Preventive Maintenance Program for Transformers
Preventive Maintenance Program for Transformers
The Complete Guide to Defining Your Preventive Maintenance Program for Transformers
Table of Contents
ToggleTransformers are a crucial component of electrical power systems, converting power from one voltage level to another. However, transformers are also subject to wear and tear, which can result in costly failures and downtime. To avoid these issues, it is crucial to establish a preventive maintenance program for transformers. In this guide, we will cover the key aspects of developing a preventive maintenance plan for transformers, including maintenance tasks, tools and techniques, best practices, and measuring efficiency.
1. Introduction to Preventive Maintenance for Transformers
Overview Preventive Maintenance for Transformers
Preventive maintenance is a proactive approach to equipment maintenance that involves regularly scheduled inspections, cleaning, lubrication, and testing to prevent equipment failure. In the case of transformers, preventive maintenance can help detect and address issues before they lead to downtime or more significant problems.
Importance of Preventive Maintenance for Transformers
Preventive maintenance is critical for transformers because they are costly to replace, and failure can result in significant downtime and lost productivity. A preventive maintenance program can help ensure that transformers are operating at peak efficiency and extend their lifespan.
Sub-assemblies and Components of Transformers
Transformers are composed of several sub-assemblies and components, each of which must be maintained to ensure the overall system’s reliability. These components include the transformer core, winding, bushings, tap changer, gasket, cooling system, and more.
2. Components of a Preventive Maintenance Plan for Transformers
Scheduled inspections and maintenance tasks
A preventive maintenance plan for transformers should include regularly scheduled inspections and maintenance tasks, such as checking the oil level, testing the insulation resistance, and verifying the cooling system’s operation. The specific maintenance tasks will depend on the transformer’s type, age, and operating conditions.
Recommended frequency of inspections and maintenance tasks
The frequency of inspections and maintenance tasks will depend on the transformer’s operating conditions and age. However, as a general rule, transformers should be inspected and tested at least once a year, and oil should be tested every three to five years.
Recording and tracking maintenance activities
It is crucial to record and track all maintenance activities to ensure that the preventive maintenance program is effective and identify any recurring issues. A computerized maintenance management system (CMMS) can help automate this process and provide valuable data for analyzing the program’s effectiveness.
3. Benefits of Preventive Maintenance for Transformers
There are several benefits to implementing a preventive maintenance program for transformers:
Improved reliability and availability
Preventive maintenance can help identify and address potential issues before they cause equipment failure, improving the transformer’s reliability and availability.
Extended equipment lifespan
Regular maintenance can help extend the transformer’s lifespan, reducing the need for costly replacements and downtime.
Reduced maintenance costs
Preventive maintenance can help reduce maintenance costs by identifying and addressing issues before they require more expensive repairs or replacements
Improved safety and compliance
A well-maintained transformer is safer to operate and can help ensure compliance with relevant regulations and standards.
Improved energy efficiency
Regular maintenance can help ensure that the transformer is operating at peak efficiency, reducing energy consumption and costs.
4. Tools and Techniques for Preventive Maintenance for Transformers
Overview of tools and techniques
There are several tools and techniques used in preventive maintenance for transformers, including cleaning and lubrication methods, inspection and testing procedures, repair and replacement guidelines, and condition monitoring techniques.
Cleaning and Lubrication Methods
Cleaning and lubrication are critical to maintaining transformer reliability. Some common cleaning and lubrication methods include vacuuming, wiping down surfaces, and applying lubricant to moving parts.
Inspection and Testing Procedures
Inspection and testing procedures are used to detect potential issues and verify that the transformer is operating as intended. Some common inspection and testing procedures include visual inspections, insulation resistance testing, and dissolved gas analysis.
Repair and Replacement Guidelines
When issues are identified during inspections, repair and replacement guidelines are used to determine the appropriate course of action. These guidelines should consider factors such as the transformer’s age, type, and operating conditions.
Condition Monitoring Techniques
Condition monitoring techniques are used to monitor transformer performance and detect potential issues before they lead to equipment failure. Some common condition monitoring techniques include temperature monitoring, vibration analysis, and partial discharge testing.
5. Developing a Preventive Maintenance Program for Transformers
Identifying critical Transformers and equipment
The first step in developing a preventive maintenance program for transformers is to identify the critical transformers and equipment that require maintenance. This can be done by analyzing past maintenance records, identifying equipment that is critical to operations, and assessing the equipment’s age and operating conditions.
Researching OEM Manuals and recommendations
Researching the transformer’s original equipment manufacturer (OEM) manuals and recommendations can provide valuable insights into recommended maintenance practices, frequency of inspections, and other relevant information.
Factoring Operational Conditions
Operational conditions, such as age of the equipment, operating conditions, and past failure history, should be factored into the maintenance program to ensure that the maintenance tasks are appropriate for the transformer’s specific situation.
Establishing maintenance schedules and tasks
Based on the above information, maintenance schedules and tasks can be established to ensure that the critical transformers and equipment are inspected, tested, and maintained on a regular basis.
Developing a system for tracking and recording maintenance activities
A system for tracking and recording maintenance activities should be established to ensure that the preventive maintenance program is effective, and issues are identified and addressed promptly. A CMMS can help automate this process and provide valuable data for analyzing the program’s effectiveness.
6. Preventive Maintenance for Specific Transformer Types
There are several types of transformers, each of which requires specific maintenance activities. Some common transformer types and their associated maintenance activities include:
Power Transformers
Power transformers require regular oil testing, insulation resistance testing, and bushing testing, among other activities.
Distribution Transformers
Distribution transformers require regular oil testing
, visual inspections, and insulation resistance testing.
Instrument Transformers
Instrument transformers require regular insulation resistance testing and visual inspections.
Autotransformers
Autotransformers require regular inspections of the tap changer and lubrication of the moving parts.
Step-down Transformers
Step-down transformers require regular inspections of the primary and secondary windings and testing of the insulation resistance.
Step-up Transformers
Step-up transformers require regular oil testing and visual inspections of the bushings and tap changer.
7. Best Practices for Preventive Maintenance for Transformers
Importance of best practices
Following best practices is crucial for ensuring that the preventive maintenance program is effective and that the transformers are operating at peak efficiency.
Regular inspections and cleaning
Regular inspections and cleaning are critical to maintaining transformer reliability and preventing issues before they occur.
Proper lubrication and fluid levels
Proper lubrication and fluid levels are essential for ensuring that the transformer is operating smoothly and efficiently.
Monitoring and analyzing Transformer performance data
Monitoring and analyzing transformer performance data can provide valuable insights into the transformer’s operating conditions and identify potential issues before they lead to equipment failure.
8. Measuring the Efficiency of Preventive Maintenance for Transformers
Importance of KPI
Key performance indicators (KPIs) are critical for measuring the effectiveness of the preventive maintenance program and identifying areas for improvement.
Key Performance Indicators
Some common KPIs for measuring the efficiency of preventive maintenance for transformers include:
Mean time between failures (MTBF): The average time between equipment failures
Mean time to repair (MTTR): The average time it takes to repair equipment after a failure
Transformer availability: The percentage of time that the transformer is available for use
Transformer reliability: The percentage of time that the transformer operates without failure
Transformer energy efficiency: The transformer’s efficiency in converting electrical energy from one voltage level to another
Transformer power factor: The ratio of real power to apparent power in the transformer
Transformer load factor: The ratio of the actual load on the transformer to the transformer’s rated capacity
Transformer losses: The amount of energy lost during the conversion process in the transformer
9. Role of CMMS
Master Data Management
A CMMS is used to manage master data, such as equipment details, maintenance schedules, and work order history, to ensure that the preventive maintenance program is effective and data is accurate.
Equipment History
The CMMS provides equipment history, including maintenance activities, inspection results, and repair history, to help identify potential issues and ensure that the preventive maintenance program is effective.
Preventive Maintenance Scheduling and Tracking
A CMMS is used to schedule preventive maintenance tasks and track their completion to ensure that the maintenance program is effective.
Operational Technology Integration and Condition Based Maintenance
A CMMS can integrate with operational technology, such as sensors and condition monitoring tools, to provide real-time data and enable condition-based maintenance.
KPIs Monitoring
A CMMS can monitor KPIs to measure the effectiveness of the preventive maintenance program and identify areas for improvement.
10. Conclusion
Preventive maintenance is critical for ensuring that transformers operate reliably and efficiently. By following best practices and developing a comprehensive preventive maintenance program that includes regular inspections, cleaning, and lubrication, transformers can operate at peak efficiency and reduce the risk of equipment failure. With the help of tools and techniques, such as condition monitoring and CMMS, preventive maintenance can be made more effective and efficient. By monitoring KPIs and measuring the effectiveness of the preventive maintenance program, areas for improvement can be identified, and the program can be continuously improved.
Request a one-one demo with our solution engineering team.
Request a one-one demo with our solution engineering team.
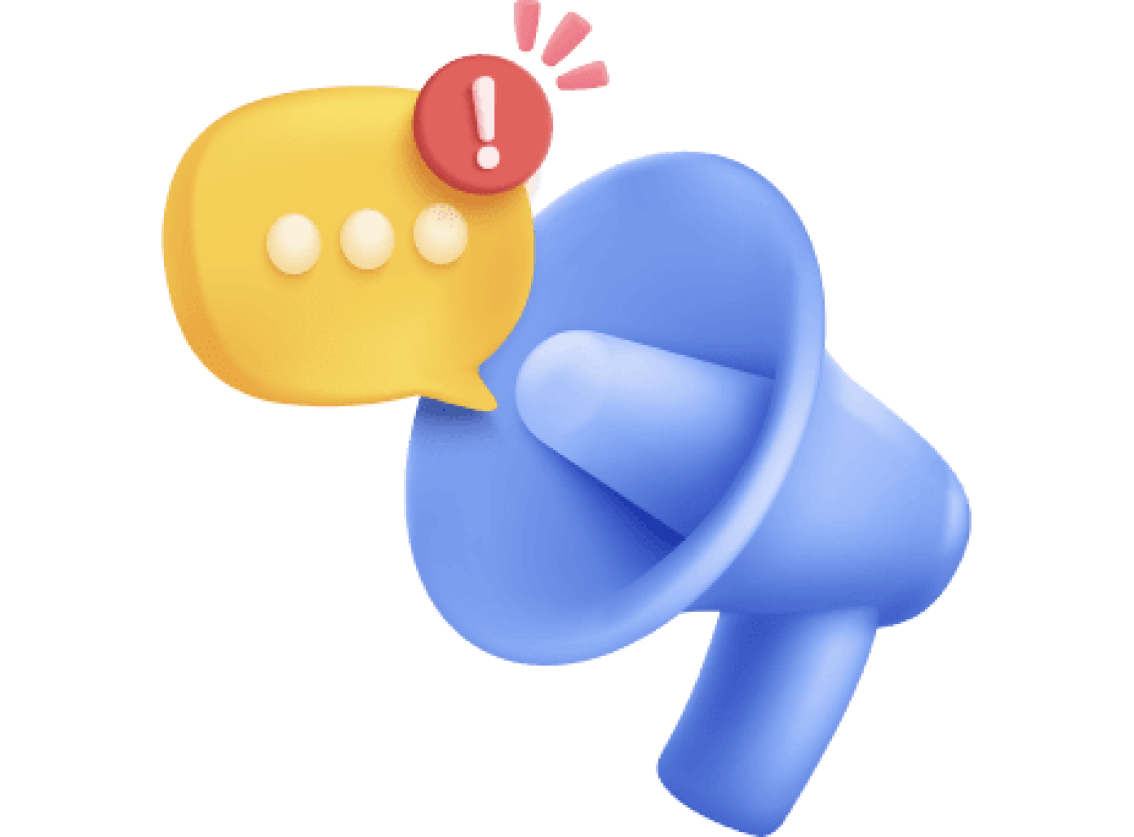