Preventive Maintenance Program for Homogenizers
Preventive Maintenance Program for Homogenizers
The Complete Guide to Defining Your Preventive Maintenance Program for Homogenizers
Table of Contents
Toggle1. Introduction to Preventive Maintenance for Homogenizers
Homogenizers are an essential part of any production process in the food and pharmaceutical industries. Preventive maintenance is critical to ensure their reliable and efficient operation. In this guide, we’ll cover everything you need to know about developing a preventive maintenance program for homogenizers.
Overview of Preventive Maintenance for Homogenizers
Preventive maintenance is a proactive maintenance strategy that involves performing regular inspections, cleaning, lubrication, and repairs to prevent equipment failure. It’s an essential component of any asset management and plant maintenance program for homogenizers.
Importance of Preventive Maintenance for Homogenizers
Preventive maintenance helps to minimize downtime and repair costs, optimize equipment efficiency and productivity, and ensure worker safety. It also helps to extend the lifespan of homogenizers and their components.
Sub-assemblies and Components of Homogenizers
Homogenizers consist of several sub-assemblies and components, including pumps, motors, valves, and seals. Each component plays a critical role in the homogenization process, and preventive maintenance is required to keep them in good working condition.
2. Components of a Preventive Maintenance Plan for Homogenizers
Scheduled Inspections and Maintenance Tasks
A preventive maintenance plan should include a schedule of regular inspections and maintenance tasks. This can include daily, weekly, monthly, or annual tasks depending on the equipment and the operating conditions. Scheduled inspections can help to identify potential issues before they become major problems, and maintenance tasks can help to prevent equipment failure.
Recommended Frequency of Inspections and Maintenance Tasks
The frequency of inspections and maintenance tasks will depend on the equipment and the operating conditions. For example, a homogenizer that operates under high-pressure conditions may require more frequent inspections and maintenance tasks than one that operates under low-pressure conditions. The OEM manual will provide recommendations for the frequency of inspections and maintenance tasks.
Recording and Tracking Maintenance Activities
Recording and tracking maintenance activities is essential to ensure that all tasks are completed on time and that there is a record of maintenance history. This can be done using a maintenance log or a computerized maintenance management system (CMMS).
3. Benefits of Preventive Maintenance for Homogenizers
Improved Reliability
Preventive maintenance can help to improve equipment reliability by identifying potential issues before they become major problems. This can help to minimize downtime and repair costs.
Increased Productivity
Preventive maintenance can help to optimize equipment efficiency and productivity by ensuring that all components are in good working condition. This can help to reduce production downtime and increase throughput.
Extended Equipment Lifespan
Preventive maintenance can help to extend the lifespan of homogenizers and their components by minimizing wear and tear and preventing equipment failure.
Improved Safety
Preventive maintenance can help to improve worker safety by identifying potential hazards and ensuring that all safety protocols and procedures are followed.
Cost Savings
Preventive maintenance can help to reduce repair costs and minimize downtime, resulting in cost savings for the organization.
4. Tools and Techniques for Preventive Maintenance for Homogenizers
Overview of Tools and Techniques
There are several tools and techniques that can be used to perform preventive maintenance on homogenizers, including cleaning and lubrication methods, inspection and testing procedures, repair and replacement guidelines, and condition monitoring techniques.
Cleaning and Lubrication Methods
Regular cleaning and lubrication of homogenizer components is essential to ensure their reliable and efficient operation. Cleaning methods can include the use of solvents or mechanical methods, while lubrication methods can include the use of oil or grease.
Inspection and Testing Procedures
Inspection and testing procedures can include visual inspections, non-destructive testing, and performance testing. These procedures can help to identify potential issues and ensure that all components are in good working condition.
Repair and Replacement Guidelines
Repair and replacement guidelines can help to ensure that all components are repaired or replaced according to the manufacturer’s recommendations. This can help to prevent equipment failure and ensure the safe and reliable operation of the equipment.
Condition Monitoring Techniques
Condition monitoring techniques can include vibration analysis, thermal imaging, and oil analysis. These techniques can help to identify potential issues before they become major problems and help to optimize equipment performance.
5. Developing a Preventive Maintenance Program for Homogenizers
Identifying Critical Homogenizers and Equipment
Identifying critical homogenizers and equipment is essential to ensure that they receive the appropriate level of preventive maintenance. Critical equipment can include equipment that is essential to the production process, equipment that is expensive to repair or replace, or equipment that poses a safety hazard if it fails.
Researching OEM Manuals and Recommendations
The OEM manual will provide recommendations for the frequency of inspections and maintenance tasks and may also provide guidelines for repair and replacement. It’s essential to follow these recommendations to ensure the safe and reliable operation of the equipment.
Factoring Operational Conditions
Operational conditions, such as the age of the equipment, operating conditions, and past failure history, should be considered when developing a preventive maintenance program. These factors can impact the frequency of inspections and maintenance tasks.
Establishing Maintenance Schedules and Tasks
Once critical equipment has been identified and operational conditions have been factored in, a maintenance schedule and tasks can be established. This should include a schedule of regular inspections and maintenance tasks, as well as guidelines for repair and replacement.
Developing a System for Tracking and Recording Maintenance Activities
Recording and tracking maintenance activities is essential to ensure that all tasks are completed on time and that there is a record of maintenance history. This can be done using a maintenance log or a computerized maintenance management system (CMMS).
6. Preventive Maintenance for Specific Homogenizer Types
Types of Homogenizers
Homogenizers come in various types, including piston homogenizers, valve homogenizers, and ultrasonic homogenizers. Each type has specific preventive maintenance requirements.
Preventive Maintenance Activities for Specific Homogenizer Types
Piston Homogenizers:
Piston homogenizers require regular cleaning and lubrication of the piston and cylinder, as well as regular replacement of wear parts such as seals and valves.
Valve Homogenizers:
Valve homogenizers require regular cleaning and lubrication of the valves and valve seats, as well as regular replacement of wear parts such as seals and valves.
Ultrasonic Homogenizers:
Ultrasonic homogenizers require regular cleaning of the ultrasonic probe and generator, as well as regular replacement of wear parts such as seals and valves.
Microfluidizer Homogenizers:
Microfluidizer homogenizers require regular cleaning and replacement of wear parts such as seals and valves. They also require periodic calibration and testing.
High-Pressure Homogenizers:
High-pressure homogenizers require regular cleaning and lubrication of the high-pressure pump and homogenizing valve, as well as regular replacement of wear parts such as seals and valves.
7. Best Practices for Preventive Maintenance for Homogenizers
Importance of Best Practices
Following best practices for preventive maintenance can help to ensure the safe and reliable operation of homogenizers and their components. This can help to minimize downtime, reduce repair costs, and improve productivity.
Regular Inspections and Cleaning
Regular inspections and cleaning are essential to identify potential issues and ensure that all components are in good working condition. Cleaning can help to remove dirt and debris that can cause wear and tear on components.
Proper Lubrication and Fluid Levels
Proper lubrication and fluid levels are essential to ensure the reliable and efficient operation of homogenizers. This can help to reduce wear and tear on components and prevent equipment failure.
Monitoring and Analyzing Homogenizer Performance Data
Monitoring and analyzing homogenizer performance data can help to identify potential issues before they become major problems. This can help to optimize equipment performance and improve productivity.
8. Measuring the Efficiency of Preventive Maintenance for Homogenizers
Importance of KPIs
Key performance indicators (KPIs) can help to measure the effectiveness of a preventive maintenance program for homogenizers. KPIs can include equipment reliability, productivity, efficiency, optimization, downtime, and cost analysis.
Key Performance Indicators
Equipment Reliability: This KPI measures the percentage of time that homogenizers are available for production.
Productivity: This KPI measures the output of homogenizers in relation to the input.
Efficiency: This KPI measures the ratio of output to input for homogenizers.
Optimization: This KPI measures the degree to which homogenizers are being used to their maximum potential.
Downtime: This KPI measures the amount of time that homogenizers are not available for production due to maintenance or repair.
Cost Analysis: This KPI measures the cost of preventive maintenance compared to the cost of repair or replacement.
Safety: This KPI measures the degree to which homogenizers are being operated safely, with minimal risk of injury or property damage.
Equipment Troubleshooting: This KPI measures the ability of maintenance personnel to diagnose and repair problems with homogenizers quickly and effectively.
Calibration and Testing: This KPI measures the degree to which homogenizers are calibrated and tested to ensure reliable and efficient operation.
9. Role of CMMS
Master Data Management
A computerized maintenance management system (CMMS) can help to manage master data for homogenizers, including equipment specifications, maintenance schedules, and maintenance history. This can help to ensure that all information is accurate and up-to-date.
Equipment History
A CMMS can track equipment history, including maintenance activities, repair history, and replacement history. This can help to identify trends and patterns that can be used to improve preventive maintenance programs.
Preventive Maintenance Scheduling and Tracking
A CMMS can help to schedule and track preventive maintenance activities for homogenizers, ensuring that all tasks are completed on time and according to schedule.
Operational Technology Integration and Condition-Based Maintenance
A CMMS can integrate with operational technology (OT) systems to enable condition-based maintenance for homogenizers. This can help to identify potential issues before they become major problems, improving equipment reliability and productivity.
KPIs Monitoring
A CMMS can monitor KPIs for homogenizers, providing real-time data on equipment reliability, productivity, efficiency, and downtime. This can help to optimize maintenance programs and improve equipment performance.
10. Conclusion
Preventive maintenance is essential to ensure the safe and reliable operation of homogenizers. A well-designed preventive maintenance program can help to minimize downtime, reduce repair costs, and improve productivity. By following best practices for preventive maintenance and using the appropriate tools and techniques, organizations can optimize equipment performance and maximize the lifespan of homogenizers and their components.
Request a one-one demo with our solution engineering team.
Request a one-one demo with our solution engineering team.
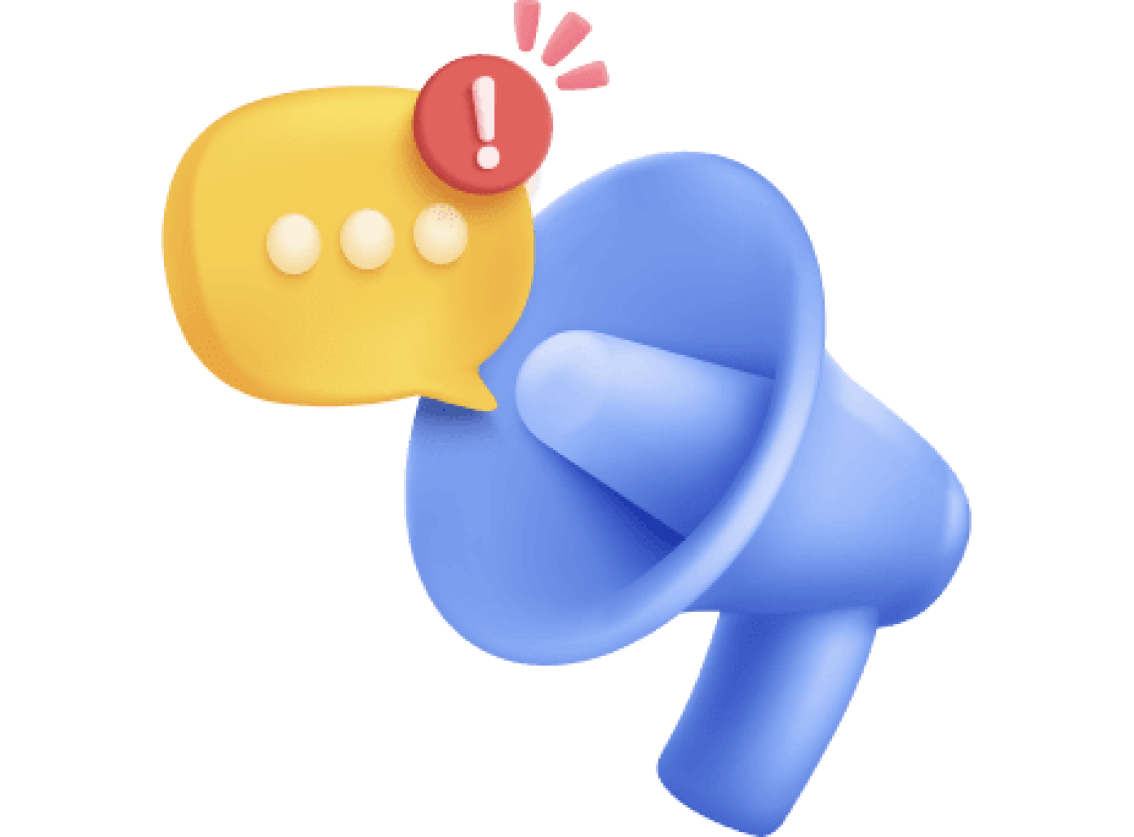