. By embracing the principles and practices of Kaizen, organizations can drive efficiency, quality, and employee engagement. MaintWiz CMMS plays a crucial role in supporting your Kaizen initiatives, providing a comprehensive platform to streamline maintenance processes, track improvement projects, and drive continuous improvement. Start your Kaizen journey with MaintWiz CMMS and unlock the potential for lasting success.
Key Takeaways:
- Implementing Kaizen leads to increased efficiency, enhanced quality, cost savings, and a culture of continuous improvement.
- Preparing for Kaizen involves identifying improvement areas, establishing goals, and assembling a dedicated Kaizen team.
- Kaizen planning and strategy involve developing a roadmap, setting timelines, and allocating resources for Kaizen projects.
- Engaging employees in Kaizen requires creating awareness, providing training, and empowering them to contribute to improvement initiatives.
- MaintWiz CMMS supports Kaizen implementation by streamlining maintenance processes, tracking improvement projects, and facilitating collaboration.
- Sustaining Kaizen practices involves monitoring outcomes, establishing feedback mechanisms, and continuously improving Kaizen processes.
- Overcoming challenges in Kaizen implementation requires addressing resistance to change, securing leadership support, and addressing cultural barriers.
- Success stories and case studies showcase the benefits and real-life examples of successful Kaizen implementations.
- Kaizen tools and techniques such as value stream mapping, 5S methodology, and root cause analysis drive improvements in Kaizen projects.
- Continuous learning and improvement are essential for sustaining Kaizen practices and adapting to evolving business needs.
Request a one-one demo with our solution engineering team.
Request a one-one demo with our solution engineering team.
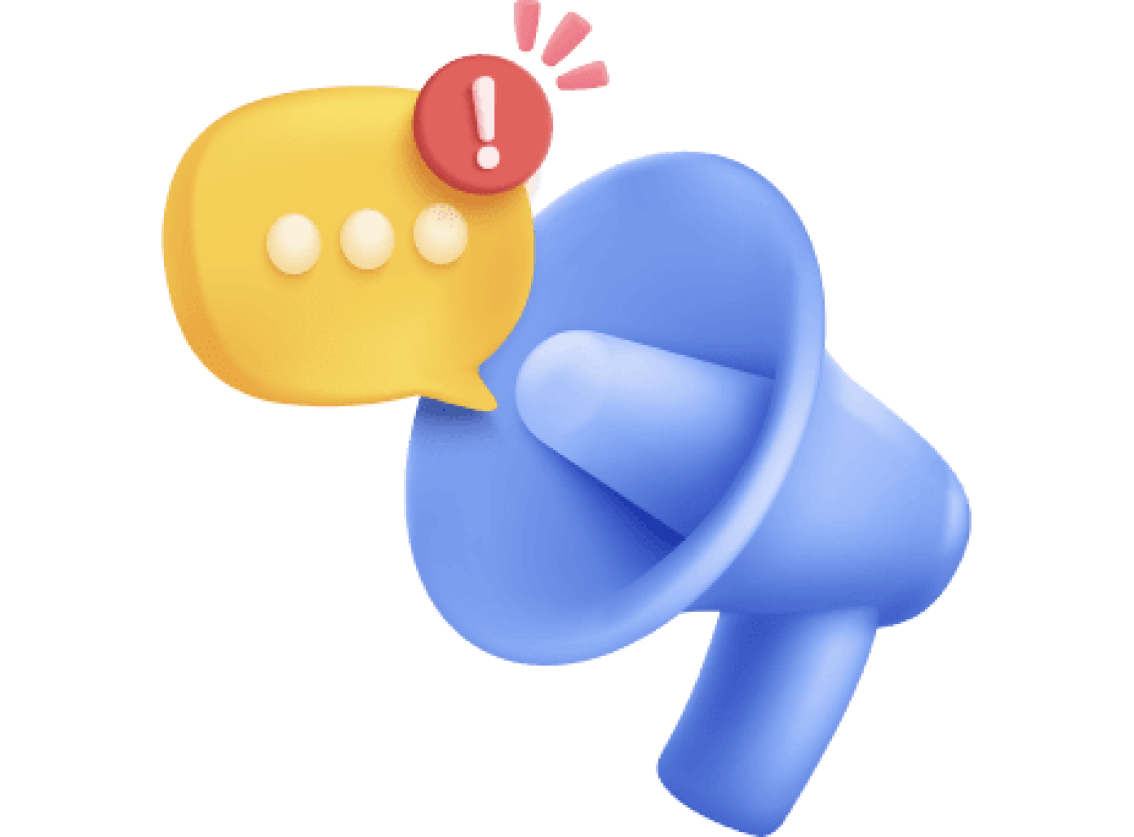