Preventive Maintenance Program for Motors
Preventive Maintenance Program for Motors
The Complete Guide to Defining Your Preventive Maintenance Program for Motors
Table of Contents
Toggle1. Introduction to Preventive Maintenance for Motors
As an asset manager or plant maintenance professional, you understand the critical role that motors play in your operations. Motors power your equipment and machines, and any downtime or failure can lead to costly disruptions, production losses, and safety risks. That’s why it’s crucial to implement a robust preventive maintenance program for motors to optimize their reliability, efficiency, and lifespan. In this guide, we’ll cover all the key aspects of developing a comprehensive preventive maintenance strategy for motors, from the importance of preventive maintenance to the role of CMMS. Let’s get started.
Importance of Preventive Maintenance for Motors
Preventive maintenance is a proactive approach to maintaining equipment and machinery by performing scheduled inspections and maintenance tasks to prevent failures or breakdowns. Preventive maintenance for motors is critical because:
- It reduces the risk of unplanned downtime and production losses.
- It extends the motor’s lifespan by identifying and fixing problems early.
- It improves motor efficiency and reduces energy consumption and costs.
- It enhances safety by preventing motor-related accidents and incidents.
- It ensures compliance with regulatory standards and requirements.
2. Components of a Preventive Maintenance Plan for Motors
A preventive maintenance plan for motors should include the following components:
Scheduled inspections and maintenance tasks
The plan should specify the types of inspections and maintenance tasks to be performed, such as:
- Visual inspections of motor components and connections
- Electrical testing of motor windings and insulation
- Lubrication of motor bearings and other moving parts
- Cleaning of motor surfaces and cooling systems
- Replacement of worn or damaged parts and components
Recommended frequency of inspections and maintenance tasks
The plan should define the recommended frequency of each task based on the motor type, size, usage, environment, and manufacturer’s recommendations. For example, a critical motor may require more frequent inspections and maintenance than a non-critical one.
Recording and tracking maintenance activities
The plan should include a system for recording and tracking all maintenance activities, including inspections, tests, repairs, and replacements. This system should capture data on the motor’s history, condition, and performance and provide insights for optimizing the maintenance program.
3. Benefits of Preventive Maintenance for Motors
Preventive maintenance for motors offers several benefits, such as:
Increased reliability
By identifying and fixing potential problems before they cause a failure or breakdown, preventive maintenance can significantly increase the motor’s reliability and reduce the risk of downtime and production losses.
Improved efficiency
Preventive maintenance can improve the motor’s efficiency by ensuring that it operates at optimal levels and reducing energy consumption and costs.
Longer lifespan
Preventive maintenance can extend the motor’s lifespan by identifying and replacing worn or damaged parts and components and ensuring that the motor operates within its design specifications.
Enhanced safety
Preventive maintenance can enhance safety by identifying potential hazards or risks related to the motor and taking corrective actions to prevent accidents or incidents.
Compliance with regulations
Preventive maintenance can help you comply with regulatory standards and requirements related to motor maintenance and operation, ensuring that you avoid penalties or legal issues.
4. Tools and Techniques for Preventive Maintenance for Motors
Preventive maintenance for motors involves using a variety of tools and techniques to identify and fix potential problems before they cause a failure or breakdown. Here are some of the most commonly used tools and techniques:
Vibration analysis
- Measures motor vibrations to detect imbalances, misalignments, and other issues.
- Benefits: early detection of problems, reduces downtime and repair costs, improves motor reliability.
Infrared thermography
- Measures motor temperature to detect hot spots, overload, and other issues.
- Benefits: early detection of problems, reduces energy costs, improves motor lifespan.
Motor current analysis
- Measures motor current to detect overload, unbalance, and other issues.
- Benefits: early detection of problems, improves motor efficiency and lifespan.
Oil analysis
- Analyzes motor oil to detect contamination, wear, and other issues.
- Benefits: early detection of problems, reduces maintenance costs, improves motor lifespan.
Ultrasonic testing
- Measures high-frequency sound waves to detect leaks, friction, and other issues.
- Benefits: early detection of problems, reduces energy costs, improves motor efficiency and reliability.
Visual inspections
- Inspects motor components and connections visually to detect wear, damage, and other issues.
- Benefits: early detection of problems, improves safety and reliability.
Electrical testing
- Tests motor windings, insulation, and other electrical components to detect faults and defects.
- Benefits: early detection of problems, improves safety and reliability.
Performance testing
- Tests motor performance under normal and extreme conditions to detect issues with efficiency, power, and other parameters.
- Benefits: early detection of problems, improves motor efficiency and reliability.
5. Developing a Preventive Maintenance Program for Motors
To develop an effective preventive maintenance program for motors, you need to follow a structured approach that takes into account the following factors:
Identifying critical motors and equipment
You need to identify the motors and equipment that are critical for your operations and require preventive maintenance to minimize downtime and production losses.
Researching OEM Manuals and recommendations
You need to research the OEM manuals and recommendations for the motors and equipment to ensure that you follow the manufacturer’s guidelines and best practices.
Factoring Operational Conditions
You need to consider the operational conditions of the motors and equipment, such as their age, usage , environment, and past failure history, to determine the appropriate frequency and types of inspections and maintenance tasks.
Establishing maintenance schedules and tasks
You need to establish maintenance schedules and tasks for each motor and equipment based on the above factors and using the appropriate tools and techniques.
Developing a system for tracking and recording maintenance activities
You need to develop a system for tracking and recording all maintenance activities, including inspections, tests, repairs, and replacements, to ensure that you have a complete and accurate record of the motor’s history, condition, and performance.
6. Preventive Maintenance for Specific Motor Types
Different types of motors have different maintenance requirements, and you need to tailor your preventive maintenance program to each type. Here are some of the most common types of motors and their preventive maintenance requirements:
AC Induction Motors
- Lubricate bearings regularly
- Inspect and clean cooling fans and ducts
- Check for voltage unbalance
- Check for overheating and hot spots
- Inspect and replace belts
DC Motors
- Clean commutators and brushes
- Check and adjust brush pressure
- Inspect and replace brushes and armature
- Lubricate bearings
- Check for voltage and current variations
Servo Motors
- Check and adjust feedback devices
- Lubricate bearings
- Inspect and clean cooling fans and ducts
- Check for misalignment and mechanical issues
- Verify motor tuning and parameters
Stepper Motors
- Check and adjust the motor and driver settings
- Verify proper wiring and connections
- Lubricate bearings
- Inspect and clean cooling fans and ducts
- Verify motor positioning and movement
Synchronous Motors
- Check and adjust field excitation
- Verify proper synchronization with the power supply
- Inspect and clean cooling fans and ducts
- Check for mechanical issues and vibrations
- Lubricate bearings
7. Best Practices for Preventive Maintenance for Motors
Here are some of the best practices for preventive maintenance for motors:
Regular inspections and cleaning
Perform regular inspections and cleaning of the motors and equipment to detect potential issues and maintain optimal performance and lifespan.
Proper lubrication and fluid levels
Ensure that the motors have proper lubrication and fluid levels to reduce friction, wear, and overheating and extend their lifespan.
Monitoring and analyzing motor performance data
Collect and analyze motor performance data, such as temperature, vibration, and current, to detect potential issues and optimize the preventive maintenance program.
8. Measuring the Efficiency of Preventive Maintenance for Motors
To measure the efficiency of your preventive maintenance program for motors , you need to use Key Performance Indicators (KPIs) that quantify the benefits and costs of the program. Here are some of the top KPIs for measuring the efficiency of preventive maintenance for motors:
Mean time between failures (MTBF)
- Measures the average time between two consecutive failures of a motor
- Indicates the reliability and availability of the motor
Mean time to repair (MTTR)
- Measures the average time to repair a motor after a failure
- Indicates the efficiency and effectiveness of the maintenance program
Overall Equipment Effectiveness (OEE)
- Measures the overall efficiency and effectiveness of the motor and equipment
- Combines factors such as availability, performance, and quality
Cost of maintenance per unit of production (CoMP)
- Measures the cost of maintenance per unit of output or production
- Indicates the cost-effectiveness of the maintenance program
Energy efficiency
- Measures the energy consumption and efficiency of the motor
- Indicates the environmental impact and cost savings of the maintenance program
9. Role of CMMS
Computerized Maintenance Management Systems (CMMS) can help you automate and optimize your preventive maintenance program for motors by providing the following features:
Master Data Management
CMMS can store and manage all the data related to your motors and equipment, such as asset information, maintenance schedules, and historical records.
Equipment History
CMMS can track and record all the maintenance activities performed on your motors and equipment, including inspections, tests, repairs, and replacements.
Preventive Maintenance Scheduling and Tracking
CMMS can schedule and track all the preventive maintenance tasks for your motors and equipment, based on factors such as time, usage, and condition.
Operational Technology Integration and Condition Based Maintenance
CMMS can integrate with other operational technologies, such as sensors, controllers, and data analytics, to enable condition-based maintenance and real-time monitoring.
KPIs Monitoring
CMMS can generate reports and dashboards that show the performance and efficiency of your preventive maintenance program, based on the KPIs discussed earlier.
10. Conclusion
Preventive maintenance for motors is a crucial aspect of asset management and plant maintenance that can improve safety, reliability, efficiency, and lifespan of motors and equipment. By following the best practices and using the appropriate tools and techniques, you can develop a comprehensive and effective preventive maintenance program for your motors, tailored to their specific types and operational conditions. Moreover, by using CMMS and monitoring KPIs, you can measure and optimize the efficiency and effectiveness of your maintenance program, and ensure compliance with regulatory standards and requirements.
Request a one-one demo with our solution engineering team.
Request a one-one demo with our solution engineering team.
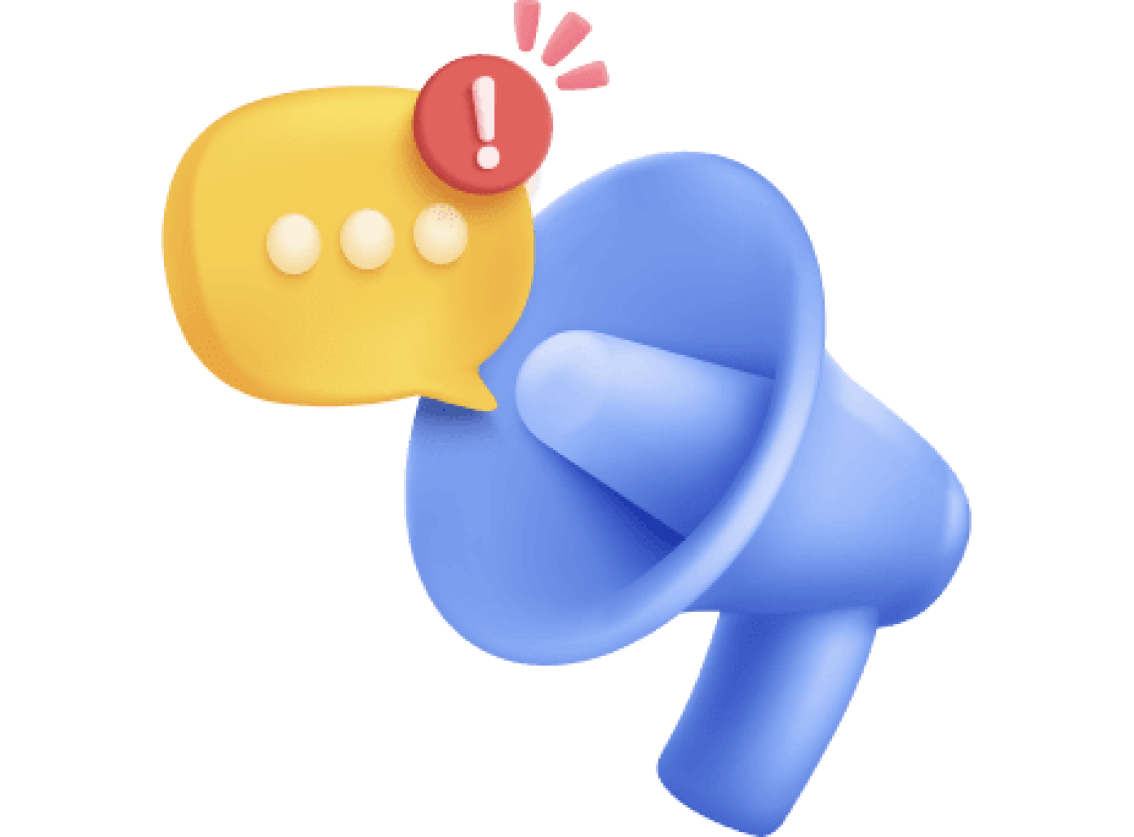