The Importance of Maintenance Planning
The Importance of Maintenance Planning
Table of Contents
ToggleThe Importance of Maintenance Planning
A well-executed maintenance planning process is crucial for organizations to ensure the smooth operation of their assets and facilities. By effectively scheduling maintenance activities and allocating resources, maintenance planning maximizes equipment uptime, reduces costs, and enhances overall operational efficiency. In this article, we will explore the key reasons why maintenance planning is important in the context of asset management and plant maintenance.
1. Maximizes equipment uptime and availability
Maintenance planning minimizes unplanned downtime by scheduling regular preventive maintenance activities. By adhering to a structured maintenance plan, organizations can proactively address potential issues before they lead to equipment failures or breakdowns. This ensures that critical assets are available and operational when needed, maximizing overall equipment uptime and availability.
2. Reduces unplanned downtime and costly breakdowns
Unplanned downtime can result in significant production losses and costly repairs. By implementing a comprehensive maintenance planning process, organizations can minimize the occurrence of unexpected equipment failures and breakdowns. Regular inspections, preventive maintenance, and timely repairs help reduce the risk of unplanned downtime, leading to improved operational continuity and cost savings.
3. Optimizes resource allocation and utilization
Maintenance planning allows organizations to allocate their resources effectively. By having a clear understanding of the maintenance requirements and schedules, maintenance teams can plan their activities accordingly, ensuring the availability of skilled personnel, tools, and materials. This optimized resource allocation enhances productivity and reduces wastage, leading to cost-effective maintenance operations.
4. Enhances equipment reliability and longevity
Regular maintenance activities prescribed in the maintenance plan help identify and address equipment issues early on. By performing preventive maintenance, organizations can identify and replace worn-out components, lubricate moving parts, and address potential sources of equipment failure. This proactive approach improves equipment reliability and longevity, reducing the frequency of breakdowns and extending the lifespan of assets.
5. Improves safety for personnel and equipment
Maintenance planning plays a crucial role in ensuring a safe working environment for personnel and equipment. By adhering to safety standards and regulations during maintenance activities, organizations can minimize the risk of accidents and injuries. Regular inspections and maintenance also help identify potential safety hazards and address them promptly, creating a safer workplace for employees and protecting valuable assets.
6. Minimizes maintenance costs and expenses
Effective maintenance planning allows organizations to minimize maintenance costs and expenses. By identifying and addressing equipment issues early on, organizations can avoid costly emergency repairs and component replacements. Additionally, preventive maintenance helps maintain equipment efficiency and prevents costly performance deterioration, resulting in reduced maintenance costs over time.
7. Increases productivity and operational efficiency
Through proper maintenance planning, organizations can streamline maintenance activities and minimize disruptions to operations. By scheduling maintenance tasks during planned downtime or non-peak periods, organizations can ensure that maintenance activities do not interfere with regular production schedules. This enhances overall productivity and operational efficiency, as maintenance activities are strategically integrated into the operational workflow.
8. Ensures compliance with regulatory requirements
Maintenance planning is essential for ensuring compliance with regulatory requirements. Industries such as manufacturing, healthcare, and transportation have specific regulations and standards that govern maintenance practices. By incorporating these requirements into the maintenance planning process, organizations can demonstrate compliance during audits and inspections, avoiding penalties and legal consequences. Maintenance planning helps establish a systematic approach to meet regulatory obligations, ensuring that maintenance activities align with industry standards and best practices.
9. Facilitates effective budgeting and cost control
Maintenance planning provides a framework for effective budgeting and cost control. By forecasting maintenance needs, organizations can allocate resources and funds accordingly. This allows for better financial planning and ensures that maintenance activities are adequately funded. With a well-planned maintenance budget, organizations can optimize costs, prioritize maintenance tasks, and make informed decisions regarding equipment repairs, replacements, and upgrades.
10. Enables proactive maintenance rather than reactive repairs
Reactive repairs are often costlier and more time-consuming compared to proactive maintenance. Maintenance planning enables organizations to shift from a reactive approach to a proactive one. By scheduling preventive maintenance tasks and inspections, organizations can identify and address potential issues before they escalate into major problems. Proactive maintenance minimizes the need for emergency repairs, reduces downtime, and improves overall equipment reliability.
11. Supports effective inventory management and spare parts control
Efficient inventory management is critical for maintaining optimal maintenance operations. By incorporating inventory management into the maintenance planning process, organizations can ensure the availability of necessary spare parts and materials. This reduces delays in equipment repairs and minimizes downtime. Maintenance planning enables better control over inventory levels, reorder points, and supplier relationships, streamlining the procurement process and minimizing inventory holding costs.
12. Enhances asset performance and Overall Equipment Effectiveness (OEE)
Maintenance planning directly impacts asset performance and Overall Equipment Effectiveness (OEE). By implementing preventive maintenance activities and optimizing maintenance schedules, organizations can improve asset performance metrics such as availability, reliability, and quality. Increased OEE leads to higher production output, improved product quality, and enhanced customer satisfaction.
13. Enables accurate and timely maintenance scheduling
Maintenance planning provides a structured approach to scheduling maintenance activities. By defining maintenance intervals, organizations can ensure that inspections, lubrications, and other preventive maintenance tasks are performed at the appropriate times. Accurate and timely maintenance scheduling minimizes the risk of missed maintenance activities and ensures that equipment remains in optimal condition, reducing the likelihood of failures or breakdowns.
14. Reduces the risk of critical equipment failure
Critical equipment failures can have severe consequences, including production losses, safety hazards, and costly repairs. Maintenance planning focuses on mitigating the risk of critical equipment failure through preventive maintenance strategies. Regular inspections, condition monitoring, and equipment health assessments help identify early warning signs of potential failures. By addressing these issues promptly, organizations can significantly reduce the risk of catastrophic equipment failures and their associated costs.
15. Enhances customer satisfaction by minimizing service disruptions
Maintenance planning plays a crucial role in delivering uninterrupted service to customers. By minimizing equipment breakdowns and unplanned downtime, organizations can provide reliable and consistent service to their customers. This enhances customer satisfaction and loyalty, as they can rely on the organization’s ability to meet their needs consistently and without unexpected disruptions.
16. Enables predictive and condition-based maintenance strategies
Maintenance planning lays the foundation for implementing advanced maintenance strategies such as
predictive and condition-based maintenance. These strategies rely on data-driven insights to identify maintenance needs based on equipment condition and performance indicators. By incorporating predictive maintenance techniques into the maintenance plan, organizations can leverage technologies like sensors, data analytics, and machine learning to detect early signs of equipment deterioration or failure. This enables proactive maintenance interventions, optimizing maintenance resources and minimizing downtime.
17. Improves data collection and analysis for informed decision-making
Maintenance planning promotes systematic data collection and analysis, providing organizations with valuable insights for informed decision-making. By documenting maintenance activities, equipment performance, and failure data, organizations can identify patterns, trends, and areas for improvement. This data-driven approach enables evidence-based decision-making regarding maintenance strategies, resource allocation, and equipment replacement or upgrades, leading to more efficient and effective maintenance operations.
18. Minimizes the impact of maintenance activities on production schedules
Unplanned maintenance activities can disrupt production schedules and cause delays. By incorporating maintenance planning, organizations can minimize the impact of maintenance on production operations. By scheduling maintenance tasks during planned downtime or low-demand periods, organizations can ensure that maintenance activities have minimal interference with production schedules. This reduces the risk of production disruptions, optimizes production throughput, and maintains customer delivery commitments.
19. Supports continuous improvement initiatives
Maintenance planning provides a framework for continuous improvement in maintenance operations. By analyzing maintenance data, organizations can identify opportunities for process optimization, equipment performance enhancement, and cost reduction. Maintenance planning facilitates the implementation of improvement initiatives such as reliability-centered maintenance (RCM), total productive maintenance (TPM), and lean maintenance, driving efficiency and effectiveness in maintenance activities.
20. Facilitates compliance with industry standards and best practices
Maintenance planning ensures that organizations adhere to industry standards and best practices. By incorporating these guidelines into the maintenance plan, organizations can demonstrate their commitment to quality, safety, and compliance. This not only helps maintain regulatory compliance but also enhances the organization’s reputation within the industry. Compliance with industry standards and best practices reflects a commitment to excellence and positions the organization as a leader in its field.
21. Reduces environmental impact through efficient maintenance practices
Efficient maintenance planning contributes to reducing the environmental impact of operations. By optimizing maintenance activities, organizations can minimize energy consumption, waste generation, and the use of hazardous materials. Regular maintenance activities, such as equipment calibration and optimization, contribute to energy efficiency and sustainable operations. By reducing the environmental footprint, organizations demonstrate their commitment to corporate social responsibility and environmental stewardship.
22. Enhances the overall reliability and availability of systems and processes
Maintenance planning improves the overall reliability and availability of systems and processes within an organization. By implementing preventive maintenance practices, organizations can identify and resolve potential issues before they impact operations. This ensures that systems and processes remain reliable and available, supporting uninterrupted production and service delivery. Enhanced reliability and availability contribute to increased customer satisfaction, operational efficiency, and competitiveness.
23. Enables effective implementation of maintenance strategies and tactics
Maintenance planning provides a roadmap for the effective implementation of maintenance strategies and tactics. Whether it’s preventive maintenance, corrective maintenance, or condition-based maintenance, a well-defined plan ensures that the right activities are executed at the right time. This alignment of strategies and tactics optimizes maintenance outcomes, reduces risks, and maximizes the value derived from maintenance activities.
24. Provides a framework for tracking and measuring maintenance performance
Maintenance planning establishes a framework for tracking and measuring maintenance performance. By setting key performance indicators (KPIs) and metrics, organizations can monitor the effectiveness and efficiency of their maintenance activities. This allows for continuous evaluation and improvement of maintenance processes. Tracking performance indicators such as mean time between failures (MTBF), mean time to repair (MTTR), and Overall Equipment Effectiveness (OEE) provides insights into maintenance efficiency, identifies areas for improvement, and supports data-driven decision-making.
25. Enhances communication and coordination among maintenance teams and other departments
Maintenance planning fosters effective communication and coordination among maintenance teams and other departments within the organization. By establishing clear maintenance schedules, sharing information on maintenance activities, and collaborating on maintenance plans, teams can work together seamlessly. This promotes cross-functional collaboration, reduces conflicts, and ensures that everyone is aligned with the maintenance objectives. Effective communication and coordination result in smoother operations, faster issue resolution, and improved overall productivity.
26. Enables effective planning for equipment upgrades and replacements
Maintenance planning allows organizations to anticipate equipment upgrades and replacements in a timely manner. By monitoring equipment performance, maintenance history, and technological advancements, organizations can plan for equipment upgrades or replacements before they become a liability. This proactive approach ensures that equipment is modern, efficient, and aligned with evolving business needs. It also avoids sudden disruptions and costs associated with equipment failures or obsolescence.
27. Minimizes equipment-related risks and potential hazards
Equipment failures and malfunctions can pose significant risks and hazards to personnel and operations. Maintenance planning helps identify and address potential risks associated with equipment. By conducting risk assessments, implementing preventive maintenance measures, and adhering to safety protocols, organizations can mitigate equipment-related risks. This contributes to a safer work environment, reduces the likelihood of accidents, and protects the well-being of employees.
28. Improves overall plant and facility maintenance management
Maintenance planning plays a critical role in overall plant and facility maintenance management. By adopting a systematic and proactive approach, organizations can effectively manage maintenance activities, optimize resource utilization, and minimize disruptions. Maintenance planning ensures that maintenance tasks are prioritized, scheduled, and executed efficiently. This leads to streamlined maintenance processes, improved asset performance, and better utilization of maintenance resources.
29. Supports effective documentation and record-keeping
Accurate documentation and record-keeping are essential for maintenance activities. Maintenance planning provides a structured framework for documenting maintenance schedules, procedures, checklists, and reports. This ensures that crucial information is recorded and easily accessible. Effective documentation facilitates knowledge sharing, aids in regulatory compliance, supports historical analysis, and enables future maintenance planning and decision-making.
30. Enhances the organization’s reputation for operational excellence
By implementing robust maintenance planning processes, organizations establish a reputation for operational excellence. A well-maintained facility, reliable equipment, and minimized downtime create a positive image of the organization. This reputation for operational excellence attracts customers, instills confidence in stakeholders, and positions the organization as a reliable and trusted partner. A strong reputation contributes to business growth, competitive advantage, and long-term sustainability.
Conclusion
Maintenance planning is a vital component of asset management and plant maintenance. It maximizes equipment uptime, reduces costs, enhances safety, and improves overall operational efficiency. By implementing a structured and proactive maintenance planning process, organizations can optimize resource allocation, minimize downtime, extend equipment life, and ensure compliance with regulatory requirements. The benefits of maintenance planning extend beyond cost savings, positively impacting productivity,
customer satisfaction, and the overall reputation of the organization. By incorporating maintenance planning into the strategic framework of the organization, businesses can achieve operational excellence and position themselves as leaders in their industry.
To maximize the benefits of maintenance planning, organizations should embrace technology and data-driven approaches. Leveraging advanced maintenance management systems, predictive analytics, and condition monitoring technologies can further enhance the effectiveness of maintenance planning. These tools enable organizations to gather real-time data, monitor equipment health, and make informed decisions based on accurate insights.
Maintenance planning is an indispensable aspect of asset management and plant maintenance. It ensures equipment reliability, minimizes downtime, optimizes resource utilization, and drives operational efficiency. By implementing a comprehensive maintenance planning process, organizations can reap numerous benefits such as improved safety, reduced costs, enhanced customer satisfaction, and a competitive edge in the market. Embracing maintenance planning as a strategic priority sets the stage for long-term success, operational excellence, and sustainable growth.
Request a one-one demo with our solution engineering team.
Request a one-one demo with our solution engineering team.
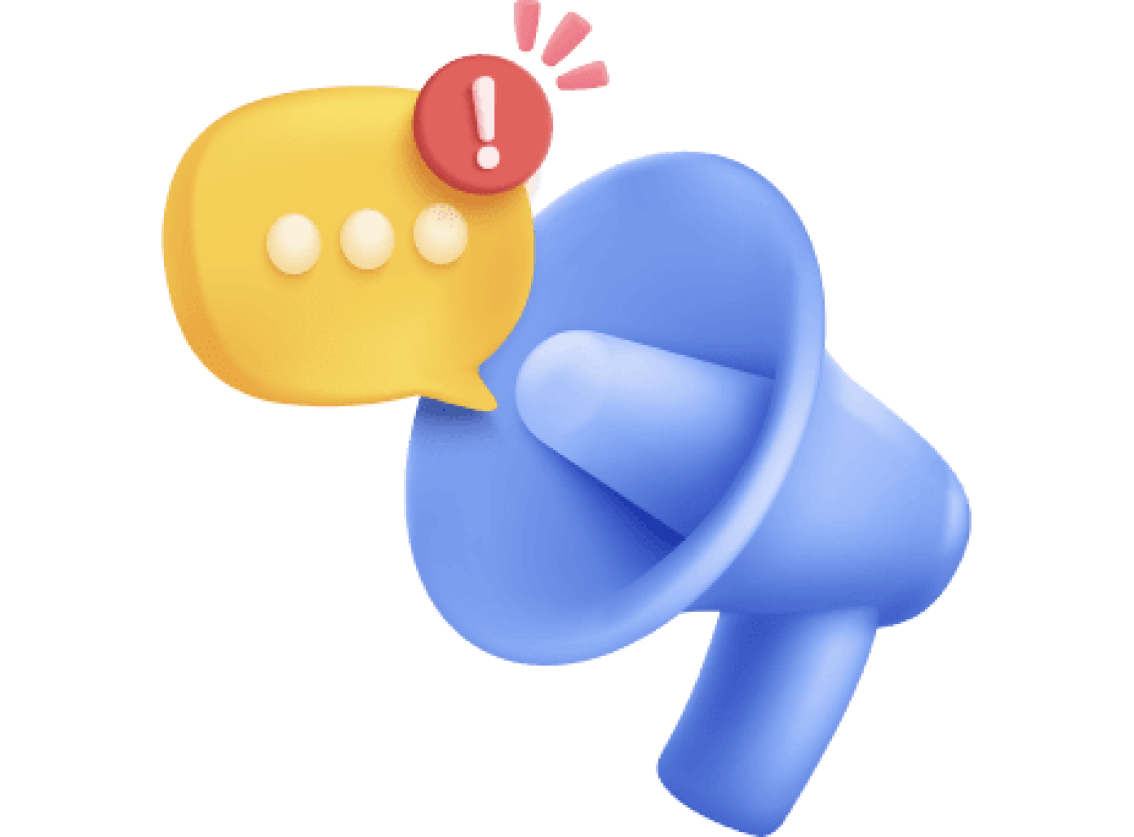