Preventive Maintenance Program for Agitators
Preventive Maintenance Program for Agitators
The Complete Guide to Defining Your Preventive Maintenance Program for Agitators
Table of Contents
ToggleAs a plant maintenance expert, you know that agitators play a critical role in many industrial processes, and keeping them running smoothly is essential to maintaining production efficiency. This guide will provide you with a comprehensive understanding of preventive maintenance for agitators, including the importance of scheduled inspections and maintenance tasks, tools and techniques for maintaining agitators, developing a preventive maintenance program, and measuring the efficiency of preventive maintenance efforts. Let’s get started.
1. Introduction to Preventive Maintenance for Agitators
Overview of Preventive Maintenance for Agitators
Preventive maintenance is the practice of regularly inspecting and maintaining equipment to prevent breakdowns and unplanned downtime. It is a proactive approach that can help you identify potential problems before they become major issues. Preventive maintenance for agitators involves a series of scheduled maintenance tasks that aim to increase equipment reliability, reduce maintenance costs, and extend the lifespan of your equipment.
Importance of Preventive Maintenance for Agitators
The benefits of preventive maintenance for agitators are significant. By implementing a preventive maintenance program, you can:
- Reduce the likelihood of equipment failure
- Increase equipment reliability and availability
- Extend the lifespan of your equipment
- Reduce maintenance costs
- Increase production efficiency
- Ensure compliance with safety and environmental regulations
Sub-assemblies and Components of Agitators
Agitators consist of various sub-assemblies and components that work together to mix and blend materials. Some of the key components of agitators include:
- Mixing shaft
- Impellers or blades
- Bearings
- Seals
- Drive unit
- Motors
- Support structures
2. Components of a Preventive Maintenance Plan for Agitators
Scheduled Inspections and Maintenance Tasks
A preventive maintenance plan for agitators should include scheduled inspections and maintenance tasks. These tasks can include:
- Visual inspections of equipment
- Cleaning and lubrication of bearings and seals
- Testing of motors and drives
- Checking and adjusting belt tension
- Checking and tightening fasteners
- Replacing worn or damaged parts
- Monitoring and analyzing agitator performance data
Recommended Frequency of Inspections and Maintenance Tasks
The frequency of inspections and maintenance tasks will depend on a variety of factors, including the age of the equipment, operating conditions, and past failure history. However, as a general rule, it is recommended to perform regular inspections and maintenance tasks at least once a year. Some tasks, such as cleaning and lubrication, may need to be performed more frequently depending on the operating conditions.
Recording and Tracking Maintenance Activities
Recording and tracking maintenance activities is an essential part of any preventive maintenance program. This can be done using a computerized maintenance management system (CMMS) or a simple spreadsheet. By keeping track of maintenance activities, you can ensure that tasks are completed on schedule and identify any recurring issues that may require further attention.
3. Benefits of Preventive Maintenance for Agitators
Preventive maintenance for agitators offers numerous benefits, including:
Increased equipment reliability and availability: Regular maintenance can help prevent breakdowns and unplanned downtime, ensuring that equipment is available when it is needed.
Extended equipment lifespan: By performing regular maintenance tasks, you can help to reduce wear and tear on equipment, extending its useful life.
Reduced maintenance costs: Preventive maintenance can help to identify potential problems early, reducing the need for expensive repairs or replacements.
Improved production efficiency: By keeping equipment running smoothly, you can maximize production efficiency and reduce the risk of production delays or stoppages.
Compliance with safety and environmental regulations: Regular maintenance can help to ensure that equipment is operating safely and in compliance with relevant regulations.
4. Tools and Techniques for Preventive Maintenance for Agitators
There are several tools and techniques that can be used to maintain agitators effectively. These include:
Cleaning and Lubrication Methods
Cleaning and lubrication are essential maintenance tasks that help to prevent wear and tear on equipment. Some cleaning and lubrication methods that can be used for agitators include:
- Dry cleaning: Removing dirt and debris using compressed air or a vacuum.
- Wet cleaning: Using water or a cleaning solution to remove dirt and debris.
- Lubrication: Applying lubricant to bearings and other moving parts to reduce friction and wear.
Inspection and Testing Procedures
Regular inspections and testing are essential for identifying potential problems early. Some inspection and testing procedures that can be used for agitators include:
- Visual inspections: Checking for signs of wear and damage.
- Vibration analysis: Measuring the level of vibration to identify potential issues.
- Oil analysis: Analyzing oil samples to identify potential issues with bearings and other components.
- Electrical testing: Testing motors and other electrical components to ensure they are functioning correctly.
Repair and Replacement Guidelines
When problems are identified, it is essential to have clear repair and replacement guidelines in place. Some guidelines that can be used for agitators include:
- Replacement of worn or damaged parts: When parts are worn or damaged, they should be replaced promptly to prevent further damage.
- Proper alignment: Ensuring that components are properly aligned can help to prevent wear and damage.
- Balancing: Balancing components can help to reduce vibration and prevent damage.
- Corrosion and erosion prevention: Taking steps to prevent corrosion and erosion can help to extend the life of components.
Condition Monitoring Techniques
Condition monitoring techniques can be used to identify potential problems before they become major issues. Some condition monitoring techniques that can be used for agitators include:
Vibration analysis
Measuring the level of vibration to identify potential issues.
Benefits of vibration analysis:
- Identifies potential problems before they become major issues
- Helps to reduce equipment downtime
- Increases equipment reliability
- Reduces maintenance costs
Oil analysis
Analyzing oil samples to identify potential issues with bearings and other components.
Benefits of oil analysis:
- Identifies potential problems before they become major issues
- Helps to extend equipment lifespan
- Reduces maintenance costs
Thermography
Measuring the temperature of components to identify potential issues.
Benefits of thermography:
- Identifies potential problems before they become major issues
- Helps to reduce equipment downtime
- Increases equipment reliability
- Reduces maintenance costs
Ultrasound
Detecting changes in sound waves to identify potential issues.
Benefits of ultrasound:
- Identifies potential problems before they become major issues
- Helps to reduce equipment downtime
- Increases equipment reliability
- Reduces maintenance costs
Acoustic emission
Detecting changes in acoustic emission to identify potential issues.
Benefits of acoustic emission:
- Identifies potential problems before they become major issues
- Helps to reduce equipment downtime
- Increases equipment reliability
- Reduces maintenance costs
5. Developing a Preventive Maintenance Program for Agitators
Identifying Critical Agitators and Equipment
The first step in developing a preventive maintenance program for agitators is to identify critical agitators and equipment. This can be done by assessing the importance of each piece of equipment to the production process and evaluating the impact of equipment failure. Equipment that is critical to production and has a significant impact on the process should be prioritized for maintenance.
Researching OEM Manuals and Recommendations
Once critical equipment has been identified, it is essential to research OEM manuals and recommendations for maintenance. These manuals provide detailed instructions on maintenance tasks, recommended schedules, and other important information. By following these recommendations, you can ensure that maintenance is performed correctly and that equipment is maintained in optimal condition.
Factoring Operational Conditions
Operational conditions, such as the age of the equipment, operating conditions, and past failure history, should be taken into account when developing a maintenance program. Older equipment may require more frequent maintenance, while equipment that operates in harsh conditions may require additional measures to prevent wear and damage.
Establishing Maintenance Schedules and Tasks
Maintenance schedules and tasks should be established based on OEM recommendations and operational conditions. Tasks should be scheduled at appropriate intervals to ensure that equipment is maintained in optimal condition. The maintenance schedule should also take into account production schedules to ensure that maintenance does not interfere with production.
Developing a System for Tracking and Recording Maintenance Activities
A system for tracking and recording maintenance activities should be developed to ensure that tasks are completed on schedule and to identify any recurring issues that may require further attention. This can be done using a computerized maintenance management system (CMMS) or a simple spreadsheet.
6. Preventive Maintenance for Specific Agitator Types
Different Types of Agitators
There are several different types of agitators, each with their own unique characteristics and maintenance requirements. Some common types of agitators include:
- Top-entry agitators
- Side-entry agitators
- Bottom-entry agitators
- Portable agitators
- Static mixers
- Magnetic mixers
- Jet mixers
- Inline mixers
Preventive Maintenance for Specific Agitator Types
Each type of agitator has its own unique maintenance requirements. Some specific preventive maintenance activities that should be carried out for each type of agitator are:
Top-entry agitators
- Inspect shaft, bearings, and seals regularly
- Check and replace lubrication as needed
- Check alignment and balance of impellers
- Clean impellers and mixing vessel regularly
- Check and replace motor brushes as needed
Side-entry agitators
- Inspect shaft, bearings, and seals regularly
- Check and replace lubrication as needed
- Check alignment and balance of impellers
- Clean impellers and mixing vessel regularly
- Check and replace motor brushes as needed
- Inspect and clean cooling water system
Bottom-entry agitators
- Inspect shaft, bearings, and seals regularly
- Check and replace lubrication as needed
- Check alignment and balance of impellers
- Clean impellers and mixing vessel regularly
- Check and replace motor brushes as needed
- Inspect and clean bottom support bearings regularly
Portable agitators
- Inspect shaft, bearings, and seals regularly
- Check and replace lubrication as needed
- Check alignment and balance of impellers
- Clean impellers and mixing vessel regularly
- Check and replace motor brushes as needed
- Inspect and clean gearbox regularly
- Check and replace mixing elements as needed
- Clean mixing vessel regularly
- Inspect and replace housing gaskets as needed
Magnetic mixers
- Inspect and replace magnetic drive components as needed
- Check and replace lubrication as needed
- Clean impellers and mixing vessel regularly
- Check and replace motor brushes as needed
- Inspect and replace control system components as needed
Jet mixers
- Check and replace nozzles as needed
- Inspect and replace seals and bearings as needed
- Clean impellers and mixing vessel regularly
- Check and replace motor brushes as needed
Inline mixers
- Check and replace mixing elements as needed
- Clean mixing vessel regularly
- Inspect and replace seals and bearings as needed
7. Best Practices for Preventive Maintenance for Agitators
Importance of Best Practices
Implementing best practices for preventive maintenance can help to ensure that equipment is maintained in optimal condition, reducing downtime, extending equipment life, and improving overall reliability. Some best practices that can be followed for agitator maintenance include:
Regular Inspections and Cleaning
Regular inspections and cleaning can help to prevent problems from developing and ensure that equipment is maintained in optimal condition. Inspections can help to identify potential issues before they become major problems, while cleaning can help to remove build-up and debris that can cause wear and damage.
Proper Lubrication and Fluid Levels
Proper lubrication and fluid levels are essential for the smooth operation of agitators. Lubrication helps to reduce wear and tear on components, while maintaining proper fluid levels ensures that equipment is operating at optimal efficiency.
Monitoring and Analyzing Agitator Performance Data
Monitoring and analyzing agitator performance data can help to identify potential issues and optimize maintenance schedules. Performance data can be used to track equipment usage, identify patterns of wear and damage, and evaluate the effectiveness of maintenance activities.
8. Measuring the Efficiency of Preventive Maintenance for Agitators
Importance of KPIs
Key performance indicators (KPIs) can be used to measure the effectiveness of preventive maintenance programs for agitators. By tracking KPIs, you can evaluate the performance of equipment, identify areas for improvement, and optimize maintenance activities to ensure that equipment is maintained in optimal condition.
Key Performance Indicators
Equipment uptime
Equipment uptime measures the percentage of time that equipment is operational over a given period. High equipment uptime indicates that maintenance activities are effective in preventing downtime and reducing the impact of failures on production.
Maintenance cost per unit of production
Maintenance cost per unit of production measures the cost of maintenance activities relative to the amount of production. This KPI can help to identify areas where maintenance costs can be reduced without compromising equipment reliability.
Mean time between failures (MTBF)
MTBF measures the average amount of time between equipment failures. High MTBF indicates that maintenance activities are effective in preventing failures and reducing the impact of failures on production.
Mean time to repair (MTTR)
MTTR measures the average amount of time it takes to repair equipment after a failure. Low MTTR indicates that maintenance activities are effective in reducing downtime and restoring equipment to operational condition quickly.
Equipment availability
Equipment availability measures the percentage of time that equipment is available for use over a given period. High equipment availability indicates that maintenance activities are effective in preventing downtime and reducing the impact of failures on production.
Inventory turnover
Inventory turnover measures the number of times inventory is sold and replaced over a given period. High inventory turnover indicates that maintenance activities are effective in reducing the need for spare parts and minimizing inventory costs.
Mean time to failure (MTTF)
MTTF measures the average amount of time it takes for equipment to fail after it is put into service. High MTTF indicates that equipment is reliable and that maintenance activities are effective in preventing premature failures.
Planned maintenance percentage
Planned maintenance percentage measures the percentage of maintenance activities that are planned in advance rather than reactive. High planned maintenance percentage indicates that maintenance activities are proactive and effective in preventing failures.
9. Role of CMMS
A computerized maintenance management system (CMMS) can be used to manage preventive maintenance programs for agitators. Some of the key functions of a CMMS include:
Master Data Management
A CMMS can be used to manage master data for equipment, such as equipment specifications, maintenance schedules, and maintenance history. This data can be used to optimize maintenance activities and ensure that equipment is maintained in optimal condition.
Equipment History
A CMMS can be used to track equipment history, including maintenance activities, repairs, and failures. This information can be used to identify patterns of wear and damage, evaluate the effectiveness of maintenance activities, and optimize maintenance schedules.
Preventive Maintenance Scheduling and Tracking
A CMMS can be used to schedule and track preventive maintenance activities for agitators, ensuring that maintenance tasks are completed on time and that equipment is maintained in optimal condition. This can help to reduce downtime and extend equipment life, while also improving overall reliability.
Operational Technology Integration and Condition-Based Maintenance
A CMMS can be integrated with operational technology (OT) systems, such as programmable logic controllers (PLCs) and supervisory control and data acquisition (SCADA) systems. This integration can be used to collect real-time data on equipment performance, allowing for condition-based maintenance (CBM) activities to be performed. CBM involves monitoring equipment in real-time to identify potential issues before they become major problems, optimizing maintenance activities, and reducing downtime.
KPIs Monitoring
A CMMS can be used to monitor KPIs, such as equipment uptime, MTBF, and MTTR. By tracking KPIs, you can evaluate the effectiveness of maintenance activities, identify areas for improvement, and optimize maintenance schedules to ensure that equipment is maintained in optimal condition.
10. Conclusion
Implementing a preventive maintenance program for agitators is essential for maintaining optimal equipment performance, reducing downtime, and extending equipment life. By following the components of a preventive maintenance plan, the benefits of preventive maintenance can be realized, including increased equipment reliability, reduced maintenance costs, and improved safety. Tools and techniques such as cleaning and lubrication, inspection and testing, and condition monitoring can be used to optimize maintenance activities and ensure that equipment is maintained in optimal condition.
Request a one-one demo with our solution engineering team.
Request a one-one demo with our solution engineering team.
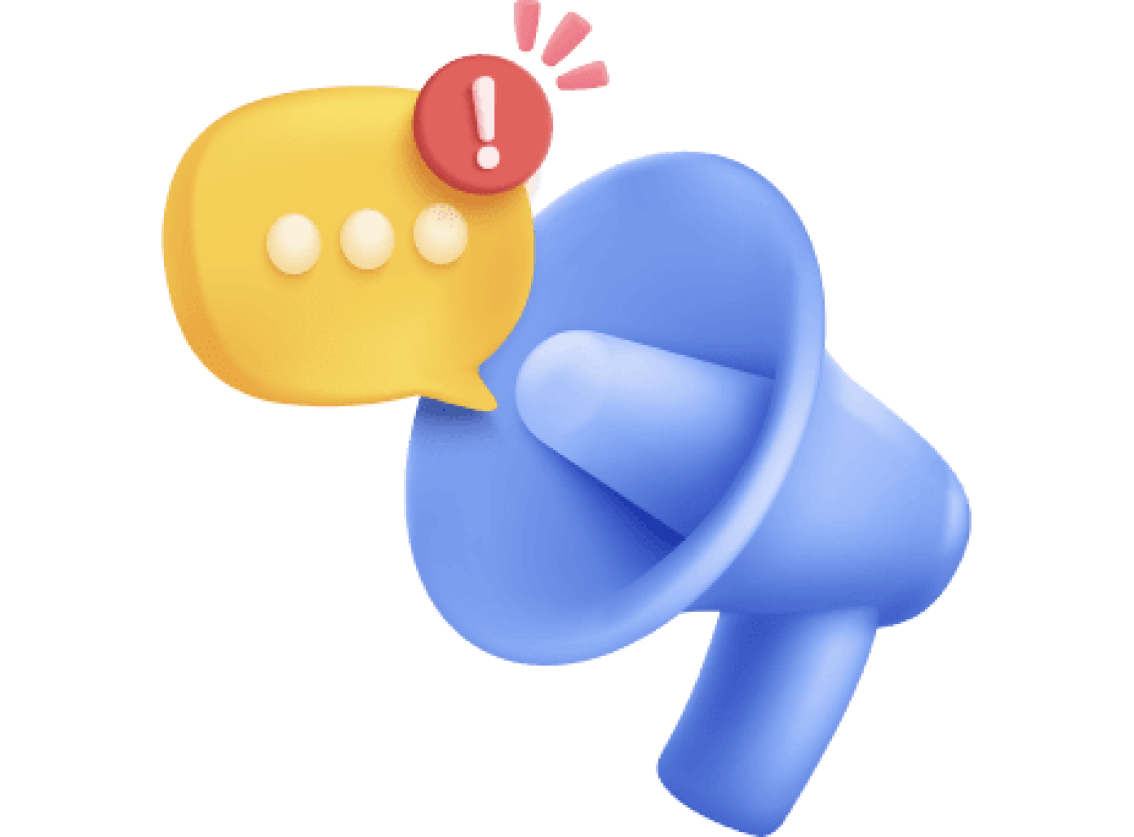