Preventive Maintenance Program for Cooling Towers
Preventive Maintenance Program for Cooling Towers
The Complete Guide to Defining Your Preventive Maintenance Program for Cooling Towers
Table of Contents
Toggle1. Introduction to Preventive Maintenance for Cooling Towers
Preventive maintenance is essential for ensuring the optimal performance and longevity of cooling towers. In this section, we’ll provide an overview of preventive maintenance for cooling towers, discuss the importance of preventive maintenance, and identify the key sub-assemblies and components of cooling towers that require regular maintenance.
Overview of Preventive Maintenance for Cooling Towers
Preventive maintenance is a proactive approach to equipment maintenance that involves regularly scheduled inspections, cleaning, lubrication, testing, and repair tasks to prevent equipment failure, minimize downtime, and extend equipment life. Preventive maintenance programs are designed to keep equipment running smoothly, reduce the risk of unplanned downtime, and improve equipment reliability and safety.
Importance of Preventive Maintenance for Cooling Towers
Preventive maintenance is particularly important for cooling towers because they are essential components of HVAC and industrial systems that play a critical role in maintaining optimal operating conditions for equipment and processes. Cooling towers are responsible for removing heat from process water, condenser water, and other industrial fluids. Without effective cooling, equipment can overheat, malfunction, and even fail, resulting in costly downtime and repairs.
Sub-assemblies and Components of Cooling Towers
Cooling towers are complex systems that consist of several sub-assemblies and components that require regular maintenance to operate efficiently and effectively. These components include:
- Fans and motors
- Nozzles and distribution systems
- Fill media and drift eliminators
- Basins and sumps
- Water pumps and valves
- Water treatment systems
2. Components of a Preventive Maintenance Plan for Cooling Towers
Now that we’ve discussed the importance of preventive maintenance for cooling towers, let’s take a closer look at the key components of a preventive maintenance plan for cooling towers.
Scheduled Inspections and Maintenance Tasks
A preventive maintenance plan for cooling towers should include regularly scheduled inspections and maintenance tasks to ensure that all components are in good working order and operating as intended. These tasks may include:
- Cleaning and disinfecting cooling tower basins, sumps, and fill media
- Inspecting and testing fans, motors, nozzles, and distribution systems
- Checking water chemistry and treatment systems
- Lubricating and adjusting bearings, belts, and pulleys
- Inspecting and repairing water pumps and valves
Recommended Frequency of Inspections and Maintenance Tasks
The frequency of inspections and maintenance tasks will depend on several factors, including the age and condition of the equipment, the operating conditions, and the past failure history. As a general rule, most cooling towers require quarterly inspections and maintenance, although some components may require more frequent attention. For example, water treatment systems may need to be checked and adjusted more frequently to ensure that the water quality remains within acceptable limits.
Recording and Tracking Maintenance Activities
A preventive maintenance plan should also include a system for recording and tracking maintenance activities. This system may include maintenance logs, work orders, and other documentation that allows you to keep track of when tasks were performed, who performed them, and what was done. This information can be used to identify trends, track equipment performance over time, and plan future maintenance activities.
3. Benefits of Preventive Maintenance for Cooling Towers
There are many benefits to implementing a preventive maintenance program for cooling towers. Here are some of the key benefits:
Improved Equipment Reliability
Preventive maintenance can help identify and address potential equipment issues before they lead to unplanned downtime or equipment failure. By regularly inspecting and maintaining cooling tower components, you can reduce the risk of unexpected breakdowns and extend the life of your equipment.
Increased Energy Efficiency
Cooling towers that are properly maintained are more energy-efficient than those that are not. Regular cleaning, lubrication, and adjustment of components can improve cooling tower performance, reduce energy consumption, and lower operating costs.
Reduced Maintenance Costs
Preventive maintenance can help reduce maintenance costs by identifying and addressing potential equipment issues before they become major problems. By addressing issues early on, you can avoid more costly repairs or replacements down the line.
Improved Safety and Compliance
Properly maintained cooling towers are safer to operate and less likely to cause accidents or injuries. In addition, regular maintenance can help ensure compliance with regulatory requirements and prevent fines or other penalties.
Extended Equipment Life
Preventive maintenance can help extend the life of your cooling tower equipment by addressing potential issues early on and ensuring that all components are operating as intended. By extending equipment life, you can avoid costly replacements and improve your return on investment.
4. Tools and Techniques for Preventive Maintenance for Cooling Towers
There are several tools and techniques that can be used to implement an effective preventive maintenance program for cooling towers. Let’s take a closer look at some of these tools and techniques.
Overview of Tools and Techniques
The following tools and techniques can be used to implement an effective preventive maintenance program for cooling towers:
- Cleaning and lubrication methods
- Inspection and testing procedures
- Repair and replacement guidelines
- Condition monitoring techniques
Cleaning and Lubrication Methods
Cleaning and lubrication are essential components of a preventive maintenance program for cooling towers. Regular cleaning and disinfecting of cooling tower basins, sumps, and fill media can help prevent the buildup of dirt, debris, and algae that can impede cooling tower performance. Lubricating and adjusting bearings, belts, and pulleys can also improve cooling tower performance and reduce the risk of equipment failure.
Inspection and Testing Procedures
Inspection and testing procedures should be included in any preventive maintenance program for cooling towers. These procedures may include visual inspections, vibration analysis, temperature monitoring, and other techniques that can be used to identify potential equipment issues before they become major problems.
Repair and Replacement Guidelines
When issues are identified during inspections or testing, repair and replacement guidelines should be in place to ensure that equipment is fixed in a timely manner. These guidelines should outline the criteria for determining whether a component can be repaired or needs to be replaced, as well as the process for carrying out the repair or replacement.
Condition Monitoring Techniques
Condition monitoring techniques can be used to track the performance of cooling tower components over time and identify potential issues before they become major problems. These techniques may include vibration analysis, oil analysis, infrared thermography, and other methods that can provide insight into the condition of equipment and help identify potential issues before they lead to equipment failure.
5. Developing a Preventive Maintenance Program for Cooling Towers
Developing a preventive maintenance program for cooling towers requires careful planning and consideration of several factors, including identifying critical cooling towers and equipment, researching OEM manuals and recommendations, factoring operational conditions, and developing a system for tracking and recording maintenance activities. Let’s take a closer look at each of these factors.
Identifying Critical Cooling Towers and Equipment
The first step in developing a preventive maintenance program for cooling towers is to identify the critical cooling towers and equipment that require regular maintenance. This may include equipment that is essential to the operation of your facility or equipment that is particularly costly or difficult to replace.
Researching OEM Manuals and Recommendations
Once you’ve identified the critical cooling towers and equipment, the next step is to research the OEM manuals and recommendations for each component. These manuals and recommendations can provide valuable information on the maintenance requirements for each component, as well as the recommended frequency of inspections and maintenance tasks.
Factoring Operational Conditions
Operational conditions, such as the age of the equipment and the operating environment, should also be taken into account when developing a preventive maintenance program for cooling towers. Equipment that is older or operating in harsh conditions may require more frequent maintenance than newer equipment or equipment that is operating in ideal conditions.
Establishing Maintenance Schedules and Tasks
Once you’ve identified the critical cooling towers and equipment and researched the OEM manuals and recommendations, the next step is to establish maintenance schedules and tasks for each component. These schedules and tasks should be based on the OEM recommendations, as well as your operational conditions and past failure history.
Developing a System for Tracking and Recording Maintenance Activities
Finally, a system for tracking and recording maintenance activities should be developed to ensure that all maintenance tasks are completed on schedule and that all maintenance activities are properly documented. This system may include maintenance logs, work orders, and other documentation that allows you to keep track of when tasks were performed, who performed them, and what was done.
6. Preventive Maintenance for Specific Cooling Tower Types
Preventive maintenance activities can vary depending on the type of cooling tower you have. Here are some of the most common types of cooling towers and the preventive maintenance activities that should be carried out for each type:
Crossflow Cooling Towers
- Clean and disinfect cooling tower basins and sumps
- Inspect and clean fill media
- Inspect and adjust fans and motors
- Monitor water chemistry and treatment systems
- Inspect and repair water pumps and valves
Counterflow Cooling Towers
- Clean and disinfect cooling tower basins and sumps
- Inspect and clean fill media
- Inspect and adjust fans and motors
- Monitor water chemistry and treatment systems
- Inspect and repair water pumps and valves
- Inspect and clean drift eliminators
Natural Draft Cooling Towers
- Inspect and repair concrete and steel structures
- Inspect and clean fill media
- Inspect and adjust fans and motors
- Monitor water chemistry and treatment systems
- Inspect and repair water pumps and valves
Induced Draft Cooling Towers
- Clean and disinfect cooling tower basins and sumps
- Inspect and clean fill media
- Inspect and adjust fans and motors
- Monitor water chemistry and treatment systems
- Inspect and repair water pumps and valves
Forced Draft Cooling Towers
- Clean and disinfect cooling tower basins and sumps
- Inspect and clean fill media
- Inspect and adjust fans and motors
- Monitor water chemistry and treatment systems
- Inspect and repair water pumps and valves
7. Best Practices for Preventive Maintenance for Cooling Towers
Following best practices for preventive maintenance can help ensure that your cooling towers operate efficiently and effectively. Here are some of the most important best practices to keep in mind:
Regular Inspections and Cleaning
Regular inspections and cleaning can help prevent issues from developing in your cooling towers. Inspections should be carried out on a regular schedule, with cleaning and maintenance tasks performed as needed based on the results of the inspections.
Proper Lubrication and Fluid Levels
Proper lubrication and fluid levels can help prevent equipment failures and extend the life of your cooling towers. Lubrication and fluid levels should be checked regularly and topped off or replaced as needed.
Monitoring and Analyzing Cooling Towers Performance Data
Monitoring and analyzing cooling towers performance data can help you identify issues and optimize the performance of your equipment. Performance data should be tracked and analyzed on a regular basis, with adjustments made as needed based on the results of the analysis.
8. Measuring the Efficiency of Preventive Maintenance for Cooling Towers
Measuring the efficiency of preventive maintenance for cooling towers is important to ensure that your maintenance program is effective and producing results. Key performance indicators (KPIs) can be used to measure the efficiency of your maintenance program. Here are some of the most important KPIs to track:
Overall Equipment Effectiveness (OEE)
OEE is a measure of the overall efficiency of your equipment. It takes into account factors like downtime, speed loss, and quality loss to provide a holistic picture of your equipment’s performance.
Mean Time Between Failures (MTBF)
MTBF is a measure of the reliability of your equipment. It measures the average time between equipment failures and can help you identify trends and potential issues before they become major problems.
Mean Time to Repair (MTTR)
MTTR is a measure of the speed with which you can repair equipment when it fails. It can help you identify inefficiencies in your maintenance processes and make adjustments to reduce downtime and increase productivity.
Equipment Availability
Equipment availability is a measure of the percentage of time that your equipment is available and ready to be used. It takes into account downtime and maintenance activities and can help you identify areas where you need to improve your maintenance program.
Maintenance Costs
Maintenance costs are a measure of the total cost of your maintenance program. By tracking maintenance costs, you can identify areas where you may be overspending and make adjustments to reduce costs while still maintaining equipment reliability.
Energy Consumption
Energy consumption is a measure of the amount of energy your cooling towers consume to operate. By tracking energy consumption, you can identify areas where you can improve efficiency and reduce costs.
Water Consumption
Water consumption is a measure of the amount of water your cooling towers consume to operate. By tracking water consumption, you can identify areas where you can improve efficiency and reduce costs while also reducing your environmental impact.
Occupational Health and Safety
Occupational health and safety is a measure of the safety of your maintenance program. By tracking occupational health and safety metrics, you can identify areas where you need to improve safety protocols and reduce the risk of injury or accidents.
9. Role of CMMS
A Computerized Maintenance Management System (CMMS) can be an important tool for managing your preventive maintenance program for cooling towers. Here are some of the key functions of a CMMS:
Master Data Management
A CMMS can help you manage your equipment data, including equipment specifications, maintenance schedules, and maintenance history. By centralizing this data, you can make it easier to manage and analyze, leading to more effective maintenance processes.
Equipment History
A CMMS can help you track the maintenance history of your equipment, including maintenance activities, repairs, and replacements. This can help you identify trends and potential issues before they become major problems.
Preventive Maintenance Scheduling and Tracking
A CMMS can help you schedule and track preventive maintenance tasks, making it easier to ensure that tasks are completed on time and according to schedule. This can help prevent equipment failures and reduce downtime.
Operational Technology Integration and Condition Based Maintenance
A CMMS can integrate with your operational technology systems, allowing you to monitor equipment performance data and trigger maintenance tasks based on that data. This can help you move towards a more proactive, condition-based maintenance approach.
KPIs Monitoring
A CMMS can track and report on KPIs, allowing you to monitor the efficiency and effectiveness of your maintenance program over time. This can help you identify areas where you need to improve and make adjustments to improve performance.
10. Conclusion
Preventive maintenance is essential for ensuring the efficient and reliable operation of your cooling towers. By developing a comprehensive preventive maintenance program, you can reduce downtime, extend equipment life, and save money on maintenance and repair costs. By following best practices, measuring performance using KPIs, and leveraging the power of a CMMS, you can ensure that your preventive maintenance program is effective and producing results.
Request a one-one demo with our solution engineering team.
Request a one-one demo with our solution engineering team.
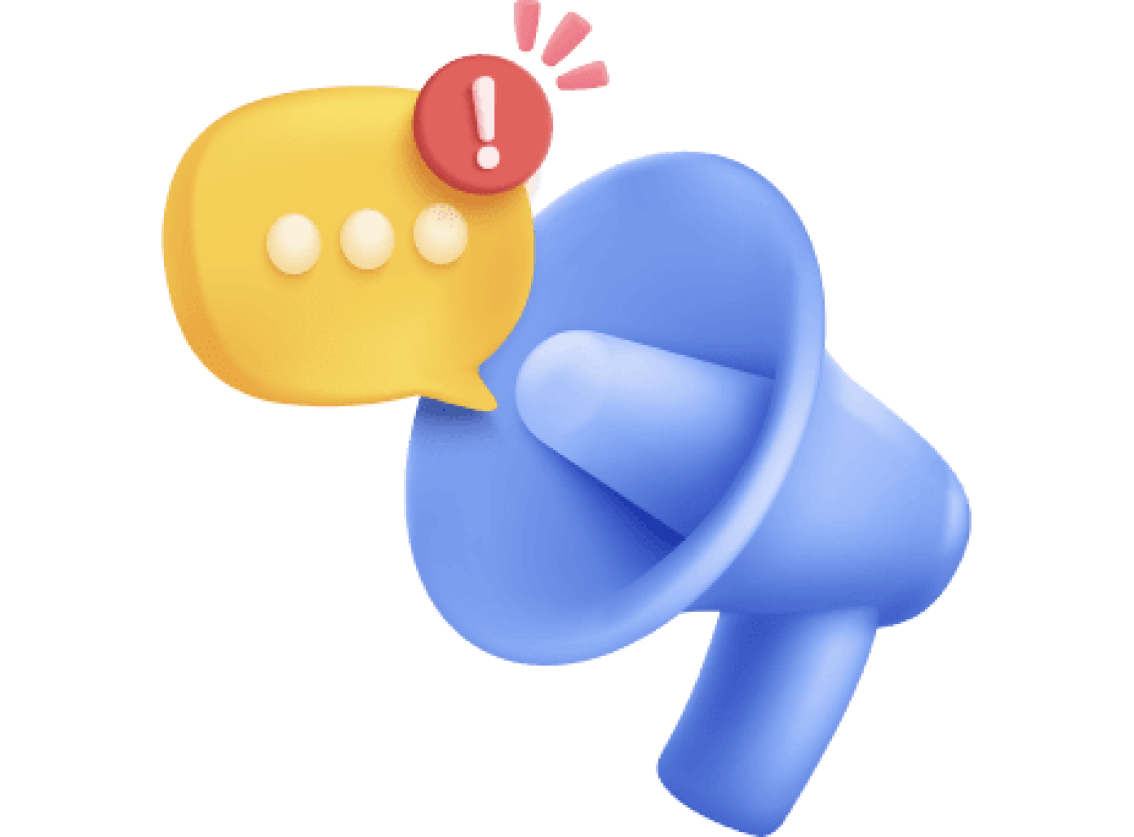