Preventive Maintenance Program for Boilers
Preventive Maintenance Program for Boilers
The Complete Guide to Defining Your Preventive Maintenance Program for Boilers
Table of Contents
ToggleIf you own or operate a boiler, you know how important it is to keep it running smoothly. Regular maintenance is essential to ensure optimal performance, reliability, and safety. In this guide, we will discuss the key aspects of developing a preventive maintenance plan for boilers. You will learn about the benefits of preventive maintenance, the components of a maintenance plan, tools and techniques for maintenance, and best practices for ensuring maximum efficiency.
1. Introduction to Preventive Maintenance for Boilers
Overview Preventive Maintenance for Boilers
Preventive maintenance is a proactive approach to maintaining equipment before problems occur. It involves regular inspections, cleaning, lubrication, testing, and repair or replacement of components. Preventive maintenance helps to minimize downtime, reduce repair costs, and increase the lifespan of equipment.
Importance of Preventive Maintenance for Boilers
Preventive maintenance is critical for boilers as they operate under high temperature and pressure, making them prone to wear and tear. A well-planned preventive maintenance program can help to identify and address potential issues before they turn into major problems. This ensures that the boiler runs safely, reliably, and efficiently.
Sub-assemblies and Components of Boilers
Boilers are complex systems with many sub-assemblies and components. Some of the key components include the burner, combustion chamber, heat exchanger, boiler tubes, and control system. Each of these components requires specific maintenance tasks to ensure optimal performance and safety.
2. Components of a Preventive Maintenance Plan for Boilers
Scheduled inspections and maintenance tasks
A preventive maintenance plan should include regular inspections and maintenance tasks, such as cleaning, lubrication, testing, and repair or replacement of components. The frequency of inspections and maintenance tasks should be based on the manufacturer’s recommendations, operational conditions, and past failure history.
Recommended frequency of inspections and maintenance tasks
The frequency of inspections and maintenance tasks will vary depending on the type of boiler, its age, and operating conditions. For example, a high-pressure steam boiler may require daily inspections, while a low-pressure hot water boiler may require monthly inspections. The manufacturer’s recommendations should always be followed.
Recording and tracking maintenance activities
A preventive maintenance plan should include a system for recording and tracking maintenance activities. This can be done manually or with the help of computerized maintenance management software (CMMS). Recording and tracking maintenance activities can help to identify trends, track costs, and ensure that maintenance tasks are being performed on schedule.
Benefits of Preventive Maintenance for Boilers
Improved reliability
Preventive maintenance can help to identify potential issues before they cause a breakdown. This helps to reduce the likelihood of unplanned downtime, which can be costly and disruptive to operations.
Increased safety
Regular maintenance can help to ensure that the boiler is operating safely. This can include checking safety valves, inspecting electrical connections, and testing the control system.
Extended lifespan of equipment
Preventive maintenance can help to extend the lifespan of the boiler and its components. By identifying and addressing potential issues before they cause damage, the boiler can continue to operate effectively for many years.
Improved energy efficiency
A well-maintained boiler can operate more efficiently, which can lead to cost savings on fuel and energy. Regular cleaning, lubrication, and adjustment of components can help to optimize performance and reduce energy consumption.
Reduced repair costs
Preventive maintenance can help to identify and address potential issues before they cause major damage. This can help to reduce the cost of repairs and minimize downtime.
3. Tools and Techniques for Preventive Maintenance for Boilers
Cleaning and Lubrication Methods
Chemical cleaning
- Removes scale, rust, and other deposits from the boiler
- Helps to improve heat transfer and reduce fuel consumption
- Should be performed by a trained technician
Manual cleaning
- Removes dirt, debris, and other contaminants from the boiler
- Helps to prevent corrosion and improve heat transfer
- Should be performed regularly by maintenance personnel
Lubrication
- Ensures that moving parts operate smoothly and efficiently
- Helps to reduce wear and tear on components
- Should be performed regularly using manufacturer-recommended lubricants
Inspection and Testing Procedures
Visual inspection
- Checks for signs of wear, damage, or corrosion
- Should be performed regularly by maintenance personnel
Non-destructive testing
- Uses methods such as ultrasonic testing, radiography, and magnetic particle testing to identify potential issues
- Should be performed by trained technicians
Performance testing
- Checks the boiler’s performance, such as fuel consumption, steam production, and emissions
- Should be performed by trained technicians using specialized equipment
4. Repair and Replacement Guidelines
Component replacement
- Identifies components that have reached the end of their lifespan and need to be replaced
- Should be performed according to the manufacturer’s recommendations
Component repair
- Identifies components that can be repaired instead of replaced
- Should be performed by trained technicians using proper procedures and equipment
Emergency repair procedures
- Defines procedures for emergency repairs, such as in the event of a breakdown or failure
- Should be established in advance to minimize downtime and ensure safety
Condition Monitoring Techniques
Vibration analysis
- Monitors vibration levels to detect potential issues with components
- Can help to identify misalignment, bearing wear, and other problems
Thermography
- Uses infrared technology to detect temperature changes in components
- Can help to identify hotspots, insulation issues, and other problems
Oil analysis
- Tests the condition of lubricating oil to identify potential issues
- Can help to detect contaminants, wear particles, and other problems
Ultrasonic testing
- Uses high-frequency sound waves to detect flaws or defects in components
- Can help to identify cracks, leaks, and other issues
Boiler water analysis
- Tests the quality of boiler water to identify potential issues
- Can help to detect scaling, corrosion, and other problems
5. Developing a Preventive Maintenance Program for Boilers
Identifying critical Boilers and equipment
The first step in developing a preventive maintenance program for boilers is to identify critical equipment. This includes boilers that are essential to operations and those that are prone to failure or have a high cost of repair.
Researching OEM Manuals and recommendations
The manufacturer’s manuals and recommendations should be used as a basis for developing a preventive maintenance program. These provide guidance on recommended maintenance tasks, frequencies, and procedures.
Factoring Operational Conditions
The age of the equipment, operating conditions, and past failure history should be considered when developing a preventive maintenance program. This can help to identify potential issues and prioritize maintenance tasks.
Establishing maintenance schedules and tasks
A preventive maintenance program should include
a schedule of maintenance tasks and frequencies. This should be based on the manufacturer’s recommendations, operational conditions, and criticality of equipment. Tasks may include inspections, cleaning, lubrication, testing, and repair or replacement of components.
Developing a system for tracking and recording maintenance activities
To ensure that the preventive maintenance program is effective, it is important to track and record maintenance activities. This can help to identify trends, monitor performance, and identify potential issues. A computerized maintenance management system (CMMS) can be used to track maintenance tasks, schedule activities, and record maintenance history.
6. Preventive Maintenance for Specific Boiler Types
There are several types of boilers, each with their own unique maintenance requirements. Some common types of boilers and their maintenance requirements include:
Fire-tube boilers
- Regular cleaning of the fire-tubes to prevent buildup of soot and ash
- Inspection of the fire-side for signs of corrosion or damage
- Testing of the safety valves to ensure they are functioning properly
Water-tube boilers
- Regular cleaning of the tubes to prevent buildup of sediment and mineral deposits
- Inspection of the water-side for signs of corrosion or damage
- Testing of the safety valves to ensure they are functioning properly
Electric boilers
- Regular inspection of the electrical components for signs of wear or damage
- Testing of the control system to ensure it is functioning properly
- Cleaning of the heating elements to prevent buildup of sediment or scale
Steam boilers
- Regular testing of the water level and pressure gauges
- Inspection of the steam traps for signs of wear or damage
- Testing of the safety valves to ensure they are functioning properly
Hot water boilers
- Regular testing of the water level and pressure gauges
- Inspection of the heat exchanger for signs of corrosion or damage
- Cleaning of the circulating pump and motor
7. Best Practices for Preventive Maintenance for Boilers
Regular inspections and cleaning
Regular inspections and cleaning can help to prevent buildup of sediment, scale, or other contaminants that can reduce the efficiency and lifespan of the boiler. Inspections should be performed according to the manufacturer’s recommendations and any applicable regulations.
Proper lubrication and fluid levels
Proper lubrication of moving parts and maintenance of fluid levels can help to prevent wear and tear on components. Lubrication should be performed according to the manufacturer’s recommendations and any applicable regulations.
Monitoring and analyzing Boiler performance data
Monitoring and analyzing boiler performance data can help to identify potential issues before they become major problems. This can include monitoring of temperature, pressure, flow rates, and other parameters. Data analysis can be used to identify trends and patterns that may indicate the need for maintenance or repair.
8. Measuring the Efficiency of Preventive Maintenance for Boilers
Measuring the efficiency of preventive maintenance for boilers can help to determine the effectiveness of the maintenance program and identify areas for improvement. Some key performance indicators that can be used to measure the efficiency of preventive maintenance include:
Boiler availability
Measures the percentage of time that the boiler is available for use. A high availability rate indicates that the boiler is well-maintained and operating efficiently.
Boiler reliability
Measures the frequency of breakdowns or failures. A low failure rate indicates that the boiler is well-maintained and operating efficiently.
Boiler efficiency
Measures the efficiency of the boiler in converting fuel into heat. A high efficiency rate indicates that the boiler is well-maintained and operating efficiently.
Maintenance costs
Measures the cost of preventive maintenance activities. A low maintenance cost indicates that the maintenance program is efficient and cost-effective.
Downtime
Measures the amount of time that the boiler is out of service due to maintenance or repair activities. A low downtime rate indicates that the maintenance program is efficient and effective.
9. Role of CMMS
A computerized maintenance management system (CMMS) can be a valuable tool for managing preventive maintenance for boilers. Some key features of a CMMS include:
Master Data Management
A CMMS can be used to manage the master data for equipment and components, including specifications, manuals, and maintenance histories.
Equipment History
A CMMS can be used to track the maintenance history for equipment and components, including maintenance tasks, frequencies, and costs.
Preventive Maintenance Scheduling and Tracking
A CMMS can be used to schedule preventive maintenance tasks, assign tasks to technicians, and track the status of maintenance activities.
Operational Technology Integration and Condition Based Maintenance
A CMMS can be integrated with operational technology systems to enable condition-based maintenance, where maintenance tasks are triggered based on real-time data from sensors and other monitoring devices.
KPIs Monitoring
A CMMS can be used to monitor key performance indicators for preventive maintenance, such as availability, reliability, efficiency, and maintenance costs.
10. Conclusion
Preventive maintenance is a critical aspect of boiler maintenance and can help to ensure that boilers are operating efficiently, safely, and reliably. A well-designed preventive maintenance program should include scheduled inspections and maintenance tasks, tracking and recording of maintenance activities, and the use of tools and techniques such as cleaning and lubrication methods, inspection and testing procedures, and condition monitoring techniques. By following best practices for preventive maintenance and using a computerized maintenance management system (CMMS), organizations can improve the efficiency and effectiveness of their boiler maintenance programs, reduce downtime and repair costs, and extend the lifespan of their equipment.
Request a one-one demo with our solution engineering team.
Request a one-one demo with our solution engineering team.
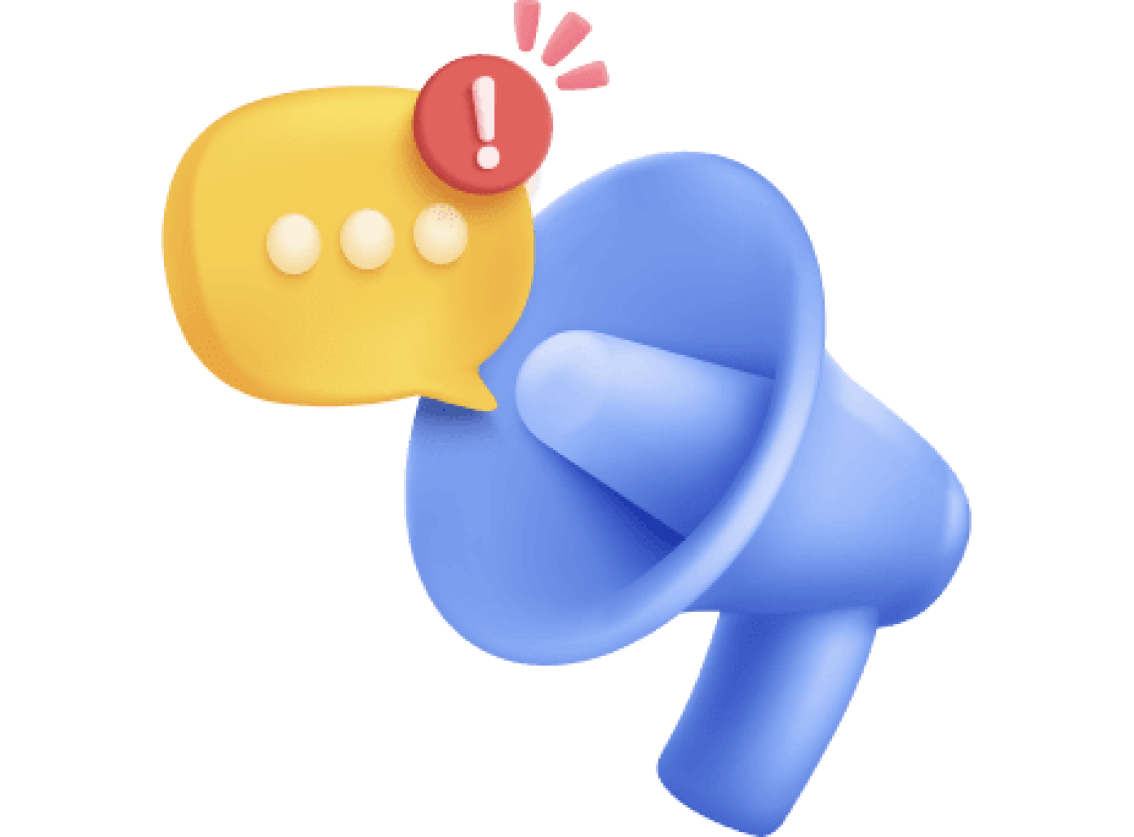