Troubleshooting Your Pipes
and Pipelines
Troubleshooting Your Pipes & Pipelines
Table of Contents
ToggleA Step-by-Step Guide to Troubleshooting Your Pipes and Pipelines: Maintenance and Repair Strategies
Welcome to MaintWiz Technologies’ guide on troubleshooting your pipes and pipelines. In this comprehensive guide, we will cover the key aspects of pipe and pipeline maintenance and repair strategies. Whether you’re an asset manager, maintenance manager, safety officer, manufacturing professional, production in-charge, supervisor, consultant or expert, this guide is for you.
1. Introduction
Pipes and Pipelines are an integral part of many industries, including oil and gas, chemical, pharmaceutical, water and wastewater, and many others. Pipes and pipelines are used for transportation, distribution, and storage of liquids and gases. They play a crucial role in ensuring the smooth functioning of processes and systems.
However, over time, pipes and pipelines can experience wear and tear, leading to various problems, such as leaks, blockages, and low flow. In this guide, we will cover the importance of pipe and pipeline maintenance, the types of pipes and pipelines, the benefits of effective troubleshooting, and more.
Types of Pipes and Pipelines
Metal Pipes: Metal pipes are widely used in industrial settings due to their durability and strength. Metal pipes are made of steel, copper, or other alloys.
PVC Pipes: PVC pipes are commonly used for water distribution systems, drainage systems, and irrigation. PVC pipes are lightweight and easy to install.
Concrete Pipes: Concrete pipes are used for stormwater drainage and sewage systems. Concrete pipes are strong and durable.
Composite Pipes: Composite pipes are made of a combination of materials, such as fiberglass, plastic, and metal. Composite pipes offer high strength and durability, as well as resistance to corrosion and chemicals.
Flexible Pipes: Flexible pipes are used for applications where flexibility is required, such as in offshore drilling, gas and oil extraction, and underground mining. Flexible pipes are made of materials such as polyethylene, polypropylene, and nylon.
Each type of pipe and pipeline has its own unique characteristics, advantages, and disadvantages. Understanding the differences between the types of pipes and pipelines is important in troubleshooting and maintenance.
The Importance of Pipe and Pipeline Maintenance:
Effective maintenance of pipes and pipelines is crucial in ensuring the smooth functioning of processes and systems. Poorly maintained pipes and pipelines can lead to downtime, breakdowns, and costly repairs. Regular maintenance can prevent these issues and increase the lifespan of pipes and pipelines.
The Benefits of Effective Troubleshooting
Effective troubleshooting is key in identifying and resolving problems with pipes and pipelines. Troubleshooting can help prevent downtime and breakdowns, increase efficiency and performance, and reduce repair costs. By identifying the root cause of the problem, troubleshooting can lead to long-term solutions that prevent future issues.
2. Key Sub-assemblies of Pipes and Pipelines
Pipe and Pipeline Material: The material of the pipe or pipeline can affect its durability, resistance to corrosion, and lifespan. Different materials are used for different applications. Understanding the properties of the materials used in pipes and pipelines is important in troubleshooting and maintenance.
Pipe and Pipeline Coatings: Coatings are applied to pipes and pipelines to protect them from corrosion, erosion, and other forms of wear and tear. Coatings can be made of materials such as epoxy, polyurethane, and zinc. Proper selection and maintenance of coatings can prevent corrosion and extend the lifespan of pipes and pipelines.
Pipe and Pipeline Insulation: Insulation is used to regulate the temperature of the contents of the pipe or pipeline. Insulation can be made of materials such as fiberglass, mineral wool, and foam. Proper insulation can prevent overheating, freezing, and other temperature-related issues.
Pipe and Pipeline Fittings: Fittings are used to connect pipes and pipelines to each other and to other equipment. Fittings can include elbows, tees, reducers, and couplings. Proper selection and maintenance of fittings can prevent leaks and ensure proper flow.
Pipe and Pipeline Valves: Valves are used to control the flow of liquids and gases in pipes and pipelines. Valves can be manual or automated and can include gate valves, ball valves, and butterfly valves. Proper selection and maintenance of valves can prevent leaks and ensure proper flow.
Free Daily, Weekly, Monthly, Quarterly and Annual Preventive Maintenance Checklists for different Equipment Categories.
3. Top 10 Most Common Pipe and Pipeline Problems
Corrosion and Rust: Corrosion and rust can weaken pipes and pipelines, leading to leaks and eventual failure. Corrosion and rust can be caused by exposure to moisture, chemicals, and other factors.
Leaks and Cracks: Leaks and cracks can lead to loss of fluids, reduced efficiency, and environmental hazards. Leaks and cracks can be caused by wear and tear, corrosion, and other factors.
Clogging and Blockages: Clogging and blockages can cause reduced flow, increased pressure, and eventual failure. Clogging and blockages can be caused by foreign objects, debris, and sediment buildup.
Faulty Valves: Faulty valves can lead to improper flow, leaks, and reduced efficiency. Faulty valves can be caused by wear and tear, corrosion, and other factors.
Low Flow and Pressure: Low flow and pressure can reduce efficiency and cause system failure. Low flow and pressure can be caused by clogging, blockages, and other factors.
Pipeline Overheating: Pipeline overheating can cause material degradation and eventual failure. Pipeline overheating can be caused by insulation failure, heat sources, and other factors.
Excessive Vibration: Excessive vibration can cause stress on pipes and pipelines, leading to leaks and eventual failure. Excessive vibration can be caused by improper installation, equipment failure, and other factors.
Pressure Buildup: Pressure buildup can cause stress on pipes and pipelines, leading to leaks and eventual failure. Pressure buildup can be caused by equipment failure, blockages, and other factors.
Temperature Fluctuations: Temperature fluctuations can cause stress on pipes and pipelines, leading to leaks and eventual failure. Temperature fluctuations can be caused by environmental factors, insulation failure, and other factors.
Regulatory Compliance Issues: Regulatory compliance issues can lead to fines, shutdowns, and legal issues. Regulatory compliance issues can be caused by failure to adhere to codes, standards, and regulations.
4. Pre-Troubleshooting Steps
Conducting an Initial Assessment: Before troubleshooting, it is important to conduct an initial assessment of the pipe and pipeline system. This assessment should include a visual inspection of the system, gathering information on the system, and identifying any potential hazards or safety issues.
Gathering Information on the Pipe and Pipeline System: Gathering information on the pipe and pipeline system is important in troubleshooting. This information should include the age of the system, the material used, the type of coating and insulation, the type of fittings and valves, and any previous maintenance or repair work that has been done.
Safety Precautions to Take: Safety should always be a top priority when troubleshooting pipes and pipelines. Proper safety precautions should be taken, such as wearing protective equipment, turning off power sources, and following safety guidelines and regulations.
5. Troubleshooting and Problem Identification
Checking the Pressure and Flow Rate: Checking the pressure and flow rate of the pipe and pipeline system can help identify potential issues. This can be done using pressure gauges and flow meters.
Inspecting the Pipes and Pipelines: Inspecting the pipes and pipelines can help identify issues such as leaks, cracks, and corrosion. This can be done visually or using technologies such as ultrasonic testing or X-ray inspection.
Troubleshooting the Valves: Troubleshooting the valves can help identify issues such as improper flow and leaks. This can be done by visually inspecting the valves, testing the valves, and replacing any faulty valves.
Testing the Pumps and Compressors: Testing the pumps and compressors can help identify issues such as low flow and pressure. This can be done by visually inspecting the pumps and compressors, testing the pumps and compressors, and replacing any faulty parts.
Inspecting the Insulation and Coatings: Inspecting the insulation and coatings can help identify issues such as overheating and corrosion. This can be done by visually inspecting the insulation and coatings, testing the insulation and coatings, and replacing any faulty parts.
6. Repairing the Pipes and Pipelines
Replacing Faulty Parts: When troubleshooting identifies faulty parts, it is important to replace them. This can include replacing valves, fittings, and pipes. Proper selection and installation of replacement parts is crucial in preventing future issues.
Repairing Welding Issues: Welding issues can lead to leaks and eventual failure. Repairing welding issues can include cleaning the area, replacing the faulty weld, and proper testing to ensure the integrity of the repair.
Cleaning and Lubricating Components: Cleaning and lubricating components can prevent issues such as clogging and blockages. This can include cleaning valves and fittings, and lubricating moving parts.
7. Testing and Maintenance
Running Tests to Ensure Proper Functionality: Running tests on the pipe and pipeline system can ensure proper functionality and identify any potential issues. This can include load testing, electrical troubleshooting, safety inspection, and testing valves and pumps.
Developing a Maintenance Plan: Developing a maintenance plan can prevent future issues and increase the lifespan of pipes and pipelines. A maintenance plan should include regular inspections, cleaning, lubrication, and replacement of faulty parts.
How CMMS can help: Computerized maintenance management systems (CMMS) can help in managing maintenance tasks, scheduling inspections, and tracking maintenance history. CMMS can also help in identifying potential issues and preventing downtime.
8. Best Practices
Tips and Tricks: Tips and tricks can help in troubleshooting and maintenance. This can include using the appropriate tools and equipment, following safety guidelines and regulations, and proper selection and installation of replacement parts.
How to Prevent Most Common Problems: Preventing the most common problems with pipes and pipelines can save time and money in the long run. This can include regular maintenance, proper selection and installation of components, and following regulatory compliance guidelines.
9. Conclusion
In conclusion, troubleshooting and maintenance of pipes and pipelines is crucial in ensuring the smooth functioning of processes and systems. Understanding the different types of pipes and pipelines, key sub-assemblies, and common issues is important in troubleshooting and maintenance. Following best practices, developing a maintenance plan, and using CMMS can help prevent issues and increase the lifespan of pipes and pipelines.
10. Key Takeaways
- Effective maintenance of pipes and pipelines is crucial in ensuring the smooth functioning of processes and systems.
- Understanding the different types of pipes and pipelines, key sub-assemblies, and common issues is important in troubleshooting and maintenance.
- Preventing issues with pipes and pipelines can save time and money in the long run.
- Following best practices, developing a maintenance plan, and using CMMS can help prevent issues and increase the lifespan of pipes and pipelines.
Request a one-one demo with our solution engineering team.
Request a one-one demo with our solution engineering team.
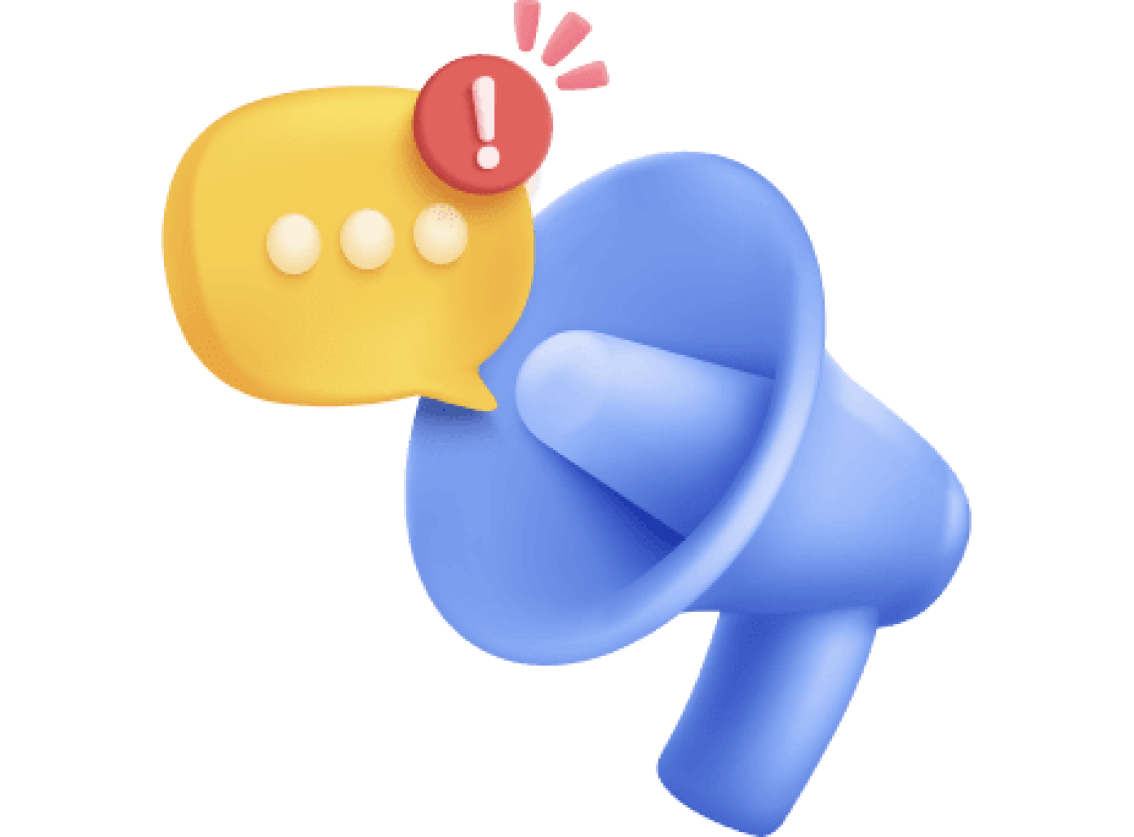