Preventive Maintenance
Program for Tanks & Vessels
Preventive Maintenance Program for Tanks & Vessels
The Complete Guide to Defining Your Preventive Maintenance Program for Tanks and Vessels
Table of Contents
Toggle1. Introduction to Preventive Maintenance for Tanks and Vessels
Preventive maintenance is an essential part of asset management in any industry that uses tanks and vessels, such as the oil and gas, chemical, and food and beverage industries. In this guide, we’ll provide a comprehensive overview of preventive maintenance for tanks and vessels, including the importance of this practice and the sub-assemblies and components of tanks and vessels.
Overview of Preventive Maintenance for Tanks and Vessels
Preventive maintenance is the practice of regularly inspecting, cleaning, repairing, and replacing parts and components of tanks and vessels to prevent equipment failures, increase equipment lifespan, and improve safety.
Importance of Preventive Maintenance for Tanks and Vessels
Preventive maintenance is essential for minimizing equipment downtime, reducing repair and replacement costs, and ensuring safe operation of tanks and vessels. By implementing a preventive maintenance program, you can detect and correct potential issues before they become major problems, saving your company time and money in the long run.
Sub-assemblies and Components of Tanks and Vessels
Tanks and vessels consist of various sub-assemblies and components, including pumps, valves, motors, and control systems. Each of these components requires specific preventive maintenance tasks to ensure proper operation and prevent failures.
2. Components of a Preventive Maintenance Plan for Tanks and Vessels
A preventive maintenance plan for tanks and vessels should include scheduled inspections and maintenance tasks, recommended frequency of inspections and maintenance tasks, and a system for recording and tracking maintenance activities.
Scheduled inspections and maintenance tasks
The preventive maintenance plan should outline specific inspections and maintenance tasks to be performed on tanks and vessels, including cleaning, lubrication, inspections, testing, repairs, and replacements. These tasks should be scheduled at regular intervals based on the equipment’s age, operating conditions, and OEM recommendations.
Recommended frequency of inspections and maintenance tasks
The frequency of inspections and maintenance tasks will vary depending on the type of tank or vessel and the specific components. However, in general, inspections and maintenance tasks should be performed at least once per year, and more frequently for critical equipment.
Recording and tracking maintenance activities
To ensure that all preventive maintenance tasks are performed on schedule and recorded properly, a tracking system should be implemented. This system should include a record of all maintenance activities performed, the date of each task, and the technician who performed the work.
3. Benefits of Preventive Maintenance for Tanks and Vessels
Preventive maintenance provides numerous benefits, including:
Reduced downtime
Preventive maintenance helps to reduce equipment downtime by detecting potential issues before they cause equipment failures. This reduces the need for emergency repairs and helps to keep operations running smoothly.
Extended equipment lifespan
By regularly cleaning, lubricating, and repairing tanks and vessels, you can extend the lifespan of your equipment and avoid costly replacements.
Improved safety
Regular preventive maintenance can help to identify potential safety hazards and correct them before they cause accidents or injuries. This can improve the safety of your workplace and protect your employees.
Reduced repair and replacement costs
By catching issues early, preventive maintenance can help to reduce the need for costly repairs or equipment replacements. This can save your company significant amounts of money in the long run.
Better equipment performance
By keeping your tanks and vessels properly maintained, you can ensure that they perform optimally. This can lead to increased efficiency and productivity.
4. Tools and Techniques for Preventive Maintenance for Tanks and Vessels
There are various tools and techniques used in preventive maintenance for tanks and vessels. These include:
Overview of tools and techniques
Preventive maintenance tools and techniques include cleaning and lubrication methods, inspection and testing procedures, repair and replacement guidelines, and condition monitoring techniques.
Cleaning and Lubrication Methods
Effective cleaning and lubrication are critical for preventing corrosion and ensuring proper equipment operation. Methods for cleaning and lubricating tanks and vessels include:
- Manual cleaning and lubrication
- Automated cleaning and lubrication
- Ultrasonic cleaning
- Vacuum cleaning
- Pressure washing
Inspection and Testing Procedures
Inspections and testing are crucial for detecting potential issues early and preventing equipment failures. Some common inspection and testing procedures for tanks and vessels include:
- Visual inspections
- Magnetic particle inspections
- Dye penetrant inspections
- Ultrasonic testing
- X-ray testing
Repair and Replacement Guidelines
When issues are detected during inspections or testing, repair and replacement guidelines should be followed to ensure proper equipment operation. These guidelines may include:
- Recommended repair procedures
- Part replacement guidelines
- Equipment upgrade recommendations
Condition Monitoring Techniques
Condition monitoring techniques are used to track the performance of tanks and vessels and detect potential issues early. Some common condition monitoring techniques include:
- Vibration analysis
- Acoustic monitoring
- Infrared thermography
- Oil analysis
- Performance testing
5. Developing a Preventive Maintenance Program for Tanks and Vessels
Developing a preventive maintenance program for tanks and vessels involves several key steps:
Identifying critical Tanks and Vessels and equipment
The first step in developing a preventive maintenance program is to identify the most critical tanks and vessels and equipment. These are the pieces of equipment that are essential to your operation and would cause significant downtime or safety hazards if they were to fail.
Researching OEM Manuals and recommendations
Once you have identified the critical equipment, research the OEM manuals and recommendations for preventive maintenance. These manuals provide guidance on the specific maintenance tasks that should be performed and the recommended frequency of these tasks.
Factoring Operational Conditions
The next step is to factor in the operational conditions of your equipment, including the age of the equipment, operating conditions, and past failure history. This information can help you to determine the frequency and type of maintenance tasks needed to prevent equipment failures and maximize equipment lifespan.
Establishing maintenance schedules and tasks
Based on the information gathered in the previous steps, establish a preventive maintenance schedule and list of tasks for each piece of equipment. The schedule should include the recommended frequency of inspections and maintenance tasks, as well as any additional tasks specific to your operation.
Developing a system for tracking and recording maintenance activities
Finally, develop a system for tracking and recording all preventive maintenance activities. This system should include a record of all maintenance tasks performed, the date of each task, and the technician who performed the work. This information can help you to identify trends and potential issues early.
6. Preventive Maintenance for Specific Tanks and Vessels Types
There are various types of tanks and vessels used in different industries, each with their own unique preventive maintenance requirements. Here are some examples:
Storage Tanks
Storage tanks require regular cleaning to prevent corrosion and ensure proper operation. In addition, inspections should be performed to check for leaks and damage to the tank walls.
Pressure Vessels
Pressure vessels require regular inspections to detect potential issues with pressure relief valves and other safety components. In addition, all piping and fittings should be checked for leaks and wear.
Heat Exchangers
Heat exchangers require regular cleaning to prevent scaling and fouling. In addition, inspections should be performed to check for leaks and wear on the tubes and fins.
Mixing Tanks
Mixing tanks require regular cleaning to prevent buildup and ensure proper mixing. In addition, inspections should be performed to check for leaks and wear on the agitators and seals.
Reactors
Reactors require regular cleaning and inspection to prevent buildup and ensure proper mixing. In addition, all seals and bearings should be checked for wear and leaks.
7. Best Practices for Preventive Maintenance for Tanks and Vessels
Following best practices for preventive maintenance can help to ensure optimal equipment performance and minimize downtime. Some key best practices include:
Regular inspections and cleaning
Regular inspections and cleaning are critical for detecting potential issues early and preventing equipment failures. All tanks and vessels should be cleaned and inspected at regular intervals based on the OEM recommendations and operational conditions.
Proper lubrication and fluid levels
Proper lubrication and fluid levels are essential for preventing corrosion and ensuring proper equipment operation. All tanks and vessels should be checked regularly for proper lubrication and fluid levels.
Monitoring and analyzing Tanks and Vessels performance data
Monitoring and analyzing performance data can help to detect trends and potential issues early. By tracking equipment performance over time, you can identify areas that require additional maintenance or upgrades to prevent failures.
8. Measuring the Efficiency of Preventive Maintenance for Tanks and Vessels
Measuring the efficiency of your preventive maintenance program can help you to identify areas for improvement and ensure that your equipment is performing optimally. Key performance indicators (KPIs) that can be used to measure the efficiency of your program include:
Equipment uptime
Equipment uptime is the amount of time that your equipment is operational. This KPI can help you to identify areas where equipment downtime is affecting your operation and implement preventive maintenance measures to reduce downtime .
Maintenance costs
Maintenance costs include all costs associated with preventive maintenance, including labor, parts, and equipment. By tracking maintenance costs, you can identify areas where costs are high and implement measures to reduce costs while maintaining equipment performance.
Mean time between failures (MTBF)
MTBF is the average amount of time between equipment failures. By tracking MTBF, you can identify areas where equipment is failing frequently and implement preventive maintenance measures to reduce failures and downtime.
Mean time to repair (MTTR)
MTTR is the average amount of time it takes to repair equipment after a failure. By tracking MTTR, you can identify areas where repair times are long and implement measures to reduce repair times and minimize downtime.
Equipment availability
Equipment availability is the percentage of time that equipment is available for use. By tracking equipment availability, you can identify areas where equipment downtime is affecting your operation and implement preventive maintenance measures to increase availability.
Repair turnaround time
Repair turnaround time is the time it takes to complete a repair after a failure. By tracking repair turnaround time, you can identify areas where repair times are long and implement measures to reduce repair times and minimize downtime.
Number of unplanned maintenance events
The number of unplanned maintenance events is the number of times that equipment fails unexpectedly and requires unplanned maintenance. By tracking unplanned maintenance events, you can identify areas where equipment is failing frequently and implement preventive maintenance measures to reduce failures and downtime.
Cost of unplanned maintenance events
The cost of unplanned maintenance events includes all costs associated with unexpected equipment failures, including labor, parts, and equipment. By tracking the cost of unplanned maintenance events, you can identify areas where equipment failures are costing your company significant amounts of money and implement measures to reduce costs.
9. Role of CMMS
A computerized maintenance management system (CMMS) can help to streamline your preventive maintenance program and improve efficiency. Some key features of a CMMS include:
Master Data Management
A CMMS can help to manage all data related to your equipment, including equipment specifications, maintenance schedules, and work history.
Equipment History
A CMMS can track all maintenance activities performed on your equipment, including the date of the activity, the technician who performed the work, and any parts or equipment used.
Preventive Maintenance Scheduling and Tracking
A CMMS can help to automate your preventive maintenance program by scheduling maintenance tasks and tracking their completion.
Operational Technology Integration and Condition Based Maintenance
A CMMS can integrate with operational technology systems to provide real-time data on equipment performance, allowing for condition-based maintenance and more efficient maintenance scheduling.
KPIs Monitoring
A CMMS can track key performance indicators to help you measure the efficiency of your preventive maintenance program and identify areas for improvement.
10. Conclusion
Developing a comprehensive preventive maintenance program for tanks and vessels is essential for ensuring optimal equipment performance, reducing downtime, and increasing safety. By following best practices and using tools such as a CMMS, you can streamline your maintenance program and maximize efficiency. Regular inspections, cleaning, lubrication, and monitoring can help to prevent equipment failures and reduce maintenance costs, while tracking KPIs can help you to identify areas for improvement and ensure that your equipment is performing optimally. By using the information in this guide, you can develop a preventive maintenance program that meets the specific needs of your operation and ensures the long-term reliability of your tanks and vessels.
Request a one-one demo with our solution engineering team.
Request a one-one demo with our solution engineering team.
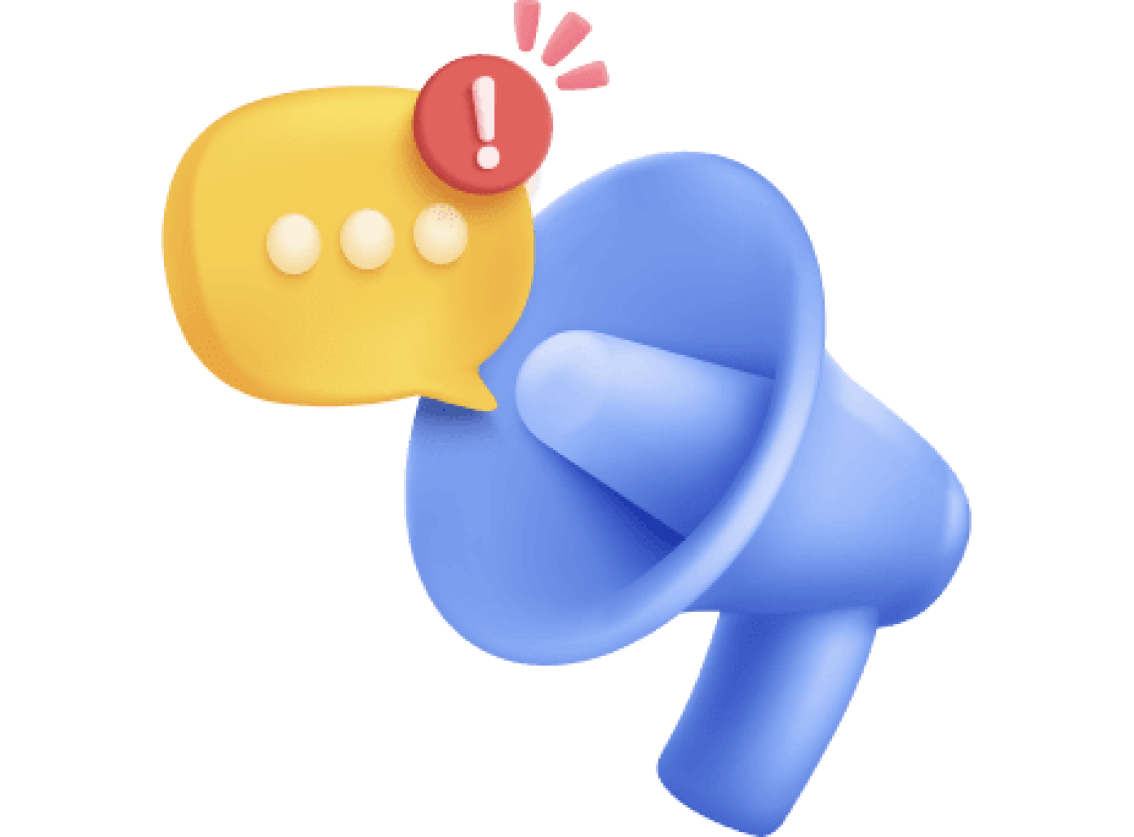