TPM Fundamentals
TPM Fundamentals
Table of Contents
ToggleTPM Fundamentals
- Total Productive Maintenance (TPM): A proactive approach to maintenance involving all employees in maintaining and improving equipment effectiveness. It aims to maximize equipment efficiency and minimize downtime through preventive maintenance, continuous improvement, and employee empowerment.
- Overall Equipment Effectiveness (OEE): A key performance indicator measuring equipment effectiveness based on availability, performance, and quality. It helps organizations identify areas for improvement and track progress towards TPM goals.
- Six Big Losses: The six major categories of losses that reduce OEE: breakdowns, setup and adjustment, small stops, reduced speed, defects, and idle time. By addressing these losses, organizations can significantly improve equipment performance and overall productivity.
TPM Pillars
- Autonomous Maintenance: Empowering operators to perform daily maintenance tasks like cleaning, lubrication, and inspections. This pillar promotes ownership and responsibility among operators, leading to improved equipment reliability and reduced downtime.
- Planned Maintenance: Implementing a systematic schedule for preventive maintenance activities to prevent breakdowns. By proactively addressing potential issues, organizations can avoid costly unplanned downtime and extend equipment life.
- Focused Improvement: A continuous improvement process targeting specific equipment or processes to eliminate losses. By focusing on specific areas, organizations can achieve significant improvements in a targeted manner.
- Quality Maintenance: Integrating quality control into maintenance activities to prevent defects and improve product quality. By ensuring that maintenance activities are performed correctly and that equipment is maintained to high standards, organizations can improve product quality and reduce rework.
- Early Equipment Management: Involving maintenance teams in the design and procurement of new equipment to ensure maintainability. By considering maintenance requirements from the outset, organizations can select equipment that is easier to maintain and less prone to breakdowns.
- Education and Training: Providing training to all employees on TPM principles, techniques, and skills. By investing in employee training, organizations can build a skilled workforce capable of implementing and sustaining TPM.
- Safety, Health, and Environment: Prioritizing safety, health, and environmental considerations in all TPM activities. By creating a safe and healthy work environment, organizations can reduce accidents and injuries, improve employee morale, and comply with environmental regulations.
- TPM in Administration: Applying TPM principles to administrative and support functions to improve efficiency and effectiveness. By extending TPM to administrative functions, organizations can improve overall organizational performance and reduce costs.
TPM Tools and Techniques
- 5S: A methodology for workplace organization and cleanliness: Sort, Set in Order, Shine, Standardize, Sustain. 5S creates a visually appealing, efficient, and safe work environment, leading to improved productivity and quality.
- TPM Pillar Teams: Cross-functional teams responsible for implementing and sustaining TPM activities within each pillar. These teams bring together diverse perspectives and expertise to drive TPM initiatives.
- TPM Loss Tree: A visual tool to identify and analyze the root causes of losses. By understanding the root causes of losses, organizations can develop effective countermeasures to eliminate them.
- TPM Roadmap: A strategic plan outlining the implementation steps and timeline for TPM. A well-defined roadmap provides a clear direction and helps organizations stay on track.
- TPM Audits: Regular assessments of TPM performance and progress. Audits help identify strengths, weaknesses, and areas for improvement, ensuring that TPM initiatives are on track.
- TPM Metrics: Key performance indicators used to measure TPM effectiveness. By tracking key metrics, organizations can monitor progress, identify trends, and make data-driven decisions.
TPM Benefits
- Increased Equipment Reliability: Reduced breakdowns and improved equipment uptime. By implementing TPM, organizations can significantly reduce unplanned downtime and increase equipment availability.
- Improved Product Quality: Fewer defects and higher product quality. TPM helps organizations identify and eliminate the root causes of defects, leading to higher product quality and customer satisfaction.
- Reduced Maintenance Costs: Lower costs associated with reactive maintenance. By focusing on preventive maintenance, organizations can reduce the frequency and severity of breakdowns, leading to lower maintenance costs.
- Enhanced Employee Morale: Increased employee engagement and ownership. TPM empowers employees to take ownership of their work and contribute to continuous improvement, leading to higher job satisfaction and morale.
- Improved Safety: Reduced accidents and injuries. By prioritizing safety in all TPM activities, organizations can create a safer work environment and reduce the risk of accidents.
- Increased Productivity: Higher output and efficiency. By eliminating waste and improving equipment performance, TPM can significantly increase productivity.
- Reduced Lead Times: Faster production cycles. TPM helps organizations reduce cycle times and improve delivery performance.
- Lower Energy Consumption: Improved energy efficiency. By optimizing equipment performance and reducing waste, TPM can help organizations reduce energy consumption and lower costs.
- Reduced Waste: Minimized waste and material losses. TPM helps organizations identify and eliminate waste in all areas of the operation, leading to cost savings and environmental benefits.
- Improved Customer Satisfaction: Higher quality products and faster delivery. By improving product quality and delivery performance, TPM can enhance customer satisfaction and loyalty.
TPM Challenges and Considerations
- Resistance to Change: Overcoming resistance from employees and management. Change can be difficult, and it is important to address resistance through effective communication, training, and leadership.
- Initial Investment: Required investment in training, tools, and equipment. Implementing TPM requires an initial investment, but the long-term benefits often outweigh the costs.
- Cultural Shift: Changing the organizational culture to embrace TPM principles. A strong cultural shift is necessary to embed TPM principles into the organization’s DNA.
- Top Management Commitment: Strong support and leadership from top management. Top management support is essential for the successful implementation of TPM.
- Employee Involvement: Encouraging active participation from all employees. Employee involvement is crucial for the success of TPM.
- Data Collection and Analysis: Accurate and timely data collection and analysis. Data is the foundation of TPM, and accurate data is essential for making informed decisions.
- Continuous Improvement: Maintaining a focus on continuous improvement. TPM is a journey, not a destination. Continuous improvement is essential for sustaining TPM benefits.
- Sustainability: Ensuring long-term sustainability of TPM initiatives. To ensure long-term success, organizations must institutionalize TPM and make it a core part of their business strategy.
TPM Case Studies and Best Practices
- Toyota Production System (TPS): A world-renowned TPM implementation model. TPS is a comprehensive system that integrates TPM with other Lean manufacturing principles.
- Lean Manufacturing: A complementary approach to TPM focused on eliminating waste. Lean manufacturing can be used to identify and eliminate waste in all areas of the operation, including maintenance.
- Six Sigma: A quality improvement methodology that can be integrated with TPM. Six Sigma can be used to identify and eliminate the root causes of defects and improve overall quality.
- Root Cause Analysis (RCA): A technique for identifying the root causes of problems. RCA is a powerful tool for identifying and addressing the root causes of equipment failures and other problems.
- Kaizen: A continuous improvement philosophy. Kaizen encourages small, incremental improvements that can lead to significant results over time.
- Visual Management: Using visual tools to communicate information and improve efficiency. Visual management can help identify problems, track performance, and improve communication.
- Standardized Work: Creating standardized procedures for tasks to ensure consistency and efficiency. Standardized work can help reduce variation and improve quality.
- Total Productive Equipment (TPE): Focusing on individual equipment rather than entire production lines. TPE allows organizations to focus on improving the performance of individual pieces of equipment.
- Total Productive Organization (TPO): Extending TPM principles to all organizational functions. By applying TPM principles to all areas of the organization, organizations can achieve greater overall efficiency and effectiveness.
- TPM Maturity Model: A framework for assessing the maturity level of a TPM implementation. A maturity model can help organizations identify areas for improvement and track progress.
TPM and Industry-Specific Applications
- TPM in Manufacturing: Applications in automotive, electronics, and other manufacturing industries. TPM is widely used in manufacturing industries to improve equipment reliability, product quality, and overall productivity.
- TPM in Healthcare: Improving equipment reliability and patient safety in hospitals. TPM can help hospitals reduce equipment downtime, improve patient care, and reduce costs.
- TPM in Food and Beverage: Ensuring food safety and quality in food processing plants. TPM can help food processing plants maintain high standards of food safety and quality.
- TPM in Energy: Optimizing energy production and distribution. TPM can help energy companies improve equipment reliability, reduce maintenance costs, and improve energy efficiency.
- TPM in Logistics and Supply Chain: Improving efficiency and reducing costs in logistics operations. TPM can help logistics companies improve equipment reliability, reduce downtime, and improve delivery performance.
Want to see MaintWiz in action?
Request a one-one demo with our solution engineering team.
Want to see MaintWiz in action?
Request a one-one demo with our solution engineering team.
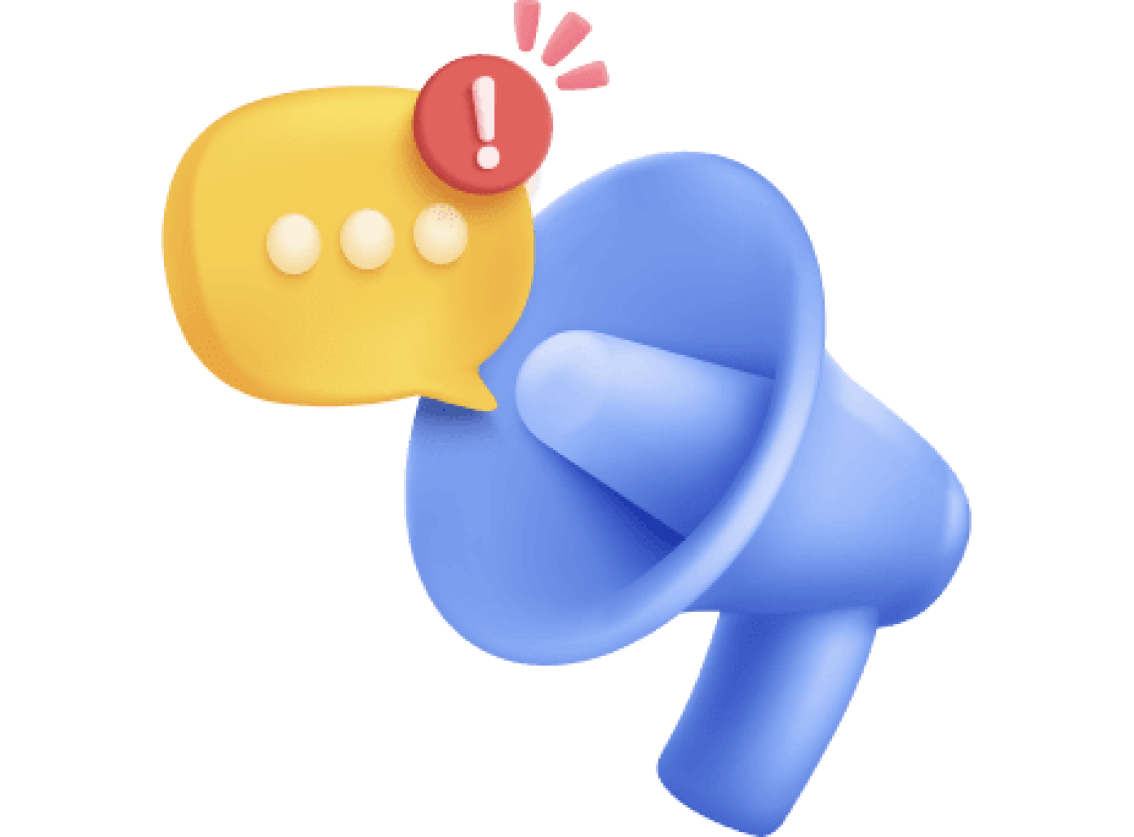