Transform Manufacturing Excellence Through TPM Focused Improvement (Kobetsu Kaizen)
Revolutionize your TPM implementation with MaintWiz CMMS's advanced Focused Improvement capabilities. Drive breakthrough results in equipment effectiveness while significantly reducing maintenance costs and improving operational reliability.
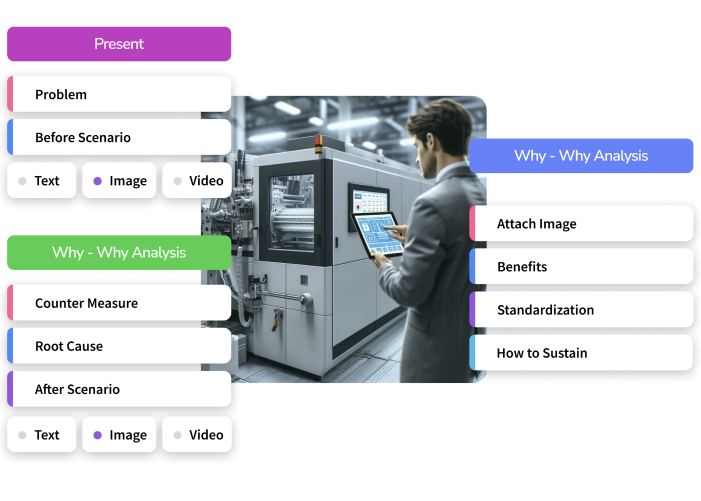
Comprehensive Downtime Management for Breakthrough Performance
Unlock hidden manufacturing capacity and maximize equipment effectiveness through data-driven insights and automated workflows that eliminate chronic losses.
Advanced Root Cause Analysis Engine Powers Systematic Loss Elimination
Transform recurring equipment issues into opportunities for permanent improvement. MaintWiz’s intelligent RCA module identifies underlying causes through structured analysis, enabling targeted countermeasures that prevent future failures and optimize maintenance strategies.
Real-time Performance Monitoring Drives Proactive Interventions
Leverage IoT integration to capture equipment data in real-time, enabling immediate maintenance response. Dynamic dashboards visualize performance trends, helping teams identify degradation patterns before they impact production efficiency.
Automated Downtime Classification and Analysis
Eliminate manual logging errors with intelligent downtime capture systems. MaintWiz’s algorithms categorize stops, calculate impact metrics, and trigger appropriate maintenance responses, ensuring critical events receive immediate attention.
Strategic KPI Tracking for World-Class Performance
Set and monitor improvement targets with customizable KPI dashboards. Benchmark performance across equipment and facilities, identifying best practices and improvement opportunities that accelerate operational excellence initiatives.
Machine Learning-Powered Failure Pattern Detection
Harness advanced algorithms to identify subtle patterns in equipment behavior. Early warning indicators trigger preventive actions, helping maintenance teams optimize intervention timing and prevent unexpected failures.
Cross-functional Digital Collaboration Platform
Break down operational silos between maintenance, production, and engineering teams. MaintWiz’s integrated platform ensures all stakeholders work together effectively, accelerating problem-solving and improvement initiatives.
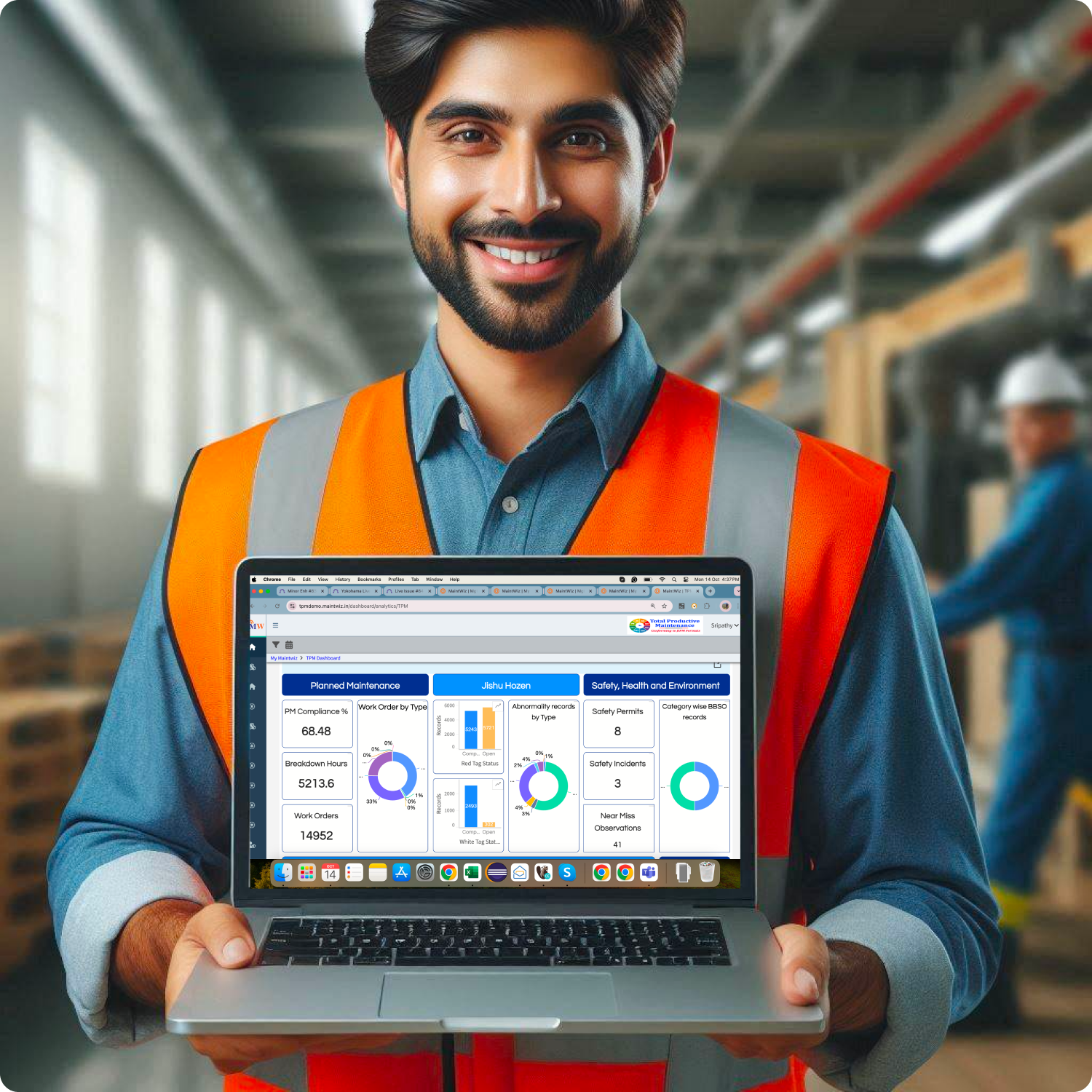
AI-Powered Maintenance Scheduling Optimization
Revolutionize maintenance effectiveness while minimizing production impact through intelligent scheduling and resource allocation.
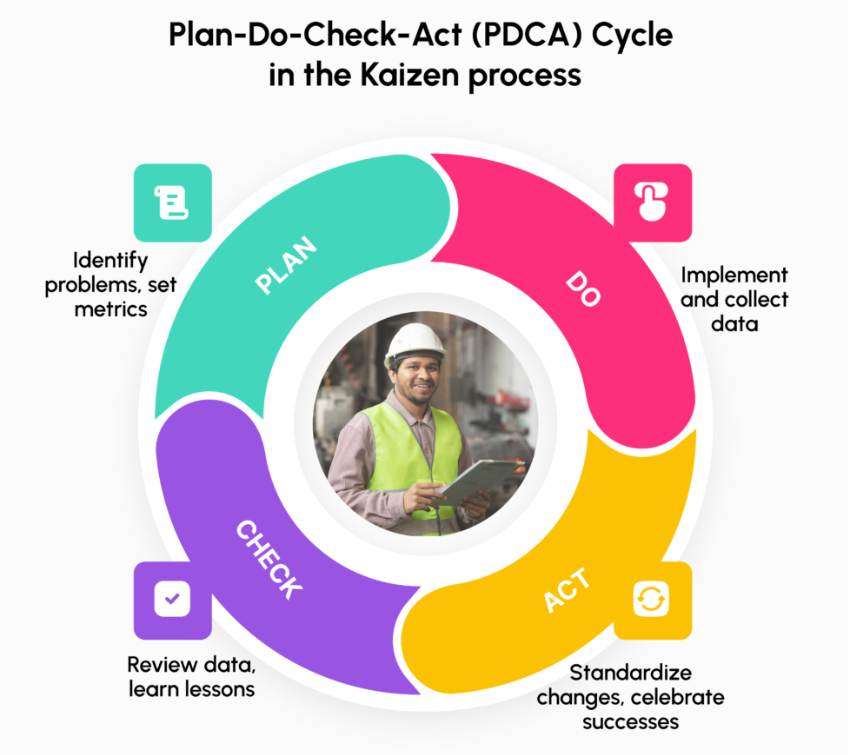
Predictive Analytics for Optimal Maintenance Timing
Leverage machine learning algorithms to predict ideal maintenance windows. MaintWiz analyzes equipment condition, production schedules, and resource availability to recommend interventions that maximize operational uptime.
Production-Synchronized Maintenance Planning
Seamlessly align maintenance activities with production demands. Smart scheduling ensures critical tasks are completed during planned downtimes, minimizing impact on production targets and improving overall efficiency.
Intelligent Resource Optimization Engine
Maximize maintenance team effectiveness with AI-powered resource allocation. MaintWiz matches technician capabilities with task requirements, ensuring efficient execution while supporting continuous skill development.
Dynamic Preventive Maintenance Scheduling
Transform traditional time-based maintenance into condition-based strategies. Advanced analytics optimize PM frequencies, eliminating unnecessary interventions while ensuring equipment reliability and performance.
Predictive Parts Requirements Planning
Eliminate maintenance delays with intelligent parts forecasting. MaintWiz predicts spare parts needs based on maintenance schedules and historical patterns, ensuring critical components are available when needed.
Automated Workload Distribution System
Maintain optimal team utilization through smart workload balancing. Intelligent algorithms distribute tasks effectively, preventing resource overload while ensuring timely completion of critical maintenance activities.
Speak to a Specialist
Get personalised advice from our experts
Integrated Safety Protocol Management
Enhance workplace safety while improving maintenance effectiveness through seamless integration of safety protocols with maintenance activities.
Safety-First Maintenance Procedure Integration
Ensure compliance with safety standards in every maintenance activity. Digital checklists and procedures guide technicians through required safety protocols, reducing risks and preventing accidents.
Automated Regulatory Compliance Tracking
Stay ahead of safety regulations with automated compliance monitoring. MaintWiz tracks regulatory requirements, schedules necessary inspections, and maintains comprehensive documentation for audit readiness.
Risk-Based Equipment Safety Assessment
Identify and prioritize equipment safety risks systematically. Advanced risk assessment tools help prioritize maintenance activities based on safety impact, ensuring critical safety issues receive immediate attention.
Digital Safety Training Management
Enhance maintenance team safety awareness through integrated training modules. Track certification requirements, schedule refresher courses, and maintain comprehensive training records for compliance purposes.
Real-time Safety Alert System
Prevent safety incidents with immediate hazard notifications. MaintWiz’s alert system immediately notifies relevant personnel of potential safety risks, enabling quick response to emerging safety concerns.
Comprehensive Safety Documentation Hub
Maintain complete safety records with automated documentation. Digital storage of safety procedures, incident reports, and corrective actions ensures easy access to critical safety information when needed.
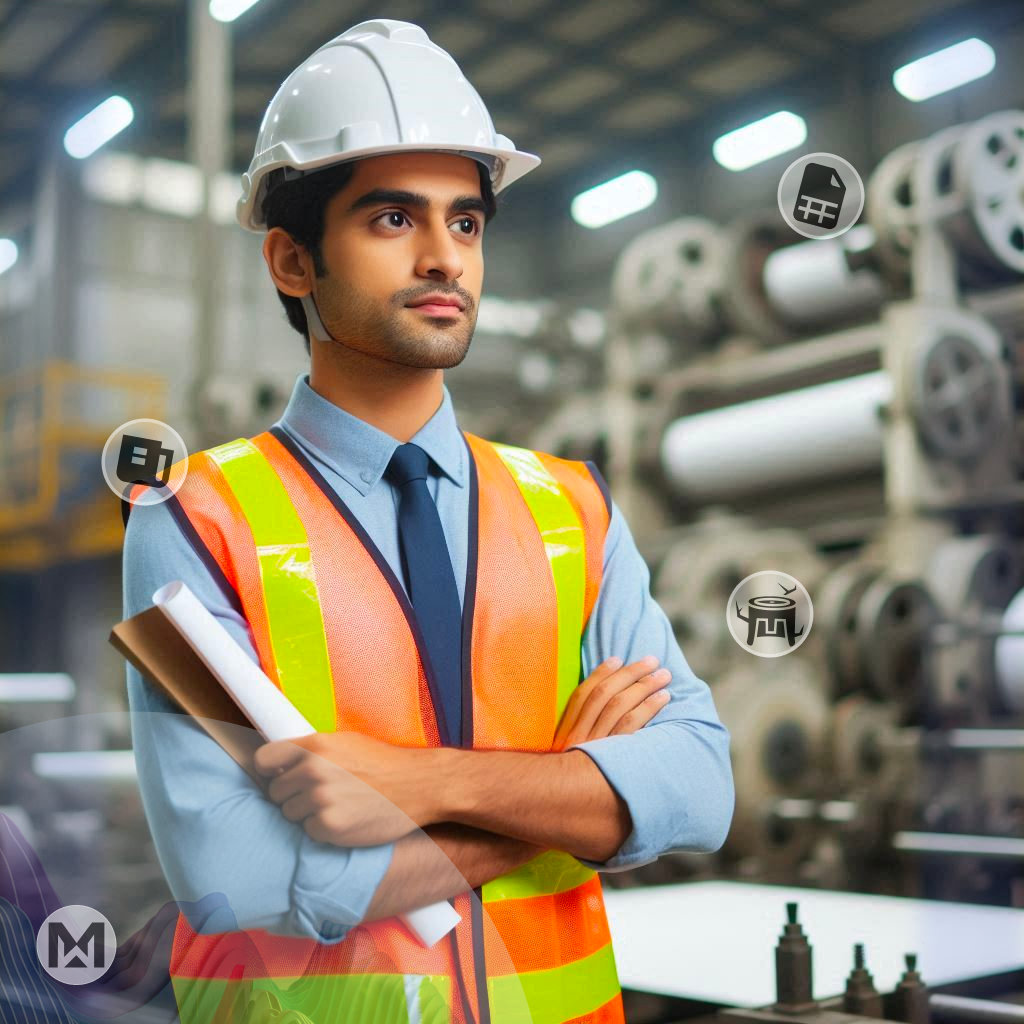
Intelligent Resource and Inventory Management
Optimize maintenance resources and spare parts inventory through data-driven decision making and automated control systems.
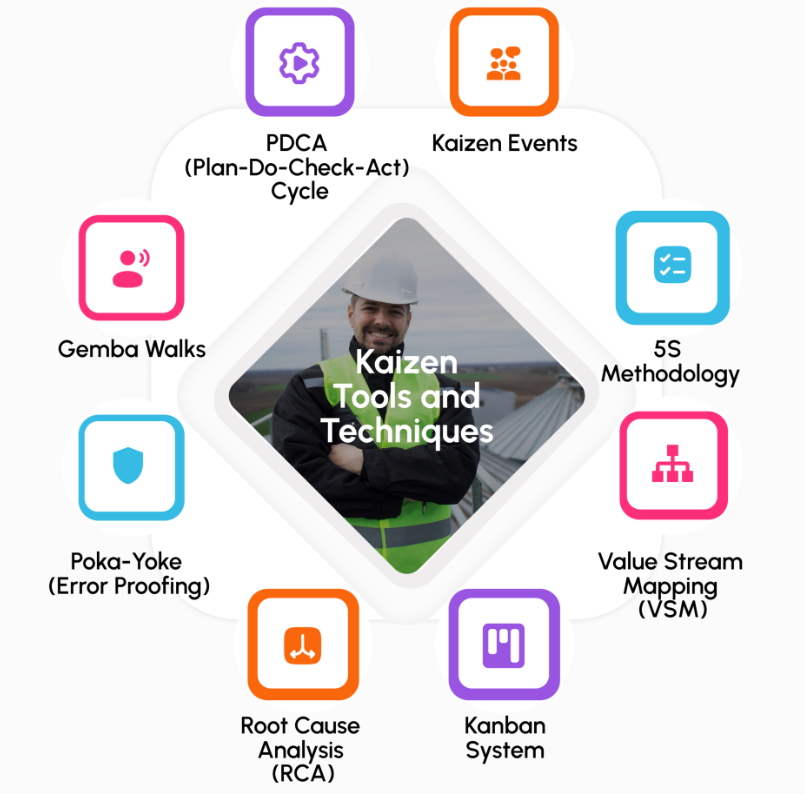
Advanced Spare Parts Inventory Optimization
Minimize inventory costs while ensuring parts availability. Smart algorithms analyze usage patterns and lead times to maintain optimal inventory levels, reducing carrying costs without compromising maintenance effectiveness.
Predictive Demand Forecasting System
Anticipate spare parts requirements before they arise. Machine learning models analyze historical data and maintenance schedules to predict future parts needs, preventing stockouts and reducing emergency purchases.
Automated Cost Tracking and Analysis
Monitor and control maintenance costs effectively. Comprehensive cost tracking systems analyze expenditure patterns, identifying opportunities for cost reduction while maintaining equipment reliability.
Integrated Supplier Management Portal
Streamline procurement processes with automated supplier integration. Digital collaboration tools facilitate efficient communication with vendors, ensuring timely delivery of critical parts and materials.
Smart Inventory Level Management
Prevent overstocking and stockouts through intelligent inventory control. Automated reorder points and dynamic safety stock calculations optimize inventory investments while ensuring parts availability.
Digital Procurement Workflow Automation
Accelerate procurement cycles with automated workflows. Streamlined approval processes and digital purchase orders reduce administrative overhead and expedite parts acquisition when needed.
Quality-Focused Performance Optimization
Drive continuous quality improvement through integrated maintenance and quality management capabilities.
Maintenance-Quality Impact Analysis
Understand how maintenance activities affect product quality. Advanced analytics correlate maintenance actions with quality metrics, enabling targeted improvements that enhance both equipment reliability and product quality.
Real-time Quality Parameter Monitoring
Track critical quality parameters continuously. IoT integration enables immediate detection of quality deviations, allowing rapid maintenance response to prevent quality issues.
Quality Improvement Project Tracking
Manage quality improvement initiatives effectively. Digital project management tools help track improvement activities, measure outcomes, and document best practices for sustained quality enhancement.
Automated Quality Data Collection
Eliminate manual quality data entry errors. Automated data collection systems ensure accurate quality information, enabling reliable analysis and effective decision-making for maintenance planning.
Predictive Quality Analysis Engine
Anticipate potential quality issues before they occur. Machine learning algorithms analyze equipment conditions and process parameters to predict quality risks, enabling preventive maintenance interventions.
Quality Cost Optimization System
Reduce quality-related costs through targeted maintenance. Cost analysis tools help identify and prioritize maintenance activities that deliver the greatest impact on quality improvement.
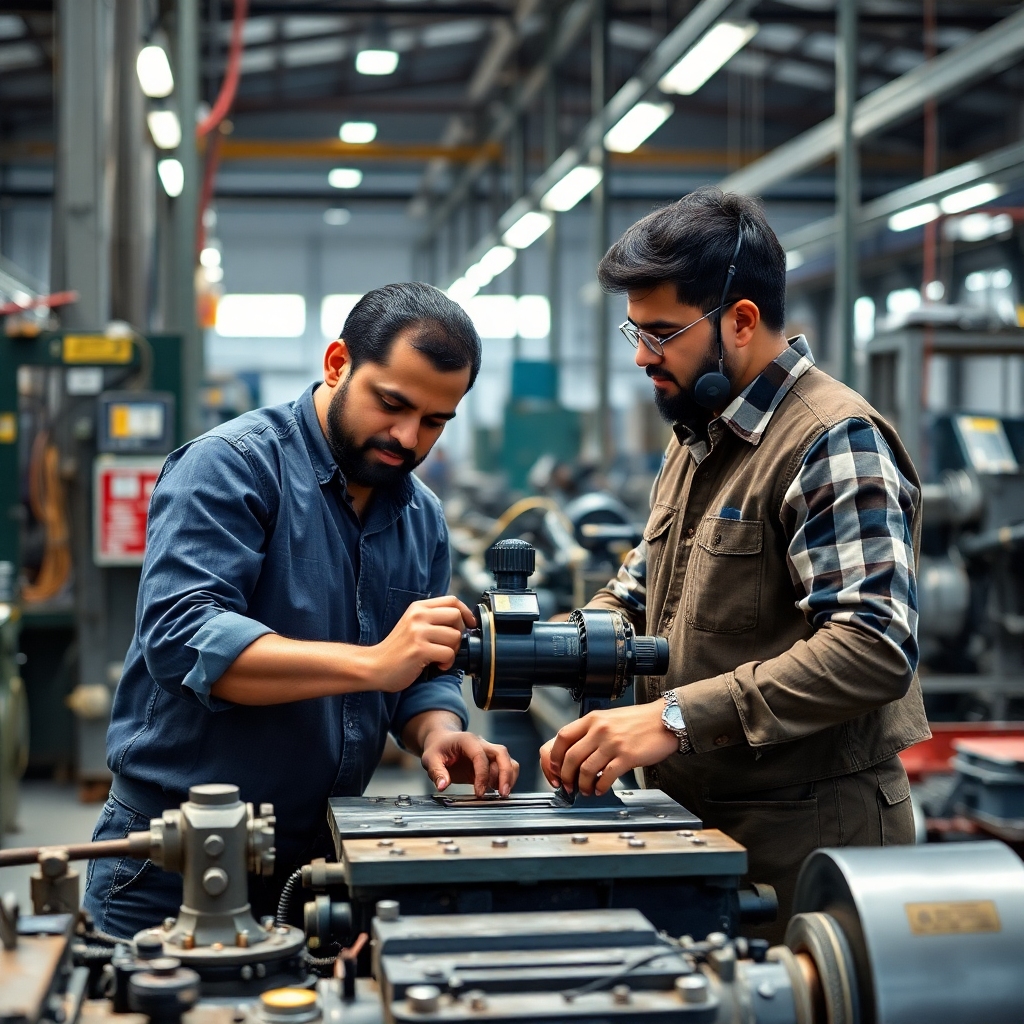
Voices of Our Valued Clients
MaintWiz’s Office TPM system has optimized administrative tasks, improving our overall organizational flow
With MaintWiz, Office TPM has transformed how we manage day-to-day activities, boosting efficiency
MaintWiz has taken Office TPM to new heights, improving administrative processes and support
With MaintWiz’s office TPM solutions, our back-office processes now align with shop-floor productivity
MaintWiz’s Office TPM tools have streamlined administrative functions, freeing up time for production.
MaintWiz helps us apply TPM principles beyond the shop floor, driving efficiency across the office.
Office TPM with MaintWiz has reduced paperwork, saving time and enhancing overall office productivity
By implementing Office TPM with MaintWiz, we’ve achieved smoother workflows across departments.
MaintWiz’s Office TPM system has optimized administrative tasks, improving our overall organizational flow
With MaintWiz, Office TPM has transformed how we manage day-to-day activities, boosting efficiency
MaintWiz has taken Office TPM to new heights, improving administrative processes and support
With MaintWiz’s office TPM solutions, our back-office processes now align with shop-floor productivity
Strategic Equipment Improvement Program
Drive systematic equipment performance enhancement through focused improvement initiatives and data-driven decision making.
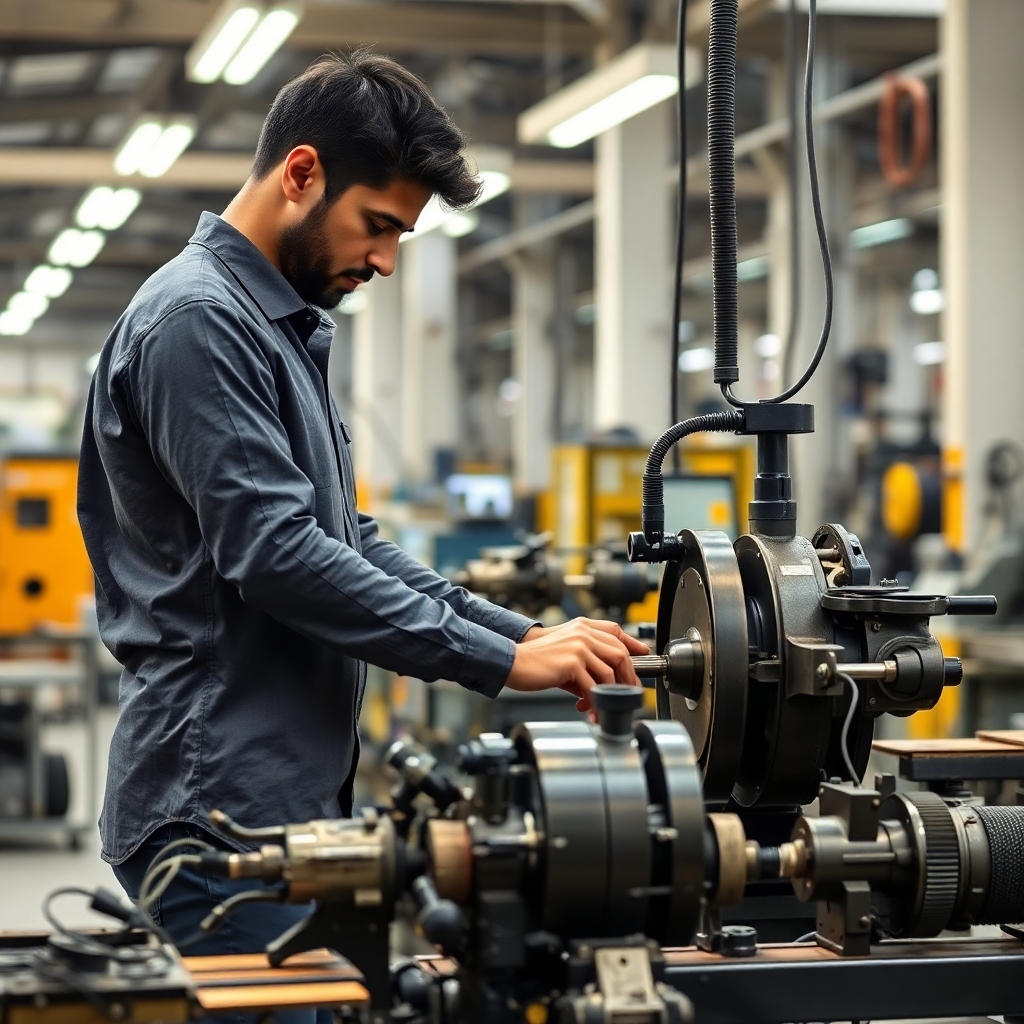
High-Impact Improvement Area Identification
Target improvement efforts where they matter most. Advanced analytics identify critical equipment and processes with the greatest potential for performance improvement, ensuring optimal resource allocation.
Performance Goal Setting and Tracking
Set and monitor ambitious improvement targets. Digital performance tracking systems help establish realistic goals, measure progress, and adjust strategies based on actual results.
Project Effectiveness Monitoring System
Ensure improvement initiatives deliver expected results. Comprehensive monitoring tools track project outcomes, validate effectiveness, and identify opportunities for further enhancement.
Task Prioritization Intelligence
Focus maintenance efforts where they deliver maximum impact. Smart prioritization algorithms analyze multiple factors to identify critical tasks, ensuring resources are allocated to the most important activities.
Maintenance Backlog Reduction Engine
Systematically reduce maintenance backlogs. Intelligent scheduling and resource allocation tools help tackle outstanding maintenance tasks efficiently while preventing new backlog accumulation.
Continuous Process Enhancement Tools
Enable ongoing equipment performance improvement. Digital tools support systematic analysis and implementation of enhancement opportunities, driving continuous operational excellence.
Request a one-one demo with our solution engineering team.
Request a one-one demo with our solution engineering team.
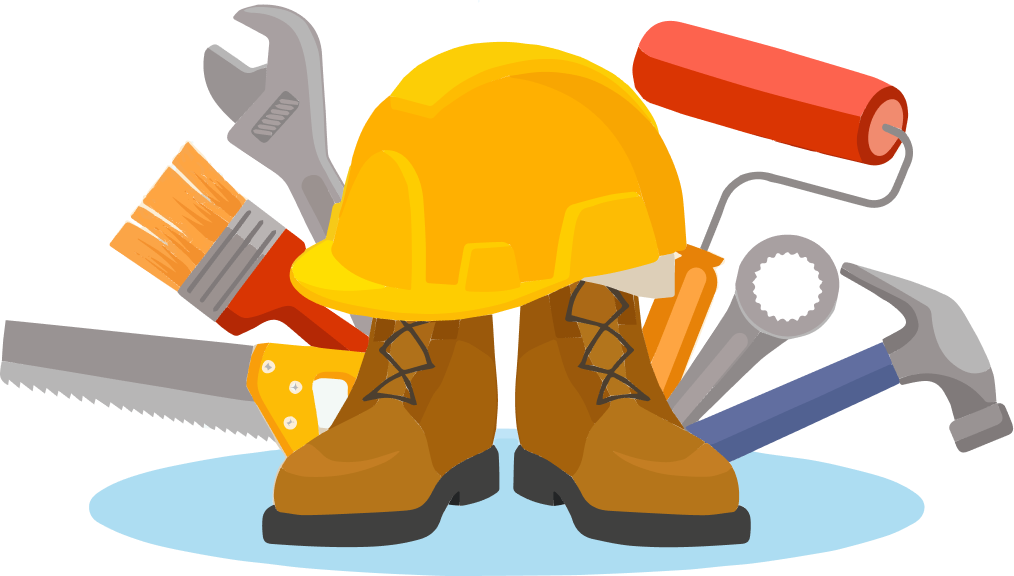