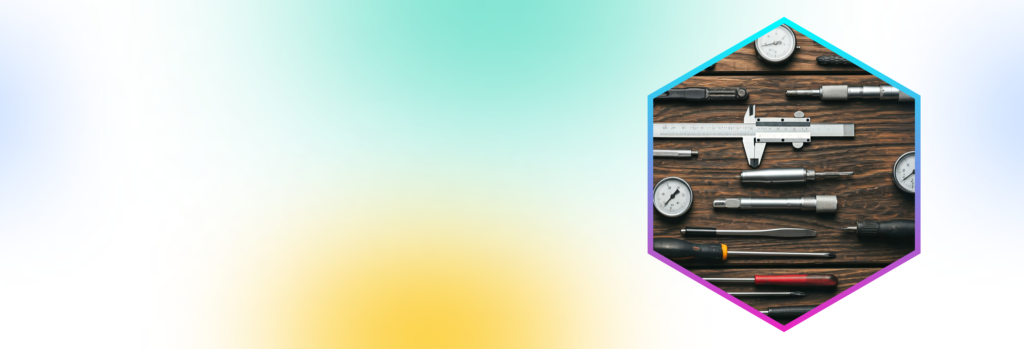
Planning & Deploying
Costly Inspection
Instruments at Client Sites
Table of Contents
TogglePlanning and Deployment of High Cost Inspection Instruments at Client Sites
Business Requirement
A Large Engineering Company provides a variety of Specialized Services to its Clients based on it’s own line of OEM Equipment and 3rd party equipment. Scope involves inspection, assessment, domain consulting, efficiency improvements, management of change and special projects. Needed a comprehensive platform to manage Client Asset Information, Projects, Field Services and efficiently managing Company owned high cost instruments (eg. Kiln alignment).
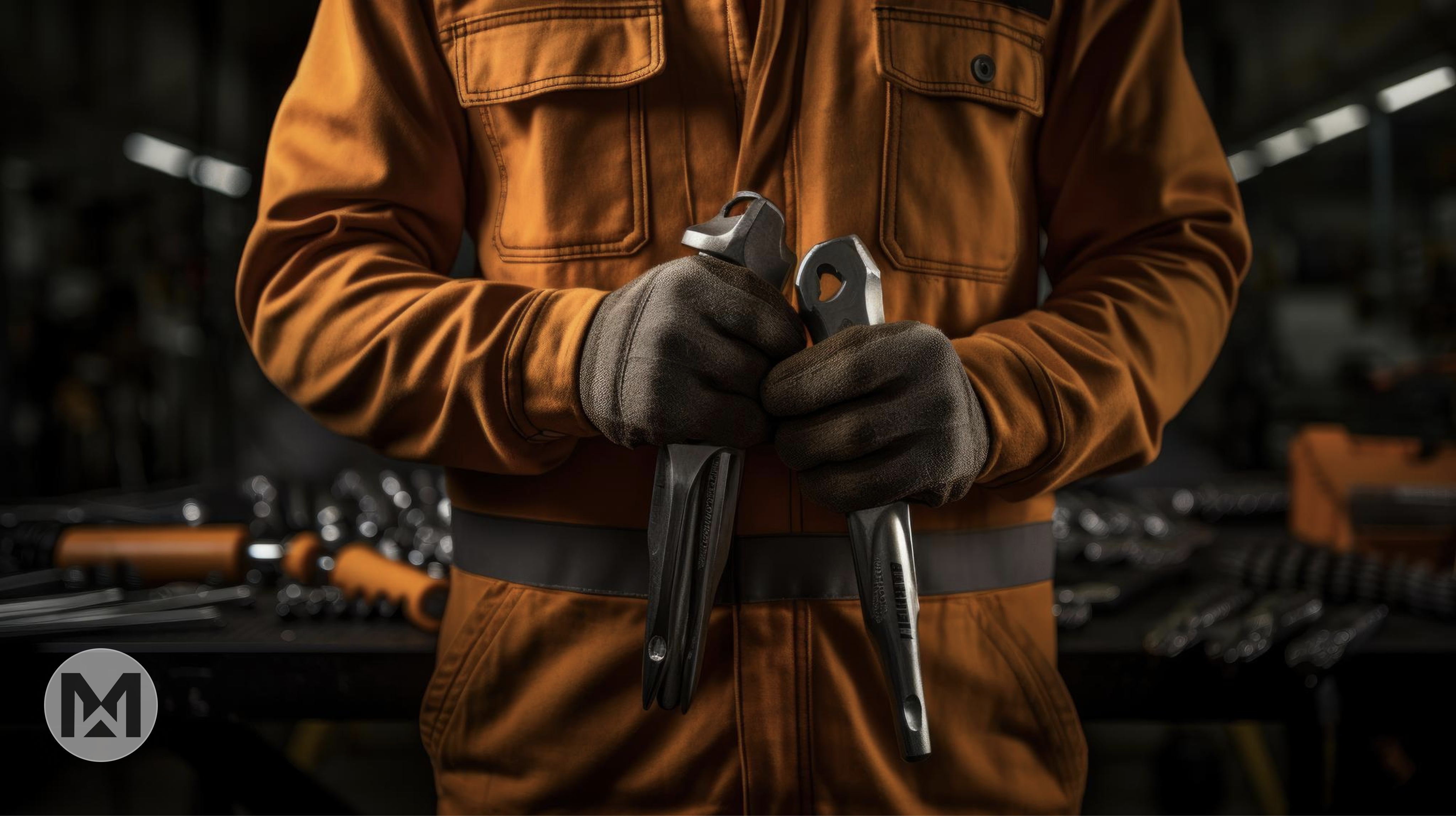
Solution Overview
MaintWiz platform supports multiple clients and managing their asset hierarchy. Inspection, Assessment schedules were configured with task lists and critical metrics were captured. Detailed Equipment history maintained helped in analyzing the equipment better. Calendar functionality and workbench helped in increasing the utilization for the high cost instruments by trimming idle time and better planning. Comprehensive metrics captured helped the experts at Headquarters to assess and provide consulting. Platform also tracked multiple special projects and accounted the resources for proper billing.
Benefits
- Comprehensive view of asset information including history to suggest improvement opportunities
- Efficient usage of high cost instruments used in alignment and plant operations study
- Manage the multiple special projects in a structured way and accounting the resources (time, labour, instrument usage etc)
- Repeatable process and cross-pollinating the project learnings strengthened the practice and business outcomes
Request a one-one demo with our solution engineering team.
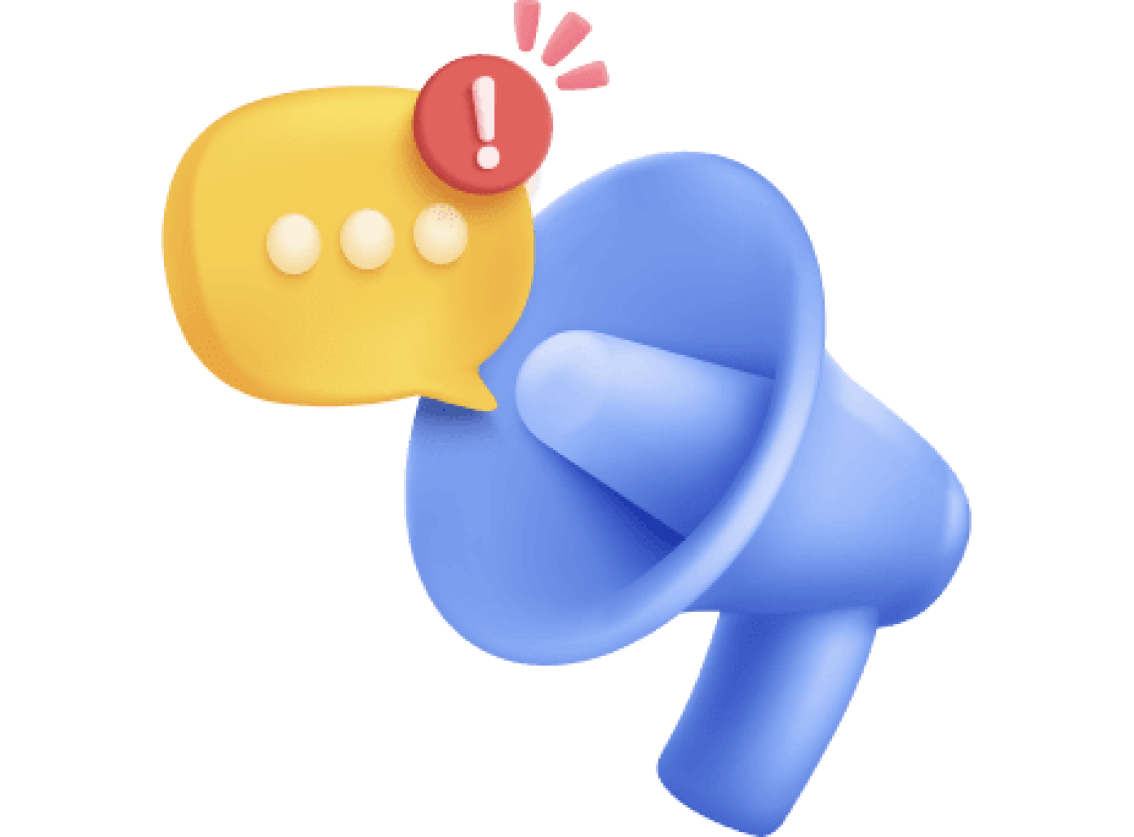
Request a one-one demo with our solution engineering team.