Preventive Maintenance
Program for Mixers
Preventive Maintenance Program for Mixers
The Complete Guide to Defining Your Preventive Maintenance Program for Mixers
Table of Contents
Toggle1. Introduction to Preventive Maintenance for Mixers
Preventive maintenance is a crucial component of asset management and plant maintenance, and mixers are no exception. In this section, we’ll provide an overview of preventive maintenance for mixers, highlight the importance of preventive maintenance, and discuss the sub-assemblies and components of mixers.
Overview Preventive Maintenance for Mixers
Preventive maintenance is a proactive approach to maintaining and repairing equipment to avoid breakdowns and unplanned downtime. A preventive maintenance program for mixers involves scheduled inspections, maintenance tasks, and repairs to minimize wear and tear, maximize efficiency, and extend the lifespan of the equipment.
Importance of Preventive Maintenance for Mixers
Preventive maintenance is essential for maintaining the reliability, safety, and performance of mixers. Without a preventive maintenance program, mixers are susceptible to unplanned downtime, increased maintenance costs, and reduced efficiency. Regular inspections, cleaning, lubrication, and repairs can prevent breakdowns, minimize downtime, and maximize the lifespan of the equipment.
Sub-assemblies and Components of Mixers
Mixers consist of several sub-assemblies and components that require regular maintenance and inspection. Some of the critical components include motors, gearboxes, belts, bearings, seals, and couplings. Maintenance of these components is necessary to ensure optimal performance and prevent premature wear and tear.
2. Components of a Preventive Maintenance Plan for Mixers
A preventive maintenance plan for mixers should include scheduled inspections, maintenance tasks, and repairs. In this section, we’ll discuss the components of a preventive maintenance plan, the recommended frequency of inspections and maintenance tasks, and the importance of recording and tracking maintenance activities.
Scheduled Inspections and Maintenance Tasks
A preventive maintenance plan should include regular inspections and maintenance tasks to ensure that the equipment is operating efficiently and safely. Some of the typical maintenance tasks include cleaning, lubrication, alignment, replacement of worn parts, testing, calibration, and monitoring of performance data. The specific tasks and frequency depend on the type of mixer, the operational conditions, and the manufacturer’s recommendations.
Recommended Frequency of Inspections and Maintenance Tasks
The frequency of inspections and maintenance tasks should be based on the operational conditions, age of the equipment, and manufacturer’s recommendations. Typically, inspections and maintenance tasks should be scheduled quarterly, biannually, or annually, depending on the type of mixer and the level of usage. Critical components may require more frequent inspections and maintenance tasks.
Recording and Tracking Maintenance Activities
Recording and tracking maintenance activities are essential components of a preventive maintenance program. It helps to identify trends, monitor equipment performance, and schedule maintenance tasks effectively. Recording and tracking can be done manually or with the help of maintenance software.
3. Benefits of Preventive Maintenance for Mixers
A preventive maintenance program for mixers has several benefits. In this section, we’ll highlight the top 5 benefits of preventive maintenance.
Maximize Equipment Efficiency
Preventive maintenance helps to ensure that equipment is operating at optimal efficiency levels, reducing energy consumption and operational costs. Regular inspections, cleaning, lubrication, and calibration can identify potential issues before they become significant problems and allow for repairs to be made before they cause downtime or costly repairs.
Reduce Downtime
Unplanned downtime can be costly and disrupt production schedules, causing delays and lost revenue. Preventive maintenance can identify potential issues before they lead to equipment failure, reducing downtime and minimizing production interruptions.
Increase Equipment Lifespan
Preventive maintenance can help to extend the lifespan of mixers, reducing the need for premature replacements and lowering capital expenditures. Regular inspections, cleaning, lubrication, and repairs can minimize wear and tear, preventing premature failure and reducing the need for costly repairs.
Improve Safety
A well-maintained mixer is a safer mixer. Preventive maintenance can identify potential safety hazards and allow for repairs to be made before accidents occur. Regular inspections and maintenance tasks can ensure that safety features, such as emergency stop buttons and safety guards, are functioning correctly.
Reduce Maintenance Costs
Preventive maintenance can help to reduce maintenance costs by identifying potential issues before they require costly repairs. Regular inspections, cleaning, lubrication, and repairs can prevent premature wear and tear, reducing the need for replacement parts and minimizing maintenance costs over the life of the equipment.
4. Tools and Techniques for Preventive Maintenance for Mixers
Preventive maintenance for mixers requires a variety of tools and techniques to ensure that the equipment is operating at optimal levels. In this section, we’ll discuss the various cleaning and lubrication methods, inspection and testing procedures, repair and replacement guidelines, and condition monitoring techniques that can be used for preventive maintenance.
Cleaning and Lubrication Methods
Cleaning and lubrication are critical components of preventive maintenance for mixers. Cleaning methods can include pressure washing, steam cleaning, and chemical cleaning, depending on the type of mixer and the level of contamination. Lubrication methods can include manual lubrication, automatic lubrication systems, and centralized lubrication systems. The frequency of cleaning and lubrication should be based on the manufacturer’s recommendations and the level of usage.
Inspection and Testing Procedures
Regular inspections and testing are essential components of preventive maintenance for mixers. Inspections can include visual inspections, vibration analysis, and ultrasonic testing, among others. Testing procedures can include load testing, torque testing, and power measurement. The frequency of inspections and testing should be based on the manufacturer’s recommendations and the level of usage.
Repair and Replacement Guidelines
Repair and replacement guidelines are necessary to ensure that mixers are operating at optimal levels. Guidelines can include recommendations for repairing or replacing critical components, such as motors, gearboxes, belts, bearings, seals, and couplings. The guidelines should be based on the manufacturer’s recommendations and the level of usage.
Condition Monitoring Techniques
Condition monitoring techniques can help to identify potential issues before they become significant problems. Techniques can include vibration analysis, oil analysis, and thermography, among others. Condition monitoring can be done manually or with the help of monitoring software.
5. Developing a Preventive Maintenance Program for Mixers
Developing a preventive maintenance program for mixers requires a systematic approach that considers the criticality of the equipment, operational conditions, and manufacturer’s recommendations. In this section, we’ll discuss the steps involved in developing a preventive maintenance program for mixers.
Identifying Critical Mixers and Equipment
The first step in developing a preventive maintenance program is to identify the critical mixers and equipment that require regular maintenance and inspection. The criticality of the equipment can be determined based on its role in the production process, the impact of downtime on production schedules, and the cost of replacement.
Researching OEM Manuals and Recommendations
Researching OEM manuals and recommendations is essential to ensure that maintenance tasks are performed correctly and in accordance with the manufacturer’s guidelines. The manuals can provide information on recommended maintenance tasks, the frequency of inspections and maintenance, and the tools and techniques required for maintenance.
Factoring Operational Conditions
Operational conditions, such as age of the equipment, operating conditions, and past failure history, should be factored into the preventive maintenance program. The frequency of inspections and maintenance tasks should be adjusted based on the age of the equipment, the level of usage, and the previous history of failures.
Establishing Maintenance Schedules and Tasks
Based on the criticality of the equipment, OEM recommendations, and operational conditions, maintenance schedules and tasks should be established. The schedules should include the frequency of inspections and maintenance tasks, the tools and techniques required, and the personnel responsible for performing the tasks.
Developing a System for Tracking and Recording Maintenance Activities
Developing a system for tracking and recording maintenance activities is essential to ensure that maintenance tasks are performed on schedule and to identify trends in equipment performance. The system can include a maintenance log, software for tracking maintenance tasks, and performance metrics to monitor the effectiveness of the preventive maintenance program.
6. Preventive Maintenance for Specific Mixer Types
Preventive maintenance tasks can vary depending on the type of mixer. In this section, we’ll discuss the top 5 types of mixers and the specific preventive maintenance activities that should be carried out for each type.
Batch Mixers
- Inspect belts and bearings for wear and damage
- Clean and lubricate mixing blades and paddles
- Check gearboxes for proper lubrication
- Inspect seals for wear and leaks
- Calibrate temperature sensors and safety controls
Continuous Mixers
- Inspect augers and paddles for wear and damage
- Clean and lubricate mixing blades and paddles
- Check gearboxes for proper lubrication
- Inspect seals for wear and leaks
- Calibrate temperature sensors and safety controls
Planetary Mixers
- Inspect planetary gears for wear and damage
- Clean and lubricate mixing blades and paddles
- Check gearboxes for proper lubrication
- Inspect seals for wear and leaks
- Calibrate temperature sensors and safety controls
Ribbon Mixers
- Inspect ribbon blades for wear and damage
- Clean and lubricate mixing blades and paddles
- Check gearboxes for proper lubrication
- Inspect seals for wear and leaks
- Calibrate temperature sensors and safety controls
Paddle Mixers
- Inspect paddles for wear and damage
- Clean and lubricate mixing blades and paddles
- Check gearboxes for proper lubrication
- Inspect seals for wear and leaks
- Calibrate temperature sensors and safety controls
7. Best Practices for Preventive Maintenance for Mixers
Adhering to best practices for preventive maintenance can help to ensure that mixers are operating at optimal levels and minimize the risk of equipment failure. In this section, we’ll discuss some of the best practices for preventive maintenance for mixers.
Regular Inspections and Cleaning
Regular inspections and cleaning are essential to identify potential issues before they become significant problems. Inspections can include visual inspections, vibration analysis, and ultrasonic testing, among others. Cleaning can include pressure washing, steam cleaning, and chemical cleaning, depending on the type of mixer and the level of contamination.
Proper Lubrication and Fluid Levels
Proper lubrication and fluid levels are critical components of preventive maintenance for mixers. Lubrication methods can include manual lubrication, automatic lubrication systems, and centralized lubrication systems. The frequency of lubrication should be based on the manufacturer’s recommendations and the level of usage. Proper fluid levels should be maintained to ensure that mixers are operating at optimal levels.
Monitoring and Analyzing Mixer Performance Data
Monitoring and analyzing mixer performance data can help to identify potential issues before they become significant problems. Performance data can include temperature, vibration, and power measurements, among others. The data can be used to identify trends in equipment performance and to adjust maintenance schedules and tasks accordingly.
8. Measuring the Efficiency of Preventive Maintenance for Mixers
Measuring the efficiency of preventive maintenance for mixers can help to identify areas for improvement and to optimize the maintenance program. In this section, we’ll discuss some of the key performance indicators (KPIs) that can be used to measure the efficiency of preventive maintenance for mixers.
Downtime
Downtime is the amount of time that equipment is not available for production. Measuring downtime can help to identify areas where maintenance tasks can be improved to reduce downtime and increase production efficiency.
Maintenance Costs
Maintenance costs include the cost of labor, parts, and supplies required for maintenance tasks. Measuring maintenance costs can help to identify areas where maintenance tasks can be improved to reduce costs and increase efficiency.
Equipment Reliability
Equipment reliability measures the likelihood of equipment failure. Measuring equipment reliability can help to identify areas where maintenance tasks can be improved to increase equipment reliability and reduce the risk of equipment failure.
Equipment Lifespan
Equipment lifespan measures the length of time that equipment is in service. Measuring equipment lifespan can help to identify areas where maintenance tasks can be improved to extend equipment lifespan and reduce the need for premature replacements.
Maintenance Frequency
Maintenance frequency measures the frequency of maintenance tasks performed on equipment. Measuring maintenance frequency can help to identify areas where maintenance tasks can be optimized to reduce the frequency of maintenance tasks while maintaining equipment reliability and efficiency.
9. Role of CMMS
Computerized Maintenance Management Systems (CMMS) can be used to optimize the preventive maintenance program for mixers. In this section, we’ll discuss some of the key features of CMMS that can be used to manage preventive maintenance for mixers.
Master Data Management
Master data management is the process of managing the data required for preventive maintenance tasks. This can include equipment specifications, maintenance schedules, and task lists, among others. CMMS can be used to manage master data and ensure that it is up-to-date and accurate.
Equipment History
Equipment history includes the maintenance history of each piece of equipment. This can include maintenance tasks performed, parts replaced, and repairs made. CMMS can be used to maintain equipment history and provide a complete record of maintenance activities.
Preventive Maintenance Scheduling and Tracking
Preventive maintenance scheduling and tracking involves the scheduling and tracking of maintenance tasks. CMMS can be used to schedule maintenance tasks, assign tasks to personnel, and track the completion of tasks.
Operational Technology Integration and Condition Based Maintenance
Operational technology integration and condition-based maintenance involves the integration of equipment performance data with the preventive maintenance program. This can include the use of sensors to monitor equipment performance and the use of data analytics to identify potential issues before they become significant problems. CMMS can be used to integrate operational technology data with the preventive maintenance program and to adjust maintenance schedules and tasks based on equipment performance data.
KPIs Monitoring
KPIs monitoring involves the monitoring of key performance indicators to measure the efficiency of the preventive maintenance program. CMMS can be used to monitor KPIs such as downtime, maintenance costs, equipment reliability, equipment lifespan, and maintenance frequency.
10. Conclusion
Preventive maintenance for mixers is an essential component of asset management and plant maintenance. A well-designed preventive maintenance program can help to minimize the risk of equipment failure, reduce downtime, and increase production efficiency. Developing a preventive maintenance program for mixers requires the identification of critical mixers and equipment, researching OEM manuals and recommendations, factoring operational conditions, establishing maintenance schedules and tasks, and developing a system for tracking and recording maintenance activities. Best practices for preventive maintenance include regular inspections and cleaning, proper lubrication and fluid levels, and monitoring and analyzing mixer performance data. Key performance indicators such as downtime, maintenance costs, equipment reliability, equipment lifespan, and maintenance frequency can be used to measure the efficiency of the preventive maintenance program. CMMS can be used to optimize the preventive maintenance program for mixers by managing master data, maintaining equipment history, scheduling and tracking maintenance tasks, integrating operational technology data, and monitoring KPIs.
Request a one-one demo with our solution engineering team.
Request a one-one demo with our solution engineering team.
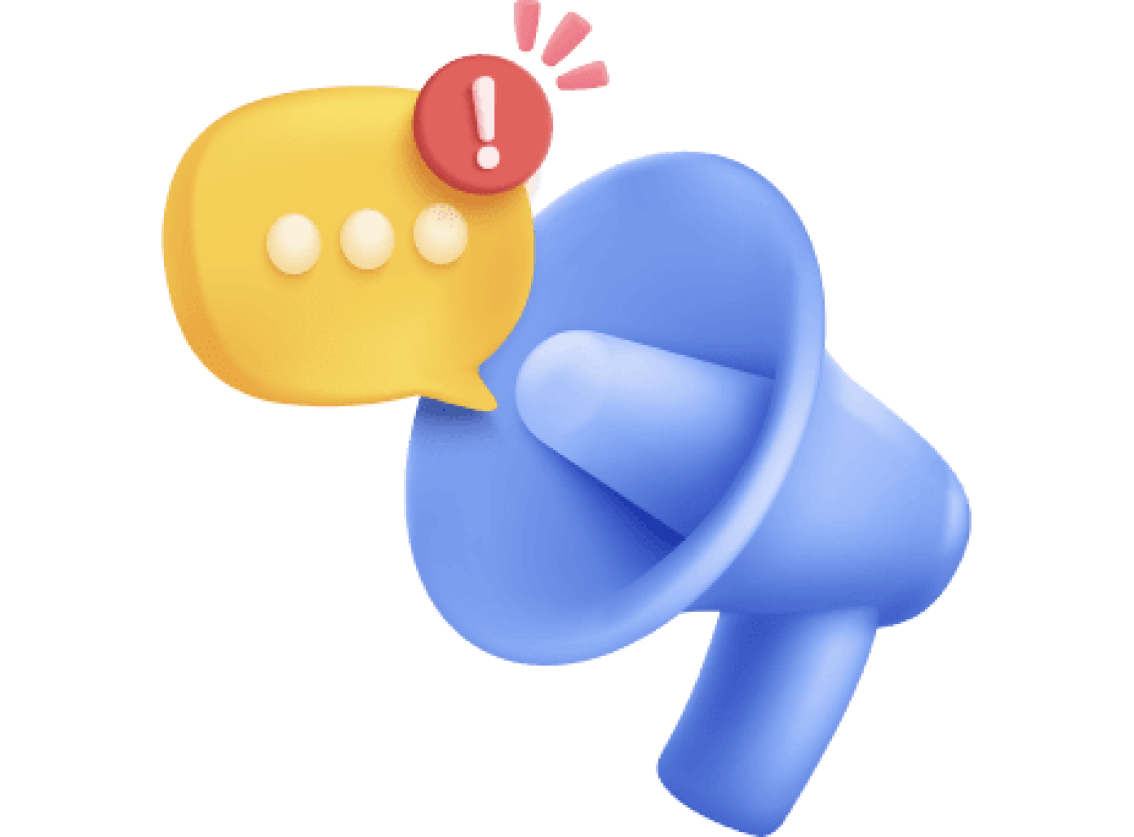