How to Prevent Equipment Failures with Preventive Maintenance
Prevent Equipment failures With preventive Maintenance
Table of Contents
ToggleHow to Prevent Equipment Failures with Preventive Maintenance
Effective preventive maintenance is crucial for ensuring the reliability and longevity of equipment in any organization. By proactively addressing potential issues before they escalate into failures, companies can minimize unplanned downtime, reduce costly repairs, and maximize operational efficiency and productivity. This comprehensive guide explores the key strategies and practices for implementing a successful preventive maintenance program and highlights how MaintWiz CMMS can assist in streamlining maintenance processes.
1. The Importance of Preventive Maintenance to Prevent Failures
Proactively maintaining equipment is essential for enhancing its overall performance and extending its lifespan. Preventive maintenance allows organizations to identify and address potential issues before they escalate into failures, ensuring the continuous operation of critical assets. By minimizing unplanned downtime and reducing the need for reactive repairs, companies can improve operational efficiency, increase productivity, and ultimately save costs. MaintWiz CMMS provides the necessary tools and features to effectively plan, execute, and track preventive maintenance tasks, helping organizations prevent equipment failures and achieve maintenance excellence.
2. Understanding Equipment Failure Modes
Equipment failures can occur due to various reasons, including wear and tear, poor maintenance practices, environmental factors, and component malfunctions. By understanding the common failure modes specific to their assets, organizations can develop targeted preventive maintenance strategies. Analyzing failure patterns and trends, as well as utilizing failure data, enables companies to identify the root causes of failures and take proactive measures to prevent their recurrence. MaintWiz CMMS offers robust reporting and analytics capabilities, empowering organizations to gain insights into failure data and make informed decisions to prevent equipment failures.
3. Developing a Preventive Maintenance Plan
A well-structured preventive maintenance plan is the foundation for an effective maintenance program. Conducting equipment risk assessments helps prioritize maintenance efforts based on criticality and potential consequences. Establishing preventive maintenance tasks and intervals ensures that inspections, lubrication, calibration, and other maintenance activities are performed at the right time. Creating a comprehensive maintenance schedule helps organizations stay on top of preventive maintenance tasks and avoid missed or delayed activities. MaintWiz CMMS simplifies the process of developing and managing preventive maintenance plans, enabling organizations to optimize their maintenance schedules and ensure equipment reliability.
4. Implementing Condition Monitoring Techniques
Condition monitoring involves the use of various techniques to assess the health and performance of equipment in real-time. Vibration analysis and monitoring help detect early signs of wear, misalignment, or unbalance in rotating machinery. Thermography inspections identify potential issues through the measurement of temperature variations. Oil analysis provides insights into the condition of lubrication systems and identifies potential contaminants or degradation. Non-destructive testing methods, such as ultrasonic testing and magnetic particle inspection, help detect hidden defects in critical components. MaintWiz CMMS facilitates the integration of condition monitoring data, allowing organizations to proactively address equipment issues and prevent failures.
5. Lubrication and Inspection Practices for Equipment Maintenance
Proper lubrication and regular inspections are vital for maintaining equipment reliability. Adequate lubrication ensures that moving parts operate smoothly, reduces friction and wear, and prevents premature failure. Organizations must follow recommended lubrication techniques, such as using the right lubricants, applying them in the correct quantity, and adhering to the specified lubrication schedules. Regular inspections help identify signs of wear, damage, or degradation, allowing for timely repairs or component replacements. MaintWiz CMMS simplifies lubrication management and inspection scheduling, ensuring that equipment receives the necessary attention to prevent failures.
6. Proactive Parts Replacement and Component Upgrades
Identifying critical components that are prone to failure and proactively replacing them can significantly reduce the risk of equipment breakdowns. Upgrading to more reliable parts and materials enhances equipment performance and extends its lifespan. Furthermore, organizations can leverage advancements in technology to improve the reliability and efficiency of their assets. MaintWiz CMMS facilitates spare parts management and provides alerts and notifications for proactive component replacements. With the ability to track and manage parts inventory, organizations can ensure they have the right components available when needed, reducing equipment downtime.
7. Utilizing Computerized Maintenance Management Systems (CMMS)
Implementing a robust CMMS like MaintWiz streamlines maintenance operations and ensures the effective management of preventive maintenance tasks. CMMS enables organizations to track maintenance activities and schedules, store and access equipment records and history, generate work orders and task assignments, and streamline communication among maintenance teams. MaintWiz CMMS provides a user-friendly interface, powerful reporting capabilities, and mobile access, empowering organizations to centralize their maintenance processes, improve efficiency, and reduce administrative overhead. By leveraging MaintWiz CMMS, companies can enhance their preventive maintenance practices and prevent equipment failures.
8. Training and Empowering Maintenance Teams
Investing in comprehensive training programs for maintenance personnel is crucial for building a skilled and proactive workforce. Providing training on equipment maintenance practices, safety protocols, and the effective use of CMMS equips employees with the necessary knowledge and skills to perform their maintenance tasks effectively. Encouraging proactive reporting of potential issues by maintenance teams ensures that early signs of equipment problems are captured and addressed promptly. Empowering employees to take ownership of equipment care fosters a culture of accountability and drives preventive maintenance success. MaintWiz CMMS offers training and resource management features, allowing organizations to efficiently train and empower their maintenance teams.
9. Monitoring Key Performance Indicators (KPIs) for Equipment Health
Tracking key performance indicators (KPIs) provides valuable insights into the health and performance of equipment. By monitoring equipment uptime and availability, organizations can identify areas of improvement and take proactive measures to minimize downtime. Analyzing mean time between failures (MTBF) and mean time to repair (MTTR) metrics helps assess the efficiency of maintenance processes and identify opportunities for optimization. Measuring Overall Equipment Effectiveness (OEE) enables organizations to evaluate the productivity and utilization of assets. MaintWiz CMMS offers comprehensive reporting and analytics capabilities, allowing organizations to monitor KPIs, identify trends, and make data-driven decisions for equipment health and maintenance improvement.
10. Continuous Improvement and Adaptation
Maintenance practices and equipment technologies continuously evolve, requiring organizations to adapt and improve their preventive maintenance strategies. Regular evaluation and optimization of preventive maintenance programs help identify areas for improvement and refine maintenance processes. Incorporating feedback and lessons learned from maintenance activities enables organizations to continuously enhance their maintenance practices. Staying updated on industry best practices and technological advancements ensures that organizations leverage the latest tools and techniques to prevent equipment failures effectively. MaintWiz CMMS provides a flexible and scalable platform that adapts to evolving maintenance needs and empowers organizations to drive continuous improvement in their maintenance practices.
Conclusion
Preventing equipment failures through effective preventive maintenance is vital for organizations aiming to enhance equipment performance, minimize downtime, and maximize operational efficiency. By following the strategies and practices outlined in this guide, organizations can establish a robust preventive maintenance program. Moreover, by leveraging the features and capabilities of MaintWiz CMMS, organizations can streamline their maintenance processes, improve efficiency, and prevent equipment failures. Take the first step towards maintenance excellence and equip your organization with MaintWiz CMMS today.
Key Takeaways:
- Implementing preventive maintenance enhances equipment performance and minimizes unplanned downtime.
- Understanding equipment failure modes helps develop targeted preventive maintenance strategies.
- A well-structured preventive maintenance plan is crucial for effective maintenance management.
- Utilizing condition monitoring techniques enables proactive equipment maintenance.
- Proper lubrication and regular inspections contribute to equipment reliability.
- Proactive parts replacement and component upgrades reduce the risk of failures.
- CMMS facilitates streamlined maintenance operations and enhances preventive maintenance.
- Training and empowering maintenance teams fosters a culture of accountability and success.
- Monitoring key performance indicators (KPIs) provides insights into equipment health.
- Continuous improvement and adaptation are necessary for maintenance success.
Request a one-one demo with our solution engineering team.
Request a one-one demo with our solution engineering team.
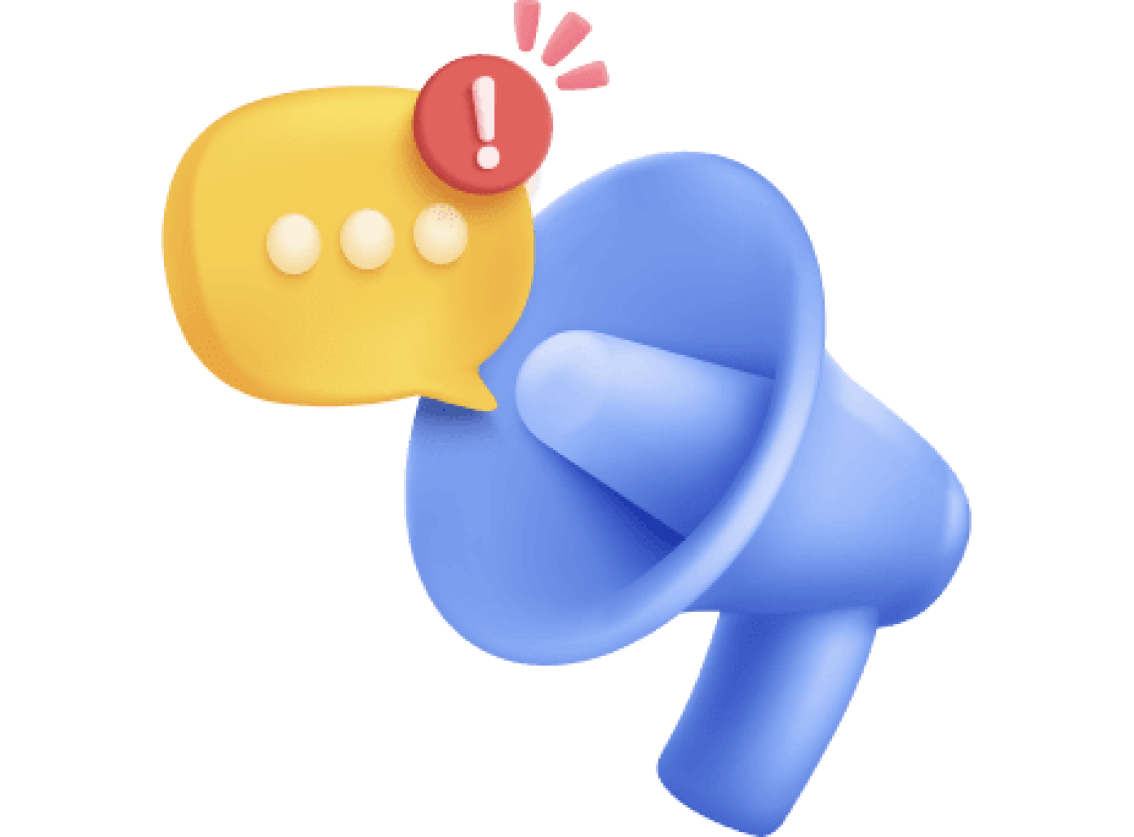