How to Create a Maintenance Schedule
How to Create a Maintenance Schedule
Table of Contents
ToggleHow to Create a Maintenance Schedule
1. Importance of Maintenance Scheduling
A well-planned maintenance schedule is crucial for efficient and reliable operations in the manufacturing industry. By implementing an effective maintenance schedule with MaintWiz CMMS, you can experience the following benefits:
- Minimized downtime: Scheduled maintenance helps prevent unexpected breakdowns and reduces unplanned equipment downtime.
- Optimized resource utilization: Proper scheduling ensures that maintenance tasks are allocated based on priority and available resources, maximizing efficiency.
Improved equipment performance: Regular maintenance enhances equipment reliability, leading to improved overall performance and productivity.
Enhanced safety: Scheduled maintenance includes safety inspections, reducing the risk of accidents and promoting a safe working environment.
Cost savings: By proactively addressing equipment issues through a well-executed maintenance schedule, you can avoid costly emergency repairs and extend the lifespan of your assets.
2. Assessing Equipment Maintenance Needs
Before creating a maintenance schedule, it’s essential to assess the maintenance needs of your equipment. This involves:
- Conducting a thorough equipment inventory: Identify all assets that require maintenance and categorize them based on criticality and priority.
- Identifying critical and non-critical assets: Prioritize maintenance efforts on critical assets that have a significant impact on production and operations.
- Determining maintenance frequency based on asset priority: Assign appropriate maintenance intervals based on the criticality of the equipment and manufacturer recommendations.
3. Types of Maintenance Tasks
A maintenance schedule should encompass various types of maintenance tasks to ensure comprehensive asset management. These include:
- Preventive maintenance tasks: Scheduled inspections, cleaning, lubrication, and other proactive measures to prevent failures and extend equipment life.
- Corrective maintenance tasks: Reactive repairs and fixes carried out in response to identified issues or breakdowns.
- Predictive maintenance tasks: Utilizing data and analytics to anticipate and address potential equipment failures before they occur.
- Event-based maintenance tasks: Specific maintenance actions triggered by events such as equipment reaching a certain usage threshold or a system malfunction.
- Planned vs. unplanned maintenance activities: Balancing scheduled maintenance tasks with unscheduled, emergency repairs to maintain optimal equipment performance.
4. Defining Maintenance Intervals
The frequency at which maintenance tasks are performed plays a vital role in maximizing equipment performance and minimizing disruptions. Maintenance intervals can be determined based on:
- Time-based maintenance intervals: Setting specific time intervals, such as daily, weekly, monthly, or annually, for conducting maintenance tasks.
- Usage-based maintenance intervals: Aligning maintenance schedules with equipment usage metrics, such as operating hours, cycles, or output quantities.
- Condition-based maintenance intervals: Monitoring the condition of equipment through sensors, data analysis, and diagnostics to schedule maintenance based on actual asset health.
- Factors influencing maintenance interval determination: Considerations such as equipment criticality, historical performance data, manufacturer recommendations, and industry best practices.
5. Scheduling Techniques and Tools
When creating a maintenance schedule, it’s essential to utilize effective techniques and tools to streamline the process and optimize resource allocation. Some key considerations include:
- Time-based scheduling: Assigning maintenance tasks based on predefined time intervals, ensuring regular inspections and upkeep.
- Calendar-based scheduling: Syncing maintenance activities with specific dates or events, such as holidays, seasonal changes, or planned shutdowns.
- Event-based scheduling: Triggering maintenance tasks based on events or conditions, such as equipment alerts, sensor readings, or system triggers.
- Hybrid scheduling for optimization: Combining different scheduling approaches to achieve maximum efficiency and resource utilization.
- Resource availability considerations: Taking into account the availability of maintenance teams, spare parts, and equipment access to avoid conflicts or delays.
- Utilizing maintenance management software or CMMS: Leveraging advanced tools like MaintWiz CMMS to automate scheduling, track maintenance activities, and generate reports for analysis and optimization.
6. Creating a Maintenance Schedule Template
To ensure consistency and ease of use, it’s beneficial to create a maintenance schedule template tailored to your organization’s needs. The template should include:
- Designing a structured schedule format: Organize the schedule with clear sections for asset details, task descriptions, frequencies, responsible parties, and any specific instructions.
- Including necessary information: Ensure relevant asset information, such as serial numbers, location, and historical data, is easily accessible in the schedule.
- Using digital tools for easy schedule management and updates: Employing maintenance management software like MaintWiz CMMS allows for efficient creation, editing, and sharing of schedules, ensuring real-time visibility and collaboration.
7. Balancing Preventive and Corrective Maintenance
When establishing a maintenance schedule, it’s crucial to strike a balance between preventive and corrective maintenance strategies. Consider the following:
- Determining the right balance between preventive and corrective maintenance: Assess the cost and impact of breakdowns versus proactive maintenance to find an optimal approach.
- Considering equipment criticality and reliability: Focus preventive maintenance efforts on critical assets or those prone to failures, while corrective maintenance can address less critical equipment.
- Incorporating feedback from maintenance teams and operators: Encourage open communication and input from those directly involved in equipment maintenance to fine-tune the balance and optimize the schedule.
8. Optimizing Maintenance Routes and Work Orders
Efficiently organizing maintenance tasks can greatly enhance productivity and reduce travel time. Consider the following optimization strategies:
- Grouping maintenance tasks by location or equipment proximity: Cluster tasks in a way that minimizes travel time and maximizes efficiency.
- Minimizing travel time and maximizing efficiency: Plan routes and schedules to minimize travel distances and avoid unnecessary backtracking.
- Streamlining work order generation and assignment: Utilize digital tools and CMMS software to automate work order generation, assignment, and tracking, eliminating manual paperwork and reducing administrative overhead.
9. Continuous Schedule Monitoring and Improvement
Creating a maintenance schedule is not a one-time task. It requires regular monitoring and improvement to ensure its effectiveness. Consider the following steps:
- Regularly reviewing and adjusting the maintenance schedule: Continuously assess the schedule’s performance and make necessary adjustments based on feedback, equipment performance data, and changing operational requirements.
- Analyzing maintenance data and performance metrics: Leverage data collected from CMMS software or other maintenance tracking systems to identify trends, detect recurring issues, and optimize maintenance intervals and tasks.
- Incorporating feedback from maintenance teams and operators: Encourage collaboration and gather insights from those directly involved in executing maintenance tasks to identify areas for improvement and enhance overall efficiency.
10. Benefits of a Well-Executed Maintenance Schedule
Implementing and maintaining a well-executed maintenance schedule with MaintWiz CMMS can lead to numerous benefits for your manufacturing operations:
- Improved equipment reliability and uptime: Regular maintenance minimizes unexpected breakdowns, improving equipment reliability and reducing costly production disruptions.
- Enhanced operational efficiency: Optimal scheduling ensures maintenance activities are conducted without interfering with critical production processes, maximizing overall operational efficiency.
- Reduced emergency breakdowns and associated costs: Proactive maintenance helps prevent emergency breakdowns, reducing the need for costly repairs, downtime, and potential safety risks.
- Extended equipment lifespan and reduced capital expenditure: Regular maintenance and timely repairs can extend the life of your assets, reducing the need for premature equipment replacements and associated capital expenditures.
Conclusion
Creating and adhering to a well-planned maintenance schedule is essential for any manufacturing organization aiming to optimize its operations and reduce downtime. By leveraging the benefits of a robust maintenance management system like MaintWiz CMMS, you can streamline scheduling, enhance equipment reliability, and achieve long-term cost savings. Take control of your maintenance processes today!
Key Takeaways:
- A well-planned maintenance schedule minimizes downtime and optimizes resource utilization.
- Assessing equipment maintenance needs helps prioritize tasks based on criticality.
- Types of maintenance tasks include preventive, corrective, predictive, and event-based maintenance.
- Maintenance intervals can be time-based, usage-based, or condition-based.
- Utilize scheduling techniques and tools, including maintenance management software or CMMS.
- Create a structured maintenance schedule template for consistency and easy management.
- Strike a balance between preventive andcorrective maintenance strategies.
- Optimize maintenance routes and work orders to minimize travel time.
- Continuously monitor and improve the maintenance schedule based on data and feedback.
- A well-executed maintenance schedule leads to improved equipment reliability, reduced costs, and enhanced operational efficiency.
Request a one-one demo with our solution engineering team.
Request a one-one demo with our solution engineering team.
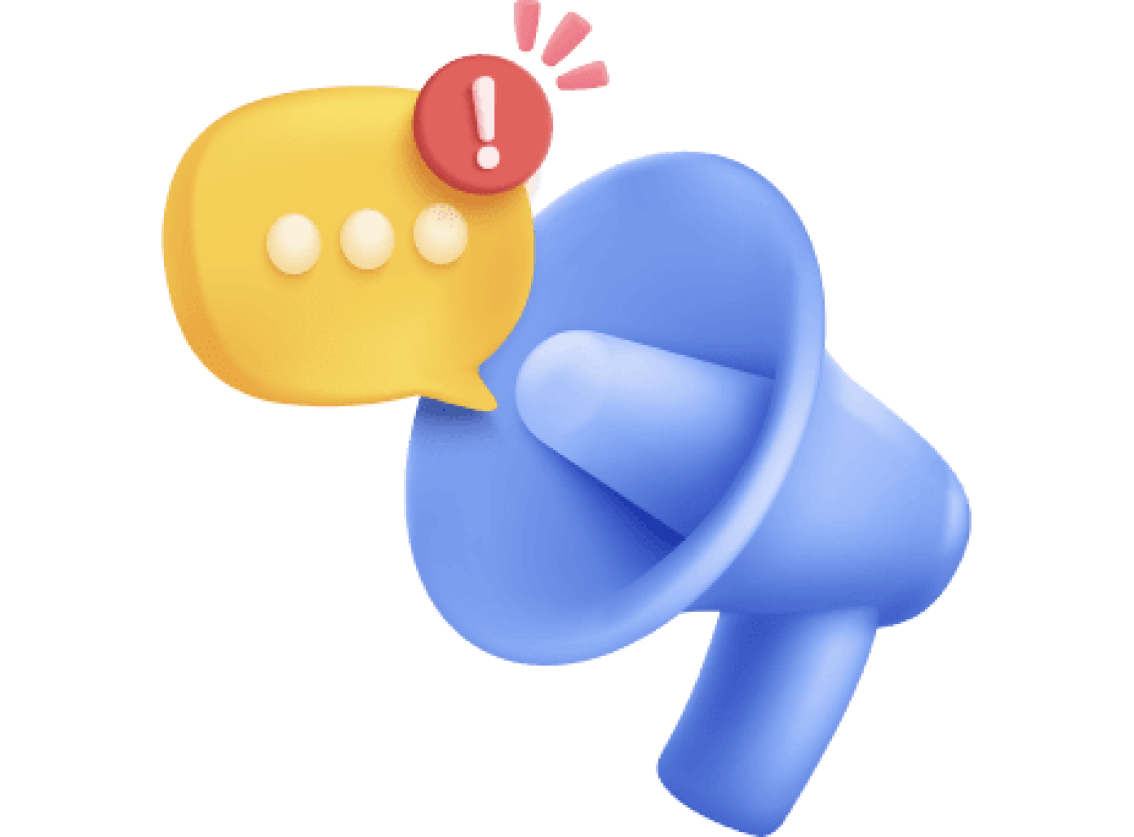