Preventive Maintenance Program
for Chillers
Preventive Maintenance Program for Chillers
The Complete Guide to Defining Your Preventive Maintenance Program for Chillers
Table of Contents
Toggle1. Introduction to Preventive Maintenance for Chillers
Preventive maintenance is essential for the smooth operation of industrial equipment and machinery, including chillers. A preventive maintenance program aims to prevent the occurrence of breakdowns and unplanned downtime, extending the lifespan of the equipment and reducing maintenance costs.
Overview Preventive Maintenance for Chillers
Preventive maintenance for chillers involves performing regular inspections, cleaning, lubrication, and testing procedures to ensure that the equipment is operating correctly. The goal is to identify and repair any issues before they become more significant problems, leading to breakdowns and downtime.
Importance of Preventive Maintenance for Chillers
The importance of preventive maintenance for chillers cannot be overstated. Regular maintenance can help prevent costly breakdowns, reduce energy consumption, extend the lifespan of the equipment, and improve safety for maintenance technicians and other employees.
Sub-assemblies and Components of Chillers
Chillers are complex pieces of equipment that consist of several sub-assemblies and components. These include compressors, evaporators, condensers, tubes, motors, and more. Understanding the various parts of the chiller is essential to develop an effective preventive maintenance program.
2. Components of a Preventive Maintenance Plan for Chillers
Developing a preventive maintenance plan involves creating a list of scheduled inspections and maintenance tasks, determining the recommended frequency of each task, and recording and tracking all maintenance activities.
Scheduled inspections and maintenance tasks
Scheduled inspections and maintenance tasks include cleaning, lubrication, testing, and other procedures that help ensure that the chiller is functioning correctly. These tasks should be scheduled at regular intervals to prevent issues from arising.
Recommended frequency of inspections and maintenance tasks
The frequency of inspections and maintenance tasks will depend on various factors, including the age of the equipment, operating conditions, and past failure history. Consulting the manufacturer’s recommendations and conducting a risk assessment can help determine the appropriate frequency of tasks.
Recording and tracking maintenance activities
Recording and tracking maintenance activities is essential to ensure that all tasks are completed on time, and any issues are addressed promptly. A computerized maintenance management system (CMMS) can help keep track of maintenance activities and schedule future tasks.
3. Benefits of Preventive Maintenance for Chillers
Preventive maintenance offers several benefits for chillers, including:
Extended lifespan of the equipment
Regular maintenance can help extend the lifespan of the equipment, reducing the need for costly replacements and repairs.
Reduced maintenance costs
Preventive maintenance can help identify and repair issues before they become more significant problems, reducing the need for expensive repairs and downtime.
Improved energy efficiency
Regular maintenance can help improve the energy efficiency of the chiller, reducing energy consumption and costs.
Improved safety
Preventive maintenance can help identify and address safety issues before they become more significant problems, improving safety for maintenance technicians and other employees.
Improved equipment performance
Regular maintenance can help ensure that the chiller is functioning correctly, improving its overall performance and reducing the risk of breakdowns.
4. Tools and Techniques for Preventive Maintenance for Chillers
There are several tools and techniques that maintenance technicians can use to perform preventive maintenance on chillers. These include cleaning and lubrication methods, inspection and testing procedures, repair and replacement guidelines, and condition monitoring techniques.
Cleaning and Lubrication Methods
Cleaning and lubrication are essential maintenance tasks that help ensure the smooth operation of chillers. Cleaning methods include pressure washing, chemical cleaning, and water treatment. Lubrication methods include oiling, greasing, and adding coolant.
Inspection and Testing Procedures
Inspection and testing procedures involve visually inspecting various parts of the chiller and testing its performance. These procedures include compressor inspection, evaporator inspection, condenser inspection, tube inspection, and motor inspection.
Repair and Replacement Guidelines
Repair and replacement guidelines involve identifying issues with the chiller and determining whether they can be repaired or require replacement. Guidelines for repairing and replacing components include consulting the manufacturer’s recommendations and conducting a risk assessment.
Condition Monitoring Techniques
Condition monitoring techniques involve using sensors and other tools to monitor the condition of the chiller and identify potential issues. These techniques include vibration analysis, oil analysis, and thermal imaging.
5. Developing a Preventive Maintenance Program for Chillers
Developing a successful preventive maintenance program for chillers involves identifying critical equipment, researching OEM manuals and recommendations, factoring in operational conditions, establishing maintenance schedules and tasks, and developing a system for tracking and recording maintenance activities.
Identifying critical Chillers and equipment
Identifying critical chillers and equipment involves determining which equipment is essential to the operation of the facility and prioritizing its maintenance.
Researching OEM Manuals and recommendations
Researching OEM manuals and recommendations can help determine the appropriate maintenance tasks, frequencies, and techniques for the chiller.
Factoring Operational Conditions
Factoring in operational conditions, including the age of the equipment, operating conditions, and past failure history, can help determine the appropriate frequency of maintenance tasks.
Establishing maintenance schedules and tasks
Establishing maintenance schedules and tasks involves creating a list of scheduled inspections and maintenance tasks, determining the recommended frequency of each task, and recording and tracking all maintenance activities.
Developing a system for tracking and recording maintenance activities
Developing a system for tracking and recording maintenance activities is essential to ensure that all tasks are completed on time, and any issues are addressed promptly. A computerized maintenance management system (CMMS) can help keep track of maintenance activities and schedule future tasks.
6. Preventive Maintenance for Specific Chiller Types
There are several types of chillers, including air-cooled, water-cooled, absorption, and centrifugal. Each type of chiller requires specific preventive maintenance activities to ensure that it operates correctly.
Types of Chillers
Types of chillers include air-cooled, water-cooled, absorption, centrifugal, and more. Each type of chiller requires specific maintenance activities.
Preventive Maintenance Activities
Preventive maintenance activities for each type of chiller include specific tasks, such as cleaning the condenser, inspecting the compressor, and testing the refrigerant levels.
7. Best Practices for Preventive Maintenance for Chillers
Following best practices for preventive maintenance can help ensure that chillers operate correctly and efficiently. These best practices include regular inspections and cleaning, proper lubrication and fluid levels, and monitoring and analyzing chiller performance data.
Regular inspections and cleaning
Regular inspections and cleaning are essential to prevent the buildup of debris and dirt, which can reduce the chiller’s efficiency.
Proper lubrication and fluid levels
Proper lubrication and fluid levels are essential to ensure that the chiller’s moving parts operate smoothly.
Monitoring and analyzing chiller performance data
Monitoring and analyzing chiller performance data can help identify potential issues and opportunities for improvement.
8. Measuring the Efficiency of Preventive Maintenance for Chillers
Measuring the efficiency of preventive maintenance for chillers involves determining key performance indicators (KPIs) that can help assess the effectiveness of the maintenance program. KPIs can include measures such as uptime, energy consumption, and maintenance costs.
Key Performance Indicators
Key performance indicators for preventive maintenance for chillers can include measures such as uptime, energy consumption, maintenance costs, and mean time between failures.
9. Role of CMMS
A computerized maintenance management system (CMMS) can help improve the effectiveness of a preventive maintenance program for chillers by providing features such as master data management, equipment history, preventive maintenance scheduling and tracking, operational technology integration, and KPI monitoring.
Master Data Management
Master data management involves creating a centralized database of all equipment, maintenance tasks, and maintenance activities, allowing for easier tracking and management.
Equipment History
Equipment history involves recording all maintenance activities and repairs, providing a comprehensive record of the equipment’s maintenance history.
Preventive Maintenance Scheduling and Tracking
Preventive maintenance scheduling and tracking involve creating a schedule of maintenance tasks and tracking their completion.
Operational Technology Integration and Condition Based Maintenance
Operational technology integration and condition-based maintenance involve using sensors and other technology to monitor the equipment’s condition and schedule maintenance tasks based on that data.
KPIs Monitoring
KPIs monitoring involves tracking and analyzing key performance indicators to assess the effectiveness of the preventive maintenance program.
10. Conclusion
Developing a preventive maintenance program for chillers is essential to ensure that they operate correctly, efficiently, and safely. By following the best practices outlined in this guide, maintenance technicians can create an effective preventive maintenance program that reduces maintenance costs, extends the lifespan of the equipment, and improves overall performance. By using a CMMS and monitoring KPIs, maintenance technicians can continue to refine and improve the program over time.
Request a one-one demo with our solution engineering team.
Request a one-one demo with our solution engineering team.
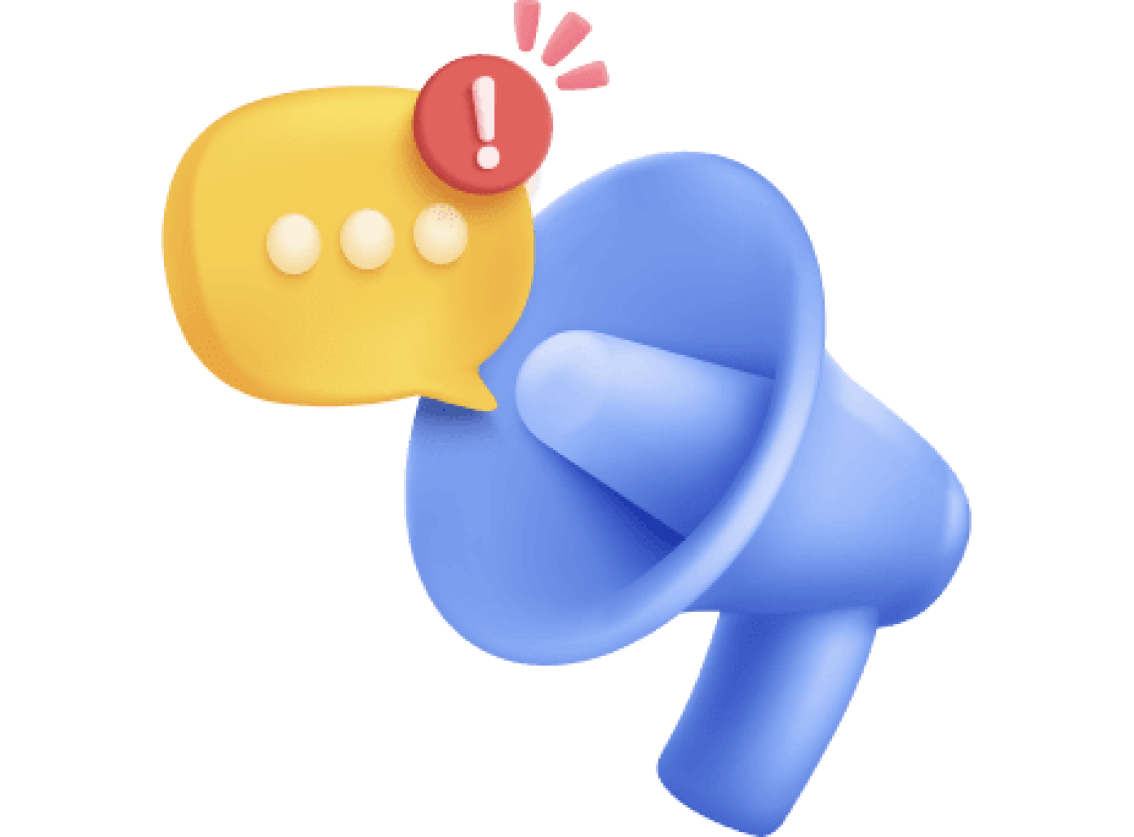