Plant Maintenance Terminologies and Keywords
Glossary of Asset Management
Comprehensive Glossary of Asset Management and Plant Maintenance Terminologies and Keywords
Alerts
Alert is a notice issued to get the attention of the stakeholder. Alert can be pre-facto (impending failure) or post-facto (work order creation or equipment failure). Maintenance alerts are triggered upon fulfillment of certain business rules and conditions, like the creation of a work order, reporting of breakdown, or breach of certain critical condition monitoring parameters.
For more detailed information about what a CMMS is and how it can benefit your organization, check out our detailed guide.
Annual Maintenance Contracts (AMC)
AMC or Annual Maintenance Contract is an agreement between the manufacturing organization and a service provider for the ongoing maintenance of certain assets. Annual Maintenance Contracts are entered for maintenance and support services, normally after the expiry of the warranty period. AMC services are typically offered by Original Equipment Manufacturers (OEM), Resellers, Specialized agencies, or third-party service providers.
Explore how Preventive Maintenance can help reduce breakdowns and optimize asset performance.
AMCs are governed by specific terms and conditions mutually entered that may include service levels, response time, resolution time, and cost coverage. AMCs cover preventive maintenance services and break-fix services andnormally labor costs and spare parts replacement. AMCs shift the maintenance expenditure from the organization to the vendor and thus help inconverting the variable costs to fixed costs. Some AMCs are structured with performance guarantees and penalties for service-levelbreaches as well. Discover how MaintWiz uses data-driven insights to improve maintenance with Predictive Maintenance.
Assembly Line
An assembly line or a production line is a production set-up, that manufactures a particular component or product. The Assembly line process breaks the manufacture of the component or product into steps, that are completed in a pre-defined order of sequence. An Assembly line normally consists of a group of equipment that aid in the production process. Manual assembly operations and packing lines may not have equipment but have people working on the pre-defined steps to complete a process. One manufacturing plant may contain many units and each unit may contain many assembly lines.
Asset
An asset is a resource, owned or controlled by an enterprise, and that creates a positive economic impact. Principal properties of industrial assets include ownership, economic value, and resourcefulness (ability to generate value). Physical assets are of interest, from a plant operations and asset maintenance point of view, as opposed to financial assets (investments, receivables) or intangible assets (goodwill, copyrights, patents, intellectual property).
Asset Intelligence
Asset intelligence relates to the insights gathered out of the wealth of asset information that the organization possesses, including their availability, performance, utilization, failure history, downtime analysis, cost of operations, maintenance interventions, cost of maintenance, etc. Asset intelligence is derived throughout the life cycle of the asset, from commissioning to retirement.
Asset intelligence is derived by combining static information (equipment specifications) with dynamic information (e.g. performance, condition monitoring data), comparison against benchmarks, trend analysis, and comparison against peer class assets or digital twin models.
Asset intelligence provides very valuable insights relating to asset utilization and performance, asset life enhancement, etc., thereby increasing return on investment.
Asset Management
Refer to Enterprise Asset Management (EAM)
Asset Management Body of Knowledge (AMBoK)
The Asset Management Body of Knowledge is provided by the Asset Management Council of Australia. AMBoK provides the principles that affect a company’s asset systems, including capabilities, learning, level assurance, and output focus of an organization.
Asset Master / Asset Register
An asset Register is a detailed list of all assets owned by the enterprise. Asset Register, in industrial plant maintenance context, includes facilities or physical locations (plants, units, assembly lines, buildings, etc.), equipment (production equipment, standby equipment, rotary equipment, mobile equipment, and other supporting equipment), instruments (inline and stand-alone), spares inventory, fleet, utilities, etc.
Asset Register includes many details about each asset including location, manufacturer, technical specifications, attributes, design, and other documentation, cost details, permits required to operate and maintain, equipment cost center and owner information, operational and failure history, etc. Asset registers used to be paper-based and manually maintained but nowadays computerized systems hold all the information. Asset Register is often referred to as Asset Master, Equipment Master, or Equipment register.
Asset Attributes
Each group or category of asset may have certain properties and unique specifications that need to be tracked, over and above what is commonly defined for all assets in the asset register. Asset attributes generally refer to such user-defined attributes, that are custom configured for a group of assets.
Audit Log
An audit log (sometimes referred to audit trail), refers to the sequence of changes made to an object. An audit log of work orders gives a record of chronological changes and events that occurred in the life cycle of the work order. i.e. when the work order was created by whom, what modifications and changes were done, when it was closed, and by whom, etc. The equipment audit log gives a record of changes and updates made to the specific equipment over its life cycle.
An audit trail helps reconstruct the set of events and changes and can be helpful for reviews, analysis, and improvement identification.
Availability
Availability or Uptime is the percentage of time a machine is ready-to-use. Availability is calculated as a percentage of the time the equipment is available and ready for use to the total planned time. Total planned time is computed as the product of the number of shifts and shift duration, less any planned downtime. Idle time does not impact availability.
Equipment Availability is a key metric related to equipment efficiency and maintenance team efficiency. Availability is a key component in computing Overall Equipment Effectiveness (OEE).
Bar Code
A barcode, consisting of bars and spaces in a certain pattern, is a machine-readable representation, that contains identification information about the product. Bar code averts human data entry and thus simplifies data capture. Bar code reading and interpretation need additional software and bar code reader hardware.
Bar code is used for spare parts inventory tracking. Bar code is nowadays replaced by a more advanced QR code. QR codes can contain more volume and variety of information and are easily readable by mobile apps, without the need for additional hardware or software.
Batch Process
The batch process or batch production is a production technique, wherein a set of identical products are produced together, rather than one at a time. All the items produced in a batch, go through the same production cycle at the same time. The manufacturer determines the size of the batch and the frequency of production of these batches. Items produced in the same batch share a common batch id, that is used for tracking and traceability.
Breakdown Maintenance
Breakdown Maintenance (also called Reactive Maintenance, Run-to-Failure Maintenance, and Corrective Maintenance) is a maintenance approach, that focuses on the repair/restoration of the equipment upon failure.
Breakdowns are unplanned events, that impact the overall production and thus can be very costly. Thus they tend to get a lot of attention and maintenance focus on preventing their occurrence by performing preventive and predictive maintenance, analyzing root causes, and instituting corrective and preventive actions.
Business Intelligence
Business Intelligence (BI) is the result of data processing and analysis of raw data. BI techniques help in analyzing raw data and identifying inferences and insights that help in strategic, tactical, and operational decision support. BI is presented as reports, graphs, charts and other visuals, dashboards, etc. to aid faster decision making. Business Intelligence systems are software driven and have many built-in ready-to-use functionalities.
Calibration
Calibration represents the units marked on an instrument that is used for measuring a certain parameter accurately and with minimal error. Instruments have measuring scales. Due to ageing and wear and tear, instrument scales tend to stray, resulting in errors. Such instruments are recalibrated to finetune and improve their accuracy.
Capital Expenditure (CapEx)Projects:
Capital expenditures (Capex) are funds used by a company to acquire, upgrade, and maintain physical assets such as facilities, plants, buildings, technology, or equipment. CapEx projects relate to the procurement, installation, and commissioning of such new assets. CapEx projects can be greenfield, wherein ground-up development is done, or brownfield, wherein the existing capacity is enhanced.
Maintenance teams, having intimate knowledge on the production process and equipment, are involved in CapEx projects. CapEx projects involve huge investment outlay and can extend for longer durations. Maintenance teams track the cost, schedule, progress, and product quality of the CapEx projects.
Checklist
A Checklist (often referred to as maintenance checklist) is a series of well-documented steps that need to be performed on the machine, as a part of maintenance intervention. Checklists are routinely used during preventive maintenance, troubleshooting during breakdowns, inspections, audits, etc.
CMMS
Checklists are printed on paper or used in electronic form. Checklists normally have 2 parts – pre-defined instructions and data entered by maintenance technicians. Data entered include problem description, non-conformances, and observations, equipment condition, recording of meter readings, etc. Completion of the checklist (or a certain percentage of it) may be mandated for the closure of the underlying maintenance order.
Code of Federal Regulations (CFR)
The Code of Federal Regulations (CFR) is the codification of the general and permanent rules promulgated by the US Federal government and published in the Federal Register by the departments and agencies. The CFR is divided into 50 titles that represent broad areas, wherefederal regulations are applicable.
Title 21 of CFR deals with Food and Drugs. Underneath Title 21, Part 211outlines Good Manufacturing Practices (GMP), Part 21 on data retention and digital signatures, Part 67 on maintenance etc. Title 14 of CFR deals with the aviation industry and outlines asset management and maintenance practices to be followed.
Condition Based Maintenance
Condition Based Maintenance (CBM) is a maintenance approach, wherein the planned preventive maintenance is executed only when certain equipment parameter conditions are met. The principle behind CBM is to perform maintenance, where it is due. Key equipment parameters are tracked and when they show signs of deterioration, a preventive maintenance order is triggered with a corresponding checklist.
The predictive maintenance strategy uses equipment conditions and parameters as input for determining the maintenance work to be carried out and hence some people use condition monitoring and predictive maintenance interchangeably. However, the scope of predictive maintenance is far larger.
Condition Monitoring
Condition Monitoring is a maintenance technique wherein equipment condition and safety are measured, by monitoring changes in certain vital parameters. These parameters act as lead indicators and continued deterioration of the parameters represents underlying problems. Monitoring of temperature, pressure and vibration, current analysis, oil analysis, etc. provide insights on equipment condition and maintenance interventions required. Learn more about how Condition Monitoring can help you monitor equipment health in real-time.
Connected Systems
Connected systems are the group of individual physical equipment that are connected with each other and other systems via the internet or private network. Connected systems can act in unison and thus their sum represents more than its parts.
Modern shop floor contains many Smart equipment, that has microprocessors and digital interfaces. All transactional information is captured and is available via the M2M interface. Additionally, industrial control systems monitor the production process and operating conditions. Modern plants have collections of interrelated and connected systems, consisting of hardware, software, data capture devices, processing algorithms, control systems, and decision support systems. Together these connected systems can collect, process, decide and control production processes through smart actions.
Continuous Improvement
Continuous improvement is a process management technique that outlines the ongoing improvement of products, processes, and services. Continuous improvement emphasizes consistent and incremental improvements done repeatedly over time to improve the process and systems. Continuous improvement relies on operators and practitioners to suggest improvements for streamlining processes and eliminating waste, based on their daily experience. Reengineering, radical innovation, and disruption normally lie outside the scope of the continuous improvement process.
Continuous Improvement, referred as Kaizen, is a key component of Japanese management and often an area of focus under Total Productive Maintenance (TPM), Lean Maintenance etc.
Continuous Process Industry
Continuous Process industries are those in which the major production operations are either continuous or occur on an indistinguishable batch of materials.
Control System
A control system is a set of electromechanical or electronic devices, that uses control loops to regulate other equipment, components, or systems. Large industrial control systems like PLC, SCADA, DCS, MES, etc. control processes or multiple equipment. Control systems monitor certain parameters and control the desired response by controlling certain dependent parameters. Control systems gather and process huge data sets of information. These datasets can provide many insights into equipment condition, performance, and history.
Corporate Social Responsibility:
Corporate Social Responsibility (CSR) encourages businesses to incorporate social and environmental issues into their everyday operations and relationships with stakeholders. CSR practices ensure that the organizations are aware of the kind of economic, social, and environmental impact they are creating. With positive contributions, CSR enables organizations to become good corporate citizens.
Corrective Actions
Corrective Actions refer to the set of immediate, one-time measures that must be taken to resolve the underlying root cause. Corrective Actions are normally identified as a result of why-why analysis (root cause analysis), non-conformances in audits, and safety incidents. Corrective Actions are powerful countermeasures to avoid the potential recurrence of the underlying issue.
Corrective Maintenance
Corrective maintenance is a type of maintenance that deals with the repair and restoration of faulty or inefficient equipment. The scope of maintenance work performed under corrective maintenance includes troubleshooting, issue detection, repair, and restoration including replacement of faulty components, adjustments and alignments, and corrective actions to prevent a recurrence. Corrective maintenance is often interchangeably used with breakdown maintenance or reactive maintenance. Some differentiate breakdown maintenance and corrective maintenance, based on the incidence of equipment failure.
Cost Center
A cost center is a department or function within an organization to which costs are charged for accounting purposes. By definition, they are not generating any revenue or profits. The maintenance department is a cost center to which all equipment maintenance-related costs (spares, labor, AMC, bought-out services, and other vendor charges) are all charged. Individual cost centres will have annual budgets against which their expenditure is tracked and variances are analyzed.
Cost Of Maintenance
Cost of maintenance (Maintenance Costs) includes all the expenses relating to the maintenance interventions for the upkeep of plant assets. Maintenance costs include fixed payroll costs and variable spare parts costs. They may incur additional costs relating to contract staffing, bought-out services, vendor services, equipment rentals, fees towards audits and inspections, etc. The cost of maintenance is tracked at the unit level, to review and analyze costs with corresponding benefits.
For all maintenance interventions, the cost of maintenance is tracked against individual work orders. Each work order tracks the cost of labor, spare parts, and vendor costs. Such work order level costing can be aggregated to view overall costs based on the type of maintenance (preventive vs breakdown) or monthly costs, budget vs actual,etc.
Cycle Time
Cycle time is the total actual time spent on the production of a good or service, from the time of initiation to completion. Cycle time is used in discrete and batch production processes. Cycle time measurement is also used in Lean Maintenance.
Daily Log Book
A daily log book (or daily logbook) is a journal entry that records all events on the shop floor, including equipment status, maintenance interventions, timings, maintenance shift allocation, energy consumption, and other important occurrences. The format of the daily logbook adheres to the business requirements of the organizations. The daily logbook is often called a maintenance logbook, equipment maintenance logbook, etc.
Daily log books can be paper-based with manual entries or electronic with a combination of manual recordings and system-generated transactions. Physical log books, though they may contain a lot of information is often restricted to local access and may pose challenges in gleaning intelligence for efficiency improvements. Maintenance log books provided as part of CMMS make them available to users outside the plant and as well can generate insights into asset management and maintenance.
Digital Twin
A digital twin is a virtual model of physical equipment or the object of reference. Digital twins are constructed based on the technical, operational, and performance aspects of the physical equipment. Historic data, operating conditions, and equipment behavior are built in and the model has been back-tested to closely resemble the behavior of the physical equipment.
Digital twins serve many purposes – from visualizing the parameters as an augmented reality to running simulations to improve performance. Once a digital twin is successfully modelled, a variety of test cases and simulation experiments can be conducted to assess the risk, reliability, performance, and efficiency of the physical equipment. Learnings derived on areas of improvement, boundary conditions for maximizing asset utilization and performance, etc. can be applied to the physical equipment.
The digital twin concept, when extended to resemble the entire factory is called a Factory Twin.
Downtime
Equipment downtime refers to the amount of time that equipment is not available or operating, due to equipment failure or malfunctioning, or planned maintenance. Equipment downtime due to breakdown is an unplanned event. Preventive maintenance may involve some planned downtime as well. Downtime is complementary to uptime and is a key metric to compute availability and Overall Equipment Effectiveness (OEE). Downtime is distinct and different from idle time, wherein the equipment is available but not up and running.
Energy Monitoring
Energy Monitoring is the process of tracking energy consumption and usage patterns, for an equipment, group of equipment, section of a plant, or the full plant. Energy monitoring helps in identifying excessive energy usage, conservation, and cost savings.
Enterprise Asset Management (EAM)
Enterprise Asset Management is a holistic process to efficiently control and utilize the assets owned or controlled by the organization to maximize the business value generated out of it. Enterprise Asset Management spans the entire lifecycle of an industrial asset including acquisition (planning, budgeting procurement, commissioning), operations, maintenance, and disposal (decommissioning, replacement planning). Enterprise Asset Management usually involves a combination of processes, systems, technology, services, and information.
Equipment
Equipment refers to the set of machines used in the production of goods or services. Equipment can be machinery directly utilized in the production or support machinery that aids production (like captive power plant equipment). Availability, and utilization of Equipment directly impacts the production and thus are critical in the manufacturing industry. Equipment can be monolithic or composite with assembly sub-assembly systems. A production line is made up of equipment that helps in progressively manufacturing or assembling a particular product in a sequential manner.
Equipment Budget
The equipment budget is the expected cost of maintaining the equipment over a certain period of time. Equipment budget is normally computed for a financial year, though certain organizations compute for a longer term of 5 years or over their life cycle.
The equipment budget includes the cost of all maintenance interventions, including preventive maintenance, breakdown maintenance, predictive maintenance, etc. The equipment budget normally excludes the running costs related to operations. Equipment budget can be categorized and visualized on the basis of labor, spare parts, and bought-out services as well.
The equipment budget gives a good benchmark to measure the maintenance costs and perform variance analysis.
Equipment Life Cycle
An Equipment Lifecycle describes the stages of equipment from acquisition to retirement. The equipment lifecycle lasts during the lifespan of the equipment. i.e. longer the lifespan better is the economic value derived. As the equipment ages, the availability and performance start to deteriorate. Maintenance interventions keep it up and running. Well-maintained equipment can have an extended life span.
The goal of the maintenance team is to have proactive and planned maintenance interventions to maximize equipment’s availability and performance and extend its lifespan.
Equipment Maintenance
Equipment Maintenance includes all the processes and procedures relating to the upkeep of production equipment and other capital assets, to ensure that they are available and in good working condition. Equipment maintenance interventions are carried out through out the life cycle of the equipment. It includes Planned Preventive Maintenance, Breakdown Maintenance, Inspections, Equipment Audits, Shutdown Maintenance, Predictive Maintenance, Performance Optimization etc.
Equipment maintenance is a critical activity in the manufacturing sector, and it impacts positively on equipment availability, reliability, performance, equipment safety, and life of the asset.
Equipment Master
Refer Asset Master
Enterprise Resource Planning (ERP):
Enterprise Resource Planning (ERP) refers to a comprehensive business software application, that organizations use to manage their daily operations. The scope of ERP covers all major business activities from supply chain to customer management, financial accounting, human resources, etc. ERP is expensive and requires huge investment, a long implementation cycle, and people’s time. Organizations use ERP as their core business application. SAP, Oracle ERP, Microsoft Dynamics, and Infor (Baan) ERP are popular commercially available ERP applications. Some companies opt for homegrown ERP application development as well.
ERP Integration
ERP applicationsaddress the entire spectrum of requirements for business organizations. ERPs, by virtue of their legacy, often act as a system of record and tend to look at all transactions from an economic perspective. Many functions within the enterprise need specialized solutions that can address all their requirements uniquely and in a deeper manner. This led to the emergence of many best-of-breed stand-alone solutions, often offered as Cloud hosted Software-as-a-Service. Organizations need such stand-alone solutions to integrate with their ERP and exchange the necessary information. ERP integration enables the connection of best-of-breed stand-alone business applications with the Enterprise Resource Planning software to facilitate seamless data exchange and synchronization.
ESG:
ESG means using Environmental, Social, and Governance factors to assess the sustainability practices of manufacturingplants and production units.
Environmental factors include the contribution to climate change through greenhouse gas emissions, along with waste management and energy efficiency. Green manufacturing practices advocate improving environmental friendliness by cutting emissions and decarbonizing.
Social include human rights, labor standards in the supply chain, any exposure to child labor and illegal labor practices, and more routine issues such as adherence to workplace health and safety. Corporate social responsibility via participation in local community development and contribution to their progress
Governance refers to a set of rules or principles defining rights, responsibilities, and expectations between different stakeholders in the governance of corporations. A well-defined corporate governance system can be used to balance or align interests between stakeholders and can work as a tool to support a company’s long-term strategy.
Event-Based Maintenance
Event-Based Maintenance (EMB) is a maintenance approach, wherein multiple maintenance work orders will be generated, upon the occurrence of an event. The event can be unplanned like a fire or flood or planned event like a customer visit.
The occurrence of certain events requires the maintenance teams to act upon many maintenance interventions within a short span of time. Time availability for planning may be limited in many cases or the same playbook has to be repeated on each occurrence. EBM comes in handy in such scenarios with the definition of all the preventive maintenance work that needs to be executed and the setting up of the associated trigger conditions. Upon the incidence of the event, EBM can be activated and all the maintenance work orders will be generated. Thus EBM provides an easy way to handle such event-based maintenance interventions.
Facility
A facility is a building, campus, manufacturing unit, or any other physical location, wherein a certain economic activity is performed. Facilities include all production units, warehouses, yards, utilities and other related areas in manufacturing plants. Facilities can also denote large industrial or office buildings, educational institutes, public utilities and service areas, government buildings, stadiums, etc. Facilities host equipment, tools, and other production assets.
Facility Maintenance
Facility Maintenance refers to the upkeep of the facilities. It includes all the repairs, corrective actions, structural and other safety inspections, audits, etc. Facility Maintenance generally involves civil, electrical, and mechanical maintenance. Facility Maintenance ensures that the physical location is available for usage, safe to operate for the people and industrial assets, reliable for continued operations, and cost-effective.
Failure
A failure is a condition or state of the equipment, in which the equipment does not or cannot be operated as intended. Failure is an unplanned event and excludes all planned outages. Equipment failure impacts production output and thus is directly related to the revenue. Breakdown maintenance is carried out to resolve the issue and bring back the machine to the stipulated working condition.
Failure Analysis
Failure analysis is a structured approach followed after an unplanned failure, to identify the causes of the failure. It involves data collection pertaining to the equipment functioning, nature of failure, past performance, maintenance history, conditions and other contributing factors. A thorough analysis is followed to determine the root causes and plan remedial measures (Corrective Actions and Preventive Actions) to avoid recurrence. Failures are costly and hence failure analysis is critical in industrial context.
Failure Code
A failure code is a short alphanumeric character that refers to one of the possible failure reasons. Failure codes help the maintenance team in tracking and analyzing the failures. A list of possible failures is published by the Original Equipment Manufacturer (OEM). However, organizations may have their own set of failure codes for tracking. Failure codes are tracked via work orders in CMMS or EAM systems.
Industry 4.0
Industry 4.0 or the Fourth Industrial revolution refers to the digital transformation of the manufacturing industry and production processes. It involves efficient information capture via the integration of physical objects with digital technologies. Information captured is analyzed and used for monitoring, controlling, improving, and predictive purposes.
Industry 4.0 is a wide umbrella and covers a gamut of technologies including Artificial Intelligence, Cloud Computing, Smart Machines, Mobile Computing, the Internet of Things, Augment Reality / Virtual Reality, Additive Manufacturing, etc.
Industry 4.0 helps in the proactive identification of problems and impending failures and in instituting remedial actions. Industry 4.0 technologies also help in delivering asset intelligence to people and improve their productivity. The usage of Artificial Intelligence, Machine Learning and Digital Twins helps improve equipment efficiency significantly.
Inspection
Inspection refers to any process wherein an asset (equipment, building, or another physical asset) is closely examined to evaluate its condition, performance, or operational parameters, to ensure that it meets the specific stipulated standards. Inspection is done to identify any potential discrepancy, deficiency, or safety issues and to determine the remedial course of action. Inspections can be carried out as a result of an event or as per a planned schedule.
Instrument
An instrument or a measuring instrument is a special-purpose device that helps in measuring certain physical parameters, related to the asset or operating conditions. Instruments obtain the physical quantity, in accordance withstandard units of measurement and within acceptable deviations. Thus it helps in understanding the performance and behavior of the asset.
Internet Of Things
The Internet of Things is a connected network of physical objects. Modern production shopfloors contain many smart equipment, that has built-in sensors, processors, PLCs, and control systems. Besides the shop floor also has other external control systems including SCADA, MES, DCS, etc. Together all of these collect, analyze, monitor, and control the data pertaining to the equipment.
The Internet of things enables positive interventions to be carried out at a micro level of equipment and/or at a macro level of the production ecosystem. The Internet of things overcomes the physical barriers of access and allows remote access to the equipment by command center experts for monitoring and improvement. The Internet of Things improves efficiency, performance, and return on investment.
ISO
International Organization for Standardization is an international, non-governmental federation of national standards bodies. Its primary role is to develop and publish standards for commercial and technical usage. ISO standards cover most of the products, processes and services that are available. ISO standards are not mandatory, though certain standards have been mandated by individual countries. Common standards ensure quality, safety, and interoperability and facilitate global trade. ISO also publishes technical reports, technical specifications, and guides.
ISO 13374
ISO 13374 outlines the open Condition Monitoring and Diagnostic (CM&D) software architecture to facilitatedata processing, communication, and presentation across different platforms. ISO 13374-1 gives a general overview of data processing, communication, and presentation. ISO 13374-2 provides greater details into data processing methodology and requirements that should be present in today’s software-enhanced systems. ISO 13374-3 provides the requirements of the data communication architecture for open CM&D systems.
ISO 14224
ISO 14224 is an industry-specific standard and is applicable to the petroleum, petrochemical, and natural gas industries. ISO 14224 outlines the collection of data for the maintenance of equipment, including reliability data. It covers both methodologies for the data collection, and details of the data to be collected.
ISO 55000
ISO 55000relates to asset management and asset management systems within the context of an organization. It outlines an overview of asset management and sets out principles and terminology. ISO 55000 can be applied to the broadest possible set of organizations across different industries and for all types of assets. ISO 55001 and ISO 55002 are related to ISO 55000. ISO 55001 specifies the requirements of an asset management system in an organization. ISO 55002 provides additional useful guidance for applying ISO 55001.
Maintainability
Maintainability is the ease with which an asset can be maintained to maximize availability, efficiency, reliability, and safety. It’s a measure of efficiency to indicate how quickly and efficiently the equipment can be restored after a breakdown or malfunction. Maintainability is dependent on the design of equipment including ease of assembly/disassembly, environmental conditions, availability of relevant information and manuals, trained resources, and other supporting organizational factors.
Maintenance Audits
A maintenance audit involves a thorough review and methodical examination of all the maintenance process assets of an organization. Maintenance audits assess the enterprise asset management and maintenance goals, systems and processes, preventive and predictive maintenance approach, past failures and response, resource availability, utilization and readiness, competency and training requirements, standards, compliance, best practices, metrics, etc.
Enterprise Asset Management has evolved at a rapid pace. Plant maintenance has not caught up at many organizations. A maintenance audit is comprehensive and can uncover gaps and areas of improvement for improving maintenance processes and practices.
Maintenance Backlog
A maintenance Backlog is a structured list of maintenance interventions required over a specified period of time, and are not yet completed. It will include preventive maintenance activities, inspections and audits, corrective actions and preventive actions, safety initiatives, energy conservation projects, overhauls, projects, shutdowns, reliability initiatives, etc.
The maintenance backlog will contain the list of tasks, prioritization, estimated person days of effort, spare parts required, vendor and other outside help required, etc. Maintenance backlog helps the maintenance planning with the right prioritization, resource allocation, project planning, and execution.
Maintenance Budget
The maintenance budget is the amount of money that is available for the maintenance department to carry out all the maintenance interventions, planned for that period. Maintenance budgets are normally allocated over the financial year. The maintenance budget can be broken down to major cost areas: labor, materials, contract staffing, bought-out services, instrument calibrations, inspections and audits, annual maintenance and service contracts, and other related expenses.
Maintenance Productivity Factor (MPF):
The maintenance Productivity Factor (MPF) is an aggregate metric derived as a function of execution efficiency, maintaining quality, and effectiveness. Execution efficiency is the amount of time taken for the completion of the maintenance work. Maintenance quality reflects the degree of excellence in the maintenance work execution. Effectiveness reflects the organizational impact of the maintenance job undertaken. The maintenance Productivity Factor (MPF) is a measure of the productivity of the maintenance workforce.
Maintenance, Repair And Operations (MRO)
MRO stands for Maintenance, Repair and Operations or sometimes referred to as Maintenance, Repairs and Overhaul. It includes the set ofactivities associated with the daily operations of the plant. MRO involves the upkeep of facilities, equipment, instruments, utilities, material handling equipment, tools, and other production-related industrial assets. MRO comprises routine, planned maintenance activities, reactive breakdown maintenance, or futuristic predictive maintenance. The goal of MRO is to optimize availability, production efficiency, and safety.
Maintenance Software
Refer Computerized Maintenance Management System (CMMS)
Maintenance Team
A maintenance Team means all the employees of the Plant Maintenance or Plant Engineering department. Maintenance team members are technicians who are trained on the plant equipment and processes and help out in the restoration and repair of malfunctioning equipment.
The maintenance team possesses competency in electrical, mechanical, hydraulic, civil, and other engineering disciplines required to support manufacturing operations. In some organizations, the maintenance team handles related functions like utilities, instrumentation, logistics, spare parts inventory, etc. In addition to break-fix, maintenance teams proactively plan and execute maintenance activities to prevent unplanned failures.
The maintenance team act as custodian of the plant assets. The goal of the maintenance team is to ensure equipment uptime, efficiency, and safety.
Mean Time Between Failures (MTBF)
Mean Time Between Failures (MTBF) of equipment represents the average elapsed time between two successive unplanned failures, during normal operations. Each failure is recorded with a date and time. The time between failures (TBF) is calculated and MTBF is computed as the arithmetic mean of all the time between failures. Some organizations compute MTBF between the same type of failure for deriving better analysis and improvement insights.
The higher the MTBF, the longer is the equipment availability without failures. The goal of the maintenance team is to maximize MTBF i.e. increase the elapsed time between failures or reduce their incidence. MTBF is normally associated with a repairable system.
Mean Time to Failure (MTTF)
Mean time to failure (MTTF) is a maintenance metric that measures the average amount of time a non-repairable asset operates before it fails. It is a predicted measure with an estimated time in the future after which a failure is expected in the non-repairable system. MTTF can be calculated for a component, sub-assembly, assembly, equipment or system and is a measure of its reliability.
Mean Time to Repair (MTTR)
MTTR is the average time required to repair a failed component or equipment and restore it to production status. Time to Repair (TTR) is the elapsed time between failure and restoration. MTTR is computed as the arithmetic mean of TTR over a specified time. It is a measure of the maintenance team’s efficiency. Shorter the MTTR, the more efficient the maintenance team. With ageing of equipment, MTTR tends to get longer, due to wear out and inter-related functions.
Near Miss Reporting
Near-miss events are incidents that could have led to bodily harm and/or property loss but didn’t, in this time. It is an unplanned event that did not result in injury or loss of life or damage but had the potential to do so. Near-miss reporting is done via paper or electronic means in the specified format. Safety teams review them, analyze the cause, and institute hazard resolution and preventive measures.
Some organizations use the terms hazard, safety concern, or unsafe condition when there is no event or action and report them as Near-miss reporting.
Non-Conformance
Non-conformance (NC) indicates deviation from standards or laid out specifications. It is a measure of quality. Non-conformance can be for a product (defect), process (deficiency or gap), system or service (deficiency).
Non-conformance can be identified via routine testing, an inspection of products and services, and via customer feedback. Non-conformance affects the quality of the end product or service and can cause financial, and reputational damages or market share loss to the organization. The goal of the organization is to reduce non-conformance or improve consistency.
Operational Efficiency
Operational Efficiency defines the degree to which the production unity or entity can produce with reference to its defined capacity. Operational Efficiency optimization involves the elimination of waste. Waste can occur in time, effort and materials and due to equipment downtime, equipment idle time, operator unavailability, and as a result of other planned and unplanned events.
Planned Maintenance
Planned maintenance is a type of maintenance that is performed on a regular, predetermined schedule. This can include tasks such as inspections, cleaning, lubrication, and minor repairs, as well as more extensive tasks such as component replacements and upgrades. Planned maintenance is typically performed on a regular basis, such as daily, weekly, monthly, or annually, and is designed to prevent equipment failure and prolong the life of the asset. It is an important part of a comprehensive maintenance plan and can help ensure that equipment is operating efficiently and effectively.
Plant Maintenance
Plant maintenance involves the upkeep of all the production and production-related equipment, available in the plant, to ensure their continued availability and running at the designed capacity. It includes breakdown, preventive and predictive maintenance. Plant maintenance may involve routine inspections, CLITA activities (Cleaning-Lubrication-Inspection-Tightening activities), Utility management, building management, and safety as well. The goals of maintenance include availability, performance, reliability, safety, and cost control.
PM Compliance
The percentage of preventive maintenance work orders that are completed to the total number of preventive maintenance orders that got generated is known as preventive maintenance compliance (PM compliance) or schedule compliance. PM Compliance is a measure of how well a period’s worth of PM tasks are getting completed.
Preventative Maintenance
Refer Preventive Maintenance
Preventive Action
Preventive Actions are the set of measures taken proactively to avert the recurrence of the underlying issue. Preventive Actions can be the result of root cause analysis (why-why analysis), or non-conformance found in audits or reviews of safety incidents. Preventive Actions may be repetitive and include strengthening the tasks performed under preventive maintenance schedules or altering their recurrence pattern.
Preventive Maintenance
Preventive Maintenance (also called as Preventative Maintenance, Scheduled Maintenance, Planned Maintenance, or simply PM) is a planned maintenance activity carried out proactively to the plant equipment. The goal of preventive maintenance is to address the frequent causes of failures before they cause a catastrophic and costly breakdown. Preventive maintenance involves inspection activities, routine maintenance tasks, replacement of worn-out or near end-of-life spares, minor overhauls, and correction of any non-conformances observed.
Reliability
The ability of an equipment to function flawlessly under predetermined circumstances for a predetermined amount of time is known as reliability. It is measured by the probability of success and is inversely related to failures. Recurrence and frequency of failures influence the probability and thus impair reliability. Reliability is used in mission-critical industries, like aviation and nuclear plant, where the risk of failure is catastrophic.
Safety
Safety entails minimizing risks, accidents, hazards, and near-misses, to ensure a safe plant with safe work environment. Safety ensures the protection of people, plant assets, and the environment from getting harmed, due to the incidence of random events.
Shop Floor
Shop floor represents the area in which people work on machines and actual production activities are carried out. Administrative areas and office space, even though they are part of the manufacturing plant, are excluded from the definition of the Shop Floor. Thus Shop Floor is figuratively used to represent production equipment or production workers.
Six Sigma
Six Sigma is a statistical approach that makes use of data analysis and statistics to analyze and reduce defects. Six Sigma was popularized by General Electric. Six Sigma represents under 3.4 defects per million units of production or opportunities of service.
Spares Inventory
A spare part is an interchangeable part of an equipment or a machine, that can be used to replace an old part, which is worn out, broken or malfunctioning. Spare parts are critical for the timely resolution of breakdowns and recommencement of production. Critical spare parts of all equipment are stored in the manufacturing plant. Spares Inventory represents the collective spare parts that is held in stock, either in centralized store or over local stores, to supply at times of need.
Sustainability
Sustainability is the resilience with which the organizational systems withstand risks and threats and continue to be effective in achieving the stated purpose. Sustainability is a delicate balance to achieve the often conflicting goals of today and the future. Sustainability extends beyond business to cover the community, environment, and society.
Task
Tasks (often referred to as Maintenance Tasks) represent the series of actions, that the maintenance technician must carry out to fulfil the specified maintenance intervention. Tasks are part of work orders and carried out as part of breakdown maintenance, preventive maintenance, shutdown maintenance, etc.
Time-Based Maintenance
Time-based maintenance (TBM) is a preventive maintenance approach, that is triggered based on elapsed calendar time. It is very simple and easy to administer. TBM is agnostic to theequipment condition or the number of hours the equipment has run since the last maintenance. TBM is a planned intervention and has to be scheduled in advance.
Total Productive Maintenance
Total Productive Maintenance (TPM) is a Japanese management approach to achieve a superior production system with zero breakdowns, zero minor stoppages, zero defects, and zero accidents. TPM has been widely practiced by manufacturing organizations across the world.
TPM framework consists of a 5S foundation and eight supporting pillars.TPM advocates a proactive and holistic approach to equipment management and maintenance, with shared ownership between operators and maintenance technicians. TPM strives to maximize overall operational efficiency.
Total Quality Management (TQM)
Total Quality Management (TQM) is a management approach with a focus on building a customer-focused organization. TQM advocates an inclusive and participatory environment, where all stakeholders are together responsible for the overall quality of the final product. It emphasizes the elimination of errors or wastages, streamlining processes, enabling culture, and continuous improvements. Eight principles around customer focus, employee involvement, process efficiency, integrated system, systematic approach, continual improvement, fact-based decisions, and communications guide the TQM implementation.
Usage-based Maintenance (UBM)
Usage-based Maintenance is a preventive maintenance approach where the maintenance schedule is based onthe actual usage of the equipment. UBM is an improvement over TBM, as it takes into account the actual usage than mere elapsed time. UBM approach includes the measurement of key metrics and when the usage exceeds the pre-defined thresholds, preventive maintenance orders are generated. Usage parameters include run hours, the number of units produced, miles traveled, etc.
Warranty
A warranty is a commitment made by the Original Equipment Manufacturer (OEM) of the equipment regarding the durability and functionality of the equipment, for a predetermined time after the initial purchase. If there is a failure during the warranty period, OEM agrees to restore the equipment free of cost. Warranty types include comprehensive, limited, and combinations of the two.
World Class Manufacturing (WCM)
World Class Manufacturing is a set of concepts, that establishes production and manufacturing standards for organizations to follow. WCM is a process-driven approach and includes techniques like Make to order, Streamlined Flow, Smaller lot sizes, Collection of parts, Doing it right the first time, Cellular or group manufacturing, Total preventive maintenance, Quick replacement, Zero Defects, Just in Time, Increased consistency, Higher employee involvement, Cross-Functional Teams, Multi, Skilled employees, Visual Signalling, and Statistical process control.
Work Order
A work order is an authorization for the execution of maintenance, repair, inspection, installation, or other types of tasks on an industrial asset or equipment. Work orders are also referred to as WO, maintenance orders (MO), maintenance work orders (MWO), etc. Work orders can be hand-written, paper-based maintenance forms, maintenance daily log book entries, system-generated printouts, digital work orders like maintenance software, mobile app, etc. Many types of work orders exist.
Work orders can be manually generated or system generated (preventive work orders, automated work order generation). Work Orders contain details relating to the maintenance transaction and may include labor, spare parts, vendor services, etc. Work orders may be associated with work permits approved by safety officers. Work orders may also contain detailed root cause analysis of the failure and corrective actions and preventive actions to prevent their recurrence in the future.
Work Request
A Work Request is a written or electronic form that is used to submit the initial maintenance request. Once approved, this document becomes a work order. Work Requests are very simple and consist of essential details and are mostly generated by production operators or other non-maintenance people. The maintenance team addresses them once they are converted to work orders.
Work Order Life Cycle
Work order lifecycle defines the series of states or statuses, that the work order passes through, often in sequential order, from initiation of the work order to completion. Common work order statuses include initiation, assignment, troubleshooting, task execution, completion, and closure. Additional states may include securing permits to work, approvals, waiting time, on hold, vendor help requested, etc.
Work Order Management
Work Order Management is the process of quickly and efficiently completing work orders by meeting the goals of time, quality, and costs. Work Order management deals with a multitude of work orders for a wide array of equipment with varying demands and priorities. All the work orders, both planned and unplanned, compete for the same set of resources (technician allocation, spares, and other resources). Work order management deals with the overall management including proper prioritization, scheduling, spare allocation, staffing, and other resources to ensure timely completion.
Workflow
Workflow is a sequence of activities that need to be carried out in a specified order, to complete a given task. Workflows may traverse through different paths based on the status of the prior state. Workflows also support decision points, where an approving authority can approve, reject, send back or put the request on hold. Workflows adhere to established business rules and are orchestrated.
Request a one-one demo with our solution engineering team.
Request a one-one demo with our solution engineering team.
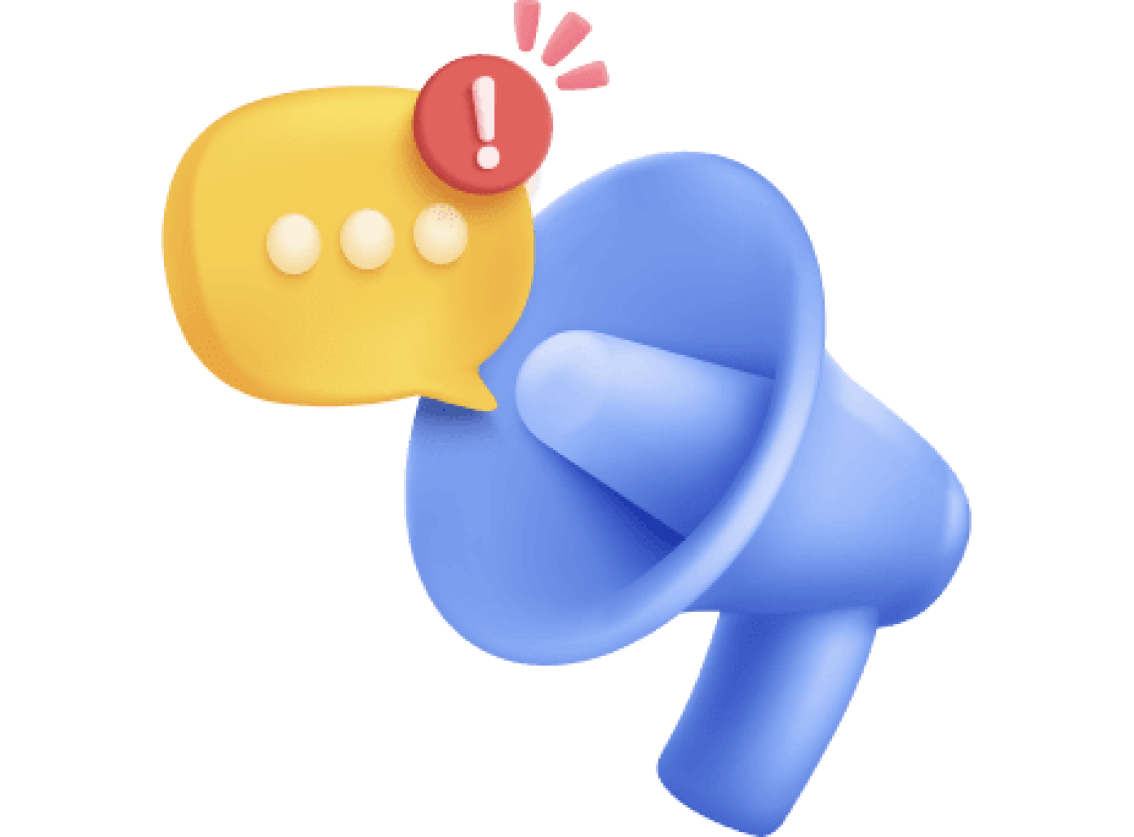