The Importance of Vibration Analysis
The Importance of Vibration Analysis
Table of Contents
ToggleThe Importance of Vibration Analysis
Vibration analysis is a crucial aspect of asset management and plant maintenance. By monitoring and analyzing the vibrations produced by machinery, professionals can gain valuable insights into equipment performance and identify potential faults and malfunctions. This process helps prevent catastrophic failures, improves reliability, reduces unplanned downtime, and enhances overall operational efficiency. In this article, we will explore the key reasons why vibration analysis is vital for organizations and how it can optimize maintenance practices and maximize productivity.
1. Identifies potential faults and malfunctions in machinery
Vibration analysis enables the early detection of faults and malfunctions in machinery. By analyzing vibration patterns, maintenance professionals can identify abnormal vibrations that may indicate underlying issues. This early warning system allows for timely interventions and prevents minor problems from escalating into major failures.
2. Helps prevent catastrophic failures and accidents
By detecting and addressing potential faults in advance, vibration analysis helps prevent catastrophic failures and accidents. Timely maintenance and repairs based on vibration analysis findings reduce the risk of sudden breakdowns and ensure the safety of personnel working with or around the equipment.
3. Improves equipment reliability and lifespan
Vibration analysis plays a significant role in improving equipment reliability and extending its lifespan. By identifying and addressing issues that contribute to equipment degradation, maintenance teams can proactively address these concerns and optimize performance. This proactive approach helps reduce unexpected failures and increases the overall lifespan of the machinery.
4. Reduces unplanned downtime and production losses
Unplanned downtime can significantly impact productivity and result in substantial financial losses for organizations. Vibration analysis allows maintenance professionals to detect potential failures in advance, enabling them to schedule maintenance activities during planned downtime. By addressing issues before they cause a breakdown, organizations can minimize unexpected disruptions and maximize production efficiency.
5. Enhances maintenance planning and scheduling
Vibration analysis provides valuable data that helps optimize maintenance planning and scheduling. By analyzing vibration trends and patterns, maintenance teams can determine the appropriate intervals for inspections, lubrication, and other maintenance activities. This data-driven approach ensures that maintenance efforts are focused on areas that require attention, minimizing unnecessary downtime and optimizing resource allocation.
6. Optimizes maintenance costs and resource allocation
Efficient allocation of maintenance resources is critical for organizations to minimize costs and maximize productivity. Vibration analysis helps optimize maintenance efforts by providing insights into the condition of equipment. By identifying specific areas that require attention, maintenance teams can allocate resources effectively, reducing unnecessary costs and ensuring that resources are utilized where they are most needed.
7. Increases energy efficiency and reduces energy consumption
By detecting and addressing issues that contribute to energy inefficiencies, vibration analysis helps organizations optimize energy consumption. Vibrations in machinery can be a result of misalignment, imbalance, or other factors that negatively impact energy efficiency. Through vibration analysis, these issues can be identified and resolved, leading to reduced energy consumption and cost savings.
8. Improves overall operational efficiency and productivity
By enabling proactive maintenance and reducing unplanned downtime, vibration analysis improves overall operational efficiency and productivity. Well-maintained equipment operates more reliably and consistently, leading to enhanced production efficiency and reduced disruptions. This increased operational efficiency translates into higher productivity levels and improved overall business performance.
9. Enhances product quality and consistency
Vibration analysis helps maintain product quality and consistency by ensuring that the machinery involved in the production process is operating optimally. Vibrations can negatively impact product quality by causing variations or defects. By monitoring vibrations and addressing any issues promptly, organizations can uphold product quality standards and deliver consistent, reliable products to their customers.
10. Minimizes equipment wear and tear
Excessive vibrations can accelerate the wear and tear of machinery components, leading to premature failure. Vibration analysis helps identify the root causes of vibrations and allows maintenance teams to take corrective actions to minimize wear and tear. By addressing these issues promptly, organizations can extend the lifespan of their equipment and reduce the frequency of costly repairs and replacements.
11. Facilitates early detection of bearing and gear defects
Vibration analysis is particularly effective in detecting bearing and gear defects, which are common causes of machinery failures. By monitoring vibrations, professionals can identify specific patterns associated with bearing and gear issues, such as increased levels of vibration or irregularities in frequency spectra. Early detection allows for timely maintenance or replacement, preventing further damage to the equipment and ensuring smooth operations.
12. Assists in identifying imbalance and misalignment issues
Imbalance and misalignment are common problems that can lead to excessive vibrations in machinery. Vibration analysis helps in identifying these issues by analyzing the vibration signatures. By addressing imbalance and misalignment, organizations can minimize vibrations, reduce wear and tear, and optimize equipment performance and longevity.
13. Enables proactive maintenance and condition-based monitoring
Vibration analysis enables organizations to adopt a proactive maintenance approach rather than a reactive one. By continuously monitoring vibrations and analyzing the data, maintenance teams can proactively identify potential issues and address them before they cause major failures or breakdowns. This condition-based monitoring helps organizations optimize maintenance efforts and minimize disruptions to operations.
14. Supports predictive maintenance strategies
Vibration analysis plays a crucial role in predictive maintenance strategies. By monitoring vibrations and analyzing the data trends, organizations can predict the future health of their equipment. This allows for the scheduling of maintenance activities based on the actual condition of the machinery, maximizing uptime and reducing unnecessary maintenance.
15. Reduces the frequency of manual inspections and interventions
Vibration analysis reduces the need for frequent manual inspections and interventions. Instead of relying solely on periodic inspections, organizations can use continuous vibration monitoring to gain real-time insights into the condition of their machinery. This data-driven approach minimizes the need for manual interventions and ensures that maintenance efforts are focused on areas that truly require attention.
16. Provides insights into equipment performance and degradation trends
Through vibration analysis, organizations can gain valuable insights into the performance of their equipment and identify degradation trends over time. By tracking vibration patterns, professionals can understand how equipment performance changes and detect any signs of deterioration. These insights enable organizations to make informed decisions regarding maintenance, repairs, or replacements.
17. Helps optimize lubrication practices and prevent lubrication-related failures
Proper lubrication is essential for the smooth operation of machinery. Vibration analysis helps optimize lubrication practices by providing insights into the effectiveness of lubricants and identifying any lubrication-related issues. By ensuring optimal lubrication, organizations can prevent failures caused by insufficient lubrication or improper lubricant selection.
18. Assists in troubleshooting complex vibration-related problems
Vibration-related problems can sometimes be complex and challenging to troubleshoot. Vibration analysis provides a systematic approach to troubleshooting such issues. By analyzing vibration data and comparing it with established baselines or industry standards, maintenance professionals can narrow down the root causes of the problems. This targeted approach saves time and resources by directing efforts towards specific areas for investigation and resolution.
19. Enables root cause analysis of machinery failures
When machinery failures occur, determining the root cause is crucial to prevent future occurrences. Vibration analysis plays a vital role in root cause analysis by providing valuable data on the vibrations leading up to the failure. By analyzing this data, maintenance teams can identify the underlying issues that contributed to the failure, whether it’s excessive vibrations, misalignment, or other factors. This understanding helps in implementing effective corrective measures to prevent similar failures in the future.
20. Enhances safety by identifying potential hazards
Vibration analysis contributes to maintaining a safe working environment by identifying potential hazards associated with machinery vibrations. Excessive vibrations can lead to structural damage, equipment failure, or even safety risks for personnel. By monitoring vibrations and addressing issues promptly, organizations can minimize the risks and ensure a safer workplace for their employees.
21. Supports compliance with industry regulations and standards
Many industries have specific regulations and standards related to equipment performance and maintenance. Vibration analysis helps organizations comply with these regulations by providing objective data on equipment condition and performance. By incorporating vibration analysis into their maintenance practices, organizations can demonstrate their commitment to safety, reliability, and adherence to industry requirements.
22. Facilitates effective asset management and lifecycle planning
Vibration analysis is a valuable tool for effective asset management and lifecycle planning. By monitoring vibrations and assessing the condition of equipment, organizations can make informed decisions regarding maintenance, repairs, or replacement of assets. This data-driven approach helps optimize asset utilization, minimize downtime, and ensure the availability of reliable equipment throughout its lifecycle.
23. Improves customer satisfaction by ensuring reliable performance
Reliable performance is a key factor in customer satisfaction. Vibration analysis helps organizations ensure the reliable performance of their equipment, minimizing disruptions and delivering consistent results. By proactively addressing potential issues and maintaining optimal operating conditions, organizations can enhance customer satisfaction and build long-term relationships based on trust and reliability.
24. Enhances the accuracy of failure prediction and reliability calculations
Vibration analysis provides valuable data for failure prediction and reliability calculations. By analyzing vibration trends and patterns, organizations can develop models and algorithms to predict the likelihood of failures and estimate equipment reliability. These calculations help organizations optimize maintenance strategies, allocate resources efficiently, and make informed decisions regarding equipment upgrades or replacements.
25. Supports continuous improvement initiatives
Vibration analysis supports continuous improvement initiatives by providing insights into equipment performance and identifying areas for enhancement. By monitoring vibrations and analyzing the data, organizations can identify opportunities for optimization, implement targeted improvements, and enhance the overall efficiency and effectiveness of their maintenance practices.
26. Assists in the optimization of rotating equipment performance
Rotating equipment, such as motors, pumps, and turbines, play a critical role in many industries. Vibration analysis helps optimize the performance of rotating equipment by identifying issues such as misalignment, unbalance, or bearing defects. By addressing these issues, organizations can ensure smooth operation, minimize energy consumption, and maximize the efficiency of their rotating equipment.
27. Provides data for evaluating and validating equipment design
Vibration analysis provides valuable data for evaluating and validating equipment design. By
analyzing vibrations during the design and prototyping stages, organizations can assess the structural integrity and performance of the equipment. This data helps engineers make informed design decisions, identify potential weaknesses or areas for improvement, and ensure that the equipment meets the desired specifications and standards.
28. Enables condition monitoring of critical machinery
For critical machinery that plays a vital role in operations, condition monitoring is essential to ensure continuous and reliable performance. Vibration analysis enables organizations to implement condition monitoring strategies, where vibrations are continuously monitored to detect any deviations from normal operating conditions. This proactive approach allows for timely maintenance interventions and helps prevent unexpected failures that could have severe consequences for operations.
29. Assists in the evaluation and selection of new equipment
When evaluating and selecting new equipment, vibration analysis can provide valuable insights. By analyzing vibration data from different equipment options, organizations can compare their performance, reliability, and potential issues. This analysis helps in making informed decisions about the selection of equipment that aligns with the organization’s requirements and ensures optimal performance and longevity.
30. Enhances the knowledge and expertise of maintenance teams
Vibration analysis enhances the knowledge and expertise of maintenance teams by providing them with valuable data and insights. By understanding the vibration characteristics of different types of machinery and the associated issues, maintenance professionals can develop a deeper understanding of equipment behavior and improve their troubleshooting skills. This knowledge empowers maintenance teams to make informed decisions and perform their tasks more effectively.
Conclusion
In conclusion, vibration analysis is of paramount importance in asset management and plant maintenance. It provides valuable insights into equipment performance, identifies potential faults, and enables proactive maintenance strategies. By implementing vibration analysis practices, organizations can optimize maintenance efforts, reduce downtime, enhance safety, and improve overall operational efficiency. The benefits include improved equipment reliability, extended lifespan, enhanced product quality, and cost savings through optimized resource allocation. For organizations striving for excellence in maintenance practices, vibration analysis is an indispensable tool.
Request a one-one demo with our solution engineering team.
Request a one-one demo with our solution engineering team.
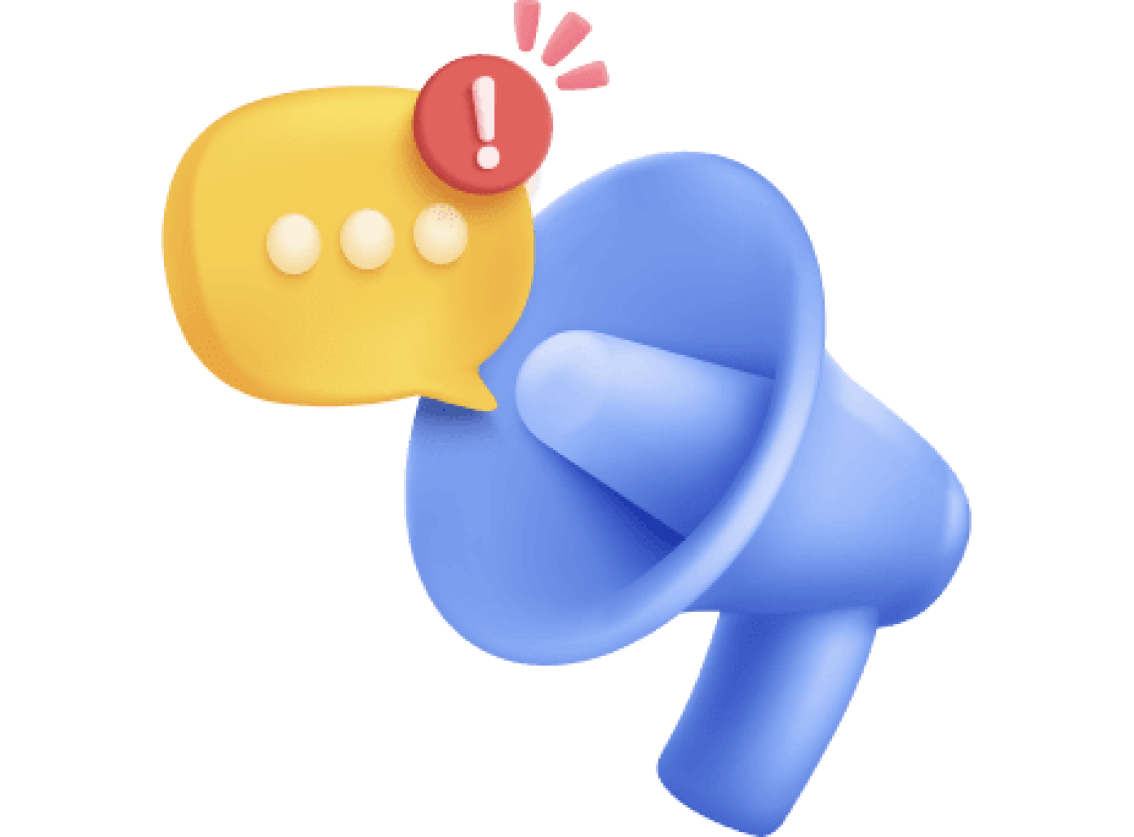