The Importance of Managing Equipment Life Cycle
The Importance of Managing Equipment Life Cycle
Table of Contents
ToggleThe Importance of Managing Equipment Life Cycle
In today’s competitive business landscape, effectively managing the life cycle of equipment is essential for maintaining a competitive edge. From an asset management and plant maintenance perspective, implementing robust strategies to manage equipment throughout its life cycle brings numerous benefits and advantages. By optimizing equipment performance, minimizing downtime, and extending operational lifespan, enterprises can maximize return on investment (ROI), reduce costs, and ensure smooth and efficient operations. Let’s explore why managing equipment life cycle is of paramount importance:
1. Maximizes the return on investment (ROI) for equipment
Managing the equipment life cycle ensures that investments made in acquiring assets yield the highest possible returns. By implementing proactive maintenance strategies, equipment downtime and associated costs can be minimized, leading to increased productivity and revenue generation.
2. Extends the operational lifespan of equipment
Proper maintenance and care throughout the life cycle of equipment significantly contribute to its longevity. Regular inspections, preventive maintenance, and timely repairs help identify and address potential issues before they escalate, thereby extending the operational lifespan of the equipment.
3. Reduces the risk of unexpected breakdowns and costly repairs
Equipment breakdowns can lead to unplanned downtime, disrupt production schedules, and incur significant repair costs. By implementing a comprehensive equipment life cycle management approach, organizations can identify and mitigate potential risks, reducing the likelihood of unexpected breakdowns and minimizing associated expenses.
4. Optimizes equipment performance and efficiency
Effective management of the equipment life cycle involves regular performance assessments and optimization initiatives. By monitoring equipment performance metrics, organizations can identify areas for improvement, implement necessary adjustments, and ensure equipment operates at peak efficiency levels.
5. Minimizes downtime and production disruptions
Equipment failures and unplanned downtime can have severe repercussions on production schedules, customer satisfaction, and overall business operations. By adopting a proactive maintenance approach and implementing equipment life cycle management strategies, organizations can minimize downtime, enhance operational continuity, and meet customer expectations more effectively.
6. Improves safety by ensuring equipment is well-maintained and in good working condition
Proper maintenance and regular inspections as part of equipment life cycle management contribute to a safer working environment. This is why condition monitoring is essential. By ensuring equipment is well-maintained and in good working condition through a robust condition monitoring system, the risk of accidents and injuries can be significantly reduced, promoting a safer workplace for employees.
7. Enhances productivity by minimizing equipment failures and associated downtime
Unplanned equipment failures and downtime can lead to productivity losses and delays in production schedules. By managing the equipment life cycle effectively, organizations can minimize the occurrence of equipment failures, optimize maintenance schedules, and maximize productivity levels, leading to improved operational efficiency.
8. Reduces the need for emergency repairs and their associated costs
Emergency repairs are often more expensive and time-consuming than planned maintenance activities. By implementing a structured equipment life cycle management approach, organizations can reduce the need for emergency repairs, resulting in cost savings and avoiding production disruptions caused by unexpected breakdowns.
9. Enables proactive maintenance planning and scheduling
Managing the equipment life cycle allows organizations to plan and schedule maintenance activities in advance. By proactively identifying maintenance requirements based on equipment performance data and manufacturer recommendations, maintenance tasks can be planned and scheduled to minimize disruptions to operations and optimize resource allocation.
10. Helps identify and address potential reliability issues early on
By closely monitoring equipment performance and analyzing maintenance data, organizations can identify early signs of potential reliability issues. This enables them to take timely corrective actions, such as conducting repairs, replacing faulty components, or adjusting maintenance procedures, before the issues escalate and cause significant operational problems.
11. Facilitates compliance with regulatory and industry standards
Effective management of the equipment life cycle helps organizations meet regulatory requirements and adhere to industry standards. By maintaining equipment in accordance with relevant regulations and standards, businesses can avoid penalties, legal issues, and reputational damage while ensuring the safety and quality of their operations.
12. Supports warranty and service agreement requirements
Many equipment purchases come with warranties and service agreements that require specific maintenance and care. Managing the equipment life cycle ensures compliance with these requirements, protecting the warranty coverage and ensuring access to necessary support and services from equipment manufacturers or service providers.
13. Assists in managing equipment-related risks and liabilities
Equipment failure or malfunction can have various risks and liabilities associated with it. By implementing a comprehensive equipment life cycle management strategy, organizations can assess and manage these risks effectively, including financial, operational, safety, and environmental risks. This proactive approach helps mitigate potential losses and liabilities.
14. Enhances asset value and resale potential
Well-maintained equipment retains its value and has higher resale potential. By managing the equipment life cycle, organizations can ensure that assets are kept in good condition, maximizing their value over time. This becomes especially important when considering equipment upgrades or replacements in the future.
15. Enables accurate budgeting and cost control for equipment maintenance
Effective equipment life cycle management provides organizations with a better understanding of maintenance costs and requirements. By analyzing historical maintenance data and considering factors such as equipment age, usage, and condition, accurate budgeting for maintenance expenses can be achieved, leading to improved cost control and resource allocation.
16. Facilitates effective spare parts and inventory management
Managing the equipment life cycle involves tracking and managing spare parts and inventory effectively. By maintaining accurate records of required spare parts, optimizing inventory levels, and implementing efficient procurement and storage processes, organizations can minimize equipment downtime and ensure timely availability of necessary components.
17. Supports effective decision-making regarding equipment repairs, replacements, and upgrades
By analyzing equipment performance data and considering factors such as maintenance costs, reliability, and technological advancements, organizations can make informed decisions regarding equipment repairs, replacements, and upgrades. This helps optimize equipment utilization, minimize operational risks,
and ensure that investments in equipment align with the overall business strategy and objectives.
18. Enables data-driven insights into equipment performance and maintenance trends
Managing the equipment life cycle involves collecting and analyzing data related to equipment performance, maintenance activities, and downtime. By leveraging this data, organizations can gain valuable insights into equipment performance trends, identify patterns of failure, and make data-driven decisions to improve maintenance practices and optimize equipment reliability.
19. Enhances asset tracking and inventory management
Effective equipment life cycle management includes robust asset tracking systems that provide real-time visibility into the location, condition, and usage of equipment. This enables organizations to optimize asset utilization, prevent loss or theft, and streamline inventory management processes for better operational efficiency.
20. Provides documentation and historical records for equipment maintenance and repairs
Maintaining detailed documentation and historical records of equipment maintenance and repairs is essential for tracking equipment performance, compliance, and warranty claims. Proper documentation ensures transparency, facilitates audits, and supports troubleshooting and decision-making processes related to equipment maintenance.
21. Facilitates effective vendor and supplier management
Managing the equipment life cycle involves establishing and maintaining relationships with vendors and suppliers. By effectively managing these relationships, organizations can ensure timely delivery of spare parts, access to technical expertise, and favorable pricing terms, thereby minimizing disruptions and optimizing equipment maintenance processes.
22. Supports equipment lifecycle planning and replacement strategies
Effective equipment life cycle management includes developing long-term strategies for equipment lifecycle planning and replacements. By considering factors such as technological advancements, asset depreciation, and changing business needs, organizations can strategically plan equipment upgrades, replacements, or retirements to ensure the continuous availability of reliable and efficient equipment.
23. Assists in evaluating equipment reliability and performance metrics
Managing the equipment life cycle involves monitoring and evaluating equipment reliability and performance metrics. By tracking key performance indicators (KPIs), organizations can assess equipment health, identify areas for improvement, and implement targeted measures to enhance reliability, reduce failures, and optimize equipment performance.
24. Improves the overall operational reliability and availability of equipment
Effective equipment life cycle management aims to maximize operational reliability and availability. By implementing preventive maintenance strategies, conducting regular inspections, and addressing maintenance needs promptly, organizations can minimize equipment downtime, improve operational continuity, and ensure that equipment is available when needed.
25. Enables efficient utilization of equipment resources
Managing the equipment life cycle ensures that equipment resources are utilized efficiently. By optimizing maintenance schedules, streamlining processes, and minimizing unplanned downtime, organizations can maximize the utilization of their equipment, reducing idle time and improving overall operational efficiency.
26. Supports continuous improvement initiatives for equipment maintenance processes
Effective equipment life cycle management involves a commitment to continuous improvement. By analyzing maintenance data, seeking feedback from maintenance teams, and implementing process enhancements, organizations can continuously refine their equipment maintenance processes, identify opportunities for optimization, and drive ongoing improvements in efficiency and effectiveness.
27. Enhances communication and collaboration among equipment stakeholders
Managing the equipment life cycle requires collaboration and communication among various stakeholders, including maintenance teams, operations personnel, and management. By promoting effective communication channels and fostering collaboration, organizations can align goals, share insights, and ensure that equipment maintenance efforts are coordinated, resulting in improved outcomes.
28. Helps in achieving and maintaining high-quality product standards
Effective equipment life cycle management plays a crucial role in achieving and maintaining high-quality product standards. Well-maintained equipment contributes to consistent product quality, reduces the risk of defects or malfunctions, and ensures that products meet customer expectations and regulatory requirements. By prioritizing equipment maintenance, organizations can uphold their reputation for delivering high-quality products.
29. Assists in meeting customer expectations and delivery deadlines
Timely and reliable equipment is essential for meeting customer expectations and delivery deadlines. By managing the equipment life cycle effectively, organizations can minimize equipment failures, maintain consistent production schedules, and fulfill customer orders on time. This enhances customer satisfaction, strengthens relationships, and improves overall business performance.
30. Promotes a culture of proactive equipment management and preventive maintenance
Managing the equipment life cycle fosters a culture of proactive equipment management and preventive maintenance within an organization. By emphasizing the importance of regular inspections, maintenance planning, and proactive measures, employees become more aware of the critical role they play in equipment reliability and performance. This culture shift leads to increased accountability, better maintenance practices, and improved overall operational efficiency.
Conclusion
Effective management of the equipment life cycle is vital for organizations to maximize ROI, optimize equipment performance, minimize downtime, and reduce risks. By implementing comprehensive asset management and plant maintenance strategies, businesses can extend the operational lifespan of equipment, enhance safety, and improve productivity. Additionally, proper equipment maintenance enables accurate budgeting, supports decision-making, and provides valuable data-driven insights. To ensure your organization benefits from these advantages, reach out to MaintWiz and unlock the full potential of managing your equipment life cycle.
Request a one-one demo with our solution engineering team.
Request a one-one demo with our solution engineering team.
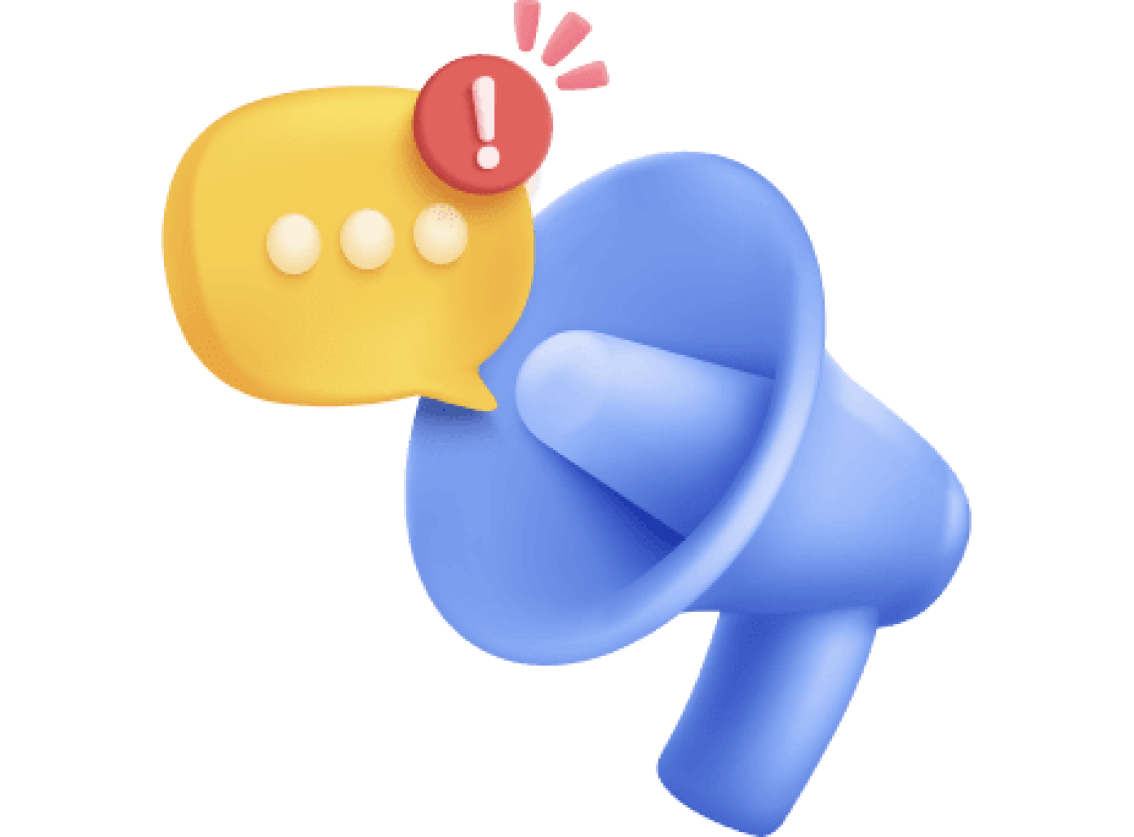