Guide to Effective Preventive Maintenance Checklists
Water Treatment Systems
Table of Contents
ToggleStreamline Your Maintenance: A Guide to Effective Preventive Maintenance Checklists
Introduction
Preventive maintenance (PM) inspections are a critical component of plant maintenance programs. Effective PM inspections can help to reduce maintenance costs, improve equipment reliability and uptime, increase safety for workers and equipment, and improve product quality and customer satisfaction.
In this guide, we will explore the benefits of PM inspections, types of inspections, implementation of PM inspections, factors affecting PM inspections, best practices for PM inspections, common PM inspection mistakes, and the role of maintenance management in effective PM inspections.
Benefits of PM Inspections
PM inspections offer many benefits to plants and facilities, including:
Cost savings through early detection of problems
PM inspections can help to identify equipment problems before they escalate into major issues, reducing maintenance costs and downtime.
Improved equipment reliability and uptime
Regular PM inspections can help to extend the lifespan of equipment and reduce breakdowns, improving reliability and uptime.
Increased safety for workers and equipment
PM inspections can help to identify safety hazards and prevent accidents, protecting workers and equipment from harm.
Improved product quality and customer satisfaction
PM inspections can help to ensure that equipment is operating at peak performance, resulting in higher quality products and greater customer satisfaction.
Types of PM Inspections
Preventative Maintenance (PM) inspections are essential for identifying equipment problems before they become major issues. There are several types of PM inspections that can be used to maintain equipment performance and extend its lifespan:
- Visual inspections:
Visual inspections involve a thorough examination of equipment to identify any visible signs of damage, wear, or corrosion. These inspections can be done regularly by trained employees or third-party contractors to detect issues such as leaks, cracks, or loose components.
- Non-destructive testing:
Non-destructive testing involves the use of specialized equipment to inspect equipment without causing damage. Examples include ultrasonic testing, magnetic particle inspection, and eddy current testing. These tests can identify hidden defects and weaknesses in equipment that may not be visible during visual inspections.
- Vibration analysis:
Vibration analysis involves measuring the vibrations produced by equipment during operation. By analyzing the frequency and intensity of these vibrations, technicians can identify potential issues such as misalignment, unbalance, or worn bearings. This type of inspection can help prevent equipment failure and improve overall performance.
- Oil analysis:
Oil analysis involves testing the quality and condition of lubricating oil in equipment to identify any signs of wear, contamination, or degradation. By analyzing the composition of oil samples, technicians can determine if equipment is functioning properly and identify any potential issues before they become major problems.
- Thermography:
Thermography involves using infrared cameras to detect abnormal temperature variations in equipment. By identifying hot spots or cold spots, technicians can detect issues such as electrical problems, overheating, or blockages. This type of inspection can help prevent equipment failure and improve safety.
Other types of PM inspections:
- Ultrasonic leak detection
- Pressure testing
- Electromagnetic testing
- X-ray testing
- Acoustic emission testing
Implementation of PM Inspections
To implement an effective PM inspection program, follow these steps:
Developing a PM inspection schedule
Create a schedule for PM inspections that takes into account the equipment being inspected, the frequency of inspections, and the resources available for inspections.
Conducting PM inspections effectively
Train personnel to conduct inspections effectively and consistently, using appropriate tools and equipment. Standardize inspection procedures to ensure that inspections are conducted in the same way each time.
Documenting PM inspections for record-keeping
Record the results of PM inspections in a log or database, including information such as the equipment inspected, the date of inspection, and the results of the inspection. Use this information to track trends over time and identify recurring issues.
Monitoring and evaluating the effectiveness of PM inspections
Regularly review the results of PM inspections and use the data to identify areas for improvement. Make adjustments to the inspection program as necessary to optimize results.
Factors Affecting PM Inspections
Several factors can impact the effectiveness of PM inspections:
Environmental factors that affect equipment performance
Environmental factors such as temperature, humidity, and vibration can impact the performance of equipment and affect the accuracy of PM inspections.
Wear and tear due to normal use
Equipment naturally wears down over time, which can impact its performance and make it more difficult to detect problems through PM inspections.
Misuse or abuse of equipment
Improper use or maintenance of equipment can lead to premature failure or breakdowns, making it more difficult to detect problems through PM inspections.
Age of equipment
As equipment ages, it becomes more prone to breakdowns and failures, which can make it more difficult to detect problems through PM inspections.
Impact of operating conditions on equipment
Equipment that operates in harsh conditions such as extreme temperatures or exposure to corrosive materials can be more prone to breakdowns and failures, making it more difficult to detect problems through PM inspections.
Best Practices for PM Inspections
Preventive Maintenance (PM) inspections are crucial to keeping equipment running smoothly and efficiently. Follow these tips and tricks to optimize PM inspection results:
Tips for optimal PM inspection results:
- Perform inspections on a regular basis to catch issues early and prevent downtime.
- Use a checklist to ensure all components are inspected and nothing is missed.
- Document all inspections and repairs to keep a record of maintenance history.
- Train employees on proper inspection techniques to ensure consistency and accuracy.
- Utilize technology such as sensors and monitoring systems to track equipment performance and identify potential issues.
Importance of regular maintenance:
Regular maintenance is essential to prevent equipment failure and avoid costly repairs. By performing regular PM inspections, you can catch issues before they become major problems, resulting in less downtime and increased productivity. In addition, regular maintenance can extend the lifespan of equipment and prevent the need for premature replacement.
Other important factors to consider during PM inspections:
- Ensure all safety protocols are followed during inspections to prevent accidents and injuries.
- Check for any abnormal sounds, vibrations, or odors that could indicate a problem.
- Clean and lubricate all components to prevent wear and tear.
- Replace worn or damaged parts immediately to prevent further damage and potential safety hazards.
- Consult manufacturer recommendations and guidelines for maintenance schedules and procedures.
Common PM Inspection Mistakes
Avoid these common PM inspection mistakes:
Not conducting inspections frequently enough
Infrequent inspections can lead to missed problems and potential equipment failures.
Inadequate inspection procedures
Inspections that are not standardized or consistent can lead to missed problems and inaccurate results.
Failure to document inspections and results
Failure to document inspections and results can make it difficult to track trends over time and identify recurring issues.
Failure to act on inspection findings in a timely manner
Ignoring inspection findings can lead to equipment failures and safety hazards.
Lack of proper training for inspection personnel
Personnel who are not properly trained in PM inspections may not be able to detect problems accurately or effectively.
Maintenance Management
Maintenance management plays a critical role in effective PM inspections:
Role of maintenance management in effective PM inspections
Maintenance management is responsible for developing and implementing a PM inspection program, ensuring that inspections are conducted effectively and efficiently, and monitoring the results of inspections.
Maintenance management software
Software tools can be used to manage and track PM inspections, making it easier to schedule inspections, track results, and identify trends over time.
Key performance indicators for maintenance management
Maintenance management can use key performance indicators such as mean time between failures (MTBF), mean time to repair (MTTR), and Overall Equipment Effectiveness (OEE) to monitor the effectiveness of PM inspections and identify areas for improvement.
Effective PM inspections are a critical component of plant maintenance programs. By following best practices for PM inspections and avoiding common mistakes, plants and facilities can reduce maintenance costs, improve equipment reliability and uptime, increase safety for workers and equipment, and improve product quality and customer satisfaction.
Request a one-one demo with our solution engineering team.
Request a one-one demo with our solution engineering team.
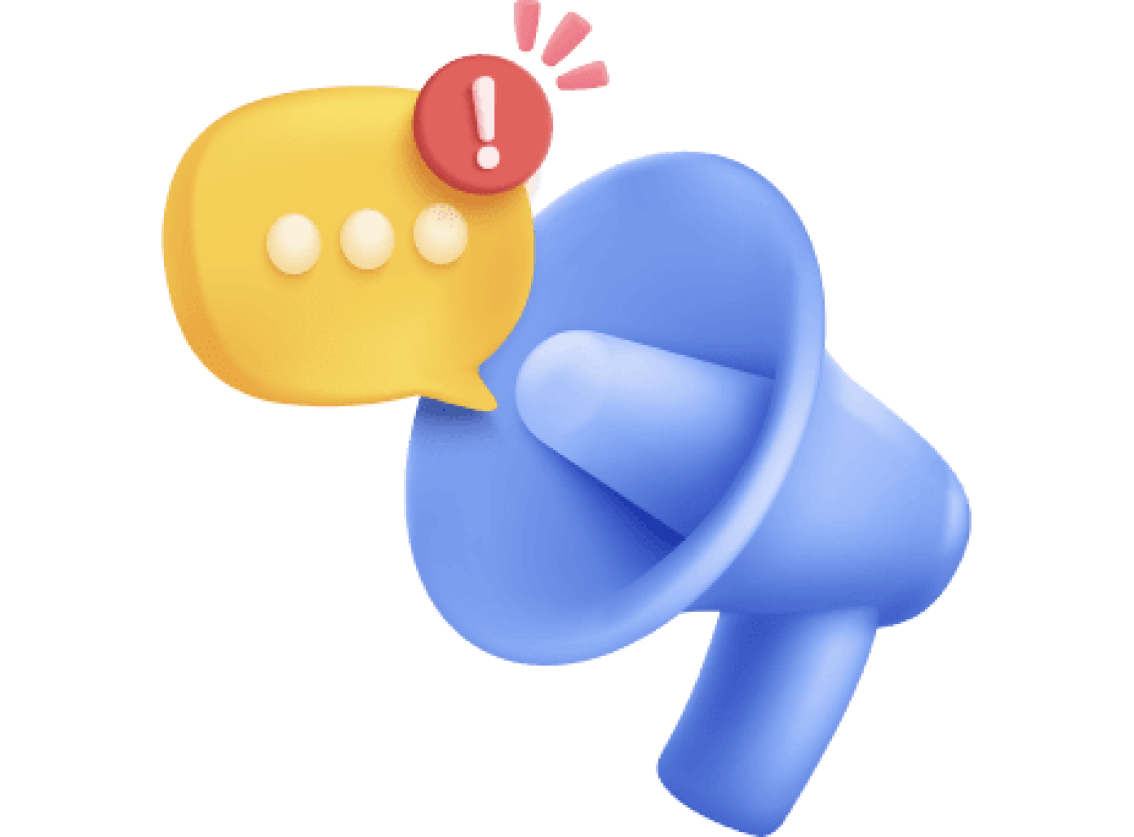